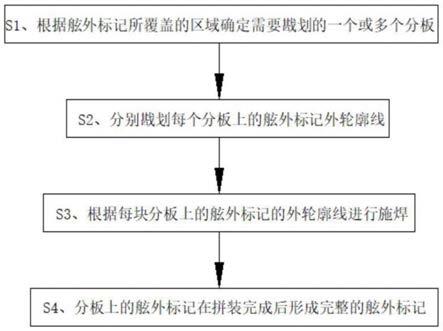
1.本技术涉及船舶建造技术领域,具体而言,涉及一种船舶舷外标记戡划方法及船舶外板。
背景技术:
2.在船舶分段建造过程中,其主体船外板涉及到舷外标记字母戡划与焊接作业,但工艺流程是在分段建造结束吊离胎架上门架后,由多名作业人员利用涤纶纸站立在简易的梯子上昂视的贴敷于分段外板进行敲洋冲戡划出标记字母,再由作业人员站立于梯子上以昂视的方式进行字母的间断焊来完成。这种传统性工艺方式影响着产品建造生产效率、立体作业强增设施工难度,同时安全风险较高。
3.因此,需要提供一种针对上述现有技术不足的改进技术方案。
技术实现要素:
4.本技术实施例的目的在于提供一种船舶舷外标记戡划方法,取代了大分段上门架后施工作业人员拿涤纶纸朝天贴附分段外板来戡划船舶外板舷外标记字母和立体作业的仰视焊接法。
5.本技术实施例的另一目的还在于提供一种船舶外板,提高了船舶外板在焊接施工过程的焊接精度,提高工作效率,保证施工安全。
6.第一方面,本技术实施例提供了一种船舶舷外标记戡划方法,包括:
7.s1,根据船舶外板中需勘划舷外标记的位置及预勘划舷外标记所覆盖的区域确定出船舶外板中需勘划的一块或多块分板。
8.s2,在所述需勘划的一块或多块分板上进行舷外标记勘划。
9.s3,在船舶的小组立阶段之前,完成对每块所述分板上对应舷外标记的施焊。
10.s4,在船舶的大组立阶段,分板上的舷外标记在所述船舶外板拼装完成后形成完整的舷外标记。
11.在一种实施方案中,在步骤s2中,在所述需勘划的一块或多块分板上进行舷外标记勘划包括:在每块分板上勘划出用于舷外标记定位的肋位线。依据所述肋位线在每个分板上勘划出舷外标记的外轮廓线。
12.在一种实施方案中,舷外标记为字母、数字或图案,所述舷外标记包括直线部分和/或曲线部分。
13.在一种实施方案中,在步骤s2中,利用切割机的喷粉机构对所述分板分别进行舷外标记的喷粉勘划。
14.在一种实施方案中,在所述舷外标记为字母、所述船舶外板包括左舷外板及右舷外板、以及所述左舷外板分为第一分板和第二分板和所述右舷外板分为第三分板和第四分板时。将所述字母划分为左舷外板字母和右舷外板字母;所述左舷外板字母的上半部分勘划在所述第一分板上,左舷外板字母的下半部分勘划在所述第二分板上;所述右舷外板字
母的上半部分勘划在所述第三分板上,右舷外板字母的下半部分勘划在所述第四分板上。
15.在一种实施方案中,在步骤s3中,对每块所述分板上对应舷外标记的施焊包括:根据所述舷外标记的外轮廓线堆焊舷外标记,堆焊的宽度为4
‑
6mm,高度为2
‑
3mm。
16.在一种实施方案中,舷外标记直线部分的焊接长度l为98
‑
102mm,间断空不焊长度s为498
‑
502mm。舷外标记曲线部分的焊接长度l为48
‑
52mm,间断空不焊长度s为98
‑
102mm。
17.在一种实施方案中,在步骤s3中,依据每块所述分板上戡划的字母外轮廓线,将每块所述分板分别放置于地面或者平整区域对舷外标记施焊。
18.本技术的第二方面,还提供了一种船舶外板,在所述船舶外板上设有舷外标记,所述舷外标记使用上述船舶舷外标记戡划方法进行戡划。
19.本技术中的船舶舷外标记戡划方法具有的有益效果:
20.本发明公开了一种船舶舷外标记戡划方法及船舶外板,实现了生产效率提升,降低施工作业难度,保障安全化生产的发展需求,更进一步推进船舶建造快速化领域奠定良好的基础。
