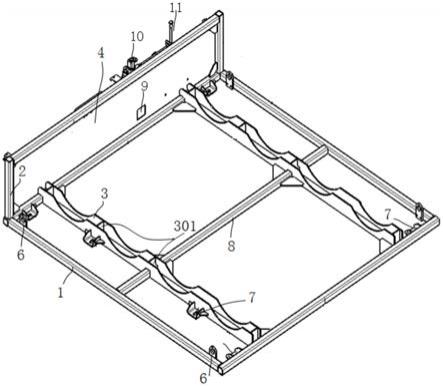
1.本实用新型涉及燃料电池汽车车载氢系统技术领域,具体涉及一种轻量化车载氢系统框架结构。
背景技术:
2.以氢能为能量来源的燃料电池以其使用效率高、无污染等特点在新能源汽车领域得到较好应用研究,突显出与传统和纯电动汽车相比的诸多优势。车载供氢系统是燃料电池汽车的重要部件,为燃料电池发动机提供燃料供应。受限于技术及加氢基础设施,当前车载氢以高压气态氢为主,储存24kg氢气的燃料电池客车车载氢系统质量大概接近1000kg,造成整车整备质量高,燃料经济性不佳。
技术实现要素:
3.本实用新型所要解决的技术问题是:提供一种轻量化车载氢系统框架结构,以解决常规承载氢燃料气瓶的架体结构质量过重,从而导致整车的整备质量高,燃料经济性不佳的问题。
4.为解决上述问题,本实用新型提供了如下技术方案:
5.一种轻量化车载氢系统框架结构;它包括设置在平面上的底支架框;在底支架框上的一个侧沿处还设置有辅助框;底支架框和辅助框均为使用轻量化型材制作的矩形框架结构;在底支架框的框内安装有若干根承载纵梁;承载纵梁为使用c型槽钢加工的直管结构,且在承载纵梁的顶部设置有用于放置氢燃料气瓶鞍座的弧形凹槽;在辅助框朝向外部的一侧还安装有支撑面板;支撑面板使用铝合金或复合材料制成;在支撑面板上安装有控制器罩板。
6.优选的,制作底支架框和辅助框的轻量化型材为截面呈矩形的管材结构,且该矩形管材的壁厚为2~5mm,矩形管材使用6061铝合金、gfrp、cfrp和镁合金中的一种材料制作而成。
7.优选的,在底支架框前后侧平行于承载纵梁的轻量化型材框架上还设置有四个吊耳;四个吊耳对应设置在底支架框内部的四个夹角位置处,且在吊耳上还开有吊孔。
8.优选的,在底支架框与承载纵梁的侧壁上还固定有8个紧固安装支架;其中四个紧固安装支架设置在底支架框左右侧垂直于承载纵梁的轻量化型材框架上,并与吊耳相邻设置;另外四个紧固安装支架均匀地安装在承载纵梁上。
9.优选的,承载纵梁采用q345或高于此牌号的槽钢结构,在承载纵梁的槽结构中还布置有若干个加强板。
10.优选的,在底支架框的中部还设置有加强梁;在承载纵梁的中部开有与加强梁的横截面形状相对应的定位槽,加强梁垂直且穿过承载纵梁进行安装。
11.优选的,在支撑面板的中部开有过线孔;且在支撑面板朝向外侧的一端上还安装有减压阀和泄放口。
12.优选的,在底支架框与辅助框之间,以及底支架框与承载纵梁之间均设置有若干个加强筋。
13.本实用新型有益效果:
14.采用本实用新型设计的轻量化车载氢系统框架,较传统设计减重25%~30%,在保障车载氢系统框架强度的同时,降低了整车整备质量,进而提高燃料经济性。
附图说明
15.图1是本实用新型在实施例中的结构示意图;
16.图2是图1中装置在支撑面板侧的示意图;
17.附图标记说明:1、底支架框,2、辅助框,3、承载纵梁,301、加强板,4、支撑面板,5、控制器罩板,6、吊耳,7、紧固安装支架,8、加强梁,9、过线孔,10,减压阀,11、泄放口。
具体实施方式
18.下面结合附图及具体的实施例对本实用新型进行进一步介绍:
19.实施例1:
20.参照图1,本实施例提供一种轻量化车载氢系统框架结构;它包括设置在平面上的底支架框1;在底支架框1上的一个侧沿处还设置有辅助框2;底支架框1和辅助框2均为使用轻量化型材制作的矩形框架结构;在底支架框1的框内安装有若干根承载纵梁3;承载纵梁3为使用c型槽钢加工的直管结构,且在承载纵梁3的顶部设置有用于放置氢燃料气瓶鞍座的弧形凹槽;在辅助框2朝向外部的一侧还安装有支撑面板4;支撑面板(7)采用厚度为1.5mm的6061铝合金制成;在支撑面板4上安装有控制器罩板5。
