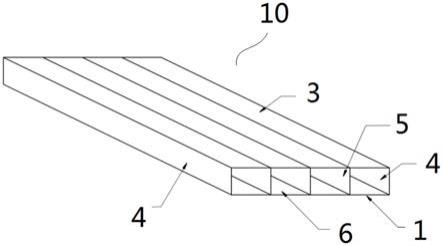
1.本发明涉及保温车厢技术领域,具体涉及一种高性能保温车厢板。
背景技术:
2.具有冷藏、保温和调温作用的车厢板,一般为“三明治”结构,具体如图1所示,由内蒙皮1、保温发泡芯材板2和外蒙皮3粘结胶合而成。其中,内蒙皮1和外蒙皮3的材质,一般选用树脂基玻璃纤维增强复合板、铝板或钢板,出于隔热、减重和防腐等原因,现大多用树脂基玻璃纤维增强复合板。树脂基玻璃纤维增强复合板与铝板或钢板相比,具有如下优点:a.铝板密度为2.7g/cm3,钢板密度为7.8g/cm3,树脂基玻璃纤维增强复合板密度为1.5-2.0g/ cm3,所以树脂基玻璃纤维增强复合板具有较大的减重优势;b.钢铁热传导系数为80w/mk,铝板热传导系数为237w/mk,树脂基玻璃纤维增强复合板热传导系数为0.4w/mk,所以树脂基玻璃纤维增强复合板具有较大的隔热保温优势;c.树脂基玻璃纤维增强复合板具有很好的耐腐蚀性,在高湿环境下,不会发生任何变化,这也是钢铁材质很难克服的使用场景。目前,保温发泡芯材板2一般为整块发泡后再进行分切成板型的硬质聚氨酯泡沫板。
[0003]“三明治”结构的车厢板,其主要成型方式为:先将内蒙皮1、保温发泡芯材板2和外蒙皮3预制成型;然后将预制成型的内蒙皮1、保温发泡芯材板2和外蒙皮3进行表面处理 (去除表面的油脂、脱模剂),并涂上粘结胶;最后用压机和锁模机构的真空压力将内蒙皮1 和外蒙皮3与保温发泡芯材板2压实,定型固化,制成具有冷藏、保温和调温功能的车厢板。
[0004]
树脂基玻璃纤维增强材料制成的蒙皮和硬质聚氨酯泡沫制成的保温发泡芯材板,制成的具有冷藏、保温、调温功能的“三明治”结构车厢板,具有以下缺陷和不足:
[0005]
(1)如图2-4所示为“三明治”结构车厢板的主要工艺流程图,其中图2为车厢板蒙皮的生产工艺流程图,图3为保温发泡芯材板的生产工艺流程图,图4为现有主流车厢板的制作工艺流程图。由流程图可知,“三明治”结构车厢板工艺流程长,生产过程机械化、自动化程度低,制造费用高,并过程质量不容易控制;
[0006]
(2)树脂基玻璃纤维增强材料蒙皮一般采用手糊工艺,纤维含量低,纤维含量只有 20%-35%,其硬度及强度低,硬度一般在20-30hba间,拉伸强度一般在80-150mpa间;
[0007]
(3)内蒙皮1和外蒙皮3与保温发泡芯材板2,采用粘结胶连接,容易出现粘结不到位,粘结强度低的问题,保温车厢在行驶过程中,蒙皮与保温芯材容易分层,导致保温车厢使用寿命不长,增加保温车厢使用成本;
[0008]
(4)制造蒙皮及保温发泡芯材需多次切割(蒙皮切割、保温泡沫芯材切割、胶合后切割),材料利用率不高于90%,并生产环境不友好。
技术实现要素:
[0009]
本发明提供一种高性能保温车厢板,增加封边和加强隔板,封边避免了保温芯材与蒙皮分层的风险,并且加强隔板实现内、外蒙皮的结构增强,使保温车厢板的稳定性得到大幅增加。
[0010]
本发明技术方案如下:
[0011]
一种高性能保温车厢板,包括壳体和保温芯材,所述壳体包括一体成型的内蒙皮、外蒙皮、封边和若干加强隔板;所述封边将所述内蒙皮和外蒙皮的左右两侧密封,所述加强隔板平行于所述封边设于所述内蒙皮和外蒙皮之间,所述加强隔板将所述壳体内部分成多个腔体;所述保温芯材均匀分布于所述腔体内。
[0012]
作为优选,所述保温芯材包括聚氨酯树脂发泡芯材,通过将所述聚氨酯树脂发泡芯材的原料灌注到所述腔体内后均匀并充分发泡形成。
[0013]
作为优选,所述内蒙皮、外蒙皮、封边和若干加强隔板均至少由一层连续长玻璃纤维和两层玻纤双轴向布制成,所述连续长玻璃纤维包裹在两层玻纤双轴向布之间。
[0014]
作为优选,所述玻纤双轴向布为0
°
和90
°