21.本发明根据船舶外板中需勘划舷外标记的位置及预勘划舷外标记所覆盖的区域确定出船舶外板中需勘划的一块或多块分板,由切割机设备先对各分板进行喷粉戡划,在小组立阶段实施舷外标记的平地化堆焊,在中组立阶段和大组立阶段拼装后上门架。能有效降低焊接施工难度、减少作业步骤、有效控制作业精度以及保障施工安全,最终提升船舶建造的生产效率,有效解决在门架上立体作业困难的技术问题。
附图说明
22.为了更清楚地说明本技术实施例的技术方案,下面将对实施例中所需要使用的附图作简单地介绍,应当理解,以下附图仅示出了本技术的某些实施例,因此不应被看作是对范围的限定,对于本领域普通技术人员来讲,在不付出创造性劳动的前提下,还可以根据这些附图获得其他相关的附图。
23.图1为根据本技术实施例示出的一种船舶舷外标记戡划方法的第二分板的坡口结构示意图;
24.图2为根据本技术实施例示出的一种船舶舷外标记戡划方法的第四分板的坡口结构示意图;
25.图3为根据本技术实施例示出的一种船舶舷外标记戡划方法的第一分板的结构示意图;
26.图4为根据本技术实施例示出的一种船舶舷外标记戡划方法的第二分板的结构示意图;
27.图5为根据本技术实施例示出的一种船舶舷外标记戡划方法的第一分板与第二分板拼合后的结构示意图;
28.图6为根据本技术实施例示出的一种船舶舷外标记戡划方法的第三分板的结构示意图;
29.图7为根据本技术实施例示出的一种船舶舷外标记戡划方法的第四分板的结构示意图;
30.图8为根据本技术实施例示出的一种船舶舷外标记戡划方法的第三分板和第四分
板拼合后的结构示意图。
31.图9为图8中a
‑
a剖面图;
32.图10为根据本技术实施例示出的船舶外板的左视图;
33.图11为图10的纵剖面图;
34.图12为根据本技术实施例示出的一种船舶舷外标记戡划方法的流程图。
35.附图标记:
36.1、左舷外板字母的上半部分;2、左舷外板字母的下半部分;3、左舷外板字母;4、右舷外板字母的上半部分;5、右舷外板字母的下半部分;6、右舷外板字母。
具体实施方式
37.为使本技术实施例的目的、技术方案和优点更加清楚,下面将结合本技术实施例中的附图,对本技术实施例中的技术方案进行清楚、完整地描述,显然,所描述的实施例是本技术一部分实施例,而不是全部的实施例。通常在此处附图中描述和示出的本技术实施例的组件可以以各种不同的配置来布置和设计。
38.因此,以下对在附图中提供的本技术的实施例的详细描述并非旨在限制要求保护的本技术的范围,而是仅仅表示本技术的选定实施例。基于本技术中的实施例,本领域普通技术人员在没有作出创造性劳动前提下所获得的所有其他实施例,都属于本技术保护的范围。
39.图12为根据本技术实施例示出的一种船舶舷外标记戡划方法的流程图,参见图12,本技术提供了一种船舶舷外标记戡划方法,包括以下步骤:
40.s1,根据船舶外板中需勘划舷外标记的位置及预勘划舷外标记所覆盖的区域确定出船舶外板中需勘划的一块或多块分板。
41.s2,在需勘划的一块或多块分板上进行舷外标记勘划。
42.s3,在船舶的小组立阶段之前,完成对每块所述分板上对应舷外标记的施焊。
43.s4,在船舶的大组立阶段,分板上的舷外标记在船舶外板拼装完成后形成完整的舷外标记。
