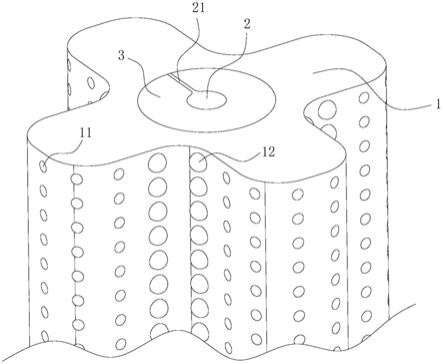
1.本发明属于纺织技术领域,具体的说是一种棉毛混纺纱面料及其制备方法。
背景技术:
2.现阶段,随着纺织行业的发展,单一纤维纺制的纯纺纺织品已经不能满足市场的需求。而且虽然有机棉和羊毛各自均具有许多优点,应用也很广泛,但是这两种纤维单独纺制而成的产品也存在一些不足。纯棉质地的纺织品吸湿性能良好,手感柔软,穿着舒适,洗涤方便,应用范围也最为广泛,但其抗皱性能较差,保暖性也不能满足消费者的需求。而毛质纺织品的弹性性能十分优异,保暖性和吸湿性均较好,然而价格昂贵,洗涤困难,而且紧贴皮肤时会产生刺痒和刺痛的感觉。但将有机棉纤维和羊毛进行混纺却可以使生产出的产品在结合两种纤维优点的同时弥补各自的不足。经纺制得到的混纺织物弹性相比于棉织物有明显的改善,不仅具有柔软触感、吸放湿好、环境友好等诸多优点,还具备了羊毛的强悬垂性,保暖性强等优良特性。而羊毛纤维与棉纤维进行混纺的一个很重要的关键问题就是纤维间的抱合力,纤维间的抱合力在很大程度上影响混纺纱的质量。
3.现有技术中也存在一些关于棉毛混纺纱面料的技术方案,如申请号为cn201610201306.2的中国专利公开了一种提高棉毛混纺纱纤维间抱合力的纺纱工艺,包括如下步骤:s1、将羊毛纤维置于温度为55℃~65℃,超声波功率为200w~230w的环境中超声处理;将棉纤维置于温度为60℃~80℃,超声波功率为230w~250w的环境中超声处理;s2、对所述步骤s1中超声处理后的羊毛纤维、棉纤维分别进行开棉工序、梳棉工序和并条工序;s3、对所述步骤s2中并合后的羊毛纤维与并合后的棉纤维进行混并工序、粗纱工序、细纱工序和络筒工序,得到棉毛混纺纱。该方案中在对羊毛纤维和棉纤维进行超声处理时,会在羊毛纤维和棉纤维的表面产生深浅不一、随机分布的坑穴,从而在纤维材料上形成了强力弱环,降低了纤维材料的强度。
技术实现要素:
4.为了弥补现有技术的不足,解决现有的棉毛混纺面料所存在的难以兼顾纤维间抱合力和纤维强度的缺陷的问题,本发明提出一种棉毛混纺纱面料及其制备方法。
5.本发明解决其技术问题所采用的技术方案是:本发明所述一种棉毛混纺纱面料,所述面料由棉毛混纺纱经过纺织制成;所述棉毛混纺纱由棉线与羊毛线混纺制得;所述棉毛混纺纱中棉线与羊毛线之间的比例为0.6-0.7:0.3-0.4;所述棉线由棉纤维与芳纶纤维混纺制成,且两者的比例为1:1;所述羊毛线由羊毛纤维与芳纶纤维混纺制成,且两者之间的比例为1:1;所述芳纶纤维为异形纤维,横截面呈十字形;
6.所述棉毛混纺纱面料的制备方法包括以下步骤:
7.s1:将棉纤维与芳纶纤维按照1:1的比例进行混纺,制得棉线;将羊毛纤维与芳纶纤维按照1:1的比例进行混纺,制得羊毛线;
8.s2:在s1步骤的基础上,将棉线与羊毛线按照0.6-0.7:0.3-0.4的比例进行混纺,
制得棉毛混纺纱;
9.s3:在s2步骤的基础上,将棉毛混纺纱按照常规方式进行纺织,制成成品面料;
10.所述s1步骤中的棉纤维与羊毛纤维使用蒸馏水中进行清洗,15~30min后取出沥干,并将沥干后的棉纤维与羊毛纤维分别使用微波进行干燥;所述s1步骤中的棉纤维与羊毛纤维干燥后分别进行混纺,制成棉线与羊毛线;
