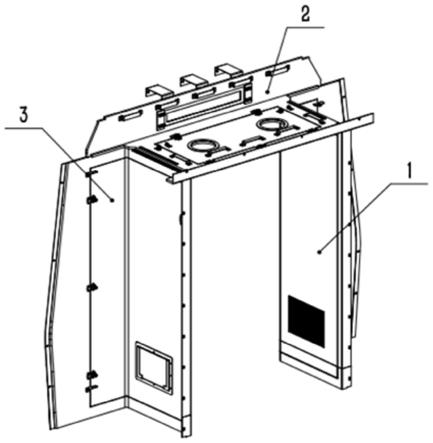
1.本发明属于轨道交通车辆设计,尤其涉及一种轨道交通车辆端墙。
背景技术:
2.随着国内外轨道交通领域的高速发展,轨道交通轻量化受到了越来越高的重视。轨道交通轻量化对于车辆减重、提速、降噪、降低能耗、提高乘坐舒适性等方面都具有特别重要的现实意义。在此背景下,在保证车辆整体强度的前提下,车辆内饰部件成为车辆轻量化的重点区域。轨道交通车辆中使用的端墙,不但要求产品美观,而且对产品的可靠性、轻量化、检修的便捷性要求越来越高。端墙是内装设计中较为复杂的一个部件,由左端墙、右端墙及上端墙组成,端墙左、右端墙及上端墙都应具有相应的检修门,用于电气部件及灯组件的检修和维护。
3.目前轨道交通车辆端墙主要采用玻璃钢夹芯、碳纤维夹芯和夹层结构铝蜂窝材料。玻璃钢夹芯一般采用玻璃纤维为蒙皮,中间辅以pet芯材,采用真空灌注的成型方式,其特点是成型工艺相对简单,造型能力强,但是尺寸稳定性相对较差,刚度低、易变形,重量较大,且防火已经达不到现在车辆的需求。碳纤维夹芯其工艺和玻璃钢夹芯相同,并且具有了高刚度、不易变形的特点,但其成本高昂,不适合大批量生产。铝蜂窝端墙具有较好的刚度、隔音、降噪方面的性能,但由于材料特性,铝蜂窝板适合用于制作造型简单,无复杂曲面造型的构件,其制作过程中需用到大量的型材及铝骨架,重量较大,不满足轻量化的要求。上述材质的端墙存在同等结构强度下重量大,成本高、安全性能不够等缺点。
技术实现要素:
4.本发明所要解决的技术问题是,克服以上背景技术中提到的不足和缺陷,提供一种不仅具有高强、防火、环保、隔音隔热及美观等优点,而且可有效降低端墙重量及成本,使大电气部件的检修更加简单方便的轨道交通车辆端墙。
5.为解决上述技术问题,本发明提出的技术方案为:一种轨道交通车辆端墙,包括一体成型的左端墙、上端墙和右端墙的三墙本体,所述左端墙、右端墙、上端墙中的至少一个通过雕刻方式在三墙本体上分离开设出一检修门,所述检修门与其从三墙本体上分离后的剩下的门框活动连接。
6.进一步的,所述检修门通过隐藏式铰链与门框活动连接,所述隐藏式铰链通过螺钉紧固在所述门框中的预埋件上。
7.进一步的,所述门框包括一体连接的侧门框和顶门框,所述左端墙、右端墙均包括匹配装设于所述侧门框上的l型检修门,所述l型检修门的开合一侧与侧门框之间设有压紧锁一;所述上端墙设有匹配装设于顶门框上的顶部检修门,所述顶部检修门的开合一侧与顶门框之间设有避免顶部检修门掉落的拉绳装置和压紧锁二。
8.进一步的,所述拉绳装置包括挂座、挂扣和挂绳,所述顶部检修门和顶门框分别对应设有挂座,两个所述挂座上均有挂孔,所述挂绳的两端均设有挂扣,所述挂扣扣装于挂孔
中。
9.进一步的,所述l型检修门的铰链一侧与侧门框之间设有能够控制l型检修门的打开角度的限位装置,所述限位装置包括尼龙带,所述尼龙带的两端分别与侧门框和l型检修门连接。
10.进一步的,所述三墙本体的基体材料为一体成型制备得到,所述基体材料包括外包覆层和轻质泡沫芯层,所述外包覆层由预浸料相互连接或搭接而成,所述轻质泡沫芯层是纤维增强材料浸渍含发泡剂的酚醛树脂胶液后经固化制备得到。
11.进一步的,所述轻质泡沫芯层的侧壁上设有可经加热膨胀的发泡胶条,所述发泡胶条加热膨胀后充填所述外包覆层和轻质泡沫芯层之间的空隙;所述外包覆层与轻质泡沫芯层之间铺设胶膜层。
