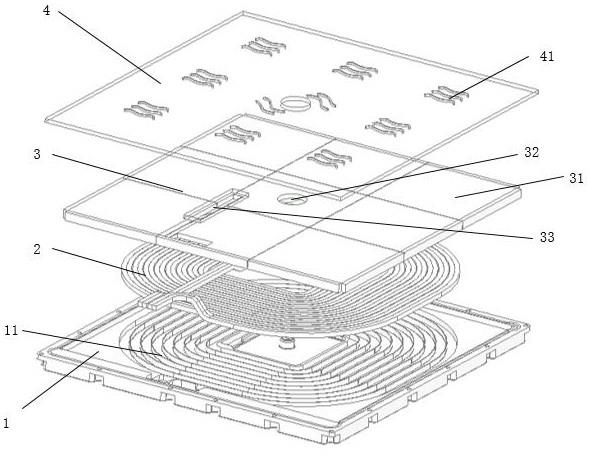
1.本实用新型属于电动汽车无线充电技术领域,特别是一种无线充电接收端结构。
背景技术:
2.随着我国近年来在电动汽车领域的高速发展,如何实现电动汽车的安全、便捷和快速的充电意义重大。电动汽车充电的传统方案是通过充电桩从电网直接获取电能,然而电动汽车进行有线充电时,充电插座或者电缆线通常有裸露在外的部分,在大功率充电时,容易产生电火花和电弧,存在重大安全隐患;同时传统的有线充电需要用户进行手动操作,人为的疏忽和充电插座的频繁插拔产生的硬件磨损均容易造成接触不良的现象,导致发生大功率环境下的人身安全事件。
3.为解决以上问题,通常采用近距离无线输电技术来实现电动汽车无线充电。电动汽车无线充电技术,通常是在电动汽车底盘安装一个接收端,并通过安装在地面或地下的发射端产生的磁场来产生感应电流,经整流成直流后向电动汽车电池充电,在结构方面,相较于常见车载充电机的全金属外壳,无线充电接收端底部需要使用塑料外壳来确保磁场能量传输,导致存在结构强度风险,此外,由于接收端磁芯数量多,体积大,在使用中热胀冷缩的现象较明显,车载充电机常用导热胶粘度低,应用在无线充电场景中会导致导热胶无法紧贴在磁芯上,散热能力不足,存在热风险。
4.因此,如何设计一种结构强度大的无线充电接收端结构是业界亟待解决的技术问题。
技术实现要素:
5.针对现有技术中,无线充电接收端的结构强度不高的问题,本实用新型提出了一种无线充电接收端结构。
6.本实用新型的技术方案为,提出了一种无线充电接收端结构,包括用于产生感应电流的线圈绕组、安装所述线圈绕组的底盘、与所述底盘配合共同封装所述线圈绕组的金属外壳、以及设于所述线圈绕组与所述金属外壳之间用于增强磁感应能力的平铺磁芯,所述平铺磁芯上开设有至少一个通孔,所述金属外壳与所述底盘通过所述通孔实现螺钉固定。
7.进一步,还包括设于所述金属外壳或所述底盘上的螺孔,当所述螺孔设于所述金属外壳上时,所述螺钉自底盘朝向所述金属外壳设置;
8.当所述螺孔设于所述底盘上时,所述螺钉自金属外壳朝向所述底盘设置。
9.进一步,所述平铺磁芯由多个相互贴合的块状磁芯相互拼接构成,所述块状磁芯的个数为奇数,所述通孔设于所述平铺磁芯中心的块状磁芯上。
10.进一步,所述平铺磁芯由多个相互贴合的块状磁芯相互拼接构成,所述块状磁芯的个数为偶数,所述通孔设于所述平铺磁芯中心四个块状磁芯的连接处。
11.进一步,所述通孔由四个角度为90度的扇形通孔拼接形成,所述平铺磁芯中心四
个块状磁芯的连接处均设有一个所述扇形通孔。
12.进一步,所述金属外壳朝向所述磁芯的一面设有至少一处条纹状凸起,所述条纹状凸起避开所述块状磁芯相互连接处设置。
13.进一步,还包括设于所述平铺磁芯与所述金属外壳之间的导热胶,所述导热胶分别连接所述平铺磁芯与金属外壳,并用于通过所述金属外壳向外部散热,所述导热胶采用带粘性的导热胶。
14.进一步,所述底盘上设有容纳所述线圈绕组放置的走线槽,所述走线槽的形状与所述线圈绕组相匹配,使每圈所述线圈绕组均置于所述走线槽内。
15.进一步,所述线圈绕组包括两条并行设置的利兹线,并通过所述利兹线绕制形成。
16.进一步,所述平铺磁芯上设有用于走线的缺口,无线充电接收端结构还包括设于所述平铺磁芯上用于覆盖所述缺口的盖板磁芯。
