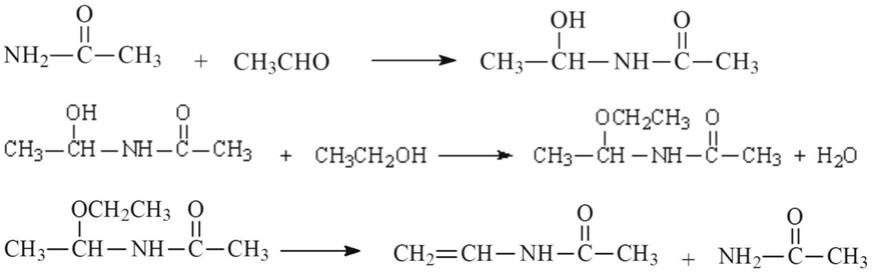
无需催化剂、高转化率、高纯度n-乙烯基乙酰胺的制备方法
技术领域
1.本发明涉及化工合成技术领域,具体涉及一种无需催化剂、高转化率、高纯度n-乙烯基乙酰胺的制备方法。
背景技术:
2.公开该背景技术部分的信息仅仅旨在增加对本发明的总体背景的理解,而不必然被视为承认或以任何形式暗示该信息构成已经成为本领域一般技术人员所公知的现有技术。
3.目前n-乙烯基乙酰胺(nva)的合成路径主要有两种:
4.(1)n-(a-烷氧乙基)-羧酸酰胺裂解法:
5.第一步羟乙基化:以乙醛、乙酰胺为原料,加入溶剂(甲醇、环己烷等),在碱性催化剂的作用下生成中间体;
6.第二步醚化:向上述物料中加入乙醇和一定的浓硫酸反应再次生成中间体;
7.第三步裂解:在高温下(400~450℃)对二次所得中间体进行裂解。
8.发明人发现,这种方法为间歇式手工操作,共分为三步进行(羟乙基化-醚化-热裂解),实验操作步骤繁琐。并且后期裂解温度太高导致副产物增多,使收率大大降低。
9.(2)n-亚乙基双乙酰胺裂解法:
10.第一步亚乙基化:以乙醛、乙酰胺为原料,在酸性催化剂的作用下生成中间产物n-(烷氧基乙基)乙酰胺;
11.第二步热裂解:对上述物料n-(烷氧基乙基)乙酰胺进行热裂解,裂解温度为180~220℃。
12.发明人发现,相对于n-(a-烷氧乙基)-羧酸酰胺裂解法,此种方法的裂解温度低,副反应少,但由于裂解温度低,导致乙酰胺的转化率仅为10%;催化剂的使用也增加了“三废”的产生。此外,n-(烷氧基乙基)乙酰胺的合成反应是一个平衡反应,反应原料会有较多剩余,反应不完全,后续分离较为繁琐;反应中使用酸作催化剂,在热裂解前需用碱将酸中和掉,不仅使得工艺繁琐,而且中和过程中不免会产生盐类固废;热裂解温度需达到400℃以上,耗能较高。
技术实现要素:
13.为了解决现有n-乙烯基乙酰胺制备过程存在的需要使用催化剂,需要酸碱中和,热裂解温度过高的问题,本发明提出一种无需催化剂、高转化率、高纯度n-乙烯基乙酰胺的制备方法。采用物理手段,通过高温高压的方法实现“一锅法”制备n-乙烯基乙酰胺,无需使用催化剂即可提高原料的转化率和n-乙烯基乙酰胺产品的纯度。
14.当选用管道反应器作为反应容器时,可以显著降低热裂解温度,当温度为200~250℃即可完成热裂解反应,能耗低,反应时间较短,可避免较多副产物的生成,反应接近于一步合成,工艺步骤也没有那么繁琐,产品提纯采用了常规的常减压蒸馏的方式,转化率相
对较高。此外,反应原料处在密闭容器中,避免了由于高温原料蒸发的问题,原料之间可以充分接触反应,反应时间较短,且转化率较高。
15.具体地,本发明是通过如下所述的技术方案实现的:
16.本发明第一方面,提供一种无需催化剂、高转化率、高纯度n-乙烯基乙酰胺的制备方法,包括以下两种方法中的至少一种:
17.采用高温高压法:以乙醛、乙酰胺、乙醇为原料,在密闭条件下,先低温预热,再高温加热,进行反应即得n-乙烯基乙酰胺;
18.或者采用管道反应器:以乙醛、乙酰胺、乙醇为原料,经管道反应器反应后,再经常压蒸馏和减压蒸馏获得n-乙烯基乙酰胺。
19.本发明第二方面,提供一种实现无需催化剂、高转化率、高纯度n-乙烯基乙酰胺的制备方法的装置,采用管道反应器制备n-乙烯基乙酰胺的装置包括:混合装置、管道反应器、常压蒸馏装置、减压蒸馏装置、冷凝装置,所述混合装置、管道反应器、常压蒸馏装置、减压蒸馏装置、冷凝装置顺序连接。
