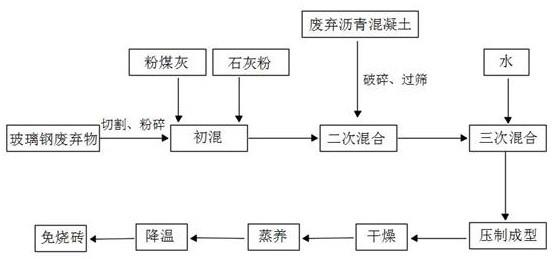
1.本发明涉及建筑垃圾资源综合利用及新型建材技术领域,特别涉及一种免烧砖及其制备方法。
背景技术:
2.我国近几十年来基础建设迅猛发展,在一些公路的高级路面中,沥青混凝 土路面所占的比例达到80%以上。按照我国路面规范设计要求,沥青路面的设计 使用寿命一般为10~15年。但由于路面交通量的急速增加,重载、超载现象严 重,致使多处沥青路面实际已处于超负荷工作状态,加之受到雨、雪和日晒等 环境因素的影响,导致其使用年限大幅降低,一般实际使用年限在10年以内。 达到使用年限的沥青道路需要进行翻修,该过程会产生大量的废弃沥青混合料, 若对其进行堆积或者填埋处理,将造成严重的环境污染和巨大的资源浪费。因 此,研究废弃沥青混凝土的综合利用及回收有重要意义。
3.玻璃钢即纤维增强复合塑料,它是以纤维及其制品为增强材料,合成树脂为基体材料的一种复合材料。大部分玻璃钢的增强纤维是玻璃纤维,此种玻璃钢称为玻璃纤维增强复合塑料;小部分玻璃钢的增强纤维是碳纤维和硼纤维,分别称为碳纤维增强复合塑料和硼纤维增强复合塑料。玻璃钢制品的使用寿命一般为15~20年左右,之后就变成了废弃物。由于其具有强度高、性质稳定、耐腐蚀性等特性,回收难度较大。传统的处理方法大都是填埋和焚烧,填埋处理占用大量土地,污染地下水;焚烧处置则会产生有害气体,既污染环境又危害人体健康,而且处理费用高,处理量有限,远不能满足玻璃钢废弃物数量剧增的要求。因此,废玻璃钢合理处置已成为当前我国玻璃钢工业一个亟待解决的问题。
4.中国专利文献cn107021709a(申请号:201710410557.6)公开了一种沥青再利用的透水路面砖及其制备方法,它是将废弃沥青混凝土粉碎后再另外加乳化沥青4~6份、62.5级硅酸盐水泥20~28份,经砌块成型机压实成型。其额外增加的乳化沥青和62.5级硅酸盐水泥价格较高,相对来说废弃物利用率低;而且砌块成型压力低,密实度较小,容易松散,抗压强度小。因此,需要对废弃沥青混凝土和再生玻璃钢纤维进行合理的利用。
技术实现要素:
5.为了解决上述背景技术中提出的问题,本发明提供一种免烧砖及其制备方法。
6.本发明提供的一种免烧砖及其制备方法,采用如下的技术方案:一种免烧砖,其由含以下质量份数的组分制备而成:废弃沥青混凝土30~45份,再生玻璃钢纤维10~15份,粉煤灰15~20份,石灰粉15~20份,所述免烧砖是以废弃沥青混凝土和再生玻璃钢纤维为主料,粉煤灰和石灰粉为辅料,加15~20份水搅拌混合,经预定压力压制成型后,于预设温度和预设压力的水蒸气中蒸养预设时间后制得。
7.优选的,所述废弃沥青混凝土35~40份,再生玻璃钢纤维12~13份,粉煤灰17~18份,石灰粉17~18份,水15~20份。
8.优选的,所述废弃沥青混凝土37份,再生玻璃钢纤维13份,粉煤灰17份,石灰粉17
份,水16份。
9.优选的,所述预定压力为20n/mm2,所述预设温度为170~180℃,所述预设压力为0.8~1.0mpa,所述预设时间为4~6h。
