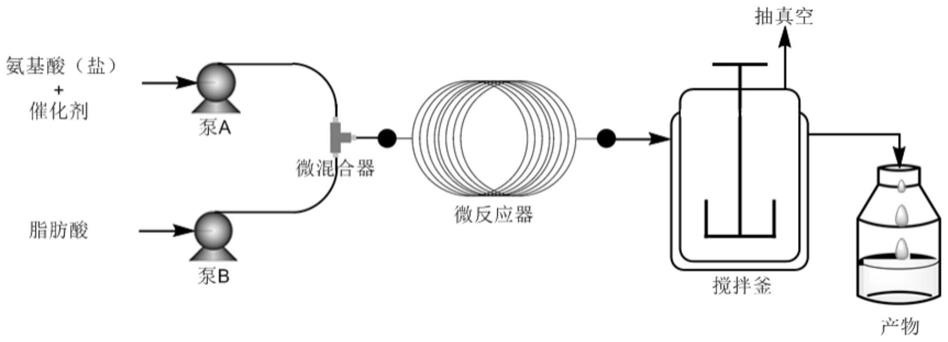
1.本发明属于化工合成领域,具体涉及脂肪酰基氨基酸型表面活性剂的一步缩合法连续化制备新方法。
背景技术:
2.脂肪酰基氨基酸型表面活性剂在分子中具有与酰胺基结合的磺酸基,与阴离子、非离子和两性表面活性剂有良好的配伍性。脂肪酰基氨基酸型表面活性剂是一种安全性较高的阴离子表面活性剂,具有优良的水溶性、耐硬水性、耐碱性和耐酸性、发泡性优良,使用后手感好,适应配制各类中高档洗发液、洗面奶和浴剂等化妆品。能够赋予毛发、皮肤温和、滋润和滑爽的感觉,也可用作毛纺和丝绸印染工业的精炼剂、净洗剂。
3.脂肪酰基氨基酸型表面活性剂的制备有间接法和直接法两种。间接法是采用肖顿-鲍曼缩合反应,由脂肪酰氯与氨基酸(盐)在碱性条件下制得产物,生成的盐残留在产物中难以除去,是目前工业生产中常用的方法。直接法是脂肪酸与氨基酸(盐)直接脱水缩合制得产物,但由于反应产率低、反应条件苛刻等原因难以工业化应用。
4.在脂肪酸与氨基酸(盐)直接法制备脂肪酰基氨基酸型表面活性剂过程中,脂肪酸与氨基酸(盐)首先络合生成粘稠状的中间体,再在高温下不断脱水生成产物。在釜式搅拌反应器中,由于反应体系的粘度增大,传质效果差,无法将反应原料脂肪酸和氨基酸(盐)进行充分混合,导致反应收率低、耗时长,并且副产物随着反应时间的增加而增加。
5.微通道反应器由于巨大的比表面积,具有传质传热效率高、反应过程容易控制(温度、时间、混合效率),以及易放大、安全性能佳等特点,在精细化工和药物中间体生产中得到越来越广泛的应用。由于微反应器持液量小、耐高温耐高压性能好,对于釜式工艺中条件苛刻的操作可带来本征安全性的提高。对于操作要求高的脂肪酸与氨基酸(盐)直接法制备脂肪酰基氨基酸型表面活性剂有良好的适用性。
技术实现要素:
6.本发明的目的是提供一种在微通道反应器中一步缩合法连续制备脂肪酰基氨基酸型表面活性剂的方法。
7.本发明的第一方面,提供了脂肪酰基氨基酸型表面活性剂一步缩合法的连续化制备方法,包括如下步骤:
8.(a)提供料液a和料液b,其中,所述的料液a为含有催化剂的氨基酸溶液(优选为氨基酸或其盐的水溶液),所述的料液b为脂肪酸;
9.(b)将所述的料液a和料液b泵入微混合器中混合,得到料液混合物;
10.(c)将所述的料液混合物通入微通道反应器中进行反应,得到反应液;其中,反应温度为160℃-300℃;
11.(d)将所述的反应液通入高温搅拌釜从而除去水分,得到所述的脂肪酰基氨基酸型表面活性剂。
12.在另一优选例中,所述的氨基酸(盐)水溶液的浓度为41%。
13.在另一优选例中,进料时,所述的料液b脂肪酸为熔融状态。
14.在另一优选例中,步骤(c)中,所述反应为脱水缩合反应。
15.在另一优选例中,步骤(d)还包括抽真空去除冷凝水。
16.在另一优选例中,所述微通道反应器中脱水缩合的反应温度为200℃-270℃,较佳为240℃-260℃。
17.在另一优选例中,所述氨基酸(盐):脂肪酸的摩尔比为1.0~5.0:1。
18.在另一优选例中,所述氨基酸(盐):脂肪酸的摩尔比为1~3:1,优选为1.5~2:1。
19.在另一优选例中,所述催化剂的用量为氨基酸(盐)的0.1-20wt%。
20.在另一优选例中,所述的催化剂的用量为氨基酸(盐)的1-5wt%。