的玻纤双轴布,采用分块分区包覆的形式,依次包覆在所述连续长玻璃纤维的外部。
[0015]
作为优选,所述玻纤双轴向布包括外层双轴向布和内层双轴向布;所述外层双轴向布在所述内蒙皮、外蒙皮和封边的外表面包覆所述连续长玻璃纤维;所述内层双轴向布在所述腔体的外围包覆所述连续长玻璃纤维。
[0016]
作为优选,所述外层双轴向布包括在所述内蒙皮和封边的外表面包覆所述连续长玻璃纤维的第一外层双轴向布和在所述外蒙皮包覆所述连续长玻璃纤维的第二外层双轴向布。
[0017]
作为优选,所述腔体为长方体形状,所述内层双轴向布包括分别在所述长方体的四个侧面包覆所述连续长玻璃纤维的第一内层双轴向布、第二内层双轴向布、第三内层双轴向布和第四内层双轴向布。
[0018]
作为优选,所述连续长玻璃纤维的纱线密度为2400tex或4800tex或9600tex。
[0019]
作为优选,所述连续长玻璃纤维的重量为所述壳体重量的60%~80%。
[0020]
作为优选,所述连续长玻璃纤维的走向与所述封边的走向相同。
[0021]
上述高性能保温车厢板可采用如下方法制成:
[0022]
通过连续拉挤成型工艺,一次成型包括内蒙皮、外蒙皮、封边和若干加强隔板的保温车厢板壳体;所述封边将内蒙皮和外蒙皮的左右两侧密封,所述加强隔板平行于所述封边设于所述内蒙皮和外蒙皮之间,在所述壳体内部形成多个腔体;然后将定量的聚氨酯树脂发泡材料注入所述壳体的腔体内,使用腔体压板密封所述腔体,待发泡稳定后,卸下腔体压板,便得到所述保温车厢板。
[0023]
具体生产步骤如下:
[0024]
s1,准备阶段,取与树脂体系相容且纱线密度相同的连续长玻璃纤维;并进行纱织数核算和分纱处理;所述纱织数核算中,纱支数=〔壳体的重量
╳
连续长玻璃纤维含量百分比〕
÷
连续长玻璃纤维纱线密度,所述连续长玻璃纤维含量百分比为60%~80%,1米长度的所述壳体重量为1.8~2.0g/cm3;所述连续长玻璃纤维纱线密度包括2400tex或4800tex或9600tex;分纱处理时,将浸胶后的连续长玻璃纤维整齐、平行地穿过连续拉挤设备的穿纱板;
[0025]
s2,壳体预成型阶段,将分纱处理的连续长玻璃纤维,采用聚氨酯或环氧树脂或不饱和树脂或乙烯基树脂浸胶后,外部包覆玻纤双轴布,并均匀、平行地穿过连续拉挤设备的预成型模具的孔位,形成包括内蒙皮、外蒙皮、封边和若干加强隔板的壳体胚;
[0026]
s3,壳体连续成型阶段,将所述壳体胚送入加热的成型模具空腔内,以20-60cm/min的速度持续牵引,并依次经过连续拉挤设备的加热区和固化区,形成固定宽度的连续壳体;其中,所述成型模具空腔的模口处温度为80℃-110℃,加热区的温度为130℃-170℃,固化区的温度为130℃-160℃;
[0027]
s4,在设于所述固化区后方的切割区,将固定宽度的所述连续壳体定长切割;
[0028]
s5,在压机或工装将壳体及腔体压板固定,将按使用需求调配后注入所述腔体内,然后用所述腔体压板封闭腔体的前后端,待聚氨酯树脂发泡材料发泡稳定后从压机或工装卸下制成的保温车厢板。
[0029]
本发明相对于现有技术优势在于:
[0030]
1、本发明所述高性能保温车厢板,增加封边和加强隔板,封边避免了保温芯材与蒙皮分层的风险,并且加强隔板实现内、外蒙皮的结构增强,使保温车厢板的稳定性得到大幅增加;
[0031]
2、本发明所述高性能保温车厢板,其壳体(树脂基玻璃纤维增强材质)的纤维含量高达 65%-80%,纵向拉伸强度达到500-800mpa,是传统“三明治”结构车厢板的4-8倍,表面硬度可达60hba,大幅度提升保温车厢板的冷藏性能、保温控温性能、使用寿命及安全性;
[0032]
3、本发明所述高性能保温车厢板,采用腔体内发泡,壳体与保温泡沫芯材形成一体化,有效避免胶合分层的风险;
[0033]
