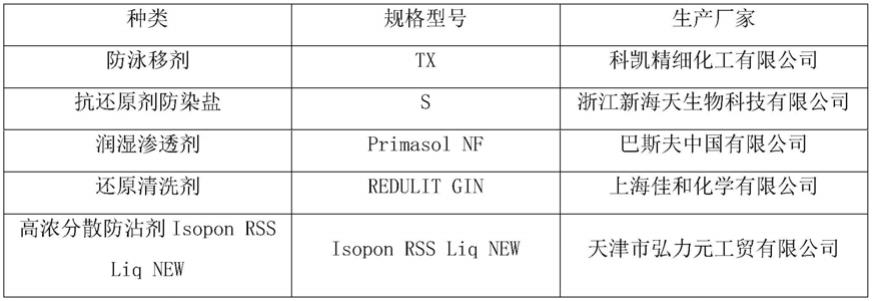
1.本发明涉及改善深色面料皂洗溶液牢度的工艺技术领域,具体涉及一种改善纤维素纤维与涤混纺的深色面料皂洗溶液牢度的工艺。
背景技术:
2.纤维素纤维包括天然纤维素纤维,如棉;还包括再生纤维素纤维,如竹黏胶纤维,莫代尔等。纤维素纤维与涤纶的混纺织物兼具了纤维素纤维良好的透气性、吸水性、舒适性、悬垂性和柔和光泽以及涤纶的强度好,滑爽挺括、易洗快干等优点,被广泛应用在纺织织物中。但是,深色面料存在着皂洗溶液牢度较差,难以达到客户标准的问题,这就阻挠了深色面料的加工与推广。
3.目前,为改善这一问题,染厂通过调整染色工艺,加强皂洗,同时在后整理拉幅时加入固色剂来进一步改善,但是对功能性整理的面料,如无氟防水整理,后整理加入固色剂后将大大降低面料的防水性,仅仅通过加强皂洗,甚至高温皂洗,织物的皂洗溶液牢度仍得不到改善,这给染整加工带来了困难。
4.cn103290668a专利公开了一种高耐皂洗色牢度和高升华牢度涤纶织物处理方法,织物染色后进行还原洗,在染色机上按还原清洗剂与织物的质量比为10-15:1的比例在每升水中加入浓度为30%的烧碱1.5
±
0.5g、二氧化硫脲1.0
±
0.5g、环氧乙烷缩合1.0
±
0.5g、烷基磺酸钠1.0
±
0.5g组成的碱性还原清洗剂,在100
±
5℃温度下还原洗30
±
2min,经水洗后,在120
±
5℃烘干。还原清洗溶液组成复杂,采用浸染方式,耗时长,效率低,对织物皂洗溶液牢度的改善较小。
5.cn106192487a专利公开了一种提高涤氨针织物皂洗色牢度的制备工艺,包括染色、还原洗、热水洗、冷水洗、酸洗、冷水洗,还原洗的工艺为将染色后的涤氨针织物取出放入40-50℃的水中,并放入2.5g/l的dm-41557的还原清洗剂,将温度升至75~90℃,再恒温20min,之后再降温处理。此工艺非常复杂,采用浸染方式,耗时长,效率低,经过热洗冷洗后的织物的皂洗溶液牢度难以改善。
6.cn113502666a专利公开了一种再生涤纶织物的高色牢度染整工艺,包括织物预处理制得初级涤纶织物,然后漂白消毒水洗,再干燥后制得次级涤纶织物,之后进行一次上色,再进行除菌去味,将一次上色的次级涤纶织物浸泡在盛满除菌剂微胶囊的除菌缸内,浸泡20分钟后加入适量的植物天然香料,最后取出水洗并干燥,然后进行二次上色,通过高压染料携带者微胶囊冲击次级涤纶织物,进行二次上色,最后进行干燥定型,需要两次对坯布进行上色,工艺繁琐,虽然所制得的再生涤纶的成品的摩擦色牢度较高,但是皂洗溶液牢度依然得不到改善,尤其是深色面料。
技术实现要素:
7.本发明要解决的技术问题是提供一种改善纤维素纤维与涤混纺的深色面料皂洗溶液牢度的工艺,解决了传统工艺中出现的深色面料皂洗溶液牢度不合格的问题,工艺简
单,节水减排,耗时短,效率高。
8.本发明所述的改善纤维素纤维与涤混纺的深色面料皂洗溶液牢度的工艺:将经过预处理的织物浸轧活性染液,浸轧后预烘,再浸轧活性固色液,然后汽蒸
→
水洗
→
还原清洗剂清洗
→
皂洗
→
水洗
→
烘干。
9.优选地,改善纤维素纤维与涤混纺的深色面料皂洗溶液牢度的工艺,包括以下步骤:
10.(1)织物预处理:将织物依次经过烧毛、冷堆、煮练、干定型、丝光、浸轧分散染料、烘干、焙烘、分散固色;
