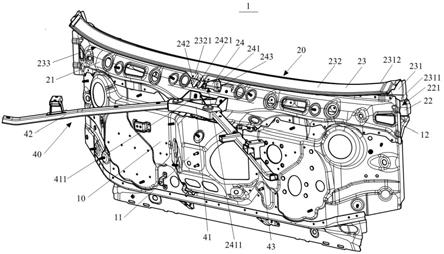
1.本实用新型涉及车辆技术领域,具体地涉及一种用于车辆的风窗横梁结构、前围板组件和车辆。
背景技术:
2.汽车,一般指由动力驱动、具有4个或4个以上车轮的非轨道承载的车辆。汽车的主要作用是代步、载人和运输等,它在给人们的生活带来便捷的同时,也提高了就业机会,促进了产业发展,加快了经济提升。
3.无论是在汽车的设计、生产、销售和使用的哪个环节,安全性始终是首要考量因素。为了提升整车的安全性能,各种主动防护系统和被动防护系统被应用到汽车中。其中,主动防护系统包括防抱死制动系统(即abs)、牵引力控制系统(即trc)、电子稳定装置(即esp)、车辆稳定控制系统(即vsc)等,其主要作用是防患于未然,避免事故的发生;被动防护系统包括安全带、安全气囊、车身的前后吸能区、和车身防撞钢梁等,其主要作用是在发生事故时汽车对被撞车辆、车内人员和被撞行人的保护。
4.近年来,随着汽车安全技术的不断发展,特别是2009年国家推荐标准《gb/t 24550-2009 汽车对行人的碰撞保护》的颁布后,行人保护受到越来越多的关注和重视。当行人与汽车发生碰撞时,行人的头部通常会在发动机舱盖和前挡风玻璃之间的区域内发生接触。在这一区域内,发动机舱盖和前挡风玻璃的扭转刚度均较弱,对行人的头部损伤较小。但是,为了给前挡风玻璃提供足够的支撑,风窗横梁结构的扭转刚度相对较大,其对车辆的hic(head injury criterion,即头部损伤判据)性能的影响较大。
5.为了提升风窗横梁结构对行人保护的碰撞性能,现有技术作了大量的研究和尝试。例如,中国实用新型专利cn214165136u公布了一种风窗横梁结构及汽车。该风窗横梁结构布置于汽车发盖总成的下方及前围板的前方,其包括相互配合围成封闭腔体的风窗上横梁和风窗下横梁,风窗上横梁与前围板的接合点低于风窗上横梁,并且风窗上横梁与前围板的接合点与发盖总成形成碰撞吸能间隙,从而提高汽车的行人保护碰撞性能。然而,当行人碰撞到该风窗横梁结构上时,上述碰撞吸能间隙如果不能将碰撞产生的应力完全吸收,行人的头部有可能直接与刚性较强的风窗上横梁和风窗下横梁接触而造成损害。因此,该风窗横梁结构存在改进的可能性。
6.相应地,本领域需要一种新的技术方案来解决上述问题。
技术实现要素:
7.为了解决现有技术中的上述问题,即为了解决现有技术中风窗横梁结构对行人的头部容易造成较大损害的技术问题,本实用新型提供一种风窗横梁结构。该风窗横梁结构配置成可固定在所述车辆的前围板上,其包括:外横梁和内横梁,所述外横梁和所述内横梁彼此间隔地布置在所述前围板的上部;和上横梁,所述上横梁具有彼此相接的竖向板和斜向板,所述竖向板的下边缘分别与所述外横梁和所述内横梁形成固定连接,并且所述斜向
板配置成从所述竖向板的与所述下边缘相对的上边缘朝向所述车辆的前部倾斜向下地延伸,使得在所述上横梁和所述外横梁之间间隔出半封闭的腔体。
8.在本实用新型风窗横梁结构中包括外横梁、内横梁和上横梁。外横梁和内横梁彼此间隔地布置在车辆的前围板的上部。上横梁具有彼此相接的竖向板和斜向板,使得该上横梁具有大致v形的形状。其中,竖向板的下边缘分别与外横梁和内横梁形成固定连接,使得风窗横梁结构具有稳定的结构,以便为前风挡玻璃提供足够的机械支撑。斜向板从竖向板的上边缘朝向车辆的前部倾斜向下地延伸,使得上横梁和外横梁之间间隔出半封闭的腔体。斜向板布置在竖向板的上边缘,而外横梁和内横梁布置在竖向板的下边缘,因此当行人碰撞到该风窗横梁结构上时,将会与容易产生变形的单层钣金结构的斜向板发生接触,而不会直接与扭转刚度较大双层钣金结构的外横梁和内横梁接触。另外,斜向板和外横梁之间的半封闭的腔体可以为上横梁(包括斜向板和竖向板)变形提供缓冲空间,进一步提升溃缩吸能效果,有效降低碰撞对行人(特别是头部)的损害,使该风窗横梁结构具有较强的行人保护性能。
