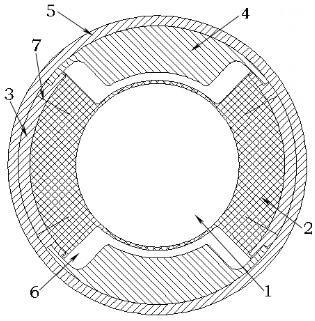
1.本发明涉及轨道交通领域,具体涉及一种液体橡胶复合节点的低径轴比调节方法及结构。
背景技术:
2.根据动力学要求转臂节点在直线高速运行(高频振动)时,提供较大的径向刚度保证运行稳定性,提高临界速度;在过曲线(低频大振幅)时,提供较小的径向刚度性能保证过曲线性能,减小磨耗;普通节点难以实现上述特性,特别对于老线路,轮轨及线路磨损较大,维护成本高,因此需要使用一种新产品同时具备上述特性—液体橡胶复合节点。
3.液体橡胶复合节点工作原理:主要通过在橡胶部件内部设计两中空型腔结构,通过流道设计将两空腔连通,预先在一型腔内灌注密封不可压缩的(粘性)液体。在载荷作用下两空腔内的容积发生变化,液体在两腔之间流动产生阻尼,消耗振动能量,达到衰减振动的目的。低频振动时,液体经通道上下流动,小刚度起到大阻尼效果,高频率区段液体来不及流动,实现大刚度特性。
4.现有的液体橡胶复合节点的橡胶体在承受径向压力时,橡胶体产生的是挤压形变。而受到液体橡胶复合节点体积的限制,难以通过增加橡胶体的厚度来减小液体橡胶复合节点的径向刚度。因此,难以实现液体橡胶复合节点刚度的小径轴比,即:径向刚度与轴向刚度的比值小。
技术实现要素:
5.本发明要解决的技术问题是:在车辆过曲线时,提供较小的径向刚度性能保证过曲线性能,减小轮轨的磨耗,同时提供较大的轴向刚度,确保车辆运行的稳定性。
6.针以上述问题,本发明提出的技术方案是:一种分瓣式液体橡胶复合节点的低径轴比刚度调节方法,液体橡胶复合节点包括芯轴、橡胶体、硫化体外套、止挡块和整体外套;硫化体外套为分瓣式的外套,在相邻的两个硫化体外套之间设置间隙,将橡胶体硫化在硫化体外套与芯轴之间,且所述硫化体外套之间的间隙延伸到橡胶体中,在止挡块和硫化体外套的外侧套上整体外套;让橡胶体承受径向压力时产生的形变为剪切与挤压的复合形变,从而减小液体橡胶复合节点的径向刚度;在芯轴上开向芯轴内侧凹陷的凹坑,在凹坑的两侧都设置凸台,在所述凹坑处设置止挡块,将芯轴的凸台的最大外径设置为大于止挡块的最小内径,让止挡块与芯轴发生轴向方向的相对移动时,芯轴的凸台能阻挡止挡块的轴向移动,从而增加液体橡胶复合节点的轴向刚度,实现液体橡胶复合节点的刚度的低径轴比。
7.优选的,将硫化体外套、橡胶体和芯轴形成的整体进行预压缩,让硫化体外套和橡胶体中的间隙完全闭合,并将所述预压缩的整体组装到整体外套;通过在径向方向挤压橡胶体,来缩小止挡块与凹坑底部的间距,从而增加止挡块与凸台的接触面积,提高液体橡胶复合节点的轴向刚度。
8.优选的,在凸台外侧设置外斜面,在硫化体外套的内侧设置有隔套斜面,在硫化在凸台的外斜面与硫化体外套的隔套斜面之间的橡胶体为斜橡胶层;通过增大凸台的外斜面的倾角和硫化体外套的隔套斜面的倾角,来增加斜橡胶层承受径向压力时,斜橡胶层的剪切形变,从而减小液体橡胶复合节点的径向刚度。
9.优选的,斜橡胶层的内侧开有向斜橡胶层的内侧凹陷的内凹槽,斜橡胶层的外侧开有向斜橡胶层的内侧凹陷的外凹槽,使得斜橡胶层在承受径向压力时,能减小液体橡胶复合节点的径向刚度。
10.优选的,通过增大凸台的外斜面的倾角和硫化体外套的隔套斜面的倾角,来增加斜橡胶层承受轴向载荷时,斜橡胶层的挤压形变,从而增加液体橡胶复合节点的轴向刚度。
11.优选的,硫化在凸台的内侧面上的橡胶体为轴向橡胶层,止挡块与芯轴发生轴向方向的相对移动且止挡块与轴向橡胶层在轴向方向上相顶时,轴向橡胶层能为液体橡胶复合节点提供轴向刚度;通过减小轴向橡胶层的厚度,能增加液体橡胶复合节点的轴向刚度。