11.工作时,将棉纤维与芳纶纤维混纺制成棉线,将羊毛纤维与芳纶纤维混纺制成羊毛线,之后,将羊毛线与棉线混纺制成棉毛混纺纱并将其经过纺织后制成成品面料,同时,由于芳纶纤维是横截面呈十字形的异形纤维,因此,在棉纤维与芳纶纤维混纺并制成棉线的过程中,部分棉纤维将嵌入到芳纶纤维表面的沟槽中,从而提升棉纤维与芳纶纤维之间的抱合力,降低棉线在制成面料并使用的过程中出现散开、分离的可能,同时,通过芳纶纤维的特性,能够有效的提升棉线的强度,降低棉线断裂的可能,进而提升制备得到的面料的强度性能;
12.同时,羊毛纤维与芳纶纤维混纺并制成羊毛纤维的过程中,部分羊毛纤维嵌入到芳纶纤维表面的沟槽中,提升羊毛纤维与芳纶纤维之间的抱合力,避免在使用过程中羊毛纤维与芳纶纤维之间出现散开、分离的可能性,同时,通过芳纶纤维的特性能够有效的提升羊毛纤维的强度,降低羊毛线断裂的可能,提升制备得到的面料的强度性能;
13.同时,将棉纤维与羊毛纤维分别制成棉线与羊毛线后再进行混纺得到棉毛混纺纱,由于棉线相对棉纤维较粗,羊毛线相对羊毛较粗,在棉线与羊毛线进行混纺的过程中,两者之间的接触面积相对较大,从而提升棉线与羊毛线之间的摩擦力,使混纺后得到的棉毛混纺纱内的纱线抱合力较大,降低使用过程中棉毛混纺纱散开、分离的可能,保证棉毛混纺纱的结构稳定,提升制备得到的面料的强度性能;
14.同时,通过使用芳纶纤维进行混纺分别制成棉线与羊毛线,提升纱线内部的纤维之间的抱合力,能够避免对棉纤维和羊毛纤维表面进行处理并在两者的表面生成深浅不一、随机分布的坑穴,在纤维材料上形成了强力弱环,影响到纤维材料的强度。
15.优选的,所述芳纶纤维在制备过程中向熔体状态的芳纶原料中均匀添加有磁粉微粒;所述磁粉微粒在芳纶纤维中的添加量为1.5wt%-2wt%;所述磁粉微粒的材质为三氧化二铁、二氧化铬、金属磁粉与钡铁氧体中的任意一种;所述磁性颗粒的表面包覆有一层聚四氟乙烯涂层;所述磁性颗粒具有磁性,且不同磁性颗粒之间存在相互吸引的磁力;
16.工作时,由于芳纶纤维中均匀混入有磁粉微粒,且不同的磁粉微粒之间存在相互吸引的磁力,因此,面料中的不同的芳纶纤维之间同样存在相互吸引的磁力,同时,棉纤维和羊毛纤维分别与芳纶纤维混纺得到棉线和羊毛线,因此,在使用羊毛线与棉线混纺制成棉毛混纺纱后,棉毛混纺纱内部的棉线与羊毛线受自身存在的芳纶纤维的影响,相互之间存在吸引力,提升棉线与羊毛线之间的摩擦力,从而进一步提高棉毛混纺纱内部的棉线与羊毛线之间的抱合力,降低棉毛混纺纱在使用过程中出现散开、分离的可能性,提升制备得到的面料的强度。
17.优选的,所述芳纶纤维在制备过程中向熔体状态的芳纶原料中均匀添加有三氧化二铝微粒;所述三氧化二铝微粒在芳纶纤维中的添加量为2.5wt%-3.5wt%;所述芳纶纤维的中间位置存在通孔,即芳纶纤维为中空纤维;
18.所述芳纶纤维在混纺前,对芳纶纤维使用稀盐酸进行洗涤10-15min;所述芳纶纤
维洗涤使用稀盐酸洗涤完成后,将芳纶纤维使用蒸馏水中进行清洗,15-30min后取出沥干,并将沥干后芳纶纤维使用微波进行干燥;