9.在上述风窗横梁结构的优选技术方案中,所述外横梁、所述竖向板和所述内横梁通过三层焊接工艺固定连接在一起。通过上述的配置,可以使外横梁、上横梁、和内横梁之间形成牢固且稳定的连接,以延长使用寿命。
10.在上述风窗横梁结构的优选技术方案中,在所述腔体的中部设有支撑件,所述支撑件具有固定在所述斜向板上的第一端和固定在所述外横梁上的第二端。支撑件的设置,可以适当增强斜向板的扭转刚度,满足机械性能要求。
11.在上述风窗横梁结构的优选技术方案中,所述支撑件为u形件,并且所述u形件具有朝向所述车辆的前部且倾斜向下的开口。u形件的设置,可以使支撑件具有简单的结构,便于加工。另外,u形件还可以在上横梁发生碰撞时容易地变形,从而不会影响上横梁的溃缩吸能性能。
12.在上述风窗横梁结构的优选技术方案中,从所述斜向板的中部形成有朝向所述车辆的前部倾斜向下延伸的固定凸耳,并且所述第一端配置成固定在所述固定凸耳上。通过上述的设置,可以使支撑件方便地固定在斜向板的固定凸耳上,从而提升装配效率。
13.为了解决现有技术中的上述问题,即为了解决现有技术中风窗横梁结构对行人的头部容易造成较大损害的技术问题,本实用新型提供一种前围板组件。该前围板组件包括:前围板;和根据上面任一项所述的用于车辆的风窗横梁结构,并且所述风窗横梁结构固定在所述前围板的上部。通过采用上面任一项所述的风窗横梁结构,本实用新型前围板组件可以有效降低碰撞对行人的损害,提升hic性能。
14.在上述前围板组件的优选技术方案中,所述外横梁、所述竖向板、所述内横梁和所述前围板的上部一起围成加强腔体。外横梁、竖向板、内横梁和前围板的上部一起围成加强腔体,可以增强整个前围板组件的扭转刚度,进而在使用该前围板组件的情况下提升整车的扭转刚度,以满足机械强度要求。
15.在上述前围板组件的优选技术方案中,在所述加强腔体的中部设有安装支架,所述安装支架具有固定在所述前围板的上部的第一连接部、固定在所述内横梁上的第二连接部、和固定在所述竖向板上的第三连接部。在加强腔体内设置安装支架,一方面可以利用加强腔体内的空间,提升空间利用率,另一方面与前围板、内横梁、和竖向板形成互连的安装
支架,也可进一步增强整个前围板组件的扭转刚度,进而提升整车的扭转刚度。
16.在上述前围板组件的优选技术方案中,所述前围板组件还包括加强支架,所述加强支架包括中间固定部、从所述中间固定部的左右两侧分别倾斜地朝向所述车辆的前部延伸的第一加强杆和第二加强杆,并且所述中间固定部配置成抵靠在所述外横梁上并可拆卸地固定在所述安装支架上。通过设置加强支架,可以进一步增强整个前围板组件的扭转刚度,进而提升整车的扭转刚度。
17.为了解决现有技术中的上述问题,即为了解决现有技术中风窗横梁结构对行人的头部容易造成较大损害的技术问题,本实用新型提供一种车辆。该车辆包括上面任一项所述的前围板组件。通过采用上面任一项所述的前围板组件,本实用新型车辆可以有效降低碰撞对行人的损害,以提升整车的hic性能。
附图说明
18.下面结合附图来描述本实用新型的优选实施方式,附图中:
19.图1是本实用新型前围板组件的实施例的结构示意图;
20.图2是本实用新型风窗横梁结构装配到前围板上的实施例的结构示意图;
21.图3是本实用新型风窗横梁结构中去除外横梁的实施例的结构示意图。
22.附图标记列表:
23.1、前围板组件;10、前围板;11、前围板本体;12、上部;20、风窗横梁结构;21、外横梁;22、内横梁;221、加强腔体;23、上横梁;231、竖向板;2311、下边缘;2312、上边缘;232、斜向板;2321、固定凸耳;233、腔体;24、支撑件;241、u形件;2411、开口;242、第一端;2421、定位槽;243、第二端;30、安装支架;31、安装支架本体;311、安装孔;312、减重孔;32、第一连接部;33、第二连接部;34、第三连接部;40、加强支架;41、中间固定部;411、安装件;42、第一加强杆;43、第二加强杆。
具体实施方式
24.下面参照附图来描述本实用新型的优选实施方式。本领域技术人员应当理解的是,这些实施方式仅仅用于解释本实用新型的技术原理,并非旨在限制本实用新型的保护范围。
25.需要说明的是,在本实用新型的描述中,术语“上”、“下”、“左”、“右”、“内”、“外”等指示的方向或位置关系的术语是基于附图所示的方向或位置关系,这仅仅是为了便于描述,而不是指示或暗示所述装置或元件必须具有特定的方位、以特定的方位构造和操作,因此不能理解为对本实用新型的限制。此外,术语“第一”、“第二”仅用于描述目的,而不能理解为指示或暗示相对重要性。
26.此外,还需要说明的是,在本实用新型的描述中,除非另有明确的规定和限定,术语“安装”、“设置”、“连接”应做广义理解,例如,可以是固定连接,也可以是可拆卸连接,或一体地连接;可以是直接相连,也可以通过中间媒介间接相连,还可以是两个元件内部的连通。对于本领域技术人员而言,可根据具体情况理解上述术语在本实用新型中的具体含义。
27.为了解决现有技术中风窗横梁结构对行人的头部容易造成较大损害的技术问题,本实用新型提供一种该风窗横梁结构20。该风窗横梁结构20配置成可固定在车辆的前围板
10上,其包括:外横梁21和内横梁22,外横梁21和内横梁22彼此间隔地布置在前围板10的上部12;和上横梁23,上横梁23具有彼此相接的竖向板231和斜向板232,竖向板231的下边缘2311分别与外横梁21和内横梁22形成固定连接,并且斜向板232配置成从竖向板231的与下边缘2311相对的上边缘2312朝向车辆的前部倾斜向下地延伸,使得在上横梁23和外横梁21之间间隔出半封闭的腔体233。
28.图1是本实用新型前围板组件的实施例的结构示意图;图2是本实用新型风窗横梁结构装配到前围板上的实施例的结构示意图;图3是本实用新型风窗横梁结构中去除外横梁的实施例的结构示意图。如图1-图3所示,在一种或多种实施例中,本实用新型前围板组件1包括前围板10、风窗横梁结构20、安装支架30、和加强支架40等部件。
29.如图1-图3所示,在一种或多种实施例中,前围板10具有大致沿竖直方向延伸的前围板本体11,以便将发动机舱室和车厢分隔开,防止发动机舱室的废气、热量、噪音窜入车厢内,从而提升车厢内人员的驾乘体验。在一种或多种实施例中,前围板本体11采用镀锌钢板通过冲压工艺加工而成,使得前围板本体11具有足够的机械强度,以便对驾乘人员提供有力保护。在前围板本体11上设置有多个安装孔(图中未标注),用于布置车辆的线束、转向管柱、制动踏板、空调系统等部件,以提升整车的集成化程度。
30.如图1-图3所示,本实用新型风窗横梁结构20配置成固定在前围板10的上部12。在一种或多种实施例中,该风窗横梁结构20包括外横梁21、内横梁22、和上横梁23。其中,外横梁21和内横梁22彼此间隔地固定在前围板10的上部12。在一种或多种实施例中,外横梁21和内横梁22均采用镀锌钢板通过冲压工艺加工而成,以简化制造工艺,降低制造成本。基于图1所示的方位,外横梁21竖直地固定在前围板10的前侧(即靠近车辆的前部),而内横梁22竖直地固定在前围板10的后侧(即靠近车辆的后部)。另外,外横梁21和内横梁22均沿大致车辆的左右方向延伸,以提升整车的扭转刚度。外横梁21、内横梁22和前围板10的固定方式包括但不限于电阻点焊(rsw,即resistance spot welding)、熔化极气体保护电弧焊(gmaw,即gas metal arc welding)等。