17.与现有技术相比,本实用新型至少具有如下有益效果:
18.1、通过在平铺磁芯上设置通孔,使金属外壳和底盘之间能够通过螺钉固定,增大了装置整体的结构强度。
19.2、通过在平铺磁芯与金属外壳之间设置带粘性的导热胶,同时在金属外壳朝向平铺磁芯的一面设置条纹状凸起,防止导热胶大面积脱落导致的散热能力不足的问题,提高了散热效果,避免了热风险的发生。
20.3、通过在平铺磁芯的缺口处设置一盖板磁芯,避免了由于缺口产生的漏磁,在一定程度上提高了能量传输效率。
附图说明
21.为了更清楚地说明本实用新型实施例中的技术方案,下面将对实施例或现有技术描述中所需要使用的附图作简单地介绍,显而易见地,下面描述中的附图仅仅是本实用新型的一些实施例,对于本领域普通技术人员来讲,在不付出创造性劳动性的前提下,还可以根据这些附图获得其他的附图。
22.图1为本实用新型无线充电接收端结构示意图。
23.图2为本实用新型一实施例的通孔设置示意图;
24.图3为本实用新型另一实施例的通孔设置示意图;
25.图4为本实用新型又一实施例的通孔设置示意图;
26.图5为本实用新型安装示意图。
27.其中,1为底盘、11为走线槽、2为线圈绕组、3为平铺磁芯、31为块状磁芯、32为通孔、33为盖板磁芯、4为金属外壳、41为条纹状凸起。
具体实施方式
28.为了使本实用新型所要解决的技术问题、技术方案及有益效果更加清楚明白,以下结合附图及实施例,对本实用新型进行进一步详细说明。应当理解,此处所描述的具体实施例仅仅用以解释本实用新型,并不用于限定本实用新型。
29.由此,本说明书中所指出的一个特征将用于说明本实用新型的一个实施方式的其中一个特征,而不是暗示本实用新型的每个实施方式必须具有所说明的特征。此外,应当注
意的是本说明书描述了许多特征。尽管某些特征可以组合在一起以示出可能的系统设计,但是这些特征也可用于其他的未明确说明的组合。由此,除非另有说明,所说明的组合并非旨在限制。
30.下面结合附图以及实施例对本实用新型的原理及结构进行详细说明。
31.电动汽车无线充电技术,通常是在电动汽车底盘安装一个接收端,并通过安装在地面或地下的发射端产生的磁场来产生感应电流,经整流成直流后向电动汽车电池充电,在结构方面,相较于常见车载充电机的全金属外壳,无线充电接收端底部需要使用塑料外壳来确保磁场能量传输,导致存在结构强度风险。本实用新型的思路在于,在中间的平铺磁芯处设置一个通孔,通过该通孔能够实现底盘和金属外壳之间的螺钉固定,从而增强结构强度。
32.具体的,请参见图1,本实用新型提出的无线充电接收端结构包括:底盘1、线圈绕组2、平铺磁芯3、金属外壳4。其中,底盘1设置在无线充电接收端结构的最底处,用于固定线圈绕组2和起到支撑作用,为确保磁场的能量传输,其一般采用塑料材料;线圈绕组2设置于底盘1上,并通过底盘1上的走线槽11起到固定作用,其由至少一根利兹线绕制而成,能够与磁场作用产生交变的电流,该交变的电流经过整流后可以提供给汽车的高压电池进行充电;平铺磁芯3设于线圈绕组2上方,并覆盖线圈绕组2,用于降低接收端与发射端之间的磁阻,能够让发射端产生的磁通更多的集中到与接收端的磁通耦合路径上,增大耦合系数,并提高传输能力;金属外壳4设于装置的最顶端,其与底盘1安装在一起,形成无线充电接收端的壳体,并将线圈绕组2和平铺磁芯3置于壳体内部,其一般采用金属材料,如铝制材料,由于发射端与接收端之间的距离一般较远,耦合路径较长,通常会产生较大的漏磁,通过金属金属外壳4的设置,能够吸收漏磁,避免其对接收端上方的工作电路产生影响。
