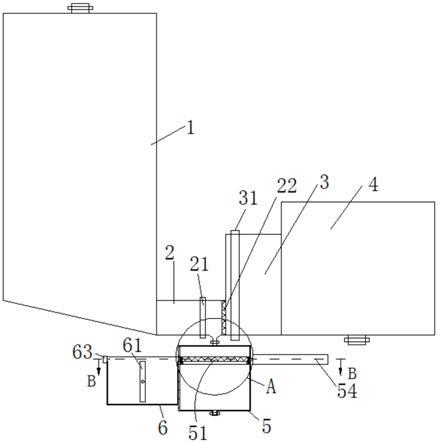
1.本发明涉及聚酯切片技术领域,特别是涉及一种化学循环再生法生产膜级共聚聚酯切片的工艺。
背景技术:
2.我国的纺织废料产量超过2千万吨/年,约占城市固体废物总生产量的6%,其中,约70%为化学纤维。如此庞大的废料,大多最终被填埋或焚化处理。与焚烧和填埋相比,废旧纺织品的回收再利用,总体上可以减少对环境的影响,并且再生技术可以减少生产原生纺织纤维的需求,并减少纺织品产品生命周期下游的工程流程;国家发改委第29号令也推行利用聚酯回收材料生产涤纶工业丝、差别化和功能性涤纶长丝、非织造材料等高附加值产品。传统的物理再生法,满足不了纺丝成衣的要求,只有通过化学法循环再生技术,以废旧聚酯及聚酯纤维制品为生产原料,制成循环再利用聚酯纤维产品,才是高品质化处理废旧聚酯纺织品最理想的路径,并且该项技术从源头到末端的设计遵循了低能耗、低排放、低污染的原则,尤其是高精度过滤、精制再聚合等工艺过程的实现,不仅能确保再生品的品质达到原生产品的水平,拓展再生产品的应用领域,而且能实现废旧原料、加工、应用、废弃到再生的全循环,真正构建纺织纤维从“摇篮到摇篮”的多级、多次闭合绿色循环体系。
3.膜级聚酯切片是差别化、功能化聚酯纤维中的一种。随着时代的进步,各式电子类产品市场迅猛发展,光学聚酯薄膜因其在高透明性、较强的耐化学性以及优越的机械性能等方面具有明显优势,在对光学性能指标要求严格的液晶显示器、触摸屏等的反射膜、保护膜领域运用十分广阔。由此使得作为光学聚酯薄膜基材的光学膜专用聚酯切片的市场需求量也不断上升。但当前市场上通用的普通膜级聚酯切片在各类性能上还存在不少缺点,比如在光泽度、透明度、凝聚粒子等性能方面存在一定的缺陷,导致基于普通膜级聚酯切片生产的聚酯薄膜产品容易出现色泽偏灰、发黄、透明度不足等不良现象,大大限制了常规聚酯切片在光学膜领域的应用推广。此外,为改善后道聚酯薄膜产品的制膜等加工性能,在常规膜级聚酯切片的生产过程中通常还会加入一些稳定剂,也会对聚酯薄膜的透明度等光学性能产生一定程度的不良影响,制约了常规膜级聚酯切片的进一步推广应用。
技术实现要素:
4.本发明的目的在于克服上述现有技术的不足,提供一种化学循环再生法生产膜级共聚聚酯切片的工艺,通过该工艺制备所得的再生膜级聚酯切片具有高开口性能、低磨损性、优越的过滤性能、优异的光学性能等特点,适应各种线速度的聚酯薄膜生产,本发明实现了废旧资源的循坏利用,同时解决环境污染问题。
5.为了实现上述目的,本发明采用如下技术方案:
6.一种化学循环再生法生产膜级共聚聚酯切片的工艺,包括以下步骤:
7.(a)将回收废旧涤纶纺织品经预处理后得到的涤纶泡料输送至解聚反应釜,加入eg、涤纶泡料、碳酸钾催化剂溶液进行解聚反应,生成bhet;
8.(b)将所得bhet混合液进行涤棉分离、浓缩处理,然后输送至酯交换反应釜中与甲醇溶液、碳酸钾催化剂溶液进行酯交换反应,得到粗dmt溶液和eg;
9.(c)将粗dmt溶液进行脱色、精馏、冷却结晶处理,得到纯净的dmt晶体;
10.(d)dmt的酯交换:将纯净的dmt与eg、酯交换催化剂和deg抑制剂加入酯交换反应釜中,边升温边进行反应,并于反应过程中析出甲醇;反应完成后逐步升温至244~246℃,同时在该时间段内加入sio2粒径在10nm以下的sio2乙二醇分散液并搅拌均匀;蒸馏出多余的eg,控制反应釜顶温在190℃以内,并向酯交换反应釜内添加聚合催化剂、稳定剂和补色剂;
