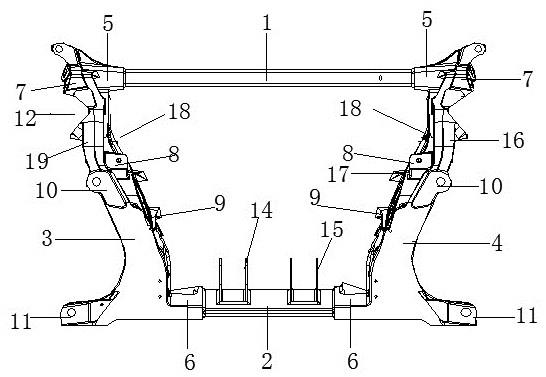
一种非对称上、下横梁的铸造式后副车架
1.本发明属于汽车零部件技术领域,尤其涉及一种非对称上、下横梁的铸造式后副车架。
背景技术:
2.汽车的后副车架是汽车底盘系统中非常重要的构件,后副车架连接车身和悬架等零部件,可减少路面的振动及噪声等激励向车身传递,同时后副车架还可以提高悬架的刚度,以使得整车具有较好的耐久和舒适性,现有技术中。
技术实现要素:
3.本发明所要解决的技术问题是:针对现有技术中,汽车后副车架的性能和轻量化要求无法得到很好包括的问题,提供一种非对称上、下横梁的铸造式后副车架会在后车架方面将保留后副车架的重量和截面特征复杂性,但是于满足轻量化要求,控制生产成本的升高和生产效率的降低,方案对后副车架的结构模态以及刚度、nvh等性能的都有提升;经过检测本后副车架刚度提升50%左右,结构模态提升约10~18%。
4.为解决上述技术问题提供一种非对称上、下横梁的铸造式后副车架,包括前横梁、后横梁、左纵梁、右纵梁整体组合为梯形;所述左纵梁、右纵梁的头端朝内横轴线设置对接筒,对接筒之间横向连接设置前横梁,所述左纵梁、右纵梁的尾端端朝内横轴线设置下对接筒,下对接筒之间横向连接设置后横梁 ,所述左纵梁、右纵梁对称结构,对接筒的外侧设置套衬羊角,套衬羊角下方设置折口角,从折口角处延铸造伸纵梁正体,折口角正下方设置中架连接头,中架连接头内部角交内侧设置转接头组,转接头组在伸纵梁正体下方还设置分支转接头,所述转接头组连接所述前横梁的左端下部以及所述左纵梁的前端下部;所述右前支撑支架连接所述前横梁的右端下部以及所述右纵梁的前端下部;所述分支转接头连接所述后横梁的左端下部以及所述左纵梁的后端下部,所述右下摆臂支架连接所述后横梁的右端下部以及所述右纵梁的后端下部;所述左连接支架连接在所述转接头组与所述分支转接头之间;所述右连接支架连接在所述右前支撑支架与所述右下摆臂支架之间。
5.作为优选,所述转接头组包括左前支撑和连接所述左前支撑的左前支撑后板,所述左连接支架的前端和所述前横梁的左端均连接所述左前支撑,所述左连接支架的前端、所述前横梁的左端和所述左纵梁的前端均连接所述左前支撑后板;所述右前支撑支架包括右前支撑和连接所述右前支撑的右前支撑后板,所述右连接支架19的前端连接所述右前支撑和所述右前支撑后板,所述右连接支架的前端和所述前横梁的右端均连接所述右前支撑,所述右连接支架的前端、所述前横梁的右端和所述右纵梁的前端均连接所述右前支撑后板。
6.作为优选,所述分支转接头包括左下摆臂和连接所述左下摆臂的左下摆臂后板,所述左连接支架的后端和所述后横梁的左端连接所述左下摆臂,所述左纵梁连接所述左下摆臂后板;
所述右下摆臂支架包括右下摆臂和连接所述右下摆臂的右下摆臂后板,所述右连接支架的后端和所述后横梁的右端连接所述右下摆臂,所述右纵梁连接所述右下摆臂后板。
7.作为优选,所述左下摆臂的前端设有用于连接所述左连接支架的后端的第一翻边,所述右下摆臂的前端设有用于连接所述左连接支架的后端的第二翻边。
8.作为优选,所述左连接支架的后端焊接在所述第一翻边上;所述右连接支架19的后端焊接在所述第二翻边上。
9.作为优选,所述前横梁、所述左纵梁和所述右纵梁均为管梁结构,所述后横梁为铸造成型件。
10.作为优选,所述前横梁、所述左纵梁和所述右纵梁的中部截面为圆形;所述左纵梁的后端、所述右纵梁的后端以及所述前横梁的左端和右端的截面呈扁平状。
11.作为优选,所述左纵梁的后端、所述右纵梁的后端以及所述前横梁的左端和右端均设有安装孔;所述左纵梁的后端、所述右纵梁的后端以及所述前横梁的左端和右端均通过穿过所述安装孔的衬套套管或衬套连接车身。
12.作为优选,所述左连接支架和所述右连接支架的截面为u形或v形状。
13.根据发明实施例的后副车架,左纵梁、右纵梁是对称结构,所以他们上面的转接头、右前支撑支架、分支转接头和右下摆臂支架之间能保证的连接稳固,以及最优化的结构模态;而前横梁、后横梁是非对称,将其改进后,同时,左连接支架连接在转接头与分支转接头之间;右连接支架19连接在右前支撑支架与右下摆臂支架之间。如此,本发明中的后副车架通过连接支架使得前支撑支架;包括转接头和右前支撑支架和下摆臂支架;包括分支转接头和右下摆臂支架构成两端支撑结构,如此,连接支架的y向跨距,显著提高了后副车架一阶扭转模态和一阶弯曲模态;结构模态提升约60hz以及前支撑支架和下摆臂支架的安装点的静态刚度和动刚度值;各种线束孔都被调整了,而且模流也进行了调整,铝铸件的下横梁和纵梁焊接位置被移动结合的更加紧固和内藏如内部腔体中,粗加工机余量被调整,经过检测本后副车架刚度提升50%左右,结构模态提升约10~18%,也进一步提升了电子机械机床制作性能;同时也显著提升了后副车架的支撑能力、强度和疲劳寿命,使得后副车架的平台化衍生能力变强,也可以在保证汽车的整车耐久性、舒适性、整车强度和刚度特性的要求的同时,减小了前支撑支架和下摆臂支架的厚度,实现轻量化目标,也降低了生产成本,提升了生产效率。同时,本发明结构简单,制作工艺简单,生产效率高,模具、开发费用投入较少,开发周期短可以满足汽车的整车耐久性、舒适性、整车强度和刚度特性的要求,改善了后副车架性能。
