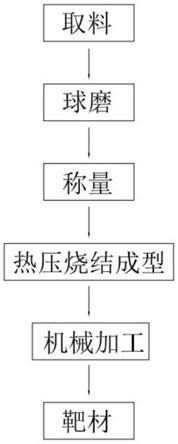
1.本申请涉及磷化铌靶材生产的技术领域,更具体地说,它涉及一种磷化铌靶材的生产工艺。
背景技术:
2.磷化铌是一种weyl半金属材料。近年来,在对weyl半金属材料的研究中,科学家制备了极薄的高导电率磷化铌薄膜,这种薄膜材料在室温下的导电率为铜的几倍,还因拓扑效应极难吸收杂质,不易产生化学变化,使得电流在电路中所散发的热量也会大幅度降低,这对制备室温低能耗电子学器件具有重大价值,为制造更大规模的集成电路提供了基础条件。
技术实现要素:
3.目前磷化铌等weyl半金属材料是全球科研工作者研究的热点材料之一,为了给研究工作和应用提供制备磁控溅射制略去磷化铌薄膜用的物质源,本申请提供一种磷化铌磁控溅射靶材的生产工艺。
4.本申请提供的一种磷化铌靶材的生产工艺,采用如下的技术方案:
5.一种磷化铌靶材的生产工艺,所述工艺包括以下步骤:将纯度≥99.9%、200目的磷化铌粉体置于球磨机中球磨,得600~800目的磷化铌粉末;将磷化铌粉末装入模具中,并将模具安装于真空热压炉内,抽真空热压炉内气压小于5pa后,通入氩气至真空热压炉内气压至0.01mpa;使真空热压炉内的温度以90~100℃/min速率升至1400~1700℃,在12~25mpa的机械压力下,烧结模具中的磷化铌粉末60~420min,随炉冷却至室温,取出得靶材坯料;对靶材坯料机械加工后清洗烘干,得磷化铌磁控溅射靶材。
6.通过采用上述技术方案,将高纯度磷化铌置于球磨机中进行球磨,使得磷化铌粉末的粒径更小,将磷化铌粉末置于模具中进行烧结时,小粒径的磷化铌粉末具有更高的烧结活性,能够提高磷化铌粉末烧结成型后的致密性,大幅度降低靶材成型后内部的孔隙率,提高了磷化铌靶材的制膜性能;将模具安装在真空热压炉内后,首先对真空热压炉进行抽真空,再注入氩气调节真空热压炉内的气压,除去真空热压炉内氧化性气体的含量,从而防止磷化铌粉末在高温环境中发生氧化,提高了磷化铌粉末的化学稳定性,进而提高了制备出磷化铌靶材的纯度;将真空热压炉以90~100℃/min的速率进行升温,使得模具中的磷化铌粉末受热均匀,且在模具中的磷化铌粉末上施加较大的机械压力,从而在远低于磷化铌熔点的情况下,对磷化铌粉末进行烧结成型;将靶材坯料配料机械加工后,使得靶材表面光滑,清洗后烘干,得到磷化铌磁控靶材,其相对致密度在96%以上,纯度在99.9%以上,是制备磷化铌weyl半金属薄膜的良好材料。
7.优选的,所述球磨机为行星球磨机,球磨大、中、小球配比为1:1:1,其中大球直径8mm,中球5.2mm,小球3.8mm;球料比(2.6~2.9):1;球磨机公转角速度200r/min;球磨时间2~2.5小时。
8.优选的,将磷化铌粉末装入模具中,并置于真空热压炉内时,先以2~5mpa的压力对磷化铌粉末进行预压。
9.通过采用上述技术方案,对磷化铌粉末进行热压成型时,先使用2~5mpa的压力对粉末进行预压,对粉末起到初步定型的作用,且能够防止在真空热压炉内调节气压时,粉末从模具中逸出,飞散在真空热压炉内。
10.优选的,升温使真空热压炉以90℃/min的速率从室温升温至600℃,再从600℃以100℃/min的速率升温至1400~1700℃。
11.优选的,所述靶材相对致密度≥96%,靶材纯度≥99.9%。
12.优选的,将磷化铌粉末加入模具中时,根据所需靶材规格,预先计算磷化铌粉末质量。
13.优选的,所述模具为石墨材质。
14.优选的,对机械加工后的靶材进行超声波清洗。
15.综上所述,本申请具有以下有益效果:
16.1、本申请采用磷化铌粉末作为靶材原料,将磷化铌粉末置于模具中,真空热压磷化铌粉末,在远低于磷化铌熔点的温度下烧结成型,得到了一种磷化铌靶材,为研究工作和应用提供了制备高性能磷化铌weyl半金属薄膜用的磁控溅射靶材。磷化铌靶材的生产技术和高性能磷化铌产品,对我国weyl半金属薄膜材料研究的开展和进步及其在更大规模集成电路上的应用有促进作用。
17.2、本申请中对磷化铌粉末进行成型烧结时,烧结温度远低于磷化铌的熔点,且将磷化铌粉末置于氩气环境中,在磷化铌粉末上施加较大的机械压力,不但能够降低生产成本,得到的磷化铌靶材的相对致密度≥96%,纯度≥99.9%。
18.3、本申请中将磷化铌置于球磨机中进行球磨,进一步降低磷化铌粉末进行烧结时的粒径,提高了磷化铌粉末的烧结活性,从而增大了磷化铌粉末烧结成型后的致密性,大幅降低靶材成型后内部的孔隙率,提高了磷化铌靶材的制膜性能。
附图说明
19.图1是本申请提供的工艺的流程图。
具体实施方式
20.以下结合附图和实施例对本申请作进一步详细说明。
21.实施例
22.实施例1
23.本实施例1制备的磷化铌靶材规格为:直径50mm
×