11.(e)采用氮气加压方式将酯交换反应釜中的bhet溶液体系过滤处理后输送至聚合釜中进行聚合反应,反应结束后经冷却、切粒、干燥,得到再生膜级聚酯切片。
12.步骤(a)中,预处理具体步骤为:将废旧涤纶纺织品分拣去除拉链,通过螺杆挤压机熔融造粒,得到涤纶泡料。
13.步骤(a)中,eg、涤纶泡料、碳酸钾催化剂溶液的物料比为15m3:8.5吨:320kg;解聚反应温度为180-250℃,反应时间为2~4h,解聚反应釜压力控制为0.2mpa。
14.步骤(b)中,涤棉分离、浓缩处理步骤具体为:将解聚所得bhet溶液过滤以分离出不溶于乙二醇的杂质,然后将涤棉分离后的bhet溶液进行加热浓缩。
15.步骤(b)中,甲醇溶液、经浓缩处理的bhet溶液及碳酸钾催化剂溶液的物料比为18~30m3:10~20m3:200~400kg;酯交换反应的反应温度为70~120℃。
16.步骤(c)中,精制纯净dmt晶体的具体步骤为:通过甲醇对粗dmt溶液进行脱色,经过多次离心分离,得到较纯净的dmt,然后在6~13kpa、200~209℃条件下进行精馏,再降温至35~50℃进行真空冷却结晶,析出纯净的dmt晶体。
17.步骤(d)中,酯交换反应完成后,sio2乙二醇分散液在酯交换反应釜升温至235℃时并在蒸馏eg前的时段内加入。
18.步骤(d)中,dmt酯交换的具体步骤为:
19.(a)将eg、dmt、酯交换催化剂和deg抑制剂加入酯交换反应釜中进行升温搅拌,eg、dmt、酯交换催化剂和deg抑制剂的用量比1180kg:2050kg:32kg:100g;
20.(b)当酯交换反应釜温度升至140~180℃时,反应开始并析出甲醇,通过回流控制反应釜顶温在70℃以内;随着温度逐渐升高,甲醇不断析出,当温度达到222℃时确认反应完成;
21.(c)采用分散处理进样装置制备sio2乙二醇分散液并将其喷淋输送至酯交换反应釜,继续均匀搅拌;sio2、乙二醇与dmt的质量比为10:400:2050。
22.(d)待酯交换反应釜内温度升温至244~246℃时,将多余的eg采出至eg接受罐,通过回流控制反应釜顶温在190℃以内,并添加聚合催化剂、稳定剂和补色剂,其中聚合催化剂、稳定剂、补色剂与dmt的质量比为47kg:2.35kg:10g:2050kg。
23.步骤(c)中,分散处理进样装置包括二氧化硅搅拌罐、胶体分散研磨泵、成品罐、屏蔽泵、质量流量计和喷淋系统,所述二氧化硅搅拌罐与胶体分散研磨泵间通过第一蒸汽保温管道、第二蒸汽保温管道连通成回路,所述胶体分散研磨泵与成品罐入口间通过第三蒸汽保温管道连通连通,所述喷淋系统设置于酯交换反应釜内,所述成品罐出口与喷淋系统间通过第四蒸汽保温管道连通,所述第四蒸汽保温管道上依次安装屏蔽泵和质量流量计;
24.sio2乙二醇分散液的配制及喷淋输送的具体步骤为:于加有乙二醇的二氧化硅搅拌罐中加入sio2并搅拌分散3h,然后输送至胶体分散研磨泵进行研磨后再回流至二氧化硅搅拌罐中继续搅拌,通过二氧化硅搅拌罐与胶体分散研磨泵回路间的多次循环操作,制得分散均匀且sio2粒径在10nm以下的sio2乙二醇分散液,循环时间为3h;sio2乙二醇分散液配制完成后,经屏蔽泵、质量流量计后输送至喷淋系统并喷出。
25.步骤(e)中,聚合反应的具体步骤为:
26.a、加热:采用热媒加热方式对聚合釜内液体进行加热,待温度升温至268~270℃时断温;
27.b、抽真空:先后通过小阀抽吸、大阀抽吸、动力蒸汽方式对聚