10.一种所述的免烧砖的制备方法,包括以下步骤:(1)将废弃沥青混凝土进行破碎,破坏骨料间沥青的胶结,形成骨料外包裹沥青的颗粒,并过筛以筛选出符合预定粒径的颗粒;(2)将玻璃钢板状废弃物切割成块粒,然后将块粒的玻璃钢废弃物经由粉碎设备进行粉碎,得到玻璃钢再生粉和玻璃钢再生纤维;(3)按照配比将步骤(1)处理后的符合预定粒径的废弃沥青混凝土、步骤(2)处理后的玻璃钢再生纤维、粉煤灰和石灰粉加水搅拌进行物料混合以得到混合料;(4)称取步骤(3)制得的混合料并输送至压制模具内,在预定压力作用下进行压制成型,压制预定时间后,制成砖坯;(5)将步骤(4)制得的砖坯放置设定时间后进行干燥,然后于预设温度和预设压力的水蒸气中蒸养预设时间,自然降温后得到免烧砖。
11.通过采用上述技术方案,废弃沥青混凝土在高温蒸养时,沥青处于熔化状态,在随后的降温冷却时,将与之接触的再生玻璃钢纤维粘结成“毛球体”,而粉煤灰与石灰粉在高温蒸养时形成水化硅酸钙固体,“毛球体”与“毛球体”之间又有玻璃钢纤维与水化硅酸钙紧密连接,使制得的免烧砖结构更加致密,平均抗压强度、抗折强度均有进一步提高;废弃沥青混凝土的加入,使制备的免烧砖抗折强度增幅大于抗压强度,其折压比较普通砖有明显提高。
12.优选的,所述步骤(1)中过筛后得到的废弃沥青混凝土的粒径在3~5mm之间。
13.优选的,所述步骤(2)中的玻璃钢再生粉呈柳絮状的蓬松团聚状态,含有大量合成树脂粉尘;所述玻璃钢再生纤维呈棉花状的蓬松团聚状态,长度在3mm~15mm之间。
14.优选的,所述步骤(3)中的物料混合包括两个过程,首先是所述步骤(2)制备的玻璃钢再生粉、玻璃钢再生纤维与粉煤灰和石灰粉在未加水前进行混合,该混合过程为初混,初混混合时间为3~5min;随后加入步骤(1)制备的沥青混凝土颗粒进行二次混合,二次混合的混合时间为1~2min;后续再加入水进行三次混合,加入的水包括自来水。
15.优选的,所述步骤(4)中压制成型使用的是压砖机,预定压力为20n/mm2,压制时间为15~25s。
16.优选的,所述步骤(5)中的设定时间为2~4h,预设温度为170~180℃,预设压力为0.8~1.0mpa,预设时间为4~6h。
17.综上所述,本发明具有如下的有益技术效果:1、本发明结合我国废弃沥青混凝土量大、玻璃钢废弃率高、利用率低的实际情况,充分利用废弃沥青混凝土、再生玻璃钢纤维的结构和化学特性,以达到这两种废弃物最大利用量和节约成本的目的,通过长期研究试验,在这两种废弃物的基础上再掺加粉煤灰、石灰粉和水,提高了砖坯的平均抗压强度和抗折强度,同时折压比也有了明显提高。
18.2、本发明生产出的以废弃沥青混凝土和再生玻璃钢纤维为主料的免烧砖,对废弃沥青混凝土、玻璃钢等废弃物进行了综合利用,其环境效益突出,成本低,经济效益明显,完全可以实现工业化生产,同时达到以废治废的创新。
19.3、本发明采用废弃沥青混凝土和再生玻璃钢纤维为主要原料,代替传统方案中大量掺水泥或粉煤灰,可以明显降低生产成本。
附图说明
20.图1是本发明一种免烧砖及其制备方法的工艺流程图。
具体实施方式
21.以下结合附图对本发明作进一步详细说明。
22.原料说明:本发明中使用的废弃沥青混凝土由市政道路路面刨铣后所得;玻璃钢废弃物由废旧品回收站回收的;粉煤灰由燃煤电厂废气中收集的;石灰粉由石灰块研磨制得。
23.本发明实施例公开一种免烧砖及其制备方法。