19.工作时,由于芳纶纤维在纺纱过程中均匀混入三氧化二铝微粒,使用稀盐酸对芳纶纤维进行洗涤时,芳纶纤维中混入的三氧化二铝微粒在接触到稀盐酸后两者之间发生反应,产生溶解,在芳纶纤维中的三氧化二铝微粒溶解后,芳纶纤维的表面出现随机分布的微坑,同时,在芳纶纤维的表面与中间通孔之间的侧壁厚度较薄的区域,芳纶纤维表面的产生微孔,使芳纶纤维的表面与中间的通孔保持连通;同时,由于磁性颗粒的表面包覆有一层聚四氟乙烯涂层,能够避免磁性颗粒与稀盐酸接触并发生反应,导致磁性颗粒出现损失,影响到芳纶纤维之间存在的磁性吸引力的存在;
20.同时,芳纶纤维在使用稀盐酸洗涤后,芳纶纤维的表面产生微坑或者微孔,提高芳纶芳纶的表面粗糙度,使芳纶纤维与棉纤维、芳纶纤维与羊毛纤维之间的抱合力提高,降低混纺得到的棉线与羊毛线出现散开、分离的可能性,同时,通过在芳纶纤维表面生成的微孔与微孔,能够提升中空芳纶纤维的透气性与柔软性,从而提高制备得到的面料的手感,从而提高使用者的使用体验。
21.优选的,所述芳纶纤维干燥后,将芳纶纤维浸入到盛装有液态的硅胶的容器中;所述芳纶纤维在容器中的浸泡时间为15-30min;所述芳纶纤维在浸泡的过程中,对容器进行加压;所述容器在加压时,容器内部压力为0.2-0.3mpa;所述芳纶纤维浸泡完成后,对芳纶纤维使用微波进行干燥;所述液态的硅胶中通过搅拌的方式均匀混入药剂,且药剂在液态的硅胶中的比例为10-15wt%;所述药剂包括抗菌剂与防虫剂,且两者在药剂中的比例为1:1;
22.工作时,将芳纶纤维浸入到盛装有液态的硅胶的容器中,并向容器中加压至0.2-0.3mpa,能够促进容器中的液态的硅胶进入到芳纶纤维内的通孔中,同时,由于芳纶纤维使用稀盐酸洗涤后,芳纶纤维表面出现连通器内部的通孔的微孔后,芳纶纤维浸入到液态的硅胶中之后,芳纶纤维上的微孔能够便于液态的硅胶进入到通孔中,从而加快芳纶纤维内的通孔中填充液态的硅胶的速度,缩短芳纶纤维在液态的硅胶中浸泡处理的时间,加快处理效率,同时,芳纶纤维在液态的硅胶中浸泡完成后,使用微波方式进行干燥,能够提高芳纶纤维中填充的液态的硅胶固化的速度以及固化的一致性;
23.同时,由于硅胶中均匀混入有药剂,能够通过药剂的作用,提升面料在使用过程中的抗菌与防虫性能,提升使用者在使用过程中的使用体验,同时,由于含有药剂的硅胶填充在芳纶纤维内的通孔中,在使用芳纶纤维进行混纺并制备成棉线与羊毛线后,能够有效的提高要药剂在面料中的均匀程度,防止药剂在面料中分布不均,引起面料内的部分区域滋生细菌或者受到虫害,同时,通过将硅胶填充到芳纶纤维的通孔中,能够有效的控制药剂的释放速度以及降低药剂受到摩擦后的流失速度,从而延长面料上的抗菌与防虫性能持续时间。
24.优选的,所述芳纶纤维在制备过程中,通过共轭复合纺丝法在其通孔中生成膨胀体;所述膨胀体与芳纶纤维中的通孔内壁之间通过连接片进行连接;所述膨胀体的横截面呈圆形,且膨胀体不与通孔内壁直接接触;所述膨胀体由聚氯乙烯制成;所述连接片的材质为聚氯乙烯与芳纶的混合体;
25.工作时,芳纶纤维在液态的硅胶中浸泡完成后,使用微波方式进行干燥的过程中,