12.一种低径轴比的分瓣式液体橡胶复合节点,包括芯轴、橡胶体、硫化体外套、止挡块和整体外套,硫化体外套为分瓣式的外套,相邻的两个硫化体外套之间设置有间隙,橡胶体硫化在硫化体外套与芯轴之间,且所述硫化体外套之间的间隙延伸到橡胶体中;芯轴、橡胶体和硫化体外套一起围成有一个外侧开口的液压腔,所述液压腔中设置有止挡块,止挡块盖合在硫化体外套上,在止挡块和硫化体外套的外侧套有整体外套;芯轴上开有向芯轴内侧凹陷的凹坑,凹坑的两侧都设置有凸台,止挡块内侧嵌在芯轴的凹坑中,当止挡块与芯轴发生轴向方向的相对移动时,芯轴的凸台能阻挡止挡块的轴向移动。
13.优选的,芯轴的凸台内侧设置有内挡面,凸台外侧设置有外斜面,硫化体外套的内侧设置有隔套斜面;硫化在凸台的内侧面上的橡胶体为轴向橡胶层,硫化在凸台的外斜面与硫化体外套的隔套斜面之间的橡胶体为斜橡胶层,斜橡胶层的厚度大于轴向橡胶层的厚度。
14.优选的,芯轴的凹坑的底部硫化的橡胶体为径向橡胶层;斜橡胶层、轴向橡胶层和径向橡胶层无缝连接在一起形成橡胶体,橡胶体与止挡块之间留有间距。
15.优选的,斜橡胶层的内侧开有内凹槽,斜橡胶层的外侧开有外凹槽,所述的内凹槽和外凹槽的形状都是向斜橡胶层的内侧凹陷的弧形槽。
16.本发明的有益技术效果是:1.将硫化体外套设置为分瓣式的外套,在相邻的两个硫化体外套之间设置间隙,将橡胶体硫化在硫化体外套与芯轴之间,且所述硫化体外套之间的间隙延伸到橡胶体中。将止挡块和硫化体外套压紧,使橡胶体产生预压缩,让硫化体外套和橡胶体中的间隙完全闭合,并将所述预压缩的整体组装到整体外套,从而组装成分瓣式液体橡胶复合节点。相比于整体式的液体橡胶复合节点,分瓣式液体橡胶复合节点在组装过程中部件之间的相互干涉会相对小些,所以分瓣式液体橡胶复合节点的斜橡胶层的径向方向的厚度能更大,倾角也能更大,且斜橡胶层中设置有间隙,斜橡胶层靠外侧的一端是裂开的,能进一步减小液体橡胶复合节点的径向刚度;同时,缩小了止挡块与凹坑底部的间距,从而增加了止挡块与凸台的接触面积,提高液体橡胶复合节点的轴向刚度。因此,分瓣式液体橡胶复合节点相比于整体式的液体橡胶复合节点的径轴比更低。
17.2.改变了现有的液体橡胶复合节点结构,将橡胶体设置为与芯轴的轴向方向成一
定倾角,即斜橡胶层采用斜角设计,使得斜橡胶层在承受径向压力时,斜橡胶层产生剪切与挤压的复合形变,从而减小了液体橡胶复合节点的径向刚度,同时有利于橡胶体抗疲劳性能,提高液体橡胶复合节点可靠性。
18.3.产品橡胶型面设计为内凹结构,即斜橡胶层的外凹槽和内凹槽都是向斜橡胶层的内侧凹陷的内凹结构,斜橡胶层的内凹结构有效降低产品的径向刚度,减小橡胶应力应变,提高产品疲劳性能。液压腔内凹型面设计还能增大液压腔体积,提高产品动态刚度特性,确保车辆在高速运行时的稳定性和可靠性。
19.4.芯轴中间段采用凸台和凹坑结合的结构设置,凸台用来提升轴向刚度,凹坑设计用来降低径向刚度,从而实现低径轴比。
20.5.斜橡胶层的立体结构类似于空心球体的一部分,可降低偏转刚度提高偏转变形能力,同时可提高疲劳可靠性。
附图说明
21.图1为实施例一的整体结构剖视示意图;图2为图1中a-a剖视图;图3为图1中去除止挡块和整体外套的结构示意图;图4为硫化体外套、止挡块和整体外套的结构剖视示意图;图5为芯轴的结构剖视示意图;图中:芯轴1、凹坑11、凸台12、内侧面121、外斜面122、橡胶体2、斜橡胶层21、内侧凹槽211、外侧凹槽212、轴向橡胶层22、径向橡胶层23、硫化体外套3、隔套斜面31、止挡块4、整体外套5、液压腔6、间隙7。