24.实施例1首先将废弃沥青混凝土进行破碎,破坏骨料间沥青的胶结,形成骨料外包裹沥青的单粒结构,然后过筛,过筛后得到的废弃沥青混凝土的粒径在3~5mm之间;将玻璃钢板状废弃物切割成小块,然后将小块的玻璃钢废弃物经由粉碎设备进行粉碎,得到玻璃钢再生粉和玻璃钢再生纤维,玻璃钢再生粉呈柳絮状的蓬松团聚状态,含有大量合成树脂粉尘,玻璃钢再生纤维呈棉花状的蓬松团聚状态,长度在3mm~15mm之间;按照配比分别称取过筛后的废弃沥青混凝土37份、再生玻璃钢纤维13份、粉煤灰17份和石灰粉17份,然后再生玻璃钢纤维、粉煤灰和石灰粉混合,混合4min,随后加入废弃沥青混凝土进行二次混合,混合时间为2min,之后加自来水16份并搅拌,进行物料混合,混合均匀后得到混合料;将混合料输送至压制模具内,在压砖机20n/mm2的压力作用下进行压制成型,压制时间为20s,制成砖坯;砖坯放置3h后进行干燥,然后于温度170℃、压力1.0mpa的水蒸气中蒸养5h,自然降温后得到免烧砖。
25.将所制得的免烧砖进行性能测试,本实施例制得的免烧砖的平均抗压强度为17.2mpa,平均抗折强度为4.9mpa。
26.实施例2首先将废弃沥青混凝土进行破碎,破坏骨料间沥青的胶结,形成骨料外包裹沥青的单粒结构,然后过筛,过筛后得到的废弃沥青混凝土的粒径在3~5mm之间;将玻璃钢板状废弃物切割成小块,然后将小块的玻璃钢废弃物经由粉碎设备进行粉碎,得到玻璃钢再生粉和玻璃钢再生纤维,玻璃钢再生粉呈柳絮状的蓬松团聚状态,含有大量合成树脂粉尘,玻璃钢再生纤维呈棉花状的蓬松团聚状态,长度在3mm~15mm之间;按照配比分别称取过筛后的废弃沥青混凝土30份、再生玻璃钢纤维15份、粉煤灰15份和石灰粉20份,然后再生玻璃钢纤维、粉煤灰和石灰粉混合,混合3min,随后加入废弃沥青混凝土进行二次混合,混合时间为2min,之后加自来水20份并搅拌,进行物料混合,混合均匀后得到混合料;将混合料输送至压制模具内,在压砖机20n/mm2的压力作用下进行压制成型,压制时间为20s,制成砖坯;砖坯放置2h后进行干燥,然后于温度170℃、压力0.8mpa的水蒸气中蒸养5h,自然降温后得到免烧砖。
27.将所制得的免烧砖进行性能测试,本实施例制得的免烧砖的平均抗压强度为
13.5mpa,平均抗折强度为3.7mpa。
28.实施例3首先将废弃沥青混凝土进行破碎,破坏骨料间沥青的胶结,形成骨料外包裹沥青的单粒结构,然后过筛,过筛后得到的废弃沥青混凝土的粒径在3~5mm之间;将玻璃钢板状废弃物切割成小块,然后将小块的玻璃钢废弃物经由粉碎设备进行粉碎,得到玻璃钢再生粉和玻璃钢再生纤维,玻璃钢再生粉呈柳絮状的蓬松团聚状态,含有大量合成树脂粉尘,玻璃钢再生纤维呈棉花状的蓬松团聚状态,长度在3mm~15mm之间;按照配比分别称取过筛后的废弃沥青混凝土45份、再生玻璃钢纤维10份、粉煤灰20份和石灰粉15份,然后再生玻璃钢纤维、粉煤灰和石灰粉混合,混合5min,随后加入废弃沥青混凝土进行二次混合,混合时间为1min,之后加自来水10份并搅拌,进行物料混合,混合均匀后得到混合料;将混合料输送至压制模具内,在压砖机20n/mm2的压力作用下进行压制成型,压制时间为15s,制成砖坯;砖坯放置4h后进行干燥,然后于温度180℃、压力1.0mpa的水蒸气中蒸养6h,自然降温后得到免烧砖。
29.将所制得的免烧砖进行性能测试,本实施例制得的免烧砖的平均抗压强度为17.0mpa,平均抗折强度为4.2mpa。