21.在另一优选例中,所述催化剂选自下组:硼酸、磷酸、多聚磷酸、四氯化钛、四氯化锡,或其组合。
22.在另一优选例中,所述的催化剂为硼酸、磷酸,或其组合。
23.在另一优选例中,所述催化剂为脱水催化剂。
24.在另一优选例中,所述的氨基酸(盐)水溶液在微通道反应器中的流速为0.01-1000l/min;所述的脂肪酸在微通道反应器中的流速为0.01-1000l/min。
25.在另一优选例中,所述的氨基酸(盐)水溶液与所述的脂肪酸在微通道反应器中的流速相同。
26.在另一优选例中,所述的氨基酸(盐)水溶液与所述的脂肪酸在微通道反应器中的流速不相同。
27.在另一优选例中,所述氨基酸(盐)水溶液在微通道反应器中的流速为0.05-100l/min;所述脂肪酸在微通道反应器中的流速为0.05-100l/min。
28.在另一优选例中,所述氨基酸(盐)水溶液在微通道反应器中的流速为0.15-10l/min;所述脂肪酸在微通道反应器中的流速为0.15-10l/min。
29.在另一优选例中,所述氨基酸(盐)水溶液在微通道反应器中的流速为0.3-0.5l/min;所述脂肪酸在微通道反应器中的流速为0.2-0.4l/min。
30.在另一优选例中,所述微混合器的型号选自下组:y型、t型、j型、两步t型、内交指型、分离汇合型、sk型。
31.在另一优选例中,所述微混合器的型号选自下组:t型、内交指型、sk型。
32.在另一优选例中,所述微混合器的型号为t型。
33.在另一优选例中,所述脂肪酸为c
2-c
30
的直链或支链脂肪酸;较佳地,所述的脂肪酸选自下组:棕榈酸、硬脂酸、油酸、亚油酸、亚麻酸、椰油酸、月桂酸、花生四烯酸、二十碳五烯酸、二十二碳六烯酸,或其组合。
34.在另一优选例中,所述氨基酸(盐)选自下组:氨基磺酸、氨基磺酸钠、氨基磺酸钾、n-甲基牛磺酸、n-甲基牛磺酸钠、n-甲基牛磺酸钾、n-乙基牛磺酸、n-乙基牛磺酸钠、n-乙基牛磺酸钾,或其组合。
35.在另一优选例中,所述微通道反应器的内径尺寸为0.5~15mm,长度为0.5~500m。
36.在另一优选例中,所述的微通道反应器的内径尺寸为1~3mm,长度为10~20m。
37.在另一优选例中,所述搅拌釜的温度为160℃-300℃,较佳地为200℃-280℃,更佳
地为240-260℃。
38.应理解,在本发明范围内中,本发明的上述各技术特征和在下文(如实施例)中具体描述的各技术特征之间都可以互相组合,从而构成新的或优选的技术方案。限于篇幅,在此不再一一累述。
附图说明
39.图1:本发明反应工艺流程示意图。
具体实施方式
40.本发明经过广泛而深入地研究,经过大量筛选首次开发了一种新颖的微通道反应器连续制备脂肪酰基氨基酸型表面活性剂的方法。本发明的工艺流程简便,产品收率高,绿色安全,易于实现大规模工业化生产。在此基础上,完成了本发明。
41.本发明的具体实施方案如下:
42.首先通过使用微混合器,保证两种反应原料的充分接触和充分混合,使原料完全转化得到粘稠状的中间体,解决了釜式反应中物料难以混合均匀的问题。在柱塞泵的高压推动下将高粘反应体系推入微反应器,在高温下脱水形成产物。由于微反应器持液量小,能够耐高温高压,本征安全性能指数级提高,解决了釜式反应器中高压体系安全性差的问题。同时,在微反应器内停留时间短、无返混、易调控,避免了长时间反应副产物增多的问题。随着反应的进行,反应体系粘度降低,最后在搅拌釜中进一步脱水熟化,抽真空将反应体系内的水快速除去获得高质量的最终产品。综上,通过使用微混合器强化反应原料混合过程,在微反应器内强化反应过程,缩短反应时间,避免反应时间增长带来的副产物增加等问题,再通过搅拌釜熟化和真空脱水,快速高效的获得目标产品,可解决现有技术中存在的混合效果差,催化剂用量大,反应时间过长,副产物多和产率低等无法工业化放大的问题。