附图说明
14.图1是本发明的主视图;图2是本发明的爆炸组合图。
具体实施方式
15.为了使本发明所解决的技术问题、技术方案及有益效果更加清楚明白,以下结合附图及实施例,对本发明进行进一步的详细说明。应当理解,此处所描述的具体实施例仅仅
用以解释本发明,并不用于限定本发明。
16.需要理解的是,术语“上”、“下”、“前”、“后”、“左”、“右”、“中部”等指示的方位或位置关系为基于附图所示的方位或位置关系,仅是为了便于描述本发明和简化描述,而不是指示或暗示所指的装置或元件必须具有特定的方位、以特定的方位构造和操作,因此不能理解为对本发明的限制。
17.如图1和图2所示,图1是本发明一实施例提供的一种非对称上、下横梁的铸造式后副车架,包括前横梁1、后横梁2、左纵梁3、右纵梁4整体组合为梯形;所述左纵梁3、右纵梁4的头端朝内横轴线设置对接筒5,对接筒5之间横向连接设置前横梁1,所述左纵梁3、右纵梁4的尾端端朝内横轴线设置下对接筒6,下对接筒6之间横向连接设置后横梁2 ,所述左纵梁3、右纵梁4对称结构,对接筒5的外侧设置套衬羊角7,套衬羊角7下方设置折口角12,从折口角12处延铸造伸纵梁正体13,折口角12正下方设置中架连接头10,中架连接头10内部角交内侧设置转接头组8,转接头组8在伸纵梁正体13下方还设置分支转接头9,所述转接头组8连接所述前横梁的左端下部以及所述左纵梁的前端下部;所述右前支撑支架连接所述前横梁的右端下部以及所述右纵梁的前端下部;所述分支转接头连接所述后横梁的左端下部以及所述左纵梁的后端下部,所述右下摆臂支架连接所述后横梁的右端下部以及所述右纵梁的后端下部;所述左连接支架连接在所述转接头组8与所述分支转接头之间;所述右连接支架19连接在所述右前支撑支架与所述右下摆臂支架之间。
18.作为优选,所述转接头组8包括左前支撑和连接所述左前支撑的左前支撑后板,所述左连接支架的前端和所述前横梁的左端均连接所述左前支撑,所述左连接支架的前端、所述前横梁的左端和所述左纵梁的前端均连接所述左前支撑后板;所述右前支撑支架包括右前支撑和连接所述右前支撑的右前支撑后板,所述右连接支架19的前端连接所述右前支撑和所述右前支撑后板,所述右连接支架19的前端和所述前横梁的右端均连接所述右前支撑,所述右连接支架19的前端、所述前横梁的右端和所述右纵梁的前端均连接所述右前支撑后板。
19.作为优选,所述分支转接头包括左下摆臂和连接所述左下摆臂的左下摆臂后板,所述左连接支架的后端和所述后横梁的左端连接所述左下摆臂,所述左纵梁连接所述左下摆臂后板;所述右下摆臂支架包括右下摆臂和连接所述右下摆臂的右下摆臂后板,所述右连接支架19的后端和所述后横梁的右端连接所述右下摆臂,所述右纵梁连接所述右下摆臂后板。
20.作为优选,所述左下摆臂的前端设有用于连接所述左连接支架的后端的第一翻边,所述右下摆臂的前端设有用于连接所述左连接支架的后端的第二翻边。
21.作为优选,所述左连接支架的后端焊接在所述第一翻边上;所述右连接支架19的后端焊接在所述第二翻边上。
22.作为优选,所述前横梁、所述左纵梁和所述右纵梁均为管梁结构,所述后横梁为铸造成型件。
23.作为优选,所述前横梁、所述左纵梁和所述右纵梁的中部截面为圆形;所述左纵梁的后端、所述右纵梁的后端以及所述前横梁的左端和右端的截面呈扁平状。
24.作为优选,所述左纵梁的后端、所述右纵梁的后端以及所述前横梁的左端和右端均设有安装孔;所述左纵梁的后端、所述右纵梁的后端以及所述前横梁的左端和右端均通过穿过所述安装孔的衬套套管或衬套连接车身。
25.作为优选,所述左连接支架和所述右连接支架19的截面为u形或v形状。
26.以上所述仅为本发明的优选实施例而已,并不用于限制本发明,对于本领域的技术人员来说,本发明可以有各种更改和变化。凡在本发明的精神和原则之内,所作的任何修改、等同替换、改进等,均应包含在本发明的保护范围之内。