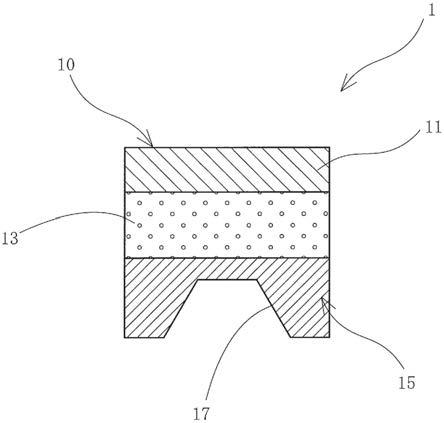
1.本实用新型涉及汽车的仪表板,特别是具有气囊门的仪表板。
背景技术:
2.在制作汽车的仪表板时,为了提高外观性,常常将片材与发泡材料一体化后的片状复合表皮紧贴在具有规定形状的基材的表面,然后从基材侧抽真空,将复合表皮用真空成型的方式贴在基材上。
3.另一方面,为了保护坐在副驾驶席上的乘车者,在汽车的仪表板的背面侧通常设置有副驾驶气囊装置。在设置有这种副驾驶气囊装置的仪表板上,设置有在副驾驶气囊装置动作时展开的气囊门,以确保副驾驶气囊装置的气囊能够向车内膨胀。
4.在该气囊门上,形成有厚度比仪表板的板厚薄的脆弱部,该脆弱部在气囊展开的压力作用下裂开,从而使气囊门敞开。这样,能够确保气囊顺利地展开,并加快气囊展开所需的时间。
5.然而,由于这种脆弱部通常是通过用成型模具(模具)进行基材的注塑成型之后、进行用立铣刀切削基材(在基材上形成截面为矩形的凹槽)的后加工而获得的,所以,存在有可能因后加工不良而导致损耗、以及因加工时间较长而导致生产效率低的问题。
6.因此,为了取消上述后加工,可以考虑采用具有截面为矩形的突起部的成型模具,利用该截面为矩形的突起部在基材上形成截面为矩形的凹槽。这样,便能在进行基材的注塑成型的同时,在基材上形成凹槽。但是,在此情况下,截面为矩形的突起部在树脂流动所产生的力的作用下有可能会破损。
7.此外,也可以考虑采用滑动模具作为成型模具,在树脂注入后且树脂固化之前,通过滑动来形成截面为矩形的凹槽。但是,在此情况下,模具结构变得复杂,从而又会出现维护次数增加、生产效率降低的问题。
技术实现要素:
8.针对上述技术问题,本实用新型的目的在于,提供一种既能确保气囊顺利展开又能提高生产效率的、具有气囊门的仪表板。
9.作为解决上述技术问题的技术方案,本实用新型提供一种具有气囊门的仪表板,该仪表板由基材、片材、及夹在所述基材与所述片材之间的发泡材料构成,所述气囊门上形成有在气囊展开的压力作用下会裂开的脆弱部,其特征在于,由成型模具成型的所述基材具有2.5mm的厚度,所述脆弱部由利用所述成型模具上设置的突起部在所述基材上形成的凹槽构成,所述凹槽的截面形状为向下方开口的梯形,所述凹槽被构成为,上底厚度为0.3mm、深度为1.9~2.1mm、斜边的倾斜角度为40~45
°
。
10.基于本实用新型的上述具有气囊门的仪表板,由于在厚度为2.5mm的基材上形成有深度为1.9~2.1mm的凹槽,并且脆弱部处的基材的残留厚度,即,凹槽的上底厚度为0.4~0.6mm,所以能够确保脆弱部在气囊展开的压力作用下裂开而使气囊门敞开,从而能够确
保气囊顺利地展开。
11.此外,由于构成脆弱部的凹槽的截面形状为向下方开口的梯形,而成型模具上设置的突起部的形状与该凹槽相对应,也具有梯形截面,所以该突起部不容易在树脂流动所产生的力的作用下破损。而且,凹槽的斜边的倾斜角度被设定为40~45
°
,从而确保了模切坡度,即使不采用滑动模具,也能够容易地进行模切。这样,通过使用设置有截面为梯形的突起部的成型模具,能够在进行基材成型的同时形成构成脆弱部的凹槽,从而能够废止使用立铣刀的后加工,提高生产效率。
12.因而,基于本实用新型,能够提供既能确保气囊顺利展开又能提高生产效率的、具有气囊门的仪表板。
附图说明