20.本发明第三方面,提供一种实现无需催化剂、高转化率、高纯度n-乙烯基乙酰胺的制备方法的装置在制备n-乙烯基乙酰胺中的应用。
21.上述一个或多个技术方案具有以下有益效果:
22.1)采用物理手段,通过高温高压的方法实现“一锅法”制备n-乙烯基乙酰胺,无需使用催化剂即可提高原料的转化率和n-乙烯基乙酰胺产品的纯度;
23.2)实验首次发现,以乙酰胺、乙醛、乙醇为原料,热裂解生产n-乙烯基乙酰胺的过程中,使用管道反应器可以明显降低热裂解温度,仅需200~250℃即可完成反应。
24.3)采用使用管道反应器生产n-乙烯基乙酰胺的过程中无需使用催化剂,避免使用催化剂带来的酸碱中和处理问题,节能环保未产生“三废”,是一条绿色合成方法。
25.4)目前常用的n-乙烯基乙酰胺生产方法无法加大反应向右的程度,但在密闭管道反应器的高压条件下,可以为此平衡反应持续不断地提供向右进行的动力,反应物持续不断的生成产品,所以参与反应的乙酰胺转化率可达97%以上,大大提高了产率。
具体实施方式
26.下面结合具体实施例,进一步阐述本发明。应理解,这些实施例仅用于说明本发明而不用于限制本发明的范围。下列实施例中未注明具体条件的实验方法,通常按照常规条件或按照制造厂商所建议的条件。
27.需要注意的是,这里所使用的术语仅是为了描述具体实施方式,而非意图限制根据本公开的示例性实施方式。如在这里所使用的,除非上下文另外明确指出,否则单数形式也意图包括复数形式,此外,还应当理解的是,当在本说明书中使用术语“包含”和/或“包括”时,其指明存在特征、步骤、操作、器件、组件和/或它们的组合。
28.为了解决现有n-乙烯基乙酰胺制备过程存在的需要使用催化剂,需要酸碱中和,热裂解温度过高的问题,本发明提出一种无需催化剂、高转化率、高纯度n-乙烯基乙酰胺的制备方法。采用物理手段,通过高温高压的方法实现“一锅法”制备n-乙烯基乙酰胺,无需使用催化剂即可提高原料的转化率和n-乙烯基乙酰胺产品的纯度。
29.当选用管道反应器作为反应容器时,可以显著降低热裂解温度,当温度为200~
250℃即可完成热裂解反应,能耗低,反应时间较短,可避免较多副产物的生成,反应接近于一步合成,工艺步骤也没有那么繁琐,产品提纯采用了常规的常减压蒸馏的方式,转化率相对较高。此外,反应原料处在密闭容器中,避免了由于高温原料蒸发的问题,原料之间可以充分接触反应,反应时间较短,且转化率较高。
30.具体地,本发明是通过如下所述的技术方案实现的:
31.本发明第一方面,提供一种无需催化剂、高转化率、高纯度n-乙烯基乙酰胺的制备方法,包括以下两种方法中的至少一种:
32.采用高温高压法:以乙醛、乙酰胺、乙醇为原料,在密闭条件下,先低温预热,再高温加热,进行反应即得n-乙烯基乙酰胺;
33.或者采用管道反应器:以乙醛、乙酰胺、乙醇为原料,经管道反应器反应后,再经常压蒸馏和减压蒸馏获得n-乙烯基乙酰胺。
34.两种方法属于同一技术构思,均是通过控制物理参数提高n-乙烯基乙酰胺的转化率和纯度。
35.高温高压法中:
36.在高温高压密闭环境中进行,例如高压釜内通过实时检测反应进程来一次性完成该反应,反应原理为:
[0037][0038]