由于微波的作用,芳纶纤维以及其内部的聚氯乙烯膨胀体的温度均升高,同时,由于芳纶纤维材料的热膨胀系数小于膨胀体材料聚氯乙烯的热膨胀系数,因此,在微波干燥并引起温度升高时,芳纶纤维受热后膨胀的体积小于膨胀体受热膨胀后的体积,因此,膨胀后的膨胀体对通孔内存在硅胶产生挤压,促使通孔中的硅胶通过芳纶纤维表面的微孔溢出,在芳纶纤维表面的微孔处固化形成凸起,提高通孔中的硅胶与芳纶纤维之间的结合强度,防止通孔中的硅胶在使用过程中出现流失,影响到硅胶中的药剂的含量,同时,在芳纶纤维表面溢出的硅胶固化后形成的凸起能够在混纺过程中提升芳纶纤维与棉纤维、芳纶纤维与羊毛纤维之间的摩擦力增加,提升芳纶纤维与棉纤维、芳纶纤维与羊毛纤维之间的抱合力,降低棉线与羊毛线在使用过程中出现散开、分离的可能性。
26.一种棉毛混纺纱面料制备方法,所述制备方法适用于上述所述的一种棉毛混纺纱面料;所述制备方法包括以下步骤:
27.a1:将棉纤维与芳纶纤维按照1:1的比例进行混纺,制得棉线;将羊毛纤维与芳纶纤维按照1:1的比例进行混纺,制得羊毛线;
28.a2:在a1步骤的基础上,将棉线与羊毛线按照0.6-0.7:0.3-0.4的比例进行混纺,制得棉毛混纺纱;
29.a3:在a2步骤的基础上,将棉毛混纺纱按照常规方式进行纺织,制成成品面料。
30.本发明的有益效果如下:
31.1.本发明所述一种棉毛混纺纱面料及其制备方法,通过使用棉纤维和羊毛纤维分别与横截面呈十字形的芳纶纤维混纺制得棉线与羊毛线,之后再使棉线与羊毛线混纺制备得到棉毛混纺纱并通过棉毛混纺纱经过纺织得到成品的面料,由于棉纤维和羊毛纤维分别与芳纶纤维混纺,因此,棉线中存在部分棉纤维嵌入到芳纶纤维表面的沟槽中,羊毛线中存在部分羊毛纤维嵌入到芳纶纤维表面的沟槽中,从而有效的提升棉线与羊毛线内部的纤维之间的摩擦力,进而使纤维之间的抱合力良好,降低纱线出现散开、分离的可能性,同时,均匀混入到芳纶纤维中的磁性颗粒,使混纺有芳纶纤维的棉线与羊毛线之间存在相互吸引的磁力,从而进一步提升面料中的各纤维之间的抱合力,降低纱线出现散开、分离的可能性,提高面料的强度。
32.2.本发明所述一种棉毛混纺纱面料及其制备方法,通过共轭复合纺丝法在芳纶纤维内的通孔中生成由聚氯乙烯材料制成的膨胀体,同时,在芳纶纤维内的通孔中填充含有药剂的硅胶,在芳纶纤维浸泡硅胶完成后使用微波干燥的过程中,膨胀体发生膨胀,使通孔中的硅胶从芳纶纤维表面的微孔中溢出并固化形成凸起,同时,芳纶纤维表面的凸起能够进一步提升混纺过程中纤维之间的摩擦力,使芳纶纤维混纺时的纤维之间的抱合力良好,降低纱线出现散开、分离的可能性。
33.3.本发明所述一种棉毛混纺纱面料及其制备方法,通过横截面呈十字形的芳纶纤维、芳纶纤维中填充的磁性颗粒以及芳纶纤维表面的凸起,提升与芳纶纤维进行混纺的纤维之间的抱合力,避免对棉纤维和羊毛纤维表面进行处理并在两者的表面生成深浅不一、随机分布的坑穴,在纤维材料上形成了强力弱环,影响到纤维材料的强度。
附图说明
34.下面结合附图对本发明作进一步说明。
35.图1是本发明的面料中使用的芳纶纤维的结构示意图;
36.图2是本发明的面料的制备方法流程图;
37.图中:芳纶纤维1、微坑11、凸起12、膨胀体2、连接片21、硅胶3。
具体实施方式
38.为了使本发明实现的技术手段、创作特征、达成目的与功效易于明白了解,下面结合具体实施方式,进一步阐述本发明。