43.与现有技术相比,本发明的优势:
44.(1)本发明通过使用微混合器和微通道反应器来连续化制备脂肪酰基氨基酸型表面活性剂,反应时间短,反应通量大,成本低廉。
45.(2)本发明制备的产品不含无机盐或有机盐等杂质,对环境污染小,绿色环保。
46.(3)本发明所述的方法能够连续不间断生产且产品的质量稳定,易于实现大规模工业化生产,有效克服直接法制备脂肪酰基氨基酸型表面活性剂难以在传统反应釜中工业化生产的缺点。
47.(4)本发明的原料转化率提高,高达为92~99%,产率高达90~98%。
48.下面结合具体实施例,进一步阐述本发明。应理解,这些实施例仅用于说明本发明而不用于限制本发明的范围。下列实施例中未注明具体条件的实验方法,通常按照常规条件,或按照制造厂商所建议的条件。除非另外说明,否则百分比和份数按重量计算。
49.在实施例中,室温指25℃。
50.实施例中所用的原料和试剂均为市售产品。
51.实施例1
52.取5000ml 41%n-甲基牛磺酸钾水溶液,加入催化剂硼酸61.5g,溶解后作为料液a,椰油酸5000ml作为料液b。使用进料泵将料液a和料液b泵入t型微混合器,混合后直接流
入内径为2.0mm,长度为15m的微通道反应器中。料液a的进料流速为390ml/min,料液b的进料流速为300ml/min。微反应器内反应温度为245℃,高温搅拌釜温度为255℃。进料12min后停止,待高温搅拌釜内无水分蒸出,抽真空30min后结束,冷却得到产物4628g,产率为91%。
53.实施例2
54.取5000ml 41%n-甲基牛磺酸钠水溶液,加入催化剂硼酸61.5g,溶解后作为料液a,月桂酸5000g熔融后作为料液b。使用进料泵将料液a和料液b泵入t型微混合器,混合后直接流入内径为2.0mm,长度为15m的微通道反应器中。料液a的进料流速为390ml/min,料液b的进料流速为300ml/min。微反应器内反应温度为245℃,高温搅拌釜温度为255℃。进料12min后停止,待高温搅拌釜内无水分蒸出,抽真空30min后结束,冷却得到产物4718g,产率为97%。
55.实施例3
56.取5000ml 41%n-甲基牛磺酸钠水溶液,加入催化剂硼酸61.5g,溶解后作为料液a,硬脂酸5000g熔融后作为料液b。使用进料泵将料液a和料液b泵入t型微混合器,混合后直接流入内径为2.0mm,长度为15m的微通道反应器中。料液a的进料流速为390ml/min,料液b的进料流速为300ml/min。微反应器内反应温度为245℃,高温搅拌釜温度为255℃。进料12min后停止,待高温搅拌釜内无水分蒸出,抽真空30min后结束,冷却得到产物4317g,产率为95%。
57.实施例4