44.本发明根据船舶外板中需勘划舷外标记的位置及预勘划舷外标记所覆盖的区域确定出船舶外板中需勘划的一块或多块分板,在小组立阶段分别对各个分板上的舷外标记进行喷粉戡划后进行施焊,在中组立阶段将各个分板进行拼装后,形成完整的舷外标记,最后在大组立阶段将拼装好的船舶外板上门架。该方法取代了大分段上门架后施工作业人员拿涤纶纸朝天贴附分段外板来戡划船舶外板舷外标记字母和立体作业的仰视焊接法。能有效降低舷外标记的焊接施工难度、减少作业步骤、有效控制作业精度以及保障施工安全,最终提升船舶建造的生产效率,有效解决在门架上立体作业困难的技术问题。
45.在一种实施方案中,在步骤s2中,利用切割机的喷粉机构在每块分板上喷粉勘划出用于舷外标记定位的肋位线,将各肋位线作为纵坐标,将距基高度线作为横坐标。其中距基高度线为距基平面的高度线,依据肋位线及距基高度线在每个分板上勘划出舷外标记的外轮廓线。在对每个分板进行舷外标记戡划时,喷粉机构利用肋位线及距基高度线进行定位戡划,保证舷外标记的戡划精度。
46.在一种实施方案中,在步骤s3中,电焊作业人员在小组立阶段将每块分板分别放
置于地面或者平整区域进行舷外标记的平地化施焊,取代了大分段上门架后施工作业人员使用涤纶纸对舷外标记进行戡划并进行仰视焊接。平地化施焊优化了施工作业的环境,降低了施工难度,从而提高舷外标记戡划的精度。
47.在一种实施方案中,施焊方式选择堆焊,根据舷外标记的外轮廓线堆焊舷外标记,堆焊的宽度为5mm,高度为2.5mm。
48.在一种实施方案中,舷外标记包括直线部分和/或曲线部分。舷外标记直线部分的焊接长度l为100mm,间断空不焊长度s为500mm。舷外标记曲线部分的焊接长度l为50mm,间断空不焊长度s为100mm。
49.在一种实施方案中,舷外标记为字母、数字或图案。
50.在一种实施方案中,船舶外板的厚度为14.5mm。
51.在舷外标记的一种实施方案中,在舷外标记为字母、船舶外板包括左舷外板和右舷外板、左舷外板分为第一分板和第二分板、右舷外板分为第三分板和第四分板时,如图5和图8所示,将字母划分为左舷外板字母3和右舷外板字母6。如图3所示,左舷外板字母的上半部分1勘划在第一分板上,如图4所示,左舷外板字母的下半部分2勘划在第二分板上。如图6所示,右舷外板字母的上半部分4勘划在第三分板上,如图7所示,右舷外板字母的下半部分5勘划在第四分板上。
52.在一种实施方案中,如图3所示,第一分板为527分段,第一分板的高度范围为17685mm
‑
22500mm,长度为16800mm,第一分板上的肋位号由左往右依次为f181、f177、f173、f169。如图4所示,第二分板为427分段,第二分板的高度范围为14305mm
‑
17685mm,长度为16800mm,第二分板的肋位号由左往右依次为f183、f181、f177、f173、f169、f165。如图6所示,第三分板为537分段,第三分板的高度范围为17685mm
‑
22500mm,长度为16800mm,第一分段上的肋位号由左往右依次为f165、f169、f173、f177、f181。如图7所示,第四分板为437分段,第四分板的高度范围为14305mm
‑
17685mm,长度为16800mm。第四分板上的肋位号由左往右依次为f165、f169、f173、f177、f181、f183。
53.在一种实施方案中,利用切割机的切割机构将船舶外板切割为第一分板、第二分板、第三分板以及第四分板。
54.在一种实施方案中,图1为第二分段的坡口结构示意图,图2为第四分板的坡口结构示意图,如图1和图2所示,在切割时,第二分板和第四分板的坡口形式相同。第二分板和第四分板的上坡口均为v型坡口,坡口面角度为15
