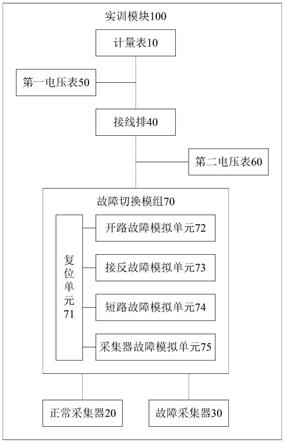
1.本发明涉及用电采集设备维护技术领域,具体涉及一种计量采集设备排故实训装置。
背景技术:
2.电力用户用电信息采集系统(简称用采系统)是智能电网建设的重要组成部分,按照国家电网公司智能电网建设总体要求,电力用户用电信息采集系统建设要实现“全覆盖、全采集、全费控”的总体目标。目前,大量数据采集设备投入运行,这些设备的日常运行维护给乡镇供电所带来了很大的压力,涉及人员较多。乡镇供电所采集运维工作是保证线损管理达标的基础,台区经理在实际工作中,针对采集不成功的处理方法是“换”,要么换采集器,要么换表,对故障原因没有分析能力,以致更换表计和采集器后故障仍不能排除,造成人力和物力浪费。
3.现有的用采仿真柜结构复杂,故障的设置需要相关软件支撑,要经过专业培训人员才能操作。并且需要建立一个与用采系统相似的仿真模拟系统作为支撑,一旦用采系统更新升级后必须花巨资同步升级模拟库。
技术实现要素:
4.本发明为解决目前用采系统运维工作中浪费人力物力,且现有用采仿真柜技术性强、购置和后期维护费用高,只适用于专业培训单位使用的技术问题,提供了一种计量采集设备排故实训装置,能够通过简单易学的设备实现对用采系统运维人员的实训,使运维人员快速提高故障排除的技能水平,保障用采系统的可靠运行,并避免因盲目更换设备而造成的资源浪费。
5.本发明采用的技术方案如下:
6.一种计量采集设备排故实训装置,包括至少一个实训模块,每个所述实训模块包括计量表、正常采集器、故障采集器、接线排、第一电压表、第二电压表和故障切换模组,所述故障切换模组包括复位单元、开路故障模拟单元、接反故障模拟单元、短路故障模拟单元和采集器故障模拟单元,其中,所述计量表、所述正常采集器和所述故障采集器的电源端均连接到电源线;所述接线排的一侧通过通信线与所述计量表的通信端相连,所述接线排的另一侧分别通过通信线与所述正常采集器和所述故障采集器的通信端相连;所述第一电压表与所述接线排的一侧相连;所述第二电压表与所述接线排的另一侧相连;所述开路故障模拟单元、所述接反故障模拟单元、所述短路故障模拟单元和所述采集器故障模拟单元均对应所述接线排的另一侧的通信线设置,以分别用于实现通信线开路故障模拟、通信线接反故障模拟、通信线短路故障模拟和采集器故障模拟;所述复位单元与所述开路故障模拟单元、所述接反故障模拟单元、所述短路故障模拟单元和所述采集器故障模拟单元相连,以用于实现故障恢复。
7.所述的计量采集设备排故实训装置还包括总开关模组,所述总开关模组对应所述
电源线设置,以用于实现所述计量采集设备排故实训装置的开启和关闭。
8.所述的计量采集设备排故实训装置包括两个所述实训模块,其中一个所述实训模块中的计量表为单相表,另一个所述实训模块中的计量表为三相表。
9.所述总开关模组包括第一按钮、第二按钮和第一继电器,所述第一按钮为常开按钮,所述第二按钮为常闭按钮,所述第一继电器为三触点常开继电器,所述第一按钮、所述第二按钮和所述第一继电器的线圈单元串联后,一端连接到第一相线、另一端连接到零线,所述第一继电器的开关单元设置于三个相线上。
10.所述复位单元包括第三按钮,所述第三按钮为常闭按钮,所述第三按钮的一端连接到所述第一相线。
11.所述计量表与所述正常采集器和故障采集器之间通过rs485通信,所述计量表的通信端、所述正常采集器的通信端和所述故障采集器的通信端分别包括两个端口,所述通信线为两根。
12.所述开路故障模拟单元包括第四按钮和第二继电器,所述第四按钮为常开按钮,所述第二继电器为双触点常闭继电器,所述第四按钮和所述第二继电器的线圈单元串联后,一端与所述第三按钮的另一端相连、另一端连接到所述零线,所述第二继电器的开关单元设置于所述接线排的另一侧与所述正常采集器之间的通信线上。