厚度10mm,纯度为99.99%的靶材。在其他实施例中,靶材的规格可以为φ27~460mm,厚度为1~50mm的圆形靶材,或长
×
宽=(80~400mm)
×
(80~400mm)的矩形靶材,根据所需制备磷化铌靶材的规格,选用大于所需靶材直径5~10mm的石墨材质模具,靶材坯料厚度留有2mm的余量。本申请实施例1中,选用φ55mm的石墨材质模具。本申请实施例1中,制备的靶材坯料规格为φ55mm,厚度12mm。
24.参照图1,本实施例1中,磷化铌靶材的生产工艺,包括以下步骤:
25.s1、将纯度大于99.99%的磷化铌加入行星球磨机中,球磨磷化铌粉末至600~800
目的粉体,时间2~2.5小时;其中,行星球磨机中大球直径8mm,中球5.2mm,小球3.8mm,大球、中球和小球1:1:1设置,球料比2.9:1,球磨机公转角速度200r/min;
26.s2、根据所需磷化铌靶材的规格,及所选用的石墨模具规格,留出机械加工余量,计算并称量所需磷化铌粉末的质量:m=nρv;其中n为预计靶材相对密度(取96%);ρ为磷化铌密度;v=π
×
552×
12/4000cm3;
27.s3、将精确称量出的磷化铌粉末均匀装入石墨模具中,并置于真空热压炉内,以2~5mpa的压力对磷化铌粉末进行预压后,将真空热压炉内抽气压小于5pa后,通入氩气至真空热压炉内气压为0.01mpa,以90℃/min的速率从室温升温至600℃,以100℃/min的速率升温至1400~1700℃后,以12~25mpa的压力压紧磷化铌粉末,保温60~420min后,随炉冷却至室温,取出得靶材坯料,将靶材坯料经过磨床加工、超声波清洗、烘干和包装即得到磷化铌磁控溅射靶材,检测到磷化铌靶材与磷化铌的相对致密度≥96%、纯度99.99%。
28.本具体实施例仅仅是对本申请的解释,其并不是对本申请的限制,本领域技术人员在阅读完本说明书后可以根据需要对本实施例做出没有创造性贡献的修改,但只要在本申请的权利要求范围内都受到专利法的保护。
技术特征:
1.一种磷化铌靶材的生产工艺,其特征在于,所述工艺包括以下步骤:步骤一,将纯度≥99.9%、粒径为200目的磷化铌粉末置于球磨机中球磨,得600~800目的磷化铌粉末;步骤二,将球磨后的磷化铌粉末装入模具中,并将模具安装于真空热压炉内,抽真空热压炉内气压小于5pa后,通入氩气至真空热压炉内气压至0.01mpa;步骤三,升温使真空热压炉内温度以90-100℃/min速率升至1400-1700℃,在12-25mpa的机械压力下,烧结模具中的磷化铌粉末60~420min,后随炉冷却至室温,取出得靶材坯料;步骤四,对靶材坯料机械加工后清洗烘干,得磷化铌磁控溅射靶材。2.根据权利要求1所述的一种磷化铌靶材的生产工艺,其特征在于:所述球磨机为行星球磨机,球磨大、中、小球配比为1:1:1,其中大球直径8mm,中球5.2mm,小球3.8mm;球料比(2.6-2.9):1;球磨机公转角速度为200r/min;球磨时间为2-2.5小时。3.根据权利要求1所述的一种磷化铌靶材的生产工艺,其特征在于:将磷化铌粉末装入模具中,并置于真空热压炉内时,先以小于5mpa的压力对磷化铌粉末进行预压。4.根据权利要求1所述的一种磷化铌靶材的生产工艺,其特征在于:首先使真空热压炉温度以90~100℃/min的速率从室温升温至1400-1700℃。5.根据权利要求1所述的一种磷化铌靶材的生产工艺,其特征在于:所述靶材相对致密度≥96%,靶材纯度≥99.9%。6.根据权利要求1所述的一种磷化铌靶材的生产工艺,其特征在于:将磷化铌粉末加入模具中时,根据所需靶材规格,预先计算磷化铌粉末质量。7.根据权利要求1所述的一种磷化铌靶材的生产工艺,其特征在于:所述模具为石墨材质。8.根据权利要求1所述的一种磷化铌靶材的生产工艺,其特征在于:对机械加工后的靶材进行超声波清洗。
技术总结
本发明涉及磷化铌靶材生产的技术领域,具体公开了一种磷化铌靶材的生产工艺,将纯度≥99.9%、200目的磷化铌粉体置于球磨机中球磨,得600-800目的磷化铌粉末;将球磨后的磷化铌粉末装入模具中,并将模具安装于真空热压炉内,抽真空热压炉内气压小于5Pa后,通入氩气至真空热压炉内气压至0.01MPa,使真空热压炉内的温度以90~100℃/min速率升至1400-1700℃,在12-25MPa的机械压力下,烧结模具中的磷化铌粉末60~420min,随炉冷却至室温,然后取出得靶材坯料;对靶材坯料机械加工后清洗烘干,得磷化铌磁控溅射靶材。本申请的生产工艺制备的磷化铌靶材致密度≥96%,纯度≥99.9%,是制备磷化铌薄膜或二维材料的良好物质源。备磷化铌薄膜或二维材料的良好物质源。备磷化铌薄膜或二维材料的良好物质源。
技术研发人员:舒小敏 吴文斌
受保护的技术使用者:江西科泰新材料有限公司
技术研发日:2021.11.19
技术公布日:2022/1/28