39.如图1和图2所示,本发明所述一种棉毛混纺纱面料,所述面料由棉毛混纺纱经过纺织制成;所述棉毛混纺纱由棉线与羊毛线混纺制得;所述棉毛混纺纱中棉线与羊毛线之间的比例为0.6-0.7:0.3-0.4;所述棉线由棉纤维与芳纶纤维1混纺制成,且两者的比例为1:1;所述羊毛线由羊毛纤维与芳纶纤维1混纺制成,且两者之间的比例为1:1;所述芳纶纤维1为异形纤维,横截面呈十字形;
40.所述棉毛混纺纱面料的制备方法包括以下步骤:
41.s1:将棉纤维与芳纶纤维1按照1:1的比例进行混纺,制得棉线;将羊毛纤维与芳纶纤维1按照1:1的比例进行混纺,制得羊毛线;
42.s2:在s1步骤的基础上,将棉线与羊毛线按照0.6-0.7:0.3-0.4的比例进行混纺,制得棉毛混纺纱;
43.s3:在s2步骤的基础上,将棉毛混纺纱按照常规方式进行纺织,制成成品面料;
44.所述s1步骤中的棉纤维与羊毛纤维使用蒸馏水中进行清洗,15~30min后取出沥干,并将沥干后的棉纤维与羊毛纤维分别使用微波进行干燥;所述s1步骤中的棉纤维与羊毛纤维干燥后分别进行混纺,制成棉线与羊毛线;
45.工作时,将棉纤维与芳纶纤维1混纺制成棉线,将羊毛纤维与芳纶纤维1混纺制成羊毛线,之后,将羊毛线与棉线混纺制成棉毛混纺纱并将其经过纺织后制成成品面料,同时,由于芳纶纤维1是横截面呈十字形的异形纤维,因此,在棉纤维与芳纶纤维1混纺并制成棉线的过程中,部分棉纤维将嵌入到芳纶纤维1表面的沟槽中,从而提升棉纤维与芳纶纤维1之间的抱合力,降低棉线在制成面料并使用的过程中出现散开、分离的可能,同时,通过芳纶纤维1的特性,能够有效的提升棉线的强度,降低棉线断裂的可能,进而提升制备得到的面料的强度性能;
46.同时,羊毛纤维与芳纶纤维1混纺并制成羊毛纤维的过程中,部分羊毛纤维嵌入到芳纶纤维1表面的沟槽中,提升羊毛纤维与芳纶纤维1之间的抱合力,避免在使用过程中羊毛纤维与芳纶纤维1之间出现散开、分离的可能性,同时,通过芳纶纤维1的特性能够有效的提升羊毛纤维的强度,降低羊毛线断裂的可能,提升制备得到的面料的强度性能;
47.同时,将棉纤维与羊毛纤维分别制成棉线与羊毛线后再进行混纺得到棉毛混纺纱,由于棉线相对棉纤维较粗,羊毛线相对羊毛较粗,在棉线与羊毛线进行混纺的过程中,两者之间的接触面积相对较大,从而提升棉线与羊毛线之间的摩擦力,使混纺后得到的棉毛混纺纱内的纱线抱合力较大,降低使用过程中棉毛混纺纱散开、分离的可能,保证棉毛混纺纱的结构稳定,提升制备得到的面料的强度性能;
48.同时,通过使用芳纶纤维1进行混纺分别制成棉线与羊毛线,提升纱线内部的纤维之间的抱合力,能够避免对棉纤维和羊毛纤维表面进行处理并在两者的表面生成深浅不
一、随机分布的坑穴,在纤维材料上形成了强力弱环,影响到纤维材料的强度。
49.作为本发明一种实施方式,所述芳纶纤维1在制备过程中向熔体状态的芳纶原料中均匀添加有磁粉微粒;所述磁粉微粒在芳纶纤维1中的添加量为1.5wt%-2wt%;所述磁粉微粒的材质为三氧化二铁、二氧化铬、金属磁粉与钡铁氧体中的任意一种;所述磁性颗粒的表面包覆有一层聚四氟乙烯涂层;所述磁性颗粒具有磁性,且不同磁性颗粒之间存在相互吸引的磁力;