31.继续参见图1-图3,在一种或多种实施例中,上横梁23包括彼此相接且均沿车辆的左右方向(即车辆的宽度方向)延伸的竖向板231和斜向板232,使得上横梁23具有简单的结构,易于加工。上横梁23可采用镀锌钢板等合适的金属材质通过冲压工艺加工而成。替代地,竖向板231和斜向板232也进而分别单独加工再固定在一起。竖向板231为大致长方形的板状结构。该板状结构具有相对的下边缘2311和上边缘2312。在一种或多种实施例中,外横梁21、内横梁22分别在竖向板231的下边缘2311形成固定连接。在一种或多种实施例中,外横梁21、竖向板231和内横梁22之间通过三层焊接工艺固定在一起,使得该风窗横梁结构20具有牢固且稳定的结构。如图1所示,在一种或多种实施例中,在组装状态下,外横梁21、竖向板231、内横梁22和前围板10的上部12一起围成加强腔体221,可以增强整个前围板组件1的扭转刚度,以满足机械强度要求。
32.继续参见图1-图3,在一种或多种实施例中,斜向板232配置成从竖向板231的上边缘2312朝向车辆的前部倾斜向下地延伸,使得整个上横梁23具有大致v形的截面。斜向板232也为大致长方形的板状结构。在斜向板232和外横梁21之间间隔出半封闭的腔体233。更具体地,该腔体233由斜向板232、外横梁21、和竖向板231一起围成。在斜向板232与外横梁21之间相距一定距离以在二者之间形成朝向车辆前部的开口,并且该开口也为腔体233的
开口,因此该腔体233被称为“半封闭的腔体”。通过上述的配置,当行人与车辆发生碰撞而与风窗横梁结构20发生接触时,由于斜向板232在竖直方向上高于外横梁21和内横梁22,因此行人首先会与容易变形的单层钣金件的斜向板232接触,而不会直接与扭转刚度较大的双层钣金件的外横梁21和内横梁22接触。另外,斜向板232和外横梁21之间的腔体233可以为上横梁23(包括斜向板232和竖向板231)产生变形提供足够的缓冲空间,进一步提升溃缩吸能效果。另外,倾斜设置的斜向板232还可以方便地与前风挡玻璃相配,以便将从前风挡玻璃流下的雨水等引导至斜向板232下部的落水槽(图中未示出)内将其排出。
33.继续参见图1-图3,在一种或多种实施例中,风窗横梁结构20还包括布置在腔体233中的支撑件24。支撑件24可采用镀锌钢、不锈钢、铸铁等合适的金属材料通过机械加工工艺制造而成。支撑件24具有相对的第一端242和第二端243。其中,第一端242固定在斜向板232上,而第二端243固定在外横梁21上。固定方式包括但不限于电阻点焊、熔化极气体保护电弧焊等。支撑件24的设置,可以适当地增加整个风窗横梁结构20的扭转刚度,以满足机械强度要求。在一种或多种实施例中,在斜向板232的中部形成有用于固定第一端242的固定凸耳2321,使得第一端242可以方便地固定在斜向板232上,以提高装配效率。固定凸耳2321配置成从斜向板232的前侧边缘朝向车辆的前部倾斜向下延伸。在一种或多种实施例中,固定凸耳2321具有大致梯形的形状。替代地,固定凸耳2321也可设置成半圆形、三角形或者其它合适的形状。在一种或多种实施例中,在支撑件24的第一端242上还形成有从第一端242的前侧边缘朝向车辆的后部方向延伸的定位槽2421,以便与布置在斜向板232下部的落水槽相配,提高落水槽的装配效率。在一种或多种实施例中,支撑件24为u形件241。该u形件241具有朝向车辆的前部且倾斜向下的开口2411。u形件241的设置,可以使支撑件24具有简单的结构,便于加工。另外,u形形状的支撑件24也可以在外力作用下方便地压缩变形,而不会影响上横梁23的溃缩吸能性能。