11.(2)活性染色:进行活性染液浸轧,三段预烘;
12.(3)活性固色:浸轧活性固色液;
13.(4)汽蒸、水洗:汽蒸温度为100~102℃,时间为1.5~2min;
14.(5)还原清洗剂清洗:在还原清洗剂中清洗75-100s,并调节ph为8~9,调节温度为90~95℃;
15.(6)皂洗、水洗:在皂洗剂溶液皂洗75~100s,水温为90~100℃;
16.(7)烘干。
17.优选地,活性染液包括染料和防泳移剂,染料为活性红、活性黄、活性蓝中的一种或者多种。
18.优选地,活性固色液包括:烧碱8~12g/l,纯碱25~30g/l,元明粉200~230g/l,抗还原剂防染盐2~5g/l,润湿渗透剂2~5g/l。
19.优选地,步骤(2)中的三段式预烘,第一段烘房的温度为80~100℃,循环风为40~80%,排风为60~70%;第二段烘房的温度为80~110℃,循环风为40~80%,排风为60~70%;第三段烘房的温度为80~110℃,循环风为40~80%,排风为50~60%。
20.优选地,还原清洗剂为还原清洗剂gin,浓度为8~10g/l。
21.优选地,还原清洗剂清洗步骤中调节ph的试剂为氢氧化钠。
22.优选地,步骤(4)到步骤(6)的车速为40~50m/min。
23.优选地,皂洗剂为高浓分散防沾皂洗剂isopon rss liq new,浓度为2~3g/l。
24.具体地,改善纤维素纤维与涤混纺的深色面料皂洗溶液牢度的工艺,包括以下步骤:
25.(1)织物预处理:将织物依次经过烧毛、冷堆、煮练、干定型、丝光、浸轧分散染料、烘干、焙烘、分散固色;
26.(2)活性染色:将织物在染色机上进行染液浸轧,浸轧方式为两浸两轧,三组温度进行烘干,其中,第一组烘房的温度为80~100℃,循环风为40~80%,排风为60~70%,第二组烘房的温度为80~110℃,循环风为40~80%,排风为60~70%,第三组烘房的温度为80~110℃,循环风为40~80%,排风为50~60%;
27.(3)活性固色:浸轧活性固色液,为烧碱8~12g/l,纯碱25~30g/l,元明粉200~230g/l,抗还原剂防染盐2~5g/l,润湿渗透剂2~5g/l,车速为40~50m/min;
28.(4)汽蒸、水洗:汽蒸温度为95~102℃,时间为1.5~2min;
29.(5)还原清洗剂清洗:在浓度为8~10g/l的还原清洗剂gin中清洗75-100s,用氢氧化钠调节ph为8~9,调节温度为90~95℃;
30.(6)皂洗、水洗:在浓度为2~3g/l的高浓分散防沾皂洗剂isopon rss liq new溶液中皂洗75~100s,水温为90~100℃,车速为40~50m/min;
31.(7)烘干。
32.上述步骤(5)和步骤(6)共九节水洗槽,依次为1#-9#水洗槽,2#和3#水洗槽为还原清洗剂溶液,5#和6#水洗槽为皂洗剂溶液,8#水洗槽为酸溶液,其他水洗槽为清水。