12.进一步的,所述预浸料的成分为浸渍酚醛树脂或环氧树脂的玻璃纤维或碳纤维;所述酚醛树脂或环氧树脂的含量在35%-45%,所述真空袋压工艺包括在恒压下加热固化;所述恒压为0.1mp,加热温度为120-130℃,加热时间为60-90分钟。
13.进一步的,所述酚醛树脂胶液中的酚醛树脂与发泡剂的质量比为9.5-12:1,所述发泡剂的壳体为热塑性丙烯酸聚合物,内核为烷烃类气体,所述发泡剂的初始发泡温度为110℃~120℃,最高发泡温度为150℃~170℃。
14.进一步的,制备所述轻质泡沫芯层的发泡预浸料中,酚醛树脂与纤维增强材料的质量比为3.2-5:1;所述轻质泡沫芯层是先后经过初步发泡、二次发泡后最终固化成型。
15.与现有技术相比,本发明的有益效果为:
16.1.左端墙、上端墙和右端墙采用外包覆层和轻质泡沫芯层一体成型,轻质泡沫芯层为纤维增强酚醛泡沫,纤维增强酚醛泡沫由一种由微球发泡和纤维增强与酚醛树脂有机结合而成,具有阻燃、轻质、环保、隔热与隔声等优点;
17.2.外包覆层和轻质泡沫芯层一体成型,根据设计的外观造型要求,在雕刻机上雕刻出需要的轮廓,使产品在成型后具有更精确的尺寸和更精致的外观;
18.3.轻质泡沫芯层的侧壁上设有发泡胶条,发泡胶条在加热过程中体积膨胀3~5倍,可确保产品成型后边缘饱满无空洞、气泡等表面缺陷;外包覆层与轻质泡沫芯层之间设有胶膜层,保证轻质泡沫芯层与外包覆层的有效粘接;
19.4.打开检修门时,拉绳装置可避免检修门直接掉落,不会撞伤检修人员,使用更安全;限位装置能够控制l型检修门的打开角度,防止开合过大,避免l型检修门和别的设备发生碰撞;
20.5.相对于传统分开制作的做法,而采用整体成型再雕刻分离的制作方法,能节省三套模具,大大降低了模具费用。并且复合材料都具有变形的缺点,分开制作再装配会导致门框和检修门的装配缝隙及平面度不美观等情况,而采用机床分离,因其为一体成型再加工,就可以保证缝隙一致,平面度一致的优点。
附图说明
21.为了更清楚地说明本发明实施例或现有技术中的技术方案,下面将对实施例或现有技术描述中所需要使用的附图作简单地介绍,显而易见地,下面描述中的附图是本发明的一些实施例,对于本领域普通技术人员来讲,在不付出创造性劳动的前提下,还可以根据
这些附图获得其他的附图。
22.图1是本发明的结构示意图;
23.图2为本发明左端墙的结构示意图;
24.图3为本发明上端墙的结构示意图;
25.图4为本发明右端墙的结构示意图;
26.图5为本发明压紧锁二的结构示意图;
27.图6为本发明限位装置的结构示意图;
28.图7为本发明拉绳装置的结构示意图;
29.图8是本发明压紧锁二的结构示意图;
30.图9是本发明压紧锁一的结构示意图;
31.图10是本发明隐藏式铰链的结构示意图。
32.附图中:1、左端墙;11、侧门框;111、外包覆层;112、轻质泡沫芯层;113、发泡胶条;114、胶膜层;12、l型检修门;13、隐藏式铰链;131、预埋件;132、螺钉;14、限位装置;141、尼龙带;15、压紧锁一;2、上端墙;21、顶门框;22、顶部检修门;23、拉绳装置;231、挂座;232、挂扣;233、挂绳;24、压紧锁二;3、右端墙。
具体实施方式
33.为了便于理解本发明,下文将结合说明书附图和较佳的实施例对本发明做更全面、细致地描述,但本发明的保护范围并不限于以下具体实施例。
34.除非另有定义,下文中所使用的所有专业术语与本领域技术人员通常理解含义相同。本文中所使用的专业术语只是为了描述具体实施例的目的,并不是旨在限制本发明的保护范围。