在本发明一个或多个实施方式中,所述采用高温高压法中,低温温度为55~75℃,低温预热时间为0.5~1.5h;
[0039]
在本发明一个或多个实施方式中,所述采用高温高压法中,高温温度为170~230℃,高温加热时间为0.5~1.0h;
[0040]
反应的进行受各种因素的影响,有的反应不需要催化剂,有的反应需要催化剂,有的反应常温进行,有的需要加压或减压等等,发明人经长期实验研究发现,以乙醛、乙酰胺、乙醇为原料,常温下反应是基本不反应的,改用高温高压的形式进行反应可以达到较高的转化率,说明高压条件给予了相当大的促进和动力作用。
[0041]
该反应受温度的影响也是比较大的,较低温度下和较高温度下发生的反应也不一样,控制温度是为了原料之间分阶段进行反应。现在工业中已经有实时检测反应进程的设备,所以可以通过实时检测反应进行来逐步调整反应温度。从而达到各反应之间的进行不相互影响。
[0042]
反应本身是以主反应为主,副反应的发生受很多因素的影响,比如温度,反应时间,催化剂添加量,压力等等,反应时间过长,主反应已经达到了稳定,如果持续加热反应,就会是副反应程度增加,原料中有乙醛,乙醇,有可能发生醇的醚化反应生成醚类物质,醛
醛之间的加成反应,反应基团之间的对换等。
[0043]
在该反应中,高温加热反应时间过长使副产物增多,减少反应时间的目的主要是降低副反应的发生,在减少反应时间的同时主反应在短时间内以相同的温度条件反应程度达不到,所以适当提高温度也会增大反应的进行,从而达到较好的效果。
[0044]
优选地,所述采用高温高压法中,所述乙酰胺:乙醛:乙醇的摩尔比为0.5~1:1~2:1~2。
[0045]
在本发明一个或多个实施方式中,所述采用高温高压法中,低温预热前还包括混合搅拌的步骤,所述混合搅拌温度低于低温预热的温度。
[0046]
在使用通道反应器的方案为一步法反应,一步合成,不需要裂解,通过管道反应器的高传热效率以及背压、流速、温度条件的控制来实现一步合成所需产品,后续的常压、减压蒸馏目的仅仅是回收未反应物质,提纯产物,并不涉及裂解。
[0047]
实验室中一般使用的管道反应器规格较小,管道内部是盘旋的,从圆的层面来讲,管道反应器的规格越大,同一弧长对应的弧度会越大,这样物料的流动性会相对更流畅,更不易堵塞,且物料的进料速度是一致的,反应会相对平稳。空间效应是影响有机反应的一个重要因素,在管道反应器中,相对于大的反应釜来讲,由于反应空间相对较小,不利于副反应的进行,从而降低了副反应的发生。
[0048]
管道反应器直径一般选择8~20mm,直径越大,控制的流速相对较快,小直径管道会使物料受热更加迅速反应更加完全。
[0049]
一般来讲,流速越大,背压会越高,两者呈正比关系,根据物料的密度和反应时间衡量,流速一般控制在每小时进10~20kg物料,同时也要考虑到管道反应器的直径大小,直径越大,每小时进的料会更多,因为反应时间基本是一致的,物料要在一定的时间内通过一定长度的管道反应管。
[0050]
在本发明一个或多个实施方式中,所述采用采用管道反应器的方法中,所述管道反应器管道直径为8~20mm,优选为8~10mm。
[0051]
优选地,所述管道反应器温度为200~250℃,反应时间为3~4h。
[0052]