33.进一步,在平铺磁芯3上设置有用于螺栓固定的通孔32,通过该通孔32能够实现金属外壳4与底盘1之间的螺钉固定。具体的,在金属外壳4上也设有通孔,在底盘1上设有用于螺钉插入的螺纹孔,在安装时,能够通过金属外壳4上的通孔穿过螺钉的杆部,并依次通过平铺磁芯3上的通孔32、线圈绕组2达到底盘1上的螺纹孔处,然后旋拧螺钉,使螺钉紧固,从而实现底盘1与金属外壳4的固定。需要说明的是,线圈绕组2中间一般不做缠绕,故不需要在线圈绕组上再做打孔设计。
34.在本实用新型其他实施例中,也可以在金属外壳4上设置相应的螺纹孔,在底盘1上设置通孔,让螺钉的杆部从底盘1从下自上穿过,并通过金属外壳4上的螺纹孔固定,其也能起到相同的效果。
35.具体的,请参见图5,其为本实用新型的安装示意图,通过螺钉穿过平铺磁芯3,能够实现金属外壳4与底盘1之间的良好固定,同时线圈绕组2和平铺磁芯3置于该装置的壳体内部,也提升了其稳定性,整体结构强度得到了提升。
36.进一步,请参见图2,其为本实用新型一实施例通孔的设置示意图,从图2中可以看出,平铺磁芯3由多个小的块状磁芯31相互拼接组成,该实施例下,平铺磁芯的数量为奇数(9个),此时平铺磁芯3的整体重心位于其正中央的一块块状磁芯31上,通孔32设置在该块状磁芯31的正中央,使得最终在进行螺钉固定时,能够保证螺钉安装于装置整体的重心处,整个装置四周的受力平衡,能够提高装置整体的稳定性。
37.优选的,请参见图4,其为本实用新型另一实施例通孔的设置示意图,其与图2中块
状磁芯31的数量相同,均为奇数,相比于图2中一个通孔32的设计,该实施例中设置了3个通孔32,相应的,在无线充电接收端结构在进行安装时,底盘1和金属外壳4上也要相应设置3个匹配的螺纹孔和通孔进行固定,其相较于一个通孔32的方案大大提高了装置的结构强度(设置有3个螺钉,装置强度明显提高)。同时,三个通孔32组成的形状中心与平铺磁芯3的重心重合,使其保证装置整体的稳定性。在本实用新型的基础上,还可以增设更多的通孔32以增强装置的结构强度,在保证多个通孔32以平铺磁芯3的重心中心对称的情况下,可以保证装置整体的稳定性。
38.进一步的,请参见图3,其为本实用新型另一实施例通孔的设置示意图,可以看出,相较于图2和图4中平铺磁芯3的设置,该实施例中块状磁芯31的个数为偶数(理论上为4的倍数,因为平铺磁芯3为正方形,其长宽设置的块状磁芯31个数相同,只有当长宽同时为偶数时平铺磁芯3中快状磁芯31的个数才为偶数,而偶数可以表达为2a的形式,由于正方形长宽相同,故平铺磁芯3中块状磁芯31的总个数为4a2,即其必然为4的倍数),此时平铺磁芯3的中心为其最中央的4个块状磁芯31的连接处,故相应的通孔32也设置在中间4个块状磁芯31的连接处。
39.进一步的,其设置方式为:在中间4个块状磁芯31的相互连接处分别给4个块状磁芯31进行开孔,每个块状磁芯31在其顶角处开设一个90度的扇形通孔,并将4个块状磁芯31的扇形通孔合并组成一个通孔,该通孔刚好可以组成一个圆形的通孔,使其供螺钉的杆部穿过。