13.图1是示意性地表示本实用新型的实施方式的仪表板的立体图。
14.图2是示意性地表示图1所示的仪表板上的脆弱部的截面图。
15.图3是表示图2所示的脆弱部处的基材规格参数的图。
16.图4是示意性地表示现有技术的仪表板上的脆弱部的截面图。
具体实施方式
17.以下,参照附图对本实用新型的实施方式进行说明。但是,本实用新型不局限于下述实施方式中记载的内容。另外,各图中的尺寸关系(长度、宽度等)不反映实际的尺寸关系。
18.图1是示意性地表示本实施方式的仪表板1的立体图。在此,采用该仪表板1的车辆(未图示)是转向装置(未图示)设置在车宽方向左侧的左舵车辆,即右侧通行车辆。此外,图1中,箭头fr示出车长方向的前侧,箭头up示出上下方向的上侧,箭头rh示出车宽方向的右侧。
19.通常,用于保护驾驶者的驾驶席气囊装置(未图示)设置在转向柱(未图示)的后端部,而用于保护乘坐在副驾驶席上的乘坐者的副驾驶席气囊装置20则如图1所示那样,设置在车宽方向右侧的仪表板1的背面侧。因而,仪表板1上设置有在副驾驶席气囊装置20动作时敞开的气囊门3,以确保副驾驶席气囊装置20的气囊能够向车内膨胀展开。
20.如图1所示,在气囊门3上形成有厚度比仪表板1的板厚薄的脆弱部10。该脆弱部10在气囊展开的压力作用下裂开,而使气囊门3可靠地敞开,从而能够确保气囊顺利展开、并加快气囊展开所需的时间。
21.图2是示意性地表示仪表板1上的脆弱部10的截面图。如图2所示,仪表板1由基材15、片材11、以及夹在基材15与片材11之间的发泡材料13构成为三层结构。
22.片材11构成仪表板1的表面(外观面),赋予外观高级感,其厚度大致为0.4~1.0mm。作为片材11,例如可采用由pv c(聚氯乙烯)、tpo(烯烃系热塑性弹性体)、tpu(热塑性聚氨酯弹性体)等热塑性树脂构成的热塑性片材。
23.发泡材料13是用于对仪表板1赋予柔软手触感的发泡体,发泡倍率为10~30倍,厚度为1.0~3.0mm左右。作为发泡材料13,例如可采用聚丙烯泡沫、聚乙烯泡沫、聚氨酯泡沫等。
24.基材15是作为仪表板1的骨架的硬质构件。作为基材15,可采用pp(聚丙烯)。本实施方式中,使用成型模具(未图示)进行的仪表板1的基材15注塑成型,所获得的基材15具有2.5mm的厚度。
25.另外,也有的用搪塑表皮和聚氨酯泡沫作为片材11和发泡材料13的结构。但是,在此情况下,在氨酯注入发泡时,为了使氨酯流动到片材11与基材15之间,需要5.0~8.0mm左右的空隙,因而存在仪表板1的板厚增加的问题。而且,在脆弱部的搪塑表皮的背面,需要使用热刀等进行后加工来形成切口,因而存在生产效率低的问题。
26.对此,本实施方式的仪表板1中,通过用热塑性片和聚丙烯泡沫作为片材11和发泡材料13,能够将发泡材料13的厚度抑制在2.0~3.0mm,因而,与采用搪塑表皮和聚氨酯泡沫的情况相比,能够减小仪表板1的板厚,扩大车厢内部空间,并且不需要在片材11上形成切口,从而能够提高生产效率。
27.下面,对气囊门3上形成的脆弱部10进行详细说明。为了使本实施方式的结构更易于理解,首先对现有技术的脆弱部进行说明。
