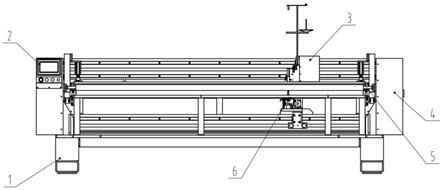
1.本发明属于家纺、绗缝技术领域,主要应用于复合材料的拼接,具体涉及一种自动缝制型接布机。
背景技术:
2.在复合材料加工中,经常要接布作业,为了生产方便,一般换卷时需要将后卷的头部与前卷的尾部进行接布处理。目前的接布工艺有缝制型和热接型,热接型接布存在接布时需要停机、接布后的边角料不易收集等缺点;传统的带刀手动缝制型接布机又存在接布效率低、缝制直线度差等缺点。
技术实现要素:
3.本发明的目的在于克服上述现有技术的不足之处,提供了一种自动缝制型接布机,本机器在结构上的优化调整,解决了常规性问题,增加了适用性。
4.本发明的目的是通过以下技术方案实现的:自动缝制型接布机,主要包括:底座、操作屏、上机头组件、鞍架组件、压料装置、下机头组件。
5.所述的底座由方刚焊接而成,结实牢靠。
6.所述的鞍架组件用螺钉直接固定在底座上。
7.所述的显示屏固定在鞍架组件左边罩体上。
8.所述的上机头组件、压料装置和下机头组件分别固定在鞍架组件上(如图1所示)。
9.上机头组件,包括:上机头、上线杆组件、电机座、电机带轮、伺服电机、上机头固定板、传感器、感应圈、机头带轮。
10.所述的伺服电机固定在电机座上。
11.所述的电机带轮固定在伺服电机的输出轴上。
12.所述的机头带轮和感应圈分别固定在上机头的输出轴上。
13.所述的上线杆组件、传感器、上机头、电机座分别固定在上机头固定板上。
14.所述的传感器与感应圈一一对应,调整好机头带轮和电机带轮的位置,通过同步带将其连接,这样电机驱动带动机头针杆的往复上下运动(如图2所示)。
15.其中,上机头的壳体加工到整个机头的组装都是由我公司自主研发,在保证产品质量的前提下,工作速度高达3000r/min,进而提高了缝制速度。
16.鞍架组件包括:左立板组件、上鞍架管、前直线导轨、x向同步带、右端传动带轮、皮带张紧架组件、右立板组件、下鞍架管、电机、电机主动轮、环形同步带、从动轮、传动轴、轴承座、左端传动带轮。
17.所述的上鞍架管、下鞍架管、左立板组件、右立板组件由螺钉组装而成。
18.所述的前直线导轨分别安装在上鞍架管和下鞍架管的一侧。
19.所述的右端传动带轮固定在皮带张紧架组件上,再整体固定在右立板组件上。
20.所述的左端传动带轮和从动轮分别安装在传动轴上,通过轴承座将其固定在左立板组件上。
21.所述的电机主动轮安装在电机输出主轴上,电机主动轮再和从动轮通过环形同步带连接。
22.最后x向同步带将左端传动带轮和右端传动带轮相连。
23.所述的x向同步带分别固定在上机头组件和下机头组件上。
24.所述的上机头组件和下机头组件固定在前直线导轨上。
25.电机驱动,带动右端传动带轮和左端传动带轮的旋转,再通过x向同步带传动使上机头组件和下机头组件往复的直线运动(如图4、5所示)。
26.其中,上鞍架管和下鞍架管是铝型材加工而成,左立板组件和右立板组件也是铝板加工组装完成的,整体结构加工工艺简单,重量也相对钢管减重一半。
27.由于直线导轨本身精度高,这样就保证了机头的行走精度,进而保证缝制直线度的精度。
28.压料装置包括:横梁连接件、激光笔、压布横梁、撑布板、气缸、上压板和气缸固定板。
29.所述的气缸分别固定在横梁连接件和气缸固定板上。
30.所述的气缸与压布横梁相连。
31.所述的上压板固定在压布横梁上。
32.所述的撑布板和横梁连接件固定在鞍架组件上。
33.所述的两端气缸控制压布横梁升降,上压板从而将辅料压在撑布板上,实现压料的作用,防止辅料收缩和起褶。
34.其中,激光笔安装在压布横梁上,目的是使辅料边缘对齐,防止拼接错位现象的发生,起到辅助的作用。
35.激光笔可根据辅料的长短来移动位置(如图5、6所示)。
36.下机头组件包括:前固定板、二倍旋梭箱、旋梭主轴带轮、传感器、感应圈、连接板、后固定板、伺服电机、电机带轮、电机座。