13.所述接反故障模拟单元包括第五按钮和第三继电器,所述第五按钮为常开按钮,所述第三继电器为双触点转换型继电器,所述第五按钮和所述第三继电器的线圈单元串联后,一端与所述第三按钮的另一端相连、另一端连接到所述零线,所述第三继电器的开关单元一侧的每条通信线分出两个静触点,在所述第三继电器的线圈单元未通电时,所述第三继电器的开关单元的状态使得所述第三继电器的开关单元两侧的通信线正接,在所述第三继电器的线圈单元通电后,所述第三继电器的开关单元的状态使得所述第三继电器的开关单元两侧的通信线反接。
14.所述短路故障模拟单元包括第六按钮和第四继电器,所述第六按钮为常开按钮,所述第四继电器为常开继电器,所述第六按钮和所述第四继电器的线圈单元串联后,一端与所述第三按钮的另一端相连、另一端连接到所述零线,所述第四继电器设置于所述接线排的另一侧与所述正常采集器之间的两根通信线的短接线上。
15.所述采集器故障模拟单元包括第七按钮和第五继电器,所述第七按钮为常开按钮,所述第五继电器为双触点转换型继电器,所述第七按钮和所述第五继电器的线圈单元串联后,一端与所述第三按钮的另一端相连、另一端连接到所述零线,所述第五继电器的开关单元的动触点连接至所述接线排的另一侧,所述第五继电器的开关单元的一组静触点连接到所述正常采集器、另一组静触点连接到所述故障采集器,在所述第五继电器的线圈单元未通电时,所述第五继电器的开关单元的动触点与所述第五继电器的开关单元的一组静触点相闭合,在所述第五继电器的线圈单元通电后,所述第五继电器的开关单元的动触点与所述第五继电器的开关单元的另一组静触点相闭合。
16.本发明的有益效果:
17.本发明通过设置计量表、正常采集器、故障采集器、接线排、第一电压表、第二电压表和故障切换模组,通过故障切换模组进行通信线开路故障模拟、通信线接反故障模拟、通信线短路故障模拟和采集器故障模拟等采集故障模拟的切换,由此,能够通过简单易学的
设备实现对用采系统运维人员的实训,使运维人员快速提高故障排除的技能水平,保障用采系统的可靠运行,并避免因盲目更换设备而造成的资源浪费。
附图说明
18.图1为本发明实施例的计量采集设备排故实训装置的方框示意图;
19.图2为本发明一个实施例的计量采集设备排故实训装置的方框示意图;
20.图3为本发明一个实施例的计量采集设备排故实训装置的一部分结构示意图;
21.图4为本发明一个实施例的计量采集设备排故实训装置的另一部分结构示意图;
22.图5为本发明一个实施例的计量采集设备排故实训装置组装后的外部结构示意图。
具体实施方式
23.下面将结合本发明实施例中的附图,对本发明实施例中的技术方案进行清楚、完整地描述,显然,所描述的实施例仅仅是本发明一部分实施例,而不是全部的实施例。基于本发明中的实施例,本领域普通技术人员在没有做出创造性劳动前提下所获得的所有其他实施例,都属于本发明保护的范围。
24.如图1所示,本发明实施例的计量采集设备排故实训装置包括至少一个实训模块100,每个实训模块100包括计量表10、正常采集器20、故障采集器30、接线排40、第一电压表50、第二电压表60和故障切换模组70,故障切换模组70包括复位单元71、开路故障模拟单元72、接反故障模拟单元73、短路故障模拟单元74和采集器故障模拟单元75,其中,计量表10、正常采集器20和故障采集器30的电源端均连接到电源线;接线排40的一侧通过通信线与计量表10的通信端相连,接线排40的另一侧分别通过通信线与正常采集器20和故障采集器30的通信端相连;第一电压表50与接线排40的一侧相连;第二电压表60与接线排40的另一侧相连;开路故障模拟单元72、接反故障模拟单元73、短路故障模拟单元74和采集器故障模拟单元75均对应接线排40的另一侧的通信线设置,以分别用于实现通信线开路故障模拟、通信线接反故障模拟、通信线短路故障模拟和采集器故障模拟;复位单元71与开路故障模拟单元72、接反故障模拟单元73、短路故障模拟单元74和采集器故障模拟单元75相连,以用于实现故障恢复。