在亚乙基双乙酰胺热裂解生成nva的方法中,使用乙酰胺与乙醛为原料,酸作催化剂,反应升温过程中会生成白色固体,生成过程较为迅速,使得未进行反应的原料的反应受阻,必须升高温度使白色固体溶解才可继续反应,由于温度较高,乙醛会大量蒸发,即使冷凝回流,回流的乙醛遇热也会大量蒸发,使得反应时间较长,再者随着加热时间过长,内部很有可能发生聚合,且反应的转化率不到30%,转化率较低。
[0053]
而在本发明中,选用管道反应器作为反应容器存在至少两个优点:
[0054]
一是常规热裂解温度需达到400℃以上,耗能较高,管道反应器作为反应容器能显著降低反应所需热裂解温度,本发明一些实施方式中热裂解温度为200~250℃即可完成反应,能耗低,反应时间较短,可避免较多副产物的生成,反应接近于一步合成,工艺步骤也没有那么繁琐,产品提纯采用了常规的常减压蒸馏的方式,转化率相对较高,避免了以上较多问题的发生。
[0055]
常规的热裂解容器相比于管道反应器来讲,管道反应器的传热效率是远远高于常规的反应釜或裂解釜的,再者就是本发明一些方案给予的一定的压力,也起到了一定的促进作用,从而达到了降低热裂解温度的作用。
[0056]
二是选用管道反应器作为反应容器,反应原料处在密闭容器中,避免高温原料蒸发的问题,原料之间可以充分接触反应,反应时间较短,且转化率较高。
[0057]
三是传统合成方法中均使用了酸或碱催化剂,中和后会产生不可避免的盐类固废,本发明采用管道反应器,没有添加任何的催化剂,通过调节背压阀给予管道反应器内部一定的压力来促进反应的进行,这样就避免了盐类固废的产生。这样在不使用催化剂,降低热裂解温度的前提下,保证产物nva具有极高的产率和纯度。
[0058]
综上所述,本发明工艺步骤简单,耗能低,反应时间短,副产物少,废物少,转化率高,是一种符合节能,绿色,环保理念的新合成工艺。
[0059]
此外,发明人研究发现微通道反应器在亚乙基双乙酰胺热裂解的方法中是不适用的,其原因如下:
[0060]
1、原料中乙酰胺过量添加,所用的乙醛不足以将乙酰胺全部溶解,进料较困难。
[0061]
2、即使将乙酰胺高温融化后进入管道反应器,在反应过程中会生成固体使得管道堵塞,且乙酰胺融化耗能较大。
[0062]
3、裂解如果使用微通道反应器更容易使管道堵塞,亚乙基双乙酰胺的熔点要比乙酰胺高,很有可能在进入反应器的过程中就堵塞了,特别是在寒冷的冬季。因此微通道反应器在该方法中不能适用。
[0063]
乙氧基乙基乙酰胺裂解生成nva的方法中,生成乙氧基乙基乙酰胺分为两步进行,需先用乙醛、乙酰胺为原料,碱作为催化剂,生成羟乙基乙酰胺,然后加入乙醇,以酸作为催化剂生成乙氧基乙基乙酰胺,在生成羟乙基乙酰胺时,乙醛是过量添加的,即使乙醛过量也不能够将乙酰胺完全反应掉,而且此反应副产物较多,在进行醚化时,由于较多副产物及大量乙醛和乙醇的存在,在气相色谱中很难判断生成的乙氧基乙基乙酰胺的出峰位置,所以在进行醚化之前必须将部分轻组分蒸除,但是生成的羟乙基乙酰胺为黄色油状物,受此状态的影响,不管是常减压蒸馏还是加溶剂稀释进行蒸馏,都不能够将乙醛全部除去,而且随着加热时间的延长,副产物反而更多,这就使得生成的产物占比减少,即使轻杂全部除净通过醚化生成乙氧基乙基乙酰胺,在裂解时本身生成的乙氧基乙基乙酰胺就少,再加上裂解温度过高,不仅有较高能耗,副产物也会急剧增多,裂解后生成的nva更是微乎其微,后续的提纯也极为困难。
[0064]