4、本发明所述高性能保温车厢板,生产过程机械化程度高达90%以上,人工成本降低 60%以上,并大幅降低人为因素产生的生产缺陷;
[0034]
5、本发明所述高性能保温车厢板,工序流程短,只有壳体的连续拉挤成型和在壳体的腔体内注射聚氨酯树脂发泡材料进行发泡形成保温芯材这两道工序,取消内外蒙皮预成型工序、保温芯材发泡分切工序,以及内外蒙皮及保温芯材的胶合切割工序;使得保温车厢板的工序流程大幅度缩短,制造效率提升50%以上,更加有利于工艺质量的过程管控;
附图说明
[0035]
图1是传统“三明治”结构车厢板的示意图;
[0036]
图2是传统“三明治”结构车厢板的车厢板蒙皮的生产工艺流程图;
[0037]
图3是传统“三明治”结构车厢板的保温发泡芯材板的生产工艺流程图;
[0038]
图4是传统“三明治”结构车厢板的制作工艺流程图;
[0039]
图5是本发明所述高性能保温车厢板的壳体结构示意图;
[0040]
图6是本发明所述高性能保温车厢板的整体结构示意图;
[0041]
图7是本发明所述高性能保温车厢板的壳体材质布局示意图;
[0042]
图8是本发明所述高性能保温车厢板的生产工艺流程图。
[0043]
附图标记列示如下:
[0044]
1—内蒙皮,2—保温芯材,3—外蒙皮,10—壳体,4—封边,5—加强隔板,6—腔体, 101—连续长玻璃纤维,102—外层双轴向布,103—内层双轴向布,1021—第一外层双轴向布, 1022—第二外层双轴向布,1031—第一内层双轴向布,1032—第二内层双轴向布,1033—第三内层双轴向布,1034—第四内层双轴向布。
具体实施方式
[0045]
为了便于理解本发明,下面结合附图1-4和具体实施例,对本发明进行更详细的说明。
[0046]
实施例1
[0047]
一种高性能保温车厢板,如图5-7所示,包括壳体10和聚氨酯树脂发泡材料发泡形成的保温芯材2;所述壳体10包括内蒙皮1、外蒙皮3、封边4和若干加强隔板5;所述封边4将内蒙皮1和外蒙皮3的左右两侧密封,所述加强隔板5平行于所述封边4设于所述内蒙皮1 和外蒙皮3之间,所述加强隔板5将所述壳体10内部形成多个腔体6;将聚氨酯树脂发泡材料注入所述腔体6内,充分发泡后形成所述保温芯材2。本发明所述高性能保温车厢板增加封边4和加强隔板5,封边避免聚氨酯保温芯材2与内蒙皮1和外蒙皮3分层的风险,并且加强隔板5实现内蒙皮1和外蒙皮3的结构增强,使保温车厢板的稳定性得到大幅增加。
[0048]
作为优选,如图7所示,所述内蒙皮1、外蒙皮3、封边4和若干加强隔板5均至少由一层连续长玻璃纤维101和两层玻纤双轴向布(102,103)制成,所述玻纤双轴向布(102,103) 为0
°
和90
°
的玻纤双轴布,采用分块分区包覆的形式,依次包覆在所述连续长玻璃纤维101 的外部。
[0049]
作为优选,所述玻纤双轴向布包括外层双轴向布102和内层双轴向布103;所述外层双轴向布102在所述内蒙皮1、外蒙皮3和封边4的外表面包覆所述连续长玻璃纤维101;所述内层双轴向布103在所述腔体6的外围也即为所述内蒙皮1、外蒙皮3和封边4的内表面和所述加强隔板5的两个表面包覆所述连续长玻璃纤维101。
[0050]
作为优选,所述外层双轴向布102包括在所述内蒙皮1及封边4的外表面包覆所述连续长玻璃纤维101的第一外层双轴向布1021和在所述外蒙皮3的外表面包覆所述连续长玻璃纤维101的第二外层双轴向布1022。
[0051]
作为优选,每个所述腔体6均为长方体形状,所述连续长玻璃纤维101的走向与所述封边4的走向相同。在一个所述腔体6内,所述内层双轴向布103包括分别在所述长方体的四个侧面包覆所述连续长玻璃纤维的第一内层双轴向布1031、第二内层双轴向布1032、第三内层双轴向布1033和第四内层双轴向布1034。也即为将所述壳体10以分块分区的形式包覆分块分区包覆。