21.制作底支架框和辅助框的轻量化型材为截面呈矩形的管材结构,且该矩形管材的壁厚为3mm,矩形管材使用cfrp材料制作而成。本实施例中,矩形管材之间通过可以采用焊接、胶接、胶接/铆接混合连接、胶接/螺接混合连接等多种方式进行连接;
22.在底支架框1前后侧平行于承载纵梁3的轻量化型材框架上还设置有四个吊耳6;四个吊耳对应设置在底支架框1内部的四个夹角位置处,且在吊耳6上还开有吊孔。本实施例中吊耳采用6061铝合金制作,壁厚4 mm~6mm,吊孔孔径20 mm~60mm;吊耳6的设置是为了供车载氢系统进行安装拆卸的辅助吊装使用。
23.在底支架框1与承载纵梁3的侧壁上还固定有8个紧固安装支架7;其中四个紧固安装支架7设置在底支架框1左右侧垂直于承载纵梁3的轻量化型材框架上,并与吊耳6相邻设置;另外四个紧固安装支架7均匀地安装在承载纵梁3上。本实施例中的紧固安装支架7通过焊接手段进行固定。
24.承载纵梁3采用q345牌号的槽钢结构,可以想到的是,在满足使用要求的前提下也能够选用或高于q345牌号的槽钢结构,在承载纵梁3的槽结构中还布置有若干个加强板301。考虑到承载纵梁的受力情况,同时为保障燃料电池汽车整车运行过程中急刹车、碰撞等情况下车载氢系统受到冲击后不发生破坏或位移量不超过13mm;故而在综合重量考虑后采用了槽钢,并设置加强板以对应提高强度。
25.在底支架框1的中部还设置有加强梁8;在承载纵梁3的中部开有到校与加强梁8的横截面形状相对应的定位槽,加强梁8垂直且穿过承载纵梁3进行安装。
26.在支撑面板4的中部开有过线孔9;且在支撑面板4朝向外侧的一端上还安装有减压阀10和泄放口11。过线孔9的设置能够便氢瓶、传感器等与控制器连接的线束能够在车载氢系统框架内侧走线及固定,避免外围走线在系统运输、安装过程中出现划伤、刮擦等损伤,同时提高外观整洁度;同时,该支撑面板4还起到固定减压阀10、泄放口11等作用。
27.在底支架框1与辅助框2之间,以及底支架框1与承载纵梁3之间均设置有若干个加强筋。本实施例中加强筋与临近的矩形管材之间均使用螺栓组件进行连接固定。
28.采用本实施例中公开的设计方法所设计的轻量化车载氢系统框架,较传统设计而言减重了30%。
29.实施例2
30.在本实施例中,支撑面板7采用厚度为2mm的6061铝合金制成;同时制作底支架框和辅助框的轻量化型材为截面呈矩形的管材结构,且该矩形管材使用壁厚为5mm的6061铝合金材料制成;其余结构设计与实施例1相同,在此不再赘述,
31.而采用本实施例中公开的设计方法所设计的轻量化车载氢系统框架,较传统设计而言减重了25%。
32.实施例3
33.在本实施例中,支撑面板7采用厚度为3mm的6061铝合金制成;同时制作底支架框和辅助框的轻量化型材为截面呈矩形的管材结构,且该矩形管材使用壁厚为2mm的gfrp材料制成;其余结构设计与实施例1相同,在此不再赘述,
34.而采用本实施例中公开的设计方法所设计的轻量化车载氢系统框架,较传统设计而言减重了28%。
35.可以理解的是,以上实施方式仅仅是为了说明本发明的原理而采用的示例性实施方式,然而本发明并不局限于此。对于本领域内的普通技术人员而言,在不脱离本发明的精神和实质的情况下,可以做出各种变型和改进,这些变型和改进也视为本发明的保护范围。