在该方法中如果使用微通道反应器,生成的羟乙基乙酰胺为油状物,且该反应放热,需在冷却环境下进行反应,一是进料易堵,二是羟乙基乙酰胺很容易黏在管道内壁发生堵塞,因此微通道反应器在该方法中是不适用的。
[0065]
因此在本发明一个或多个实施方式中,所述管道反应器管道直径为8-10mm。
[0066]
本发明一个或多个实施方式使用的是管道反应器,不建议使用微通道反应器,一般最小的管道反应器直径都在微通道反应器的10倍以上,微通道反应器尺寸特征在1mm以下,虽然本发明中加入了超过量的乙醛与乙醇来溶解乙酰胺,还是要避免不溶的微小颗粒进入反应器发生堵塞,因此使用管道反应器而不使用微通道反应器。
[0067]
优选地,所述管道反应器反应后,还包括添加阻聚剂的步骤;
[0068]
优选地,管道反应器反应后,向体系内加入阻聚剂,接着进行常压蒸馏,收集过量的乙醛和乙醇,然后进行减压蒸馏收集顶温60~65℃馏分,冷凝即可;
[0069]
优选地,所述阻聚剂选自特丁基对苯二酚、对羟基苯甲醚、对苯二酚、2-叔丁基对
苯二酚、甲基氢醌中的至少一种;
[0070]
由于生成的n-乙烯基乙酰胺含有碳碳双键,在高温下容易发生聚合反应,加入一定量的阻聚剂是避免在生成的产品在后期的常减压蒸馏中持续加热会生成该产品的聚合物,影响产率,增加副产物。阻聚剂本身是防止聚合反应的发生,现有技术中使用了大量的阻聚剂,能达到物料的5~10%,而在本发明中使用的仅仅是50~500ppm,相比较而言阻聚剂使用量极少。
[0071]
在本发明一个或多个实施方式中,所述常压蒸馏温度为85~95℃;
[0072]
优选地,所述减压蒸馏温度为110~120℃,真空度为100~150pa;
[0073]
优选地,所述冷凝温度为-10~-15℃;
[0074]
优选地,所述乙酰胺:乙醛:乙醇的摩尔比为2:2~3:2~4;
[0075]
乙酰胺、乙醛、乙醇反应生成亚乙基双乙酰胺时,乙酰胺的添加量是过量的,由于裂解后生成的nva的沸点与乙酰胺极为接近,通过常压蒸馏与减压蒸馏都很难将其分离,使得提纯工作较为困难。本发明中原料中乙醛与乙醇是过量的,乙酰胺可以几乎全部反应掉,即使有少量残留,对产品的纯度影响也不会太大,且乙醛与乙醇沸点低,可以使用常规的蒸馏将其除去并可以回收利用,也不用担心乙酰胺与产品的分离问题。
[0076]
乙酰胺常温下是固体形式,泵入管道反应器需以液态形式进入,乙醇与乙醛均为液体,先用乙醇将乙酰胺溶解是因为溶解乙酰胺后若直接混入乙醛会由一个物理放热再冷却的过程,这样乙酰胺会重新析出变为固体,使用计量泵就无法进料了。如若需要三者同时进料,那么乙醇或乙醛必须有一者大大过量,这样对于乙酰胺的稀释程度会更大,反应进行会更慢,使用原料会更多,后处理量也比较大,所以不建议三者同时进料。因此在一些实施方式中,先将乙醇与部分乙酰胺混合,再将乙醛与剩余乙酰胺混合,分别通入管道反应器中;
[0077]
优选地,与乙醇混合的部分乙酰胺占全部乙酰胺用量的50%。
[0078]
本发明第二方面,提供一种实现无需催化剂、高转化率、高纯度n-乙烯基乙酰胺的制备方法的装置,采用管道反应器制备n-乙烯基乙酰胺的装置包括:混合装置、管道反应器、常压蒸馏装置、减压蒸馏装置、冷凝装置,所述混合装置、管道反应器、常压蒸馏装置、减压蒸馏装置、冷凝装置顺序连接。
[0079]
在本发明一个或多个实施方式中,所述混合装置用于混合乙酰胺、乙醛、乙醇;