[0052]
作为优选,所述连续长玻璃纤维101的纱线密度为2400tex或4800tex或9600tex。所述连续长玻璃纤维101的重量为所述壳体10重量的60%~80%。1米长度的壳体10重量为1.8~ 2.0g/cm3,所述保温芯材重量为高性能保温车厢板重量的25%~35%,该高性能保温车厢板的纵向拉伸强度达到500-800mpa,是传统“三明治”结构车厢板的4-8倍,表面硬度可达60hba,大幅度提升保温车厢板的冷藏性能、保温控温性能、使用寿命及安全性。
[0053]
实施例2
[0054]
一种高性能保温车厢板可采用如下方法制成:通过连续成型工艺生产如图5所示的包括内蒙皮1、外蒙皮3、封边4和若干加强隔板5的壳体10;所述封边4将内蒙皮1和外蒙皮3 的左右两侧密封,所述加强隔板5平行于所述封边4设于所述内蒙皮1和外蒙皮3之间,所述加强隔板5在所述壳体10内部形成多个腔体6;然后将定量的聚氨酯树脂发泡材料20注入所述壳体10的腔体6内,使用腔体压板密封所述腔体6,待发泡稳定后,卸下腔体压板,便得到高性能保温车厢板,其整体结构如图6所示。
[0055]
本发明所述高性能保温车厢板,工序流程短,只有壳体1的连续拉挤成型和在壳体1的腔体6内注射聚氨酯树脂发泡材料进行发泡形成保温芯材2这两道工序,取消内外蒙皮预成型工序、保温芯材发泡分切工序,以及内外蒙皮及保温芯材的胶合切割工序;使得保温车厢板的工序流程大幅度缩短,制造效率提升50%以上,更加有利于工艺质量的过程管控;生产过程机械化程度高达90%以上,人工成本降低60%以上,并大幅降低人为因素产生的生产缺陷,能有效避免胶合分层的风险,且加强隔板5实现内、外蒙皮的结构增强,使保温车厢板的稳定性得到大幅增加。
[0056]
高性能保温车厢板的生产方法,其生产工艺流程图如图8所示,包括如下步骤:
[0057]
s1,准备阶段,取与树脂体系相容、且同一纱线密度的连续长玻璃纤维;并进行纱织数核算和分纱处理;纱织数核算时,纱支数=〔壳体的重量
╳
连续长玻璃纤维含量百分比〕
÷
连续长玻璃纤维纱线密度,其中,所述连续长玻璃纤维含量百分比为60%~80%,1米长度的壳体重量为1.8~2.0g/cm3,所述连续长玻璃纤维纱线密度包括2400tex或4800tex或9600tex;分纱处理时,将浸胶后的连续长玻璃纤维整齐、平行地穿过连续拉挤设备的穿纱板;
[0058]
s2,壳体预成型阶段,将分纱处理并采用聚氨酯或环氧树脂或不饱和树脂或乙烯基树脂浸胶后的连续长玻璃纤维外部包覆玻纤双轴布后均匀、平行地穿过连续拉挤设备的预成型模具的孔位,形成包括内蒙皮1、外蒙皮3、封边4和若干加强隔板5的壳体胚;其中,所述玻纤双轴布为0
°
和90
°
玻纤双轴布,采用分块分区包覆的形式,依次包覆在所述连续长玻璃纤维的外部。
[0059]
s3,壳体连续成型阶段,将所述壳体胚送入加热的成型模具空腔内,加热的成型模具空腔的模口处温度为80℃-110℃,加热区的温度为130℃-170℃,固化区的温度为130℃-160℃,以20-60cm/min的速度持续牵引,并依次经过连续拉挤设备的加热区和固化区,形成固定宽度的连续壳体1;
[0060]
s4,在设于所述固化区后方的切割区,将固定宽度的所述连续壳体1定长切割;
[0061]
s5,在压机或工装将壳体1及腔体压板固定,将聚氨酯树脂发泡材料的黑白料按使用需求调配后注入所述腔体6内,然后用所述腔体压板封闭腔体6的前后端,待聚氨酯树脂发泡材料发泡稳定后从压机或工装卸下,制成所述高性能保温车厢板。
[0062]
以上所述仅为本发明较佳的具体实施方式,但本发明的保护范围并不局限于此,任何熟悉本技术领域的技术人员在本发明揭露的技术范围内,可轻易想到的变化或替换等都应涵盖在本发明的保护范围之内。因此,本发明的保护范围应该以权利要求书的保护范围为准。