33.本发明所述的改善纤维素纤维与涤混纺的深色面料皂洗溶液牢度的工艺,包括将已经染完涤的面料浸轧活性染液,浸轧后预烘,再浸轧活性染料的固色液,然后经过在汽蒸箱中汽蒸、水洗、还原清洗剂清洗、皂洗、水洗,烘干后完成,采用在活性固色时的还原清洗槽中加入还原清洗剂gin,naoh溶液调节ph值为8~9,温度为90~95℃的条件下,还原清洗剂gin所产生的氧化还原电位足以破坏分散染料,但不足以破坏活性染料,在其较强的分散能力下,纤维表面吸附的未固着的分散染料被破坏后,其降解产物会被很好的分散在处理浴中,不会回沾在布面上,能够有效去除纤维表面的浮色,从根本上解决织物皂洗溶液牢度不合格的问题,并且工艺条件温和,无需强酸强碱条件,或者高温、冷洗环节,并省去高温皂洗流程,简化工艺步骤。
34.与现有技术相比,本发明具有以下的有益效果:
35.(1)本发明所述的改善纤维素纤维与涤混纺的深色面料皂洗溶液牢度的工艺,织物皂洗溶液牢度高,满足客户需求,提高合格率;
36.(2)本发明所述的改善纤维素纤维与涤混纺的深色面料皂洗溶液牢度的工艺,步骤简单,条件温和,适应市场推广;
37.(3)本发明所述的改善纤维素纤维与涤混纺的深色面料皂洗溶液牢度的工艺,用水量较少,免去高温皂洗,节能减耗,工艺中采用绿色环保试剂,利于污水处理。
附图说明
38.图1为本发明的检测面料的皂洗溶液牢度评级灰卡。
具体实施方式
39.本发明提供了一种改善纤维素纤维与涤混纺的深色面料皂洗溶液牢度的工艺,本领域技术人员可以借鉴本文内容,适当改进工艺参数实现。特别需要指出的是,所有类似的替换和改动对本领域技术人员来书是显而易见的,它们都属于本发明保护的范围。本发明的制备方法已经通过较佳实施例进行了描述,相关人员明显能在不脱离本发明内容、精神和范围内对本发明的制备方法进行改动和适当变更与组合,来实现和应用本发明技术。为了进一步说明本发明,以下结合实施例对本发明的改善纤维素纤维与涤混纺的深色面料皂洗溶液牢度的工艺进行详细描述。
40.以下实施例所用的试剂均来自市购,优选结果如表1所示:
41.表1 试剂
[0042][0043]
实施例1
[0044]
织物采用涤棉混纺,组织规格:cvc16*cvc12*108*56*58/59,织物组织:3/1s;
[0045]
所述的改善纤维素纤维与涤混纺的深色面料皂洗溶液牢度的工艺,包括以下步骤:
[0046]
改善纤维素纤维与涤混纺的深色面料皂洗溶液牢度的工艺,包括以下步骤:
[0047]
(1)织物预处理:将织物依次经过烧毛、冷堆、煮练、干定型、丝光、浸轧分散染料、烘干、焙烘、分散固色;
[0048]
(2)活性染色:将织物在染色机上进行染液浸轧,活性染料染液:活性红oc-3r:4.19g/l,活性蓝r.bf-2b:1.81g/l,活性蓝everzol blue brf 150%:29.64g/l,防泳移剂tx:10g/l,浸轧方式为两浸两轧,三组温度进行烘干:第一组烘房的温度为80℃,循环风为50%,排风为65%,第二组烘房的温度为90℃,循环风为60%,排风为70%,第三组烘房的温度为100℃,循环风为70%,排风为60%;
[0049]
(3)活性固色:浸轧活性固色液,其组成为烧碱:11.5g/l,纯碱:30g/l,元明粉:225g/l,抗还原剂防染盐s:2g/l,润湿渗透剂nf:2g/l,其余为水,车速为40m/min;
[0050]
(4)汽蒸、水洗:汽蒸温度为100℃,时间为1.8min;
[0051]
(5)还原清洗剂清洗:在浓度为10g/l的还原清洗剂gin中清洗75s,用氢氧化钠调节ph为8.4,调节温度为95℃;