37.所述的前固定板和后固定板与连接板相连。
38.所述的旋梭主轴带轮和感应圈分别固定在二倍旋梭箱的输出主轴上。
39.所述的电机固定在电机座上,电机带轮固定在伺服电机的输出主轴上。
40.所述的二倍旋梭箱和电机座分别固定在连接板上。
41.与现有技术相比,本发明的有益效果是:本发明克服了以往缝纫慢、毛边多、缝制直线度差、接缝后需修整的缺点,通过本发明的设计,操作简单、接布效率高、缝制直线度高,接布不打褶,节约成本,提高成品率。
附图说明
42.图1 为整机示意图;图2为上机头组件示意图;图3为鞍架组件示意图;图4为鞍架组件左视图示意图;
图5为压料装置示意图;图6为压料装置右视图示意图;图7下机头组件示意图。
43.1.底座
ꢀꢀꢀ
2.操作屏
ꢀꢀꢀ
3.上机头组件
ꢀꢀꢀ
4.鞍架组件
ꢀꢀꢀ
5.压料装置
ꢀꢀꢀ
6.下机头组件
ꢀꢀꢀ
7.上机头
ꢀꢀꢀ
8.上线杆组件
ꢀꢀꢀ
9.电机座
ꢀꢀꢀ
10.电机带轮
ꢀꢀꢀ
11.伺服电机
ꢀꢀꢀ
12.上机头固定板
ꢀꢀꢀ
13.传感器
ꢀꢀꢀ
14.感应圈
ꢀꢀꢀ
15.机头带轮
ꢀꢀꢀ
16.左立板组件
ꢀꢀꢀ
17.上鞍架管
ꢀꢀꢀ
18.前直线导轨
ꢀꢀꢀ
19. x向同步带
ꢀꢀꢀ
20.右端传动带轮
ꢀꢀꢀ
21.皮带张紧架组件
ꢀꢀꢀ
22.右立板组件
ꢀꢀꢀ
23.下鞍架管
ꢀꢀꢀ
24.电机
ꢀꢀꢀ
25.电机主动轮
ꢀꢀꢀ
26.环形同步带
ꢀꢀꢀ
27.从动轮
ꢀꢀꢀ
28.传动轴
ꢀꢀꢀ
29.轴承座
ꢀꢀꢀ
30.左端传动带轮
ꢀꢀꢀ
31.横梁连接件
ꢀꢀꢀ
32.激光笔
ꢀꢀꢀ
33.压布横梁
ꢀꢀꢀ
34.撑布板
ꢀꢀꢀ
35.气缸
ꢀꢀꢀ
36.上压板
ꢀꢀꢀ
37.气缸固定板
ꢀꢀꢀ
38.前固定板
ꢀꢀꢀ
39.二倍旋梭箱
ꢀꢀꢀ
40.旋梭主轴带轮
ꢀꢀꢀ
41.传感器
ꢀꢀꢀ
42.感应圈
ꢀꢀꢀ
43.连接板
ꢀꢀꢀ
44.后固定板
ꢀꢀꢀ
45.伺服电机
ꢀꢀꢀ
46.电机带轮
ꢀꢀꢀ
47.电机座。
具体实施方式
44.为能进一步了解本发明的内容、特点以及功效,兹例举以下实施例,并配合附图详细说明如下。需要说明的是,本实施例是描述性的,不是限定性的,不能由此限定本发明的保护范围。
45.自动缝制型接布机,主要包括:底座(1)、操作屏(2)、上机头组件(3)、鞍架组件(4)、压料装置(5)、下机头组件(6)。
46.所述的底座(1)由方刚焊接而成,结实牢靠。
47.所述的鞍架组件(4)用螺钉直接固定在底座(1)上。
48.所述的显示屏(2)固定在鞍架组件(4)左边罩体上。
49.所述的上机头组件(3)、压料装置(5)和下机头组件(6)分别固定在鞍架组件(4)上(如图1所示)。
50.上机头组件(3)包括:上机头(7)、上线杆组件(8)、电机座(9)、电机带轮(10)、伺服电机(11)、上机头固定板(12)、传感器(13)、感应圈(14)和机头带轮(15)。
51.所述的伺服电机(11)固定在电机座(9)上。
52.所述的电机带轮(10)固定在伺服电机(11)的输出轴上。
53.所述的机头带轮(15)和感应圈(14)分别固定在上机头(7)的输出轴上。
54.所述的上线杆组件(8)、传感器(13)、上机头(7)、电机座(9)分别固定在上机头固定板(12)上。
55.所述的传感器(13)与感应圈(14)一一对应,调整好机头带轮(15)和电机带轮(10)的位置,通过同步带将其连接,这样电机驱动带动机头针杆的往复上下运动(如图2所示)。
56.其中,上机头(7)的壳体加工到整个机头的组装都是由我公司自主研发,在保证产品质量的前提下,工作速度高达3000r/min,进而提高了缝制速度。
57.鞍架组件(4)包括:左立板组件(16)、上鞍架管(17)、前直线导轨(18)、x向同步带(19)、右端传动带轮(20)、皮带张紧架组件(21)、右立板组件(22)、下鞍架管(23)、电机(24)、电机主动轮(25)、环形同步带(26)、从动轮(27)、传动轴(28)、轴承座(29)、左端传动带轮(30)。