35.除非另有特别说明,本发明中用到的各种原材料、试剂、仪器和设备等均可通过市场购买得到或者可通过现有方法制备得到。
36.实施例:
37.如图1~图8所示,一种轨道交通车辆端墙,包括一体成型的左端墙1、上端墙2和右端墙3的三墙本体,左端墙1、右端墙3、上端墙2均通过雕刻方式在三墙本体上分离开设出一检修门,检修门与其从三墙本体上分离后的剩下的门框活动连接。检修门通过隐藏式铰链13与门框活动连接,如图10所示,隐藏式铰链13通过螺钉132紧固在门框中的预埋件131上。相比于传统的自行设计的几字形铰链更便宜,且配合机床制作的高精度的顶部检修门22和顶门框21,使得顶门框21和顶部检修门22的安装和调试更便捷,省时省力。
38.门框包括一体连接的侧门框11和顶门框21,左端墙1、右端墙3均包括匹配装设于侧门框11上的l型检修门12,l型检修门12的开合一侧与侧门框11之间设有压紧锁一15;上端墙2设有匹配装设于顶门框21上的顶部检修门22,顶部检修门22的开合一侧与顶门框21之间设有避免顶部检修门22掉落的拉绳装置23和压紧锁二24。打开顶部检修门22时,拉绳装置23可避免顶部检修门22直接掉落,不会撞伤检修人员,使用更安全。如图9所示,压紧锁一15为挂扣式压紧锁,能保证l型检修门12在锁闭后不会出现结构弹性位移而自动打开的情况。
39.拉绳装置23包括挂座231、挂扣232和挂绳233,顶部检修门22和顶门框21分别对应
设有挂座231,两个挂座231上均有挂孔,挂绳233的两端均设有挂扣,232挂扣232扣装于挂孔中。
40.l型检修门12的铰链一侧与侧门框11之间设有能够控制l型检修门12的打开角度的限位装置14,限位装置14包括尼龙带141,尼龙带141的两端分别与侧门框11和l型检修门12连接,且与隐藏式铰链13同侧。
41.三墙本体的基体材料为一体成型制备得到,基体材料包括外包覆层111和轻质泡沫芯层112,外包覆层111由预浸料相互连接或搭接而成,轻质泡沫芯层112是纤维增强材料浸渍含发泡剂的酚醛树脂胶液后经固化制备得到。
42.轻质泡沫芯层112的侧壁上设有可经加热膨胀的发泡胶条113,发泡胶条113加热膨胀后充填外包覆层111和轻质泡沫芯层112之间的空隙;外包覆层111与轻质泡沫芯层112之间铺设胶膜层114,保证轻质泡沫芯层112与外包覆层111的有效粘接。
43.一种轨道交通车辆端墙的制作方法,包括以下步骤:
44.s1:制作:左端墙1、上端墙2和右端墙3均采用外包覆层111和轻质泡沫芯层112一体成型,外包覆层111相互连接或搭接并由预浸料固化得到,外包覆层111中间包裹轻质泡沫芯层112;轻质泡沫芯层112的侧壁上设有可经加热膨胀的发泡胶条113,发泡胶条113加热膨胀后充填外包覆层111和轻质泡沫芯层112之间的空隙;外包覆层111与轻质泡沫芯层112之间铺设胶膜层114,保证轻质泡沫芯层112与外包覆层111的有效粘接。
45.预浸料的成分为玻璃纤维或碳纤维和酚醛树脂或环氧树脂,树脂含量在35%到45%之间的预浸料,克重可以为200克、300克、400克或其他克重。采用真空袋压工艺,使产品均匀受到0.1mp的压力,持续保压送入烘箱中加热固化,成型的最佳温度为120-130℃,且在该温度间的时间不超过90分钟,60-90分钟为最佳。温度控制可采用以下三种方式:
46.第一种温度控制方式:从60
°
到80
°
到100
°
到130
°