[0052]
(6)皂洗、水洗:在浓度为2g/l的高浓分散防沾皂洗剂isopon rss liq new溶液中皂洗75s,水温为95℃,车速为45m/min;
[0053]
(7)烘干。
[0054]
上述步骤(5)和步骤(6)共九节水洗槽,2#3#水洗槽为还原清洗剂溶液,5#6#水洗槽为皂洗剂溶液,其他水洗槽为清水。
[0055]
实施例2
[0056]
织物采用经向竹涤混纺,纬向竹涤混纺包氨纶,组织规格:bam/t50*bam/t50(spandex40d)*160*100*53/54,织物组织:3/1缎纹;
[0057]
所述的改善纤维素纤维与涤混纺的深色面料皂洗溶液牢度的工艺,包括以下步骤:
[0058]
(1)织物预处理:将织物依次经过烧毛、冷堆、煮练、干定型、丝光、浸轧分散染料、烘干、焙烘、分散固色;
[0059]
(2)活性染色:将织物在染色机上进行染液浸轧,活性染料染液:活性红oc-3r:2.85g/l、活性蓝everzol blue brf 150%:49.88g/l、活性黄ye-3g:4.41g/l,防泳移剂:
10g/l,浸轧方式为两浸两轧,三组温度进行烘干:第一组烘房的温度为90℃,循环风为60%,排风为60%,第二组烘房的温度为100℃,循环风为70%,排风为70%,第三组烘房的温度为110℃,循环风为80%,排风为60%;
[0060]
(3)活性固色:浸轧活性固色液,为烧碱11.5g/l,纯碱30g/l,元明粉225g/l,抗还原剂防染盐s:2g/l,润湿渗透剂nf:2g/l,其余为水,车速为50m/min;
[0061]
(4)汽蒸、水洗:汽蒸温度为100℃,时间为1.5min;
[0062]
(5)还原清洗剂清洗:在浓度为10g/l的还原清洗剂gin中清洗100s,用氢氧化钠调节ph为8.5,调节温度为95℃;
[0063]
(6)皂洗、水洗:在浓度为2g/l的高浓分散防沾皂洗剂isopon rss liq new溶液中皂洗100s,水温为95℃,车速为50m/min;
[0064]
(7)烘干。
[0065]
上述步骤(5)和步骤(6)共九节水洗槽,依次为1#-9#水洗槽,2#和3#水洗槽为还原清洗剂溶液,5#和6#水洗槽为皂洗剂溶液,8#水洗槽为酸溶液,其他水洗槽为清水。
[0066]
实施例3
[0067]
织物采用竹涤混纺,组织规格:bam/t50*bam/t50*150*100*57/58,织物组织:1/3+db;
[0068]
所述的改善纤维素纤维与涤混纺的深色面料皂洗溶液牢度的工艺,包括以下步骤:
[0069]
(1)织物预处理:将织物依次经过烧毛、冷堆、煮练、干定型、丝光、浸轧分散染料、烘干、焙烘、分散固色;
[0070]
(2)活性染色:将织物在染色机上进行染液浸轧,活性染液包括活性黄ys-3r:0.58g/l、活性红rs-b:6.02g/l、活性黑se:60g/l,防泳移剂10g/l,其余为水;浸轧方式为两浸两轧,三组温度进行烘干:第一组烘房的温度为80℃,循环风为50%,排风为60%,第二组烘房的温度为90℃,循环风为60%,排风为70%,第三组烘房的温度为100℃,循环风为80%,排风为60%;
[0071]
