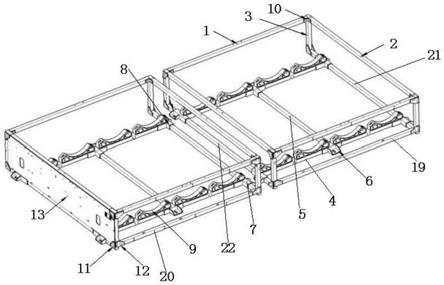
1.本发明属于新能源汽车技术领域,特别是一种轻量化镁合金气瓶框架。
背景技术:
2.新能源汽车是取代燃油汽车最理想、最有希望的绿色交通工具,随着新能源汽车的兴起,其相关问题越来越受到人们的重视,最重要的就是汽车的轻量化问题。汽车轻量化是实现汽车环保、节能和减排的的重要途径。对于汽车而言,车厢越轻,意味着载重量的增加,即运输效率的提高。因此汽车轻量化技术成为当今世界上各汽车厂商争相追逐的研究重点。汽车要实现轻量化主要有两个途径,一是汽车结构设计的优化,二是使用轻量化材料,特别是复合材料。前者经过不断的研究,技术手段已经非常先进,轻量化减重的空间已经非常狭窄。后者随着材料科学技术的发展,为汽车轻量化开辟了广阔空间。
3.目前市面上流行的是一种铝合金气瓶框架,其结构完整,各横梁、纵梁、支撑梁均采用挤压成型的工艺制造而成,操控侧板用铝合金板材制作,梁之间用角块焊接形成整副框架;铝合金密度约2.7g/cm,整副气瓶框架具有较轻的重量,对提高运输效率有一定的积极作用。但是,虽然重量比较轻,但连接性能有限,其整体性较差,整体强度较弱,汽车在行驶途中,使得气瓶框架易受振动冲击力损坏,使用寿命不长。
技术实现要素:
4.本发明所要解决的技术问题是针对上述缺陷,提供一种以镁合金材料为基础结合整体性的结构设计,以便在减轻气瓶框架重量的基础上提高框架强度,进而提高汽车的运输效率,提高经济效益。
5.为解决上述技术问题,本发明所采用的技术方案是一种轻量化镁合金气瓶框架,包括左右并列的两个框架体,所述框架体由横梁、纵梁、支撑梁、载重梁、短纵梁、第一套接筒、第二套接筒、第三套接筒、瓶托、直角片、第一铆接块、第二铆接块、铆钉和操控侧板组装而成;其中所述横梁、纵梁、支撑梁、载重梁、短纵梁、第一套接筒、第二套接筒、第三套接筒和瓶托采用镁合金材料制作,所述直角片、第一铆接块、第二铆接块、铆钉采用不锈钢材料制作,所述操控侧板采用铝合金材料制作。
6.所述第一套接筒包括方形孔筒、矩形孔筒和框型板,所述矩形孔筒上钻设有铆接孔,所述框型板上钻设有第一腰型孔,所述第一腰型孔用于将框架固定在车辆上,所述方形孔筒垂直设置在矩形孔筒的正侧面中部,所述框型板垂直设置在矩形孔筒的背侧面中部,构成第一套接筒。
7.所述第二套接筒包括方形孔筒、矩形孔筒和框型板,所述矩形孔筒上钻设有铆接孔,所述框型板上钻设有第一腰型孔,所述矩形孔筒垂直设置在方形孔筒的正侧面,所述框型板垂直设置在方形孔筒的背侧面的右边部,构成第二套接筒。
8.所述第三套接筒包括方形孔筒、矩形孔筒和框型板,所述矩形孔筒上钻设有铆接孔,所述框型板上钻设有第一腰型孔,所述矩形孔筒垂直固定在方形孔筒的正侧面,所述框
型板垂直设置在方形孔筒的背侧面的左边部,构成第三套接筒。
9.所述瓶托由底板、托板、内撑板、外撑板和固位板一体生成固定连接,其中托板为弧形板,其余均为直条板,所述固位板上钻设有第二腰型孔,所述第二腰型孔用于固定氢气瓶,所述底板上钻设有铆接孔;所述底板的两端各连接一个外撑板,底板的中部连接若干个内撑板,内撑板的顶部连接托板,托板的两端各连接一个固位板,两个固位板各连接底板两端的外撑板,构成瓶托。
10.所述横梁、纵梁、支撑梁和短纵梁为方形管,采用镁合金挤压成型。
11.所述载重梁为矩形管,中间设计有加强肋,采用镁合金挤压成型;整副框架安装气瓶后,需吊装到车顶,所以在载重梁侧面设置有吊装孔。
12.所述操控侧板为长方形板体,其长度等于纵梁的长度,其宽度等于支撑梁的长度。一般采用铝合金板材通过水切割工艺制作而成,上面设有铆接孔,以及用于安装各种传感器、气阀的安装孔。
13.所述直角片、第一铆接块和第二铆接块一般采用不锈钢板通过水切割工艺制作而成,上面设有铆接孔。
14.其组装方法包括如下步骤进行:
15.⑴