,每个区间升温半小时,保温半小时,共4个小时,阶梯式升温和保温有利于产品的完全固化,使产品成型后变形小,是最经济实惠且质量好的方法。
47.第二种温度控制方式:中温固化预浸料,为优先方式,温度为50-130℃温度低,对加热设备的要求低,对模具要求不严,内应力小,尺寸稳定。
48.第三种温度控制方式:高温固化预浸料,固化温度较高,温度在130℃以上,使得制品材料产生较大的内应力,影响尺寸精度控制,严重时会导致材料提前破坏。
49.轻质泡沫芯层112由酚醛树脂和纤维材料制备得到的预浸料压制而成,所述发泡材料的板材厚度为10mm-30mm,密度为≥75g/cm3。
50.s2:加工:对制作好的左端墙1、上端墙2和右端墙3进行打袋密封并抽真空,之后送入烘箱进行加热固化,最后冷却至常温再脱模;
51.s3:分离:左端墙1、上端墙2和右端墙3脱模后,进行雕刻,并在左端墙1和右端墙3上分别分离出侧门框11、l型检修门12,在上端墙2上分离出顶门框21和顶部检修门22;在分离后,采用结构胶对左端墙1、上端墙2和右端墙3表面的微小缺陷分别进行修补;
52.s4:上漆和组装:对侧门框11、l型检修门12、顶门框21和顶部检修门22分别进行试装配,保证其缝隙均匀,平面度合格;再对左端墙1、上端墙2和右端墙3表面分别进行油漆处理;对产品进行组装及附件的安装。
53.轻质泡沫芯层112由酚醛树脂和纤维材料制备得到的预浸料压制而成,发泡材料
的板材厚度为10~30mm,密度为≥75g/cm3。的制备方法,包括以下步骤:
54.(1)按配比,将酚醛树脂与发泡剂加入容器中,充分搅拌,搅拌速度为30-80r/min,搅拌时间为30-60min,制备出酚醛树脂胶液。
55.酚醛树脂由苯酚与甲醛在碱催化作用下发生加成缩聚反应得到,其固含量大于65%,ph值8.0~9.0;粘度在800~1500m pa.s/25℃,凝胶时间为98~110s@150℃,发泡剂壳体为热塑性丙烯酸聚合物,内核为烷烃类气体,在受一定温度后会发生膨胀,发泡剂微球的平均球直径为30~40um,初始发泡温度为110℃~120℃,最高发泡温度为150℃~170℃;
56.酚醛树脂胶液中的酚醛树脂与发泡剂的质量比为9.5-12:1。
57.(2)步骤(1)中得到酚醛树脂胶液导入浸胶槽内,将纤维增强材料浸入酚醛树脂胶液中进行浸胶,使用浸胶机控制纤维增强材料与离型膜走速为2m/min-4m/min,烘道长度为30~50m,挤胶棍之间的间距为0.15-0.3mm,烘道温度分段四段设置,分别为80-90℃,125-140℃,130-140℃,90℃-100℃;
58.纤维增强材料为玻璃纤维,面密度为50g/m2;酚醛树脂胶液与纤维增强材料的质量比为3.2-5:1;
59.(3)经过连续浸胶,烘烤初步发泡与固化,通过烘道80~140℃,多段温度加热;收卷裁片,制备出酚醛树脂发泡预浸料;
60.(4)预浸料出来厚度为1.5~3.5mm左右,面密度为220g/m2~280g/m2。手感松软,带黏性;
61.(5)将已制备的初步发泡预浸料按照每10mm板材3层数进行堆叠;
62.(6)调节平板压机至120℃~135℃,四周垫入10~30mm的垫块;
63.(7)将已堆叠好的预浸料至于平板压机中;
64.(8)合模压制,压制时间为20~30min,其中每隔2min,开模进行排气,该过程使预浸料第二次充分发泡,填满型腔厚度,并最终固化;
65.(9)开模,取板材,切割边缘毛边。
66.所述板材力学性能如表1:
67.表1实施例1板材力学性能
68.