[0080]
优选地,所述混合装置与管道反应器之间设有计量泵。
[0081]
在本发明一个或多个实施方式中,所述常压蒸馏装置设有至少一个加料口和出料口,所述加料口为阻聚剂加料口,出料口为乙醛和乙醇收集口。
[0082]
在本发明一个或多个实施方式中,所述减压蒸馏装置与冷凝装置之间设有接收罐,所述减压蒸馏装置与接收罐通过接收管连接,所述接收管外侧设有伴热带。
[0083]
本发明第三方面,提供一种实现无需催化剂、高转化率、高纯度n-乙烯基乙酰胺的制备方法的装置在制备n-乙烯基乙酰胺中的应用。
[0084]
下面结合具体的实施例,对本发明做进一步的详细说明,应该指出,所述具体实施例是对本发明的解释而不是限定。
[0085]
一、采用高温高压法制备n-乙烯基乙酰胺
[0086]
实验例1
[0087]
低温常压方法:向250ml三口烧瓶中加入乙醛41.8g,乙酰胺28g,乙醇25g,0.5g浓硫酸(催化剂),放入有水浴中,水浴温度为6℃,搅拌12h后,gc分析显示,反应无法进行,各物质之间未发生反应。
[0088]
实验例2
[0089]
高温常压方法:向250ml三口烧瓶中加入乙醛42g,乙酰胺28.3g,乙醇25.1g,0.5g浓硫酸(催化剂),放入油浴中,油浴温度设温为200℃,搅拌12h后,gc分析显示,各物质之间虽然发生了反应,但是乙酰胺的转化率仅为11.3%,由于此反应为平衡反应,所以在此条件下反应无法持续向右进行。
[0090]
实验例3
[0091]
高温高压方法:向500ml烧杯中加入乙酰胺80g,乙醇100.5g,利用磁力搅拌将乙酰胺溶解,随后加入乙醛98.3g与1g浓硫酸。向高压釜进料,开启搅拌和冷凝水循环,搅拌0.5h;设温60℃,继续反应3h;升温至180℃,反应2h,在线监测乙酰胺转化率与生成各物质的占比,结果发现,乙酰胺在此条件下的转化率可达到96%,但是由于反应时间过长,导致生成的副产物增多。
[0092]
实施例1
[0093]
高温高压条件下,缩短反应时间,适当提高反应温度的方法:向500ml烧杯中加入乙酰胺80.1g,乙醇100.3g,利用磁力搅拌将乙酰胺溶解,随后加入乙醛98.5g。向高压釜进料,开启搅拌和冷凝水循环,搅拌0.5h;设温60℃,继续反应1h;升温至200℃,反应0.5h,在线监测乙酰胺转化率与生成各物质的占比,结果发现,乙酰胺在此条件下的转化率可达到96.5%,并且最终n-乙烯基乙酰胺的纯度为98.5%,产率为97%。
[0094]
等待温度降至70℃后,放出物料,即得到合格产品。
[0095]
二、采用管道反应器制备n-乙烯基乙酰胺
[0096]
实验例4
[0097]
传统方法,n-α-烷氧基乙基羧酰胺受热分解法
[0098]
在具有蛇形冷凝管的500ml玻璃烧瓶中加入乙酰胺52.57g,甲苯(溶剂)181.65g、乙醛47.1g、碳酸氢钠(催化剂)0.3g,将-10℃的冷却水在蛇形冷凝管中流动,在氮气氛围下40℃加热搅拌6h。将分成两层的反应液中的下层用蒸发仪浓缩,未反应的乙酰胺结晶析出,过滤,粗生成物为淡黄色油状物63g,含有42%的羟乙基乙酰胺和58%的乙酰胺。对其进行纯化,用乙酸乙酯溶出羟乙基乙酰胺,进行减压浓缩获得白色固体羟乙基乙酰胺。
[0099]