25.进一步地,如图2所示,本发明实施例的计量采集设备排故实训装置还可包括总开关模组200,总开关模组200对应电源线设置,以用于实现计量采集设备排故实训装置的开启和关闭。
26.在本发明的一个实施例中,如图3和图4所示(图3、4中的a、b表示连接关系,即图3中的a点与图4中的a点连接,图3中的b点与图4中的b点连接),计量采集设备排故实训装置包括两个实训模块,其中一个实训模块中的计量表10为单相表,另一个实训模块中的计量表10为三相表,含单相表的实训模块可用以模拟照明用户,含三相表的实训模块可用以模拟动力用户。
27.如图3和图4所示,总开关模组200可包括第一按钮sb1、第二按钮sb2和第一继电器km1,第一按钮sb1为常开按钮,第二按钮sb2为常闭按钮,第一继电器km1为三触点常开继电器,第一按钮sb1、第二按钮sb2和第一继电器km1的线圈单元串联后,一端连接到第一相线
(如u相)、另一端连接到零线n,第一继电器km1的开关单元设置于三个相线u、v、w上。
28.如图3和图4所示,复位单元71包括第三按钮sb3,第三按钮为常闭按钮,第三按钮sb3的一端连接到第一相线。
29.在本发明的一个实施例中,计量表10与正常采集器20和故障采集器30之间通过rs485通信,计量表10的通信端、正常采集器20的通信端和故障采集器30的通信端分别包括两个端口,通信线为两根(图中分别以a、b表示)。本发明实施例中的正常采集器20和故障采集器30分别为不存在故障的采集器和存在故障的采集器。
30.如图3和图4所示,在含单相表的实训模块中,开路故障模拟单元72包括第四按钮sb4和第二继电器km2,第四按钮sb4为常开按钮,第二继电器km2为双触点常闭继电器,第四按钮sb4和第二继电器km2的线圈单元串联后,一端与第三按钮sb3的另一端相连、另一端连接到零线n,第二继电器km2的开关单元设置于接线排40的另一侧与正常采集器20之间的通信线上。
31.在含三相表的实训模块中,第四按钮为sb8,第二继电器为km6,各部件的连接关系与含单相表的实训模块相同。
32.如图3和图4所示,在含单相表的实训模块中,接反故障模拟单元73包括第五按钮sb5和第三继电器km3,第五按钮sb5为常开按钮,第三继电器km3为双触点转换型继电器,第五按钮sb5和第三继电器km3的线圈单元串联后,一端与第三按钮sb3的另一端相连、另一端连接到零线n,第三继电器km3的开关单元一侧的每条通信线分出两个静触点,在第三继电器km3的线圈单元未通电时,第三继电器km3的开关单元的状态使得第三继电器km3的开关单元两侧的通信线正接,即a线与a线相接,b线与b线相接,在第三继电器km3的线圈单元通电后,第三继电器km3的开关单元的状态使得第三继电器km3的开关单元两侧的通信线反接,即a线与b线相接,b线与a线相接。
33.在含三相表的实训模块中,第五按钮为sb9,第三继电器为km7,各部件的连接关系与含单相表的实训模块相同。
34.如图3和图4所示,在含单相表的实训模块中,短路故障模拟单元74包括第六按钮sb6和第四继电器km4,第六按钮sb6为常开按钮,第四继电器km4为常开继电器,第六按钮sb6和第四继电器km4的线圈单元串联后,一端与第三按钮sb3的另一端相连、另一端连接到零线n,第四继电器km4设置于接线排40的另一侧与正常采集器20之间的两根通信线的短接线上。应当理解的是,第四继电器km4可以为单触点继电器,动、静触点作为两个端点串接于短接线上;也可以为双触点继电器,两个动触点相连,两个静触点作为两个端点串接于短接线上。