取两根横梁和两根纵梁相间首尾连接成长方形,并在连接处用直角片和铆钉铆接固定,构成上框架;
16.⑵
取一根横梁和两根纵梁相间连接成缺一根横梁框边的长方形,并在连接处用直角片和铆钉铆接固定,构成缺边下框架;其中一根纵梁为右纵梁,另一根纵梁为左纵梁;采用这种缺边下框架既便于安装工型托架,又可减轻整体重量。
17.⑶
取两根载重梁、一根短纵梁和两只第一套接筒,将两只第一套接筒的矩形孔筒分别套插在两根载重梁的中部,再将短纵梁的两端分别插入在两只第一套接筒的方形孔筒中,然后用铆钉铆接固定,构成工型架。
18.⑷
取八只瓶托,将八只瓶托的底板分别用铆钉铆接固定在工型架中载重梁的上表面上,且短纵梁的两侧的载重梁上各安装两只,且两根载重梁上的瓶托两两对齐,构成工型托架。
19.⑸
取两只第二套接筒和两只第三套接筒,依次将第二套接筒和第三套接筒中的矩形孔筒插在工型托架的载重梁的两端,然后将第(2)步形成的缺边下框架从缺边方向插入第二套接筒和第三套接筒的方形孔筒,调整工型托架到缺边下框架的中间位置,然后用铆钉铆接固定,构成下框托架。
20.⑹
取四根支撑梁,将上框架的四个转角和下框托架的两个转角及两个边端一一对齐并用支撑梁连接,并在连接处的纵梁与支撑梁的外侧边用第一铆接块和铆钉铆接固定,将连接处的横梁与支撑梁的外侧边用第二铆接块和铆钉铆接固定;构成右框架体。
21.⑺
在铆接固定纵梁和支撑梁后,将操控侧板与纵梁和支撑梁所构成的侧边框并接,然后用铆钉铆接固定,构成左框架体。
22.使用时,将八个氢气瓶固定在瓶托上面,然后通过吊装孔分别将两个框架体吊上车顶,将左框架体和右框架体并列,并经过第一腰型孔连接安装在汽车车顶上,然后将相关传感器固定在操控侧板上,并连接各种通气管和气阀,即构成整副气瓶框架。
23.本发明的有益效果是整副框架的主体由镁合金材料通过铆接构成,有效的实现了轻量化,固定瓶托的载重梁中间设计有加强肋,有效地提高了强度;采用铆钉将各横梁、纵梁、支撑梁铆接,避免了焊接变形;结合镁合金本身具有高的抗阻尼性,能缓冲汽车在行驶中给气瓶框架带来的振动,整体上在减轻了气瓶框架重量的基础上加强了强度,大大提高了气瓶框架的整体性能。
附图说明
24.图1为本发明轻量化镁合金气瓶框架的整体斜视结构示意图。
25.图2为本发明中采用的三种套接筒的结构示意图。
26.图3为本发明中采用的瓶托的结构示意图。
27.图4为本发明中采用的直角片、第一铆接块和第二铆接块的结构示意图。
28.图中:1.横梁、2.纵梁、3.支撑梁、4.载重梁、5.短纵梁、6.第一套接筒、7.第二套接筒、8.第三套接筒、9.瓶托、10.直角片、11.第一铆接块、12.第二铆接块、13.操控侧板、14.方形孔筒、15.矩形孔筒、16.框型板、17.铆接孔、18.第一腰型孔、91.底板、92.托板、93.内撑板、94.外撑板、95.固位板、96.第二腰型孔、21.右纵梁、22.左纵梁、19.右框架体、20.左框架体。
具体实施方式
29.下面结合实施例对本发明作进一步说明,以下实施例旨在说明本发明而不是对本发明的进一步限定,不应以此限制本发明的保护范围。
30.如图所示,制作一种轻量化镁合金气瓶框架,首先用镁合金材料制作横梁1、纵梁2、支撑梁3、载重梁4和短纵梁5。
31.将所述横梁1、纵梁2、支撑梁3和短纵梁5做成为方形管,一般壁厚4
±
0.4mm,采用镁合金挤压成型后通过机加和微弧氧化制作而成。
32.将所述载重梁4做成为矩形管,一般壁厚4mm
±
0.4,中间设计有加强肋,加强肋厚3mm
±
0.4,采用镁合金挤压成型后通过机加和微弧氧化制作而成。
33.再用镁合金材料制作第一套接筒6、第二套接筒7、第三套接筒8和瓶托9,通过采用镁合金压铸、机加和微弧氧化制作而成。