向羟乙基乙酰胺中加入72g乙醇,1.2g浓硫酸,冷凝温度-10℃,在50℃下搅拌4h,得到乙氧基乙基乙酰胺粗品,含有39%的乙氧基乙基乙酰胺,
[0100]
将得到的乙氧基乙基乙酰胺粗品在405℃下进行热裂解,加热3h,得到n-乙烯基乙酰胺粗品,裂解率在55%,进行减压蒸馏,将混合物中的乙醇和羟乙基乙酰胺除去,对产品进行提纯,得到的产品纯度为97.6%。
[0101]
实验例5
[0102]
在具有蛇形冷凝管的500ml玻璃烧瓶中加入乙酰胺62.4g,环己烷(溶剂)150.95g、乙醛52.4g、碳酸钠(催化剂)0.69g,将-10℃的冷却水在蛇形冷凝管中流动,在氮气氛围下45℃加热搅拌6h。将反应液进行旋蒸,未反应的乙酰胺结晶析出,过滤,粗生成物为淡黄色油状物71g,含有45%的羟乙基乙酰胺和55%的乙酰胺。对其进行纯化,用乙酸乙酯溶出羟
乙基乙酰胺,进行减压浓缩获得白色固体羟乙基乙酰胺。
[0103]
向羟乙基乙酰胺中加入66g乙醇,2.5g浓盐酸,冷凝温度-10℃,在50℃下搅拌4h,得到乙氧基乙基乙酰胺粗品,含有35%的乙氧基乙基乙酰胺,
[0104]
将得到的乙氧基乙基乙酰胺粗品在425℃下进行热裂解,加热3h,得到n-乙烯基乙酰胺粗品,裂解率在60%,在195℃、25pa下进行精馏,严格控制回流比,将混合物中的乙醇和羟乙基乙酰胺除去,对产品进行提纯,得到的产品纯度为97.3%。
[0105]
该方法反应步骤较为繁琐,既有催化剂又有溶剂的添加,裂解温度也比较高,反应时间较长,相对于本发明,本发明操作更加简单,反应时间较短,不添加任何其它物质。
[0106]
实验例6
[0107]
传统方法,亚乙基双乙酰胺热裂解法:
[0108]
在具有蛇形冷凝管的500ml玻璃烧瓶中加入90.5g乙酰胺,27g乙醛,3.62g6m的硫酸水溶液,将-15℃的冷却水在蛇形冷凝管中流动,搅拌下加热逐步升温至130℃,内部温度达到90℃会立即生成白色固体,随着温度的逐步升高,白色固体逐步溶解,反应3h,得到的溶液中含有20%的产物,对其继续升温进行裂解,将加热温度逐步升至220℃,持续加热2h,得到的混合物中仅含有10%的产物,并且混合物中含有大量的乙酰胺,乙酰胺与n-乙烯基乙酰胺的沸点相差极小,很难实现分离,并且还没有有关该方法成功的工业化报道,所以该方法较难实现。
[0109]
实验例7
[0110]
将乙酰胺固体与乙醇按照摩尔配比为1:3的原料比将乙酰胺进行搅拌溶解,以乙酰胺与乙醛摩尔比为1:2.5的原料比与溶解后的混合液分别通过计量泵泵入内径为8mm的管道反应器,流速控制在10kg/h,通过控制泵流量使得物料体系在管道反应器中停留足1.5h,在150℃温度下进行,背压调节2mpa,反应后的乙酰胺转化率37.5%,转化率较低,提纯后的产品纯度66.3%。
[0111]
实验例8
[0112]
将乙酰胺固体与乙醇按照摩尔配比为1:3的原料比将乙酰胺进行搅拌溶解,以乙酰胺与乙醛摩尔比为1:2.5的原料比与溶解后的混合液分别通过计量泵泵入内径为8mm的管道反应器,流速控制在10kg/h,通过控制泵流量使得物料体系在管道反应器中停留足2.5h,在180℃温度下进行,背压调节2.5mpa,反应后的乙酰胺转化率49.5%,转化率较低,提纯后的产品纯度60%。
[0113]
实验例9
[0114]