58.取5000ml 41%n-甲基牛磺酸钠水溶液,加入催化剂硼酸61.5g,溶解后作为料液a,油酸5000ml作为料液b。使用进料泵将料液a和料液b泵入t型微混合器,混合后直接流入内径为2.0mm,长度为15m的微通道反应器中。料液a的进料流速为390ml/min,料液b的进料流速为300ml/min。微反应器内反应温度为245℃,高温搅拌釜温度为255℃。进料12min后停止,待高温搅拌釜内无水分蒸出,抽真空30min后结束,冷却得到产物4730g,产率为98%。
59.实施例5
60.取5000ml 41%n-甲基牛磺酸钠水溶液,加入催化剂硼酸61.5g,溶解后作为料液a,亚麻酸5000ml作为料液b。使用进料泵将料液a和料液b泵入t型微混合器,混合后直接流入内径为2.0mm,长度为15m的微通道反应器中。料液a的进料流速为390ml/min,料液b的进料流速为300ml/min。微反应器内反应温度为245℃,高温搅拌釜温度为255℃。进料12min后停止,待高温搅拌釜内无水分蒸出,抽真空30min后结束,冷却得到产物4707g,产率为96%。
61.实施例6
62.取5000ml 41%n-甲基牛磺酸钾水溶液,加入催化剂硼酸61.5g,溶解后作为料液a,月桂酸5000g熔融后作为料液b。使用进料泵将料液a和料液b泵入t型微混合器,混合后直接流入内径为2.0mm,长度为15m的微通道反应器中。料液a的进料流速为390ml/min,料液b的进料流速为300ml/min。微反应器内反应温度为245℃,高温搅拌釜温度为255℃。进料12min后停止,待高温搅拌釜内无水分蒸出,抽真空30min后结束,冷却得到产物4820g,产率为99%。
63.实施例7
64.取5000ml 41%n-甲基牛磺酸钠水溶液,加入催化剂磷酸61.5g,溶解后作为料液a,椰油酸5000ml作为料液b。使用进料泵将料液a和料液b泵入t型微混合器,混合后直接流
入内径为2.0mm,长度为15m的微通道反应器中。料液a的进料流速为390ml/min,料液b的进料流速为300ml/min。微反应器内反应温度为245℃,高温搅拌釜温度为255℃。进料12min后停止,待高温搅拌釜内无水分蒸出,抽真空30min后结束,冷却得到产物4832g,产率为95%。
65.实施例8
66.取5000ml 41%n-甲基牛磺酸钠水溶液,加入催化剂多聚磷酸61.5g,溶解后作为料液a,椰油酸5000ml作为料液b。使用进料泵将料液a和料液b泵入t型微混合器,混合后直接流入内径为2.0mm,长度为15m的微通道反应器中。料液a的进料流速为390ml/min,料液b的进料流速为300ml/min。微反应器内反应温度为245℃,高温搅拌釜温度为255℃。进料12min后停止,待高温搅拌釜内无水分蒸出,抽真空30min后结束,冷却得到产物4881g,产率为96%。
67.实施例9
68.取5000ml 41%n-甲基牛磺酸钠水溶液,加入催化剂磷酸61.5g,溶解后作为料液a,椰油酸5000ml作为料液b。使用进料泵将料液a和料液b泵入t型微混合器,混合后直接流入内径为2.0mm,长度为15m的微通道反应器中。料液a的进料流速为390ml/min,料液b的进料流速为300ml/min。微反应器内反应温度为255℃,高温搅拌釜温度为265℃。进料12min后停止,待高温搅拌釜内无水分蒸出,抽真空30min后结束,冷却得到产物4933g,产率为97%。
69.实施例10