35.在含三相表的实训模块中,第六按钮为sb10,第四继电器为km8,各部件的连接关系与含单相表的实训模块相同。
36.如图3和图4所示,在含单相表的实训模块中,采集器故障模拟单元75包括第七按钮sb7和第五继电器km5,第七按钮sb7为常开按钮,第五继电器km5为双触点转换型继电器,第七按钮sb7和第五继电器km5的线圈单元串联后,一端与第三按钮sb3的另一端相连、另一端连接到零线n,第五继电器km5的开关单元的动触点连接至接线排40的另一侧,第五继电器km5的开关单元的一组静触点连接到正常采集器20、另一组静触点连接到故障采集器30,在第五继电器km5的线圈单元未通电时,第五继电器km5的开关单元的动触点与第五继电器
km5的开关单元的一组静触点相闭合,即将正常采集器20与接线排40的另一侧相接通;在第五继电器km5的线圈单元通电后,第五继电器km5的开关单元的动触点与第五继电器km5的开关单元的另一组静触点相闭合,即将故障采集器30与接线排40的另一侧相接通。
37.在含三相表的实训模块中,第七按钮为sb11,第五继电器为km9,各部件的连接关系与含单相表的实训模块相同。
38.如图3和图4所示,在含单相表的实训模块中,第一电压表50、第二电压表60的符号分别为dv1、dv2,在含三相表的实训模块中,第一电压表50、第二电压表60的符号分别为dv3、dv4。
39.上述包括两个实训模块的计量采集设备排故实训装置在组装后的外部结构如图5所示,四个电压表dv1~dv4位于面板上部,用以显示各类故障下的电压变化情况;三个按钮sb1~sb3位于面板下部,分别用以控制计量采集设备排故实训装置的开启、控制计量采集设备排故实训装置的关闭、故障的恢复;八个按钮sb4~sb11位于四个电压表之下,用以进行单相表各类采集故障的切换和三相表各类采集故障的切换。
40.上述任一实施例的计量采集设备排故实训装置在使用时,使用人员还可利用掌机和万用表进行实际的测量,将测量的数据与当前模拟的故障、电压表显示的数据等相结合,加深对各类故障之间区别的认识。
41.在实际使用时,参照图3和图4理解,在三相总电源接通后,按下sb1,km1吸合,给单相表和三相表以及各个采集器通电。此时km2~km9在非工作状态,单相表与相应的采集器间的rs485通信线没有故障,用掌机可以通过正常采集器的红外口读取计量表内部信息(例如计量表地址等)。
42.按下sb4,km2吸合,单相表至正常采集器间的rs485通信线断开,从而模拟出现场rs485通信线开路故障。此时dv1显示+5v左右电压值,拆下接线排一侧的rs485通信线,此时dv2显示0v电压值,完成面板显示,用掌机通过正常采集器红外口无法读取单相表的信息,用万用表测量rs485通信线和单相表通信端的电压,确认rs485通信线开路故障电压值。按下sb3,km2退出运行,单相表至正常采集器间rs485通信线恢复正常。
43.按下sb5,km3吸合,使km3进线和出线位置互换,模拟现场rs485通信线正负接反故障。此时dv1显示负2.5伏至正2.5v之间,拆下接线排一侧的rs485通信线,此时dv2显示-5v电压值,完成面板显示,用掌机通过正常采集器红外口无法读取单相表信息,用万用表测量rs485通信线和单相表通信端电压,确认rs485通信线反接故障电压值。按下sb3,km3退出运行,单相表至正常采集器间rs485通信线恢复正常。
44.按下sb6,km4吸合,使km4进线短接,模拟现场rs485通信线短路故障。此时dv1显示负0v左右,拆下接线排一侧的rs485通信线,此时dv2显示0v左右电压值,完成面板显示,用掌机通过正常采集器红外口无法读取单相表信息,用万用表测量rs485通信线和单相表通信端电压,确认rs485通信线短路故障电压值。按下sb3,km4退出运行,单相表至正常采集器间rs485通信线恢复正常。