将乙酰胺固体与乙醇按照摩尔配比为1:3的原料比将乙酰胺进行搅拌溶解,以乙酰胺与乙醛摩尔比为1:2.5的原料比与溶解后的混合液分别通过计量泵泵入内径为8mm的管道反应器,流速控制在10kg/h,通过控制泵流量使得物料体系在管道反应器中停留足3h,在205℃温度下进行,背压调节3mpa,反应后的乙酰胺转化率72.9%,转化率较低,提纯后的产品纯度79.9%。
[0115]
实验例10
[0116]
将乙酰胺固体与乙醇按照摩尔配比为1:3的原料比将乙酰胺进行搅拌溶解,以乙酰胺与乙醛摩尔比为1:2.5的原料比与溶解后的混合液分别通过计量泵泵入内径为12mm的管道反应器,流速控制在12kg/h,通过控制泵流量使得物料体系在管道反应器中停留足
3.5h,在210℃温度下进行,背压调节3mpa,反应后的乙酰胺转化率75.1%。转化率较低,提纯后的产品纯度80.7%。
[0117]
实施例2
[0118]
物料配比同实验例10,通过计量泵泵入内径为12mm的管道反应器,流速控制在12kg/h,通过控制泵流量使得物料体系在管道反应器中停留足3.5h,在230℃温度下进行,背压调节4mpa,反应后的乙酰胺转化率96.2%。在进行蒸馏前,向得到的物料中加入200ppm阻聚剂特丁基对苯二酚,然后进行常压蒸馏收集乙醛和乙醇、减压蒸馏得到产品,提纯后的产品纯度97.5%。
[0119]
温度和压力对反应的影响是较大的,实例2相比于实例10分别提高了20℃和1mpa的压力,从而使得转化率和纯度有了较大的提高。主要是受温度和压力的影响。
[0120]
实施例3
[0121]
物料配比同实验例10,通过计量泵泵入内径为16mm的管道反应器,流速控制在15kg/h,通过控制泵流量使得物料体系在管道反应器中停留足3.5h,在240℃温度下进行,背压调节4mpa,反应后的乙酰胺转化率97.1%。在进行蒸馏前,向得到的物料中加入100ppm阻聚剂对羟基苯甲醚和100ppm对苯二酚,然后进行常压蒸馏收集乙醛和乙醇、减压蒸馏得到产品,提纯后的产品纯度97.9%。
[0122]
实施例4
[0123]
物料配比同实验例10,通过计量泵泵入内径为16mm的管道反应器,流速控制在15kg/h,通过控制泵流量使得物料体系在管道反应器中停留足3.5h,在240℃温度下进行,背压调节4.5mpa,反应后的乙酰胺转化率98.4%。转化率较高,在进行蒸馏前,向得到的物料中加入100ppm阻聚剂2-叔丁基对苯二酚和100ppm甲基氢醌,然后进行常压蒸馏收集乙醛和乙醇、减压蒸馏得到产品,提纯后的产品纯度98.5%。
[0124]
实施例5
[0125]
物料配比同实验例10,通过计量泵泵入内径为16mm的管道反应器,流速控制在15kg/h,通过控制泵流量使得物料体系在管道反应器中停留足3.5h,在245℃温度下进行,背压调节4.5mpa,反应后的乙酰胺转化率98.9%。转化率较高,在进行蒸馏前,向得到的物料中加入200ppm阻聚剂甲基氢醌,然后进行常压蒸馏收集乙醛和乙醇、减压蒸馏得到产品,提纯后的产品纯度99%。
[0126]
以上所述仅为本发明的优选实施例而已,并不用于限制本发明,尽管参照前述实施例对本发明进行了详细的说明,对于本领域的技术人员来说,其依然可以对前述各实施例所记载的技术方案进行修改,或者对其中部分技术特征进行等同替换。凡在本发明的精神和原则之内,所作的任何修改、等同替换、改进等,均应包含在本发明的保护范围之内。