40.需要说明的是,该设置方法只针对平铺磁芯3上的块状磁芯31的个数为偶数时,当其个数为奇数时,只用在最中间的一个块状磁芯31上开孔即可。
41.进一步的,请参见图2、图3和图4,在平铺磁芯3上设有用于走线的缺口,由于线圈绕组2产生的交变电流需要传输到接收端上方的电路中,其需要通过走线连接,故该缺口是不可避免的。但由于该缺口的设置,将会导致此处的磁芯不连贯,部分磁通会进入到空气中,产生漏磁,其会切割线圈并在金属外壳4上产生涡流,从而产生额外损耗。本实施例中,在平铺磁芯3的缺口处设置有盖磁芯33,通过盖板磁芯33将平铺磁芯3上的缺口盖住,并将位于缺口两侧的平铺磁芯3连通,通过盖板磁芯33的设置,能够将磁通维持在平铺磁芯3内部,从缺口处流过的磁通能够通过盖板磁芯33流入到缺口另一侧的平铺磁芯3中,从而避免了该磁通流入空气,进而减少漏磁的产生。
42.进一步,在金属外壳4与平铺磁芯3之间填充有导热胶,由于无线充电接收端在进行工作时会产生热量,如果热量过高容易烧坏器件,故在平铺磁芯3与金属外壳4之间填充有导热胶,由于金属外壳4为无线充电接收端壳体的一部分,其与外部相互连接,使得导热胶能够通过金属外壳4将热量散发出去,避免器件的损坏。
43.在无线充电接收端工作时,由于其热胀冷缩较为明显,容易造成导热胶连接不牢固,从而松开与平铺磁芯之间的连接,从而导致散热效果不佳,为解决上述问题,本实用新型中采用粘性强的导热胶,如聚氨酯胶等材料,能够增强平铺磁芯3与金属外壳4之间的粘结效果。
44.进一步的,请参见图1,在金属外壳4朝向平铺磁芯3的一面设置有条纹状凸起41(为便于观察,图1中金属外壳4中朝向平铺磁芯3的一面向上放置,实际中设有条纹状凸41起的一面应为朝向平铺磁芯3向下设置),其设置有至少一处,通过条纹状凸起41与导热胶
连接,能够进一步增强导热胶与金属外壳4之间的连接,同时,条纹状凸起41还能够增大金属外壳4与导热胶的接触面积,从而提高散热效果,在本实用新型一些其他实施例中,还可以将凸起的形状设计为方形等,只要能起到增大接触面积的效果即可。优选的,条纹状凸起41避开平铺磁芯31上块状磁芯31的相互连接处设置,以减少涡流损耗。
45.进一步,在底盘1上设有容纳线圈绕组2放置的走线槽11,其用于更好的安装线圈绕组2,以保证线圈绕组2的稳定性,走线槽11的形状与线圈绕组2的形状相匹配,线圈绕组2由至少一根利兹线绕制而成,整体呈涡流形,走线槽11的形状也呈涡流形,使得每一圈线圈绕组2均能置于走线槽11内,起到良好的固定效果,避免线圈绕组2发生偏移影响感应电流的产生。
46.进一步的,本实用新型中,线圈绕组2由两根并行设置的利兹线绕组而成,相较于一根利兹线的方案,在相同截面积的情况下,可以避免因为单根线线径过粗导致的加工,绕制的困难。
47.与现有技术相比,本实用新型通过在平铺磁芯3上设置通孔,提高了装置整体的结构强度,同时通过金属外壳4上设置的条纹状凸起41,增加了散热面积以及与导热胶的接触面积,避免了热风险问题的发生。同时,通过盖板磁芯33的设置,进一步降低了漏磁,提高了能量传输效率。
48.上述实施例仅用于说明本实用新型的具体实施方式。应当指出的是,对于本领域的普通技术人员来说,在不脱离本实用新型构思的前提下,还可以做出若干变形和变化,这些变形和变化都应属于本实用新型的保护范围。