50.工作时,由于芳纶纤维1中均匀混入有磁粉微粒,且不同的磁粉微粒之间存在相互吸引的磁力,因此,面料中的不同的芳纶纤维1之间同样存在相互吸引的磁力,同时,棉纤维和羊毛纤维分别与芳纶纤维1混纺得到棉线和羊毛线,因此,在使用羊毛线与棉线混纺制成棉毛混纺纱后,棉毛混纺纱内部的棉线与羊毛线受自身存在的芳纶纤维1的影响,相互之间存在吸引力,提升棉线与羊毛线之间的摩擦力,从而进一步提高棉毛混纺纱内部的棉线与羊毛线之间的抱合力,降低棉毛混纺纱在使用过程中出现散开、分离的可能性,提升制备得到的面料的强度。
51.作为本发明一种实施方式,所述芳纶纤维1在制备过程中向熔体状态的芳纶原料中均匀添加有三氧化二铝微粒;所述三氧化二铝微粒在芳纶纤维1中的添加量为2.5wt%-3.5wt%;所述芳纶纤维1的中间位置存在通孔,即芳纶纤维1为中空纤维;
52.所述芳纶纤维1在混纺前,对芳纶纤维1使用稀盐酸进行洗涤10-15min;所述芳纶纤维1洗涤使用稀盐酸洗涤完成后,将芳纶纤维1使用蒸馏水中进行清洗,15-30min后取出沥干,并将沥干后芳纶纤维1使用微波进行干燥;
53.工作时,由于芳纶纤维1在纺纱过程中均匀混入三氧化二铝微粒,使用稀盐酸对芳纶纤维1进行洗涤时,芳纶纤维1中混入的三氧化二铝微粒在接触到稀盐酸后两者之间发生反应,产生溶解,在芳纶纤维1中的三氧化二铝微粒溶解后,芳纶纤维1的表面出现随机分布的微坑11,同时,在芳纶纤维1的表面与中间通孔之间的侧壁厚度较薄的区域,芳纶纤维1表面的产生微孔,使芳纶纤维1的表面与中间的通孔保持连通;同时,由于磁性颗粒的表面包覆有一层聚四氟乙烯涂层,能够避免磁性颗粒与稀盐酸接触并发生反应,导致磁性颗粒出现损失,影响到芳纶纤维1之间存在的磁性吸引力的存在;
54.同时,芳纶纤维1在使用稀盐酸洗涤后,芳纶纤维1的表面产生微坑11或者微孔,提高芳纶芳纶的表面粗糙度,使芳纶纤维1与棉纤维、芳纶纤维1与羊毛纤维之间的抱合力提高,降低混纺得到的棉线与羊毛线出现散开、分离的可能性,同时,通过在芳纶纤维1表面生成的微孔与微孔,能够提升中空芳纶纤维1的透气性与柔软性,从而提高制备得到的面料的手感,从而提高使用者的使用体验。
55.作为本发明一种实施方式,所述芳纶纤维1干燥后,将芳纶纤维1浸入到盛装有液态的硅胶3的容器中;所述芳纶纤维1在容器中的浸泡时间为15-30min;所述芳纶纤维1在浸泡的过程中,对容器进行加压;所述容器在加压时,容器内部压力为0.2-0.3mpa;所述芳纶纤维1浸泡完成后,对芳纶纤维1使用微波进行干燥;所述液态的硅胶3中通过搅拌的方式均匀混入药剂,且药剂在液态的硅胶3中的比例为10-15wt%;所述药剂包括抗菌剂与防虫剂,且两者在药剂中的比例为1:1;
56.工作时,将芳纶纤维1浸入到盛装有液态的硅胶3的容器中,并向容器中加压至0.2-0.3mpa,能够促进容器中的液态的硅胶3进入到芳纶纤维1内的通孔中,同时,由于芳纶
纤维1使用稀盐酸洗涤后,芳纶纤维1表面出现连通器内部的通孔的微孔后,芳纶纤维1浸入到液态的硅胶3中之后,芳纶纤维1上的微孔能够便于液态的硅胶3进入到通孔中,从而加快芳纶纤维1内的通孔中填充液态的硅胶3的速度,缩短芳纶纤维1在液态的硅胶3中浸泡处理的时间,加快处理效率,同时,芳纶纤维1在液态的硅胶3中浸泡完成后,使用微波方式进行干燥,能够提高芳纶纤维1中填充的液态的硅胶3固化的速度以及固化的一致性;