28.图4是示意性地表示现有技术的仪表板101上的脆弱部110的截面图。如图4所示,现有技术的仪表板101也由基材115、片材111、以及夹在基材115与片材111之间的发泡材料113构成为三层结构。在这样的仪表板101中,脆弱部110是通过在基材115上形成截面形状为向下方开口的矩形凹槽117而构成的。这样,通过形成厚度比仪表板101的板厚薄的脆弱部110,在气囊展开的压力作用下该脆弱部110会裂开而使气囊门敞开,从而能够确保气囊顺利展开、加快气囊展开所需的时间。
29.但是,现有技术的脆弱部110是通过用成型模具(未图示)进行基材115的注塑成型之后,进行用立铣刀(未图示)切削基材115(在基材115上形成截面为矩形的凹槽117)的后加工而获得的,因此,存在有可能因后加工不良而导致损耗、以及因加工时间较长而导致生产效率低的问题。
30.因此,为了取消后加工,可以考虑采用具有截面为矩形的突起部的成型模具,利用该截面为矩形的突起部在基材115上形成截面为矩形的凹槽117。这样,便能在进行基材115的注塑成型的同时,在基材115上形成凹槽117。但是,在此情况下,截面为矩形的突起部在树脂流动所产生的力的作用下有可能会破损。
31.此外,也可以考虑采用滑动模具作为成型模具,在树脂注入后且树脂固化之前,通过滑动来形成截面为矩形的凹槽117。但是,在此情况下,模具结构变得复杂,从而又会出现维护次数增加、生产效率降低的问题。
32.对此,本实施方式中,利用成型模具上设置的截面为梯形的突起部(未图示),在基材15上形成用于构成脆弱部10的梯形凹槽17。详细而言,如图1所示,凹槽17被构成为,截面形状为向下方开口且上底宽度小于开口宽度的梯形。
33.图3是表示脆弱部10处的基材15的规格参数的图。首先,脆弱部10的残留厚度(凹槽17的上底厚度)t是影响气囊展开并与拉伸强度相关的重要尺寸,因而采用与现有技术的脆弱部110相同的尺寸。具体而言,本实施方式的脆弱部10与现有技术的脆弱部110一样,通过在厚度为2.5mm的基材15上形成深度h为1.9~2.1mm的凹槽17,而将残留厚度t设定为0.4~0.6mm。
34.通过将脆弱部10处的基材15的残留厚度t设定为0.4~0.6mm,与现有技术的脆弱
部110一样,脆弱部10能够在气囊展开的压力作用下容易地裂开而使气囊门3敞开,因而,能够确保气囊顺利展开。
35.另外,通过进行用立铣刀切削基材115的后加工而形成的现有技术的脆弱部110的凹槽117的宽度b为1.0mm,而本实施方式的脆弱部10的凹槽17的宽度b(凹槽17的上底)被设定为模具成型的极限尺寸0.3mm。
36.另外,为了使脆弱部10上的应力集中状况与现有技术的脆弱部110相同,需要使脆弱部10的斜边角度θ(凹槽17的斜边的倾斜角度)在40
°
以上。同时,为了防止因树脂流动而导致成型模具破损,需要斜边角度θ在45
°
以下,以确保模具的强度。因此,本实施方式中,将脆弱部10的斜边角度θ设定为40~45
°
。
37.由于在成型模具上设置的突起部的截面形状是与凹槽17的截面形状相对应的梯形,所以,该突起部不容易因树脂流动所产生的力而破损。此外,由于斜边角度θ被设定为40~45
°
,所以确保了模切坡度。因而,即使不采用滑动模具,也能够容易地进行模切。如此,能够在使用成型模具进行基材15的成型的同时,形成构成脆弱部10的凹槽17,因而,能够取消使用立铣刀的后加工,从而能够提高生产效率。
38.因此,基于本实施方式,能够提供既能确保气囊顺利展开又能提高生产效率的、具有气囊门3的仪表板1。