45.按下sb7,km5吸合,使km5进线切换至故障采集器,模拟现场采集器故障。此时dv1显示负5v左右,拆下接线排一侧的rs485通信线,此时dv2显示5v左右电压值,完成面板显示,用掌机通过故障采集器红外口无法读取表计信息,用万用表测量rs485通信线和单相表通信端电压,确认采集器故障电压值。按下sb3,km5退出运行,单相表重新切换至与正常采
集器通信。
46.通过以上操作,可完成单相表四种采集故障之间的切换。同理,三相表的采集故障模拟与此类似,在此不再赘述。
47.在完成所有培训项目后,按下sb2,km1退出运行,从而切断所有电源。
48.综上所述,根据本发明实施例的计量采集设备排故实训装置,通过设置计量表、正常采集器、故障采集器、接线排、第一电压表、第二电压表和故障切换模组,通过故障切换模组进行通信线开路故障模拟、通信线接反故障模拟、通信线短路故障模拟和采集器故障模拟等采集故障模拟的切换,由此,能够通过简单易学的设备实现对用采系统运维人员的实训,使运维人员直观感受故障现象、判断故障原因、感受排除故障过程,从而使运维人员快速提高故障排除的技能水平,保障用采系统的可靠运行,并避免因盲目更换设备而造成的资源浪费。
49.在本发明的描述中,术语“第一”、“第二”仅用于描述目的,而不能理解为指示或暗示相对重要性或者隐含指明所指示的技术特征的数量。由此,限定有“第一”、“第二”的特征可以明示或者隐含地包括一个或者更多个该特征。“多个”的含义是两个或两个以上,除非另有明确具体的限定。
50.在本发明中,除非另有明确的规定和限定,术语“安装”、“相连”、“连接”、“固定”等术语应做广义理解,例如,可以是固定连接,也可以是可拆卸连接,或成一体;可以是机械连接,也可以是电连接;可以是直接相连,也可以通过中间媒介间接相连,可以是两个元件内部的连通或两个元件的相互作用关系。对于本领域的普通技术人员而言,可以根据具体情况理解上述术语在本发明中的具体含义。
51.在本发明中,除非另有明确的规定和限定,第一特征在第二特征“上”或“下”可以是第一和第二特征直接接触,或第一和第二特征通过中间媒介间接接触。而且,第一特征在第二特征“之上”、“上方”和“上面”可是第一特征在第二特征正上方或斜上方,或仅仅表示第一特征水平高度高于第二特征。第一特征在第二特征“之下”、“下方”和“下面”可以是第一特征在第二特征正下方或斜下方,或仅仅表示第一特征水平高度小于第二特征。
52.在本说明书的描述中,参考术语“一个实施例”、“一些实施例”、“示例”、“具体示例”、或“一些示例”等的描述意指结合该实施例或示例描述的具体特征、结构、材料或者特点包含于本发明的至少一个实施例或示例中。在本说明书中,对上述术语的示意性表述不必针对相同的实施例或示例。而且,描述的具体特征、结构、材料或者特点可以在任一个或多个实施例或示例中以合适的方式结合。此外,在不相互矛盾的情况下,本领域的技术人员可以将本说明书中描述的不同实施例或示例以及不同实施例或示例的特征进行结合和组合。
53.此外,在本发明各个实施例中的各功能单元可以集成在一个处理模块中,也可以是各个单元单独物理存在,也可以两个或两个以上单元集成在一个模块中。上述集成的模块既可以采用硬件的形式实现,也可以采用软件功能模块的形式实现。所述集成的模块如果以软件功能模块的形式实现并作为独立的产品销售或使用时,也可以存储在一个计算机可读取存储介质中。
54.尽管上面已经示出和描述了本发明的实施例,可以理解的是,上述实施例是示例性的,不能理解为对本发明的限制,本领域的普通技术人员在本发明的范围内可以对上述
实施例进行变化、修改、替换和变型。