57.同时,由于硅胶3中均匀混入有药剂,能够通过药剂的作用,提升面料在使用过程中的抗菌与防虫性能,提升使用者在使用过程中的使用体验,同时,由于含有药剂的硅胶3填充在芳纶纤维1内的通孔中,在使用芳纶纤维1进行混纺并制备成棉线与羊毛线后,能够有效的提高要药剂在面料中的均匀程度,防止药剂在面料中分布不均,引起面料内的部分区域滋生细菌或者受到虫害,同时,通过将硅胶3填充到芳纶纤维1的通孔中,能够有效的控制药剂的释放速度以及降低药剂受到摩擦后的流失速度,从而延长面料上的抗菌与防虫性能持续时间。
58.作为本发明一种实施方式,所述芳纶纤维1在制备过程中,通过共轭复合纺丝法在其通孔中生成膨胀体2;所述膨胀体2与芳纶纤维1中的通孔内壁之间通过连接片21进行连接;所述膨胀体2的横截面呈圆形,且膨胀体2不与通孔内壁直接接触;所述膨胀体2由聚氯乙烯制成;所述连接片21的材质为聚氯乙烯与芳纶的混合体;
59.工作时,芳纶纤维1在液态的硅胶3中浸泡完成后,使用微波方式进行干燥的过程中,由于微波的作用,芳纶纤维1以及其内部的聚氯乙烯膨胀体2的温度均升高,同时,由于芳纶纤维1材料的热膨胀系数小于膨胀体2材料聚氯乙烯的热膨胀系数,因此,在微波干燥并引起温度升高时,芳纶纤维1受热后膨胀的体积小于膨胀体2受热膨胀后的体积,因此,膨胀后的膨胀体2对通孔内存在硅胶3产生挤压,促使通孔中的硅胶3通过芳纶纤维1表面的微孔溢出,在芳纶纤维1表面的微孔处固化形成凸起12,提高通孔中的硅胶3与芳纶纤维1之间的结合强度,防止通孔中的硅胶3在使用过程中出现流失,影响到硅胶3中的药剂的含量,同时,在芳纶纤维1表面溢出的硅胶3固化后形成的凸起12能够在混纺过程中提升芳纶纤维1与棉纤维、芳纶纤维1与羊毛纤维之间的摩擦力增加,提升芳纶纤维1与棉纤维、芳纶纤维1与羊毛纤维之间的抱合力,降低棉线与羊毛线在使用过程中出现散开、分离的可能性。
60.一种棉毛混纺纱面料制备方法,所述制备方法适用于上述所述的一种棉毛混纺纱面料;所述制备方法包括以下步骤:
61.a1:将棉纤维与芳纶纤维1按照1:1的比例进行混纺,制得棉线;将羊毛纤维与芳纶纤维1按照1:1的比例进行混纺,制得羊毛线;
62.a2:在a1步骤的基础上,将棉线与羊毛线按照0.6-0.7:0.3-0.4的比例进行混纺,制得棉毛混纺纱;
63.a3:在a2步骤的基础上,将棉毛混纺纱按照常规方式进行纺织,制成成品面料。
64.具体工作流程如下:
65.工作时,将棉纤维与芳纶纤维1混纺制成棉线,将羊毛纤维与芳纶纤维1混纺制成羊毛线,之后,将羊毛线与棉线混纺制成棉毛混纺纱并将其经过纺织后制成成品面料,同时,由于芳纶纤维1是横截面呈十字形的异形纤维,因此,在棉纤维与芳纶纤维1混纺并制成棉线的过程中,部分棉纤维将嵌入到芳纶纤维1表面的沟槽中,同时,羊毛纤维与芳纶纤维1混纺并制成羊毛纤维的过程中,部分羊毛纤维嵌入到芳纶纤维1表面的沟槽中;芳纶纤维1
15min,之后使用清水洗涤15-30min;所述芳纶纤维干燥后,将芳纶纤维浸入到液态的硅胶中15-30min,浸泡完成后使用微波干燥;所述液态的硅胶中含有10-15wt%的由抗菌剂和防虫剂混合组成的药剂;所述芳纶纤维经过上述处理后,再用于混纺,并最终制备得到棉毛混纺纱线,且棉毛混纺纱线细度为33tex,捻度为64.5捻/10cm。