30.实施例4首先将废弃沥青混凝土进行破碎,破坏骨料间沥青的胶结,形成骨料外包裹沥青的单粒结构,然后过筛,过筛后得到的废弃沥青混凝土的粒径在3~5mm之间;将玻璃钢板状废弃物切割成小块,然后将小块的玻璃钢废弃物经由粉碎设备进行粉碎,得到玻璃钢再生粉和玻璃钢再生纤维,玻璃钢再生粉呈柳絮状的蓬松团聚状态,含有大量合成树脂粉尘,玻璃钢再生纤维呈棉花状的蓬松团聚状态,长度在3mm~15mm之间;按照配比分别称取过筛后的废弃沥青混凝土35份、再生玻璃钢纤维12份、粉煤灰17份和石灰粉17份,然后再生玻璃钢纤维、粉煤灰和石灰粉混合,混合4min,随后加入废弃沥青混凝土进行二次混合,混合时间为2min,之后加自来水19份并搅拌,进行物料混合,混合均匀后得到混合料;将混合料输送至压制模具内,在压砖机20n/mm2的压力作用下进行压制成型,压制时间为25s,制成砖坯;砖坯放置3h后进行干燥,然后于温度180℃、压力0.8mpa的水蒸气中蒸养4h,自然降温后得到免烧砖。
31.将所制得的免烧砖进行性能测试,本实施例制得的免烧砖的平均抗压强度为14.2mpa,平均抗折强度为3.8mpa。
32.实施例5首先将废弃沥青混凝土进行破碎,破坏骨料间沥青的胶结,形成骨料外包裹沥青的单粒结构,然后过筛,过筛后得到的废弃沥青混凝土的粒径在3~5mm之间;将玻璃钢板状废弃物切割成小块,然后将小块的玻璃钢废弃物经由粉碎设备进行粉碎,得到玻璃钢再生粉和玻璃钢再生纤维,玻璃钢再生粉呈柳絮状的蓬松团聚状态,含有大量合成树脂粉尘,玻璃钢再生纤维呈棉花状的蓬松团聚状态,长度在3mm~15mm之间;按照配比分别称取过筛后的废弃沥青混凝土40份、再生玻璃钢纤维13份、粉煤灰18份和石灰粉18份,然后再生玻璃钢纤维、粉煤灰和石灰粉混合,混合4min,随后加入废弃沥青混凝土进行二次混合,混合时间为2min,之后加自来水11份并搅拌,进行物料混合,混合均匀后得到混合料;将混合料输送至压制模具内,在压砖机20n/mm2的压力作用下进行压制成型,压制时间为20s,制成砖坯;
砖坯放置3h后进行干燥,然后于温度170℃、压力1.0mpa的水蒸气中蒸养5h,自然降温后得到免烧砖。
33.将所制得的免烧砖进行性能测试,本实施例制得的免烧砖的平均抗压强度为15.2mpa,平均抗折强度为4.1mpa。
34.由实施例1-5的性能测试结果可知,本发明制备的免烧砖的平均抗压强度和抗折强度有了明显提高。本发明中废弃沥青混凝土在高温蒸养时,沥青处于熔化状态,在随后的降温冷却时,将与之接触的再生玻璃钢纤维粘结成“毛球体”,而粉煤灰与石灰粉在高温蒸养时形成水化硅酸钙固体,“毛球体”与“毛球体”之间又有玻璃钢纤维与水化硅酸钙紧密连接,使制得的免烧砖结构更加致密,平均抗压强度、抗折强度均有进一步提高;废弃沥青混凝土的加入,使制备的免烧砖抗折强度增幅大于抗压强度,其折压比较普通砖有明显提高。且能够缓解废弃沥青混凝土、玻璃钢堆存处理带来的环境污染问题,实现废弃沥青混凝土和玻璃钢的资源化,大大减少能源的消耗。所制备的免烧砖既满足其使用性能,同时完全达到了国家标准的要求,在更大意义上实现这两种废弃物“变废为宝”的资源再循环利用。
35.以上均为本发明的较佳实施例,并非依此限制本发明的保护范围,故:凡依本发明的结构、形状、原理所做的等效变化,均应涵盖于本发明的保护范围之内。