58.所述的上鞍架管(17)、下鞍架管(23)、左立板组件(16)、右立板组件(22)由螺钉组装而成。
59.所述的前直线导轨(18)分别安装在上鞍架管(17)和下鞍架管(23)的一侧。
60.所述的右端传动带轮(20)固定在皮带张紧架组件(21)上,再整体固定在右立板组件(22)上。
61.所述的左端传动带轮(30)和从动轮(27)分别安装在传动轴(28)上,通过轴承座(29)将其固定在左立板组件(16)上。
62.所述的电机主动轮(25)安装在电机(24)输出主轴上,电机主动轮(25)再和从动轮(27)通过环形同步带(26)连接。
63.最后x向同步带(19)将左端传动带轮(30)和右端传动带轮(20)相连。
64.所述的x向同步带(19)分别固定在上机头组件(3)和下机头组件(6)上。
65.所述的上机头组件(3)和下机头组件(6)固定在前直线导轨(18)上。
66.电机(24)驱动,带动右端传动带轮(20)和左端传动带轮(30)的旋转,再通过x向同步带(19)传动使上机头组件(3)和下机头组件(6)往复的直线运动。如图4、5所示。
67.其中,上鞍架管(17)和下鞍架管(23)是铝型材加工而成,左立板组件(16)和右立板组件(22)也是铝板加工组装完成的,整体结构加工工艺简单,重量也相对钢管减重一半。由于直线导轨本身精度高,这样就保证了机头的行走精度,进而保证缝制直线度的精度。
68.压料装置(5)包括:横梁连接件(31)、激光笔(32)、压布横梁(33)、撑布板(34)、气缸(35)、上压板(36)和气缸固定板(37)。
69.所述的气缸(35)分别固定在横梁连接件(31)和气缸固定板(37)上。
70.所述的气缸(35)与压布横梁(33)相连。
71.所述的上压板(36)固定在压布横梁(33)上。
72.所述的撑布板(34)和横梁连接件(31)固定在鞍架组件(4)上。
73.所述的两端气缸(35)控制压布横梁(33)升降,上压板(36)从而将辅料压在撑布板(34)上,实现压料的作用,防止辅料收缩和起褶。
74.其中,激光笔(32)安装在压布横梁(33)上,目的是使辅料边缘对齐,防止拼接错位现象的发生,起到辅助的作用。激光笔(32)可根据辅料的长短来移动位置。如图5、6所示。
75.下机头组件(6)包括:前固定板(38)、二倍旋梭箱(39)、旋梭主轴带轮(40)、传感器(41)、感应圈(42)、连接板(43)、后固定板(44)、伺服电机(45)、电机带轮(46)、电机座(47)。
76.所述的前固定板(38)和后固定板(44)与连接板(43)相连。
77.所述的旋梭主轴带轮(40)和感应圈(42)分别固定在二倍旋梭箱(39)的输出主轴上。
78.所述的电机(45)固定在电机座(47)上,电机带轮(46)固定在伺服电机(45)的输出主轴上。
79.所述的二倍旋梭箱(39)和电机座(47)分别固定在连接板(43)上。
80.调整好电机带轮(46)和旋梭主轴带轮(40)的位置,通过同步带将其连接,伺服电机(45)驱动带动二倍旋梭箱(39)主轴的旋转(如图7所示)。
81.综上所述,上机头组件和下机头组件通过单独的伺服电机(45)同步带动,实现机针与旋梭的同步配合,将面线带上底线以完成绗缝工作。
82.在绗缝作业同时,上、下机头组件沿直线导轨轴相对于机座架在x方向上移动位置,保证了缝制精度,因只涉及到面线自动剪线,所以不会产生布料毛边的问题,自动缝制型接布机操作简单,运行稳定,故障率低。
83.这里简单说明一下操作步骤:在操作屏(2)上提前设定好花型尺寸,缝制速度和针步大小后,按下启动按钮,上、下机头组件自动缝制,当缝制完成自动剪线后,上、下机头组件会自动移动到起点位置,等待下一个工作循环。