具体实施方式
22.下面结合实施例和附图对本发明做进一步的描述:实施例一如图1、图2和图3所示,将硫化体外套3设置为分瓣式的外套,在相邻的两个硫化体外套3之间设置间隙7,将橡胶体2硫化在硫化体外套3与芯轴1之间,且所述硫化体外套3之间的间隙7延伸到橡胶体2中。将止挡块4和硫化体外套3压紧,使橡胶体2产生预压缩,让硫化体外套3和橡胶体2中的间隙7完全闭合,并将所述预压缩的整体组装到整体外套5,从而组装成分瓣式液体橡胶复合节点。且芯轴1、橡胶体2和硫化体外套3一起围成有一个外侧开口的液压腔6,液压腔6中设置有止挡块4,止挡块4的纵向截面为t字形。止挡块4的上端盖合在硫化体外套3上,将液压腔6密封为一个封闭的空腔,能向封闭的液压腔6中注入液体,从而形成液体与橡胶复合的节点。整体外套5为空心的圆管状,止挡块4和硫化体外套3以预压缩的方式安装在整体外套5中,让整体外套5约束、并压紧止挡块4和硫化体外套3。轴上开有向芯轴1内侧凹陷的凹坑11,所述的凹坑11是液压腔6的下端,橡胶体2的一部分硫化在所述的凹坑11内。凹坑11的两侧都设置有凸台12,止挡块4内侧嵌在芯轴1的凹坑11中。
23.如图1、图3、图4和图5所示,芯轴1的凸台12内侧设置有内挡面,凸台12外侧设置有外斜面122,硫化体外套3的内侧设置有隔套斜面31。硫化在凸台12的内侧面121上的橡胶体2为轴向橡胶层22,硫化在凸台12的外斜面122与硫化体外套3的隔套斜面31之间的橡胶体2
为斜橡胶层21,斜橡胶层21的厚度大于轴向橡胶层22的厚度。芯轴1的凹坑11的底部硫化的橡胶体2为径向橡胶层23,斜橡胶层21、轴向橡胶层22和径向橡胶层23无缝连接在一起形成橡胶体2,橡胶体2与止挡块4之间留有间距。斜橡胶层21的宽度方向相对于芯轴1的轴线方向倾斜设置,轴向橡胶层22厚度方向设置为与芯轴1的轴线方向平行。所述芯轴1的轴线方向、斜橡胶层21的宽度方向和轴向橡胶层22厚度方向都是指图1中的左右方向。
24.本实施例中,硫化体外套3的隔套斜面31与芯轴1的轴向方向之间的夹角,即隔套斜面31的倾角为角b,角b优选的角度为40-70度;凸台12的外斜面122与芯轴1的轴向方向之间的夹角,即外斜面122的倾角为角c,角c优选的角度也为40-70度。由于斜橡胶层21是硫化在隔套斜面31与外斜面122之间,因此,隔套斜面31与外斜面122的倾角,使得斜橡胶层21也与芯轴1的轴向方向成一定倾角,即斜橡胶层21相对于芯轴1而言是采用斜角设计。
25.而现有的液体橡胶复合节点的橡胶体2,相对于芯轴1而言是采用的是平行设计,这种平行设置的橡胶体2在承受径向压力时,橡胶体2产生的是挤压形变。这种挤压形变要降低径向刚度,需要增加橡胶体2径向方向的厚度,而受到液体橡胶复合节点体积的制约,橡胶体2径向方向的厚度难以大幅度的增加。这就使得现有的液体橡胶复合节点的结构要进一步减小径向刚度非常困难。
26.本实施例中,斜橡胶层21与芯轴1的轴向方向成一定倾角,能使得斜橡胶层21在承受径向压力时,斜橡胶层21会产生剪切与挤压的复合形变。而橡胶在产生剪切形变时,其刚度小于橡胶产生挤压形变的刚度。因此,斜橡胶层21能减小了液体橡胶复合节点的径向刚度。且上述角b和角c的倾角增大时,斜橡胶层21承受径向压力,斜橡胶层21的剪切形变会更显著。因此,随着上述角b和角c倾角的增大,即:增加斜橡胶层21的倾角,能减小液体橡胶复合节点的径向刚度,同时有利于橡胶体2抗疲劳性能,提高液体橡胶复合节点可靠性。