(3)活性固色:浸轧活性固色液,为烧碱12g/l,纯碱25g/l,元明粉220g/l,抗还原剂防染盐s:3g/l,润湿渗透剂nf:5g/l,车速为40m/min;
[0072]
(4)汽蒸、水洗:汽蒸温度为102℃,时间为1.8min;
[0073]
(5)还原清洗剂清洗:在浓度为10g/l的还原清洗剂gin中清洗100s,用氢氧化钠调节ph为8.2,调节温度为95℃;
[0074]
(6)皂洗、水洗:在浓度为3g/l的高浓分散防沾皂洗剂isopon rss liq new溶液中皂洗100s,水温为100℃,车速为40m/min;
[0075]
(7)烘干。
[0076]
上述步骤(5)和步骤(6)共九节水洗槽,依次为1#-9#水洗槽,2#和3#水洗槽为还原清洗剂溶液,5#和6#水洗槽为皂洗剂溶液,8#水洗槽为酸溶液,其他水洗槽为清水。
[0077]
对比例1
[0078]
织物采用涤棉混纺,组织规格:cvc16*cvc12*108*56*58/59,织物组织:3/1s;
[0079]
按照cn113502666a的工艺,工艺步骤包括:
[0080]
(1)织物预处理:将织物放置到平整的处理台面上,对不规则的边角料,脱线部分
进行剪裁,然后对所述织物的表面进行快速的高温明火烧制,使得织物表面的细小绒毛被烧除,制得初级织物;
[0081]
(2)漂白消毒:将步骤一中制得的初级织物置于漂白缸内,添加足量的漂白液和消毒水,同时进行适当的升温和按压,确保漂白液和消毒液浸泡至织物内部,浸泡30~50min后取出进行水洗,再干燥后制得次级织物;
[0082]
(3)一次上色:将次级织物置于装满一半染料的染缸内,然后从染缸顶部以高压喷出剩余的染料。使得高压染料冲击次级织物,直至染料漫过全部的次级织物,再对染料进行升温,浸泡1.6~2.5h后取出,完成一次上色;
[0083]
(4)除菌去味:将一次上色的次级织物取出进行水洗,洗去多余的染料后干燥,然后浸泡在盛满除菌剂微胶囊的除菌缸内,浸泡20min后加入适量的植物天然香料,保持低速的搅拌,持续30~50min后取出水洗并干燥;
[0084]
(5)二次上色:将经过除菌去味后的次级织物重新置于装满一半染料的染缸内,与一次上色不同的是,从染缸顶部以高压喷出的染料内还需添加染料微胶囊,使得高压染料携带着微胶囊冲击次级织物,直至染料漫过全部的次级织物,再对染料进行升温,浸泡1.6~2.5h后取出,完成二次上色;
[0085]
(6)干燥定型:将完成二次上色的次级织物取出进行充分的水洗后进行干燥,在通过定型机进行定型,得到成品织物。
[0086]
对比例2
[0087]
织物采用经向竹涤混纺,纬向竹涤混纺包氨纶,组织规格:bam/t50*bam/t50(spandex40d)*160*100*53/54,织物组织:3/1缎纹;
[0088]
一种现有的深色面料的制备工艺,包括以下步骤:
[0089]
(1)织物预处理:将织物依次经过烧毛、冷堆、煮练、干定型、丝光、浸轧分散染料、烘干、焙烘、分散固色;
[0090]
(2)活性染色:浸轧活性染料染液:oc-3r:2.85g/l、everzol blue brf 150%:49.88g/l、ye-3g:4.41g/l,防泳移剂:10g/l,其余为水,浸轧染液后,三段预烘;
[0091]