34.所述第一套接筒6包括方形孔筒14、矩形孔筒15和框型板16,所述矩形孔筒15和方形孔筒14上面钻设有铆接孔17,所述框型板16上钻设有第一腰型孔18,所述第一腰型孔18用于将框架固定在车辆上,所述方形孔筒14垂直设置在矩形孔筒15的正侧面中部,所述框型板16垂直设置在矩形孔筒15的背侧面中部,构成第一套接筒6。
35.所述第二套接筒7包括方形孔筒14、矩形孔筒15和框型板16,所述矩形孔筒15和方形孔筒14上面钻设有铆接孔17,所述框型板16上钻设有第一腰型孔18,所述矩形孔筒15垂直设置在方形孔筒14的正侧面,所述框型板16垂直设置在方形孔筒14的背侧面的右边部,构成第二套接筒7。
36.所述第三套接筒8包括方形孔筒14、矩形孔筒15和框型板16,所述矩形孔筒15和方形孔筒14上面钻设有铆接孔17,所述框型板16上钻设有第一腰型孔18,所述矩形孔筒15垂直设置在方形孔筒14的正侧面,所述框型板16垂直设置在方形孔筒14的背侧面的左边部,
构成第三套接筒8。
37.所述瓶托9由底板91、托板92、内撑板93、外撑板94和固位板95一体生成固定连接,其中托板92为弧形板,其余均为直条板,所述固位板上钻设有第二腰型孔96,所述第二腰型孔96用于固定氢气瓶,所述底板91上钻设有铆接孔17;所述底板91的两端各连接一个外撑板94,底板91的中部连接若干个内撑板93,内撑板93的顶部连接托板92,托板92的两端各连接一个固位板95,两个固位板95各连接底板91两端的外撑板94,构成瓶托9。
38.所述操控侧板13为长方形板体,其长度等于纵梁2的长度,其宽度等于支撑梁3的长度。一般采用3
±
0.4mm厚的铝合金板材通过水切割工艺制作而成,上面有铆接孔17,以及用于安装各种传感器、气阀的安装孔。
39.再用不锈钢板制作第一铆接块11和第二铆接块12,用不锈角钢制作直角片10;所述第一铆接块11和第二铆接块12一般采用4
±
0.4mm厚不锈钢板通过水切割工艺制作而成;另外配备若干铆钉。
40.然后制作整副气瓶框架,如下步骤进行:
41.⑴
取两根横梁1和两根纵梁2相间首尾连接成长方形,并在连接处用直角片10和铆钉铆接固定,构成上框架;
42.⑵
取一根横梁1和两根纵梁2相间连接成缺一根横梁1框边的长方形,并在连接处用直角片10和铆钉铆接固定,构成缺边下框架;其中一根纵梁为右纵梁21,另一根纵梁为左纵梁22。
43.⑶
取两根载重梁4、一根短纵梁5和两只第一套接筒6,将两只第一套接筒6的矩形孔筒15分别套插在两根载重梁4的中部,再将短纵梁5的两端分别插入在两只第一套接筒6的方形孔筒14中,然后用铆钉铆接固定,构成工型架。
44.⑷
取八只瓶托9,将八只瓶托的底板91分别用铆钉铆接固定在工型架中载重梁4的上表面上,且短纵梁5的两侧的载重梁4上各安装两只,且两根载重梁4上的瓶托9两两对齐,构成工型托架。
45.⑸
取两只第二套接筒7和两只第三套接筒8,依次将第二套接筒7和第三套接筒8中的矩形孔筒15插在工型托架的载重梁4的两端,然后将第(2)步形成的缺边下框架从缺边方向插入第二套接筒7和第三套接筒8的方形孔筒14,调整工型托架到缺边下框架的中间位置,然后用铆钉铆接固定,构成下框托架。
46.⑹
取四根支撑梁3,将上框架的四个转角和下框托架的两个转角及两个边端一一对齐并用支撑梁3连接,并在连接处的纵梁2与支撑梁3的外侧边用第一铆接块11和铆钉铆接固定,将连接处的横梁1与支撑梁3的外侧边用第二铆接块12和铆钉铆接固定;构成右框架体19。
47.⑺
在铆接固定纵梁2和支撑梁3后,将操控侧板13与纵梁2和支撑梁3所构成的侧边框并接,然后用铆钉铆接固定,构成左框架体20。
48.⑻
喷涂防腐漆,待漆液干后,即做成本发明轻量化镁合金气瓶框架。
49.经测量,本发明轻量化镁合金气瓶框架的整体重量为70kg,比现有的铝合金气瓶框架的整体重量98kg降低了30%,有效地实现了新能源汽车的轻量化。