27.在斜橡胶层21的内侧开有内凹槽,在斜橡胶层21的外侧开有外凹槽,且内凹槽和外凹槽的形状都是向斜橡胶层21的内侧凹陷的弧形槽。斜橡胶层21上开设的内凹槽和外凹槽,减小了斜橡胶层21在轴向方向上的宽度,能进一步减小液体橡胶复合节点的径向刚度。且内凹槽和外凹槽都是向斜橡胶层21的内侧凹陷,而不是向斜橡胶层21的外侧凸起。因此,当斜橡胶层21产生径向方向的压缩形变时,斜橡胶层21不会产生折皱,能提高斜橡胶层21的抗疲劳性能,不易开裂。
28.止挡块4嵌在液压腔6中,且止挡块4内侧嵌在凹坑11中,止挡块4的最小外径小于芯轴1的凸台12的最大外径。使得当止挡块4与芯轴1发生轴向方向的相对移动时,止挡块4的内侧会与凸台12的外侧相顶,因此,芯轴1的凸台12能阻挡止挡块4的轴向移动。
29.止挡块4受到轴向的推力,止挡块4会沿轴向方向产生位移。当止挡块4还与轴向橡胶层22之间存在间隙7时,液体橡胶复合节点的轴向刚度主要由斜橡胶层21提供。且上述隔套斜面31的倾角b和外斜面122的倾角c增大时,斜橡胶层21承受轴向的推力,斜橡胶层21的挤压形变会更显著。而橡胶在产生挤压形变时,其刚度大于橡胶产生剪切形变的刚度。因此,增加斜橡胶层21的倾角,能增大液体橡胶复合节点的轴向刚度。
30.止挡块4沿轴向方向产生位移,且止挡块4与轴向橡胶层22相顶时,液体橡胶复合节点的轴向刚度由斜橡胶层21和轴向橡胶层22一起提供。由于,轴向橡胶层22的轴向厚度小于斜橡胶层21的轴向厚度,且轴向橡胶层22主要是挤压形变来产生轴向刚度。因此,轴向橡胶层22能提供的最大轴向刚度要大于斜橡胶层21能提供的最大轴向刚度,从而使得液体
橡胶复合节点的轴向刚度能大幅度提升。
31.如图1至图5所示,液压腔6是个封闭的空腔,液压腔6中注入有液体,芯轴1上设置凹坑11以及在斜橡胶层21上设置向内侧凹陷的内侧凹槽211,都增大了液压腔6的容积。而车辆在直线高速运行(高频振动)时,大容积的液压腔6能更有效的提供较大的径向刚度保证运行稳定性,提高临界速度。在过曲线(低频大振幅)时,大容积的液压腔6能更有效的提供较小的刚度性能保证过曲线性能,减小磨耗。因此,芯轴1上设置的凹坑11和斜橡胶层21上设置的内侧凹槽211,增大了液压腔6的容积,让液压腔6中能容纳更多的液体,提高了产品动态刚度特性,确保了车辆在小曲率半径转弯和高速运行时的稳定性和可靠性。
32.本实施例中,通过改变液体橡胶复合节点的结构来减小液体橡胶复合节点的径向刚度,且通过改变液体橡胶复合节点的结构来增大液体橡胶复合节点的轴向刚度,从而实现液体橡胶复合节点的刚度低径轴比的调节。且相比于整体式的液体橡胶复合节点,分瓣式液体橡胶复合节点在组装过程中部件之间的相互干涉会相对小些,所以分瓣式液体橡胶复合节点的斜橡胶层21的径向方向的厚度能更大,倾角也能更大,且斜橡胶层21中设置有间隙7,斜橡胶层21靠外侧的一端是裂开的,能进一步减小液体橡胶复合节点的径向刚度。同时,缩小了止挡块4与凹坑11底部的间距,从而增加了止挡块4与凸台12的接触面积,提高液体橡胶复合节点的轴向刚度。因此,分瓣式液体橡胶复合节点相比于整体式的液体橡胶复合节点的径轴比更低。
33.显然,在不脱离本发明所述原理的前提下,作出的若干改进或修饰都应视为本发明的保护范围。