34.如图3所示,在一种或多种实施例中,安装支架30布置在由外横梁21、竖向板231、内横梁22和前围板10的上部12一起围成的加强腔体221内。安装支架30具有安装支架本体31。该安装支架本体31可采用镀锌钢、不锈钢、铸铁等合适的金属材料通过机械加工工艺制造而成。在安装支架本体31上设有4个安装孔311,每个安装孔311可与安装件411相配,以便安装加强支架40。安装孔311也可设置成比4个多或少的其它合适的数量。在一种或多种实施例中,在安装支架本体31的中部还设有减重孔312,以降低安装支架30的重量,提升整车的轻量化程度。安装支架30还具有与前围板10形成固定连接的第一连接部32、与内横梁22形成固定连接的第二连接部33、和与竖向板231形成固定连接的第三连接部34,使得通过安装支架30可以进一步增强前围板10、内横梁22和上横梁23之间的固定连接。
35.如图1所示,在一种或多种实施例中,加强支架40包括中间固定部41、第一加强杆42、和第二加强杆43等部件。加强支架40可采用不锈钢、铝合金、铸铁等合适的金属材质加工而成。加强支架40的设置,可以进一步增强整车的扭转刚度。其中,中间固定部41抵靠在外横梁21上,并通过4个与安装孔311配合的安装件411可拆卸地固定在安装支架30上。安装件411包括但不限于螺钉、螺栓等。替代地,安装件411的数量也可设置成比4个多或少的其它合适的数量,只要能够与安装孔311相配使加强支架40牢固且稳定地固定在安装支架30上即可。基于图1所示的方位,第一加强杆42配置成从中间固定部41的左侧端面倾斜地向左后方延伸(朝向车辆前部延伸),第二加强杆43配置成从中间固定部41的右侧端面倾斜地向
右后方延伸(朝向车辆前部延伸)。在一种或多种实施例中,第一加强杆42和第二加强杆43相对于中间固定部41的竖直中心线对称布置,使得加强支架40具有简单、规整的结构,便于加工。在一种或多种实施例中,第一加强杆42和第二加强杆43均为具有长方形截面的中空管,以减轻其重量。替代地,第一加强杆42和第二加强杆43也可设置成具有其它合适形状的截面的中空管,例如圆形、椭圆形等。
36.在一种或多种实施例中,本实用新型车辆(图中未示出)为轿车。替代地,该车辆也可为suv(sport utility vehicle,即运动型多用途汽车)、mpv(multi-purpose vehicles,即多用途车辆)或者其它合适的车辆。在一种或多种实施例中,该车辆为电动汽车。该电动汽车可以是纯电动汽车、混合动力汽车或燃料电池汽车。替代地,该车辆也可为燃油汽车,或者其它合适的车辆。该车辆包括上面任一实施例所述的前围板组件1。该车辆还包括但不限于车身、车轮、车座、发动机舱盖、前风挡玻璃等其它部件。通过采用上面任一实施例所述的前围板组件1,本实用新型车辆可以有效降低碰撞对行人的损害,以提升整车的hic性能。
37.至此,已经结合附图所示的优选实施方式描述了本实用新型的技术方案,但是,本领域技术人员容易理解的是,本实用新型的保护范围显然不局限于这些具体实施方式。在不偏离本实用新型的原理的前提下,本领域技术人员可以对相关技术特征作出等同的更改或替换,这些更改或替换之后的技术方案都将落入本实用新型的保护范围之内。