74.经测试,本实施例制得的棉毛混纺纱的断裂强力为301.4n,断裂伸长率为5.52%。
75.实施例二:
76.本实施例提供了一种棉毛混纺纱面料及其制备方法,所述制备方法与实施例一中的制备方法一致,仅改变制备得到的芳纶纤维的横截面的形状:在本实施例中的芳纶纤维的横截面呈圆形;本实施例中并最终制备得到的棉毛混纺纱线细度为32tex,捻度为62.0捻/10cm。
77.经测试,本实施例制得的棉毛混纺纱的断裂强力为296.2n,断裂伸长率为5.71%。
78.实施例三:
79.本实施例提供了一种棉毛混纺纱面料及其制备方法,所述制备方法与实施例一中的制备方法一致,仅对芳纶纤维制备过程中的添加原料进行改变:本实施例中的芳纶纤维在制备过程中仅均匀混入磁性颗粒;本实施例中制备得到的芳纶纤维不使用稀盐酸进行洗涤;本实施例中并最终制备得到的棉毛混纺纱线细度为33tex,捻度为63.5捻/10cm。
80.经测试,本实施例制得的棉毛混纺纱的断裂强力为298.9n,断裂伸长率为5.65%。
81.实施例四:
82.本实施例提供了一种棉毛混纺纱面料及其制备方法,所述制备方法与实施例一中的制备方法一致,仅对芳纶纤维制备过程中的添加原料进行改变:本实施例中的芳纶纤维在制备过程中仅均匀混入三氧化二铝微粒;本实施例中并最终制备得到的棉毛混纺纱线细度为33tex,捻度为64.5捻/10cm。
83.经测试,本实施例制得的棉毛混纺纱的断裂强力为294.8n,断裂伸长率为5.68%。
84.实施例五:
85.本实施例提供了一种棉毛混纺纱面料及其制备方法,所述制备方法与实施例一中的制备方法一致,仅对制备得到的芳纶纤维进行改变:在芳纶纤维制备过程中,不同过共轭复合纺丝法在芳纶纤维内的通孔中生成膨胀体;本实施例中并最终制备得到的棉毛混纺纱线细度为28.5tex,捻度为60.5捻/10cm。
86.经测试,本实施例制得的棉毛混纺纱的断裂强力为297.6n,断裂伸长率为5.67%。
87.实施例六:
88.本实施例提供了一种棉毛混纺纱面料及其制备方法,所述制备方法与实施例一中的制备方法一致,仅对芳纶纤维制备过程中的添加原料进行改变:本实施例中的芳纶纤维在制备过程中不添加磁性颗粒与三氧化二铝微粒;本实施例中制备得到的芳纶纤维不适用稀盐酸进行洗涤;本实施例中并最终制备得到的棉毛混纺纱线细度为31tex,捻度为62.5捻/10cm。
89.经测试,本实施例制得的棉毛混纺纱的断裂强力为295.3n,断裂伸长率为5.85%,即本发明制备得到的棉毛混纺纱相对于普通方式制备得到的棉毛混纺纱的性能具有较大的提高,性能更好,同时,由于本发明的制备得到的面料通过棉毛混纺纱经过纺织得到,因此,本发明制备得到的面料相对与普通的棉毛混纺纱制备得到的面料同样在性能上更佳。
90.以上显示和描述了本发明的基本原理、主要特征和优点。本行业的技术人员应该了解,本发明不受上述实施例的限制,上述实施例和说明书中描述的只是说明本发明的原理,在不脱离本发明精神和范围的前提下,本发明还会有各种变化和改进,这些变化和改进都落入要求保护的本发明范围内。本发明要求保护范围由所附的权利要求书及其等效物界定。