(3)活性固色:浸轧活性固色液,其组成为元明粉:225g/l、naoh:11.5g/l、na2co3:30g/l、防染盐s:2g/l、润湿渗透剂nf:2g/l,其余为水,车速为50m/min;
[0092]
(4)汽蒸:汽蒸温度为101℃,时间为1.5min;
[0093]
(6)皂洗:在2g/l皂洗剂raytexil wo-n溶液中皂洗,水温为95℃,车速为50m/min;
[0094]
上述步骤(6)共九节水洗槽,5#6#水洗槽为皂洗剂溶液,8#水洗槽为酸溶液,其他水洗槽为清水;
[0095]
(7)烘干。
[0096]
对比例3
[0097]
织物采用竹涤混纺,组织规格:bam/t50*bam/t50*150*100*57/58,织物组织:1/3+db;
[0098]
一种利用现有的技术中的还原清洗剂深色面料的工艺,包括以下步骤:
[0099]
(1)织物预处理:将织物依次经过烧毛、冷堆、煮练、干定型、丝光、浸轧分散染料、烘干、焙烘、分散固色;
[0100]
(2)活性染色:在活性染液中染色,活性染液包括活性黄ys-3r:0.58g/l、活性红
rs-b:6.02g/l、活性黑黑se:60g/l,防泳移剂10g/l,其余为水,浸轧染液后,三段预烘;
[0101]
(3)活性固色:浸轧活性固色液,元明粉:225g/l、naoh:11.5g/l、na2co3:30g/l、防染盐s:2g/l、润湿渗透剂nf:2g/l,其余为水,车速为40m/min;
[0102]
(4)汽蒸:汽蒸时间为100℃,时间为1.5min;
[0103]
(5)还原清洗剂清洗:在10g/l浓度还原清洗剂gh中清洗,并用氢氧化钠溶液调节ph为8.2,调节温度为95℃;
[0104]
(6)皂洗:在2g/l的高浓分散防沾皂洗剂isopon rss liq new中皂洗,水温为95℃,车;
[0105]
上述步骤(5)和步骤(6)共九节水洗槽,2#3#水洗槽为还原清洗剂溶液,5#6#水洗槽为皂洗剂溶液,8#水洗槽为酸溶液,其他水洗槽为清水。
[0106]
将实施例1-3和对比例1-3所制得的深色面料,进行皂洗,皂洗步骤为:
[0107]
准备2l自来水升温到40℃,放入6g洗衣液(蓝月亮),取150g重量面料,浸泡在40℃温水的盆中,浸泡30min,期间常规揉搓5-10次;
[0108]
皂洗处理后的深色面料的评级:将实施例1-3和对比例1-3皂洗后的溶液分别倒入透明的玻璃烧杯中,将其溶液的颜色和原深色面料的颜色同时与评级灰卡进行比对,即可得出皂洗溶液的牢度等级;
[0109]
皂洗溶液牢度的评级借鉴国际通用的5级9档规格类型,当某一级观感色差最接近于原样与试验后样间的观感色差程度时,就作为该试样的牢度级数。只有当实验后样品与原样之间没有观感色差时,才评定为5级。
[0110]
采用上述方式检测实施例1-3和对比例1-3所制得的深色面料的皂洗溶液牢度,结果如表2所示:
[0111]
表2 皂洗溶液牢度的检测结果
[0112]
项目皂洗溶液牢度/等级实施例14/5实施例24实施例34/5对比例13对比例22对比例33
[0113]
当然,上述内容仅为本发明的较佳实施例,不能被认为用于限定对本发明的实施例范围。本发明也并不仅限于上述举例,本技术领域的普通技术人员在本发明的实质范围内所做出的均等变化与改进等,均应归属于本发明的专利涵盖范围内。