70.取5000ml 41%n-甲基牛磺酸钠水溶液,加入催化剂磷酸61.5g,溶解后作为料液a,椰油酸5000ml作为料液b。使用进料泵将料液a和料液b泵入内交指型微混合器,混合后直接流入内径为2.0mm,长度为15m的微通道反应器中。料液a的进料流速为390ml/min,料液b的进料流速为300ml/min。微反应器内反应温度为245℃,高温搅拌釜温度为255℃。进料12min后停止,待高温搅拌釜内无水分蒸出,抽真空30min后结束,冷却得到产物4882g,产率为96%。
71.实施例11
72.取5000ml 41%n-甲基牛磺酸钠水溶液,加入催化剂磷酸61.5g,溶解后作为料液a,椰油酸5000ml作为料液b。使用进料泵将料液a和料液b泵入sk型微混合器,混合后直接流入内径为2.0mm,长度为15m的微通道反应器中,料液a的进料流速为390ml/min,料液b的进料流速为300ml/min。微反应器内反应温度为245℃,高温搅拌釜温度为255℃。进料12min后停止,待高温搅拌釜内无水分蒸出,抽真空30min后结束,冷却得到产物4781g,产率为94%。
73.实施例12
74.取5000ml 41%n-甲基牛磺酸钠水溶液,加入催化剂磷酸61.5g,溶解后作为料液a,椰油酸5000ml作为料液b。使用进料泵将料液a和料液b泵入t型微混合器,混合后直接流入内径为2.0mm,长度为15m的微通道反应器中,料液a的进料流速为390ml/min,料液b的进料流速为300ml/min。微反应器内反应温度为245℃,高温搅拌釜温度为255℃。进料12min后停止,待高温搅拌釜内无水分蒸出,抽真空30min后结束,冷却得到产物4730g,产率为93%。
75.对比例1
76.称取41%n-甲基牛磺酸钠水溶液5000ml,加入催化剂磷酸61.5g,溶解后作为料液a,椰油酸5000ml作为料液b。使用进料泵将料液a和料液b泵入t型微混合器,混合后直接流入内径为2.0mm,长度为15m的微通道反应器中,料液a的进料流速为390ml/min,料液b的进
料流速为300ml/min。微反应器内反应温度为275℃,高温搅拌釜温度为265℃。进料12min后停止,待高温搅拌釜内无水分蒸出,抽真空30min后结束,冷却得到产物4170g,产率为82%。
77.对比例2
78.称取41%n-甲基牛磺酸钠水溶液5000ml,加入催化剂磷酸61.5g,溶解后作为料液a,椰油酸5000ml作为料液b。使用进料泵将料液a和料液b泵入t型微混合器,混合后直接流入内径为2.0mm,长度为15m的微通道反应器中,料液a的进料流速为390ml/min,料液b的进料流速为300ml/min。微反应器内反应温度为235℃,高温搅拌釜温度为265℃。进料12min后停止,待高温搅拌釜内无水分蒸出,抽真空30min后结束,冷却得到产物4374g,产率为86%。
79.本发明中,表面活性剂的制备工艺采用管式反应进行,因此需要取得足够高的产率,以及合适的反应速度。申请人发现,当反应温度降低时,反应难以进行导致收率大幅降低,而当反应温度过高情况下,产物容易炭化,产生副产物导致收率降低,因此,优选在240℃-260℃下进行反应。
80.在本发明提及的所有文献都在本技术中引用作为参考,就如同每一篇文献被单独引用作为参考那样。此外应理解,在阅读了本发明的上述讲授内容之后,本领域技术人员可以对本发明作各种改动或修改,这些等价形式同样落于本技术所附权利要求书所限定的范围。