°
。第二分板和第四分板的下坡口均为工型坡口。
55.在一种实施方案中,根据上述各个分板尺寸信息切割时,均留出外框余量,切割机单板切割余量精准度为
±
1mm。
56.在一种实施方案中,利用切割机的喷粉机构,以肋位线作为纵坐标,以距基高度线作为横坐标。依据肋位线、距基高度线及定位信息,舷外标记定位信息的数据精准度为
±
0.01mm。在小组立阶段把各分板放平整后,电焊作业人员依据图3所示,在第一分板上喷粉勘划左舷外板的舷外标记的上半部分,电焊作业人员依据图4所示,在第二分板上喷粉勘划左舷外板的舷外标记的下半部分。电焊作业人员依据图6所示,在第三分板上喷粉勘划右舷外板的舷外标记的上半部分,电焊作业人员依据图7所示,在第四分板上喷粉勘划右舷外板的舷外标记的下半部分,切割机喷粉划线的精度为
±
0.5mm。
57.在一种实施方案中,根据图3、图4、图6及图7中戡划的外轮廓线,进行堆焊,堆焊精度为
±
2mm。
58.在一种实施方案中,施焊完成后,在中组立阶段对各分板进行组装,如图5所示,将第一分板和第二分板拼装成左舷外板。第一分板和所述第二分板之间采用陶瓷衬垫单面焊双面成型横焊,焊接时坡口之间的间隙为6mm。如图8和图9所示,将第三分板和第四分板拼装成右舷外板,第三分板和第四分板之间采用陶瓷衬垫单面焊双面成型横焊,图9中a处表示焊接时坡口之间的间隙,a为6mm。左舷外板以及右舷外板的底部均与下边水舱焊接,完成中组立阶段的拼装。第二分板与下边水舱之间、第四分板与下边水舱之间均采用无间隙焊接,图9中b处表示分板与下边水舱之间的间隙,b为0
‑
1mm。如图5所示,第一分板和第二分板拼装完成后形成完整的左舷外板的舷外标记。如图8所示,第三分板和第四分板拼装完成后形成完整的右舷外板的舷外标记。即437分段和537分段、427分段和527分段在总组区域进行总装合拢获得总段舷外标记。
59.在一种实施方案中,为了使舷外标记在中组立阶段能够准确拼合,因此中组立阶段的片段定位精度为
±
1mm。
60.在一种实施方案中,图10为根据本技术实施例示出的船舶外板的左视图,图11为图10的纵剖面图。参见图10和图11,在船舶的大组立阶段,将舷侧片段和下边水舱片段合拢成大分段,大组立阶段的合拢精度为
±
2mm。最后大分段上门架,总组合拢精度控制为
±
2mm。
61.本发明还提供了一种船舶外板,在船舶外板上设有舷外标记,舷外标记通过上述船舶舷外标记戡划方法进行戡划,提高了船舶外板在焊接施工过程的焊接精度,提高工作效率,保证施工安全。
62.本发明公开了一种船舶舷外标记戡划方法及船舶外板,实现了生产效率提升,降低施工作业难度,保障安全化生产的发展需求,更进一步推进船舶建造快速化领域奠定良好的基础。
63.本发明根据船舶外板中需勘划舷外标记的位置及预勘划舷外标记所覆盖的区域确定出船舶外板中需勘划的一块或多块分板,由切割机设备先对各分板进行喷粉戡划,在小组立阶段实施舷外标记的平地化堆焊,在中组立阶段和大组立阶段拼装后上门架。能有效降低焊接施工难度、减少作业步骤、有效控制作业精度以及保障施工安全,最终提升船舶建造的生产效率,有效解决在门架上立体作业困难的技术问题。
64.以上所述仅为本技术的优选实施例而已,并不用于限制本技术,对于本领域的技术人员来说,本技术可以有各种更改和变化。凡在本技术的精神和原则之内,所作的任何修改、等同替换、改进等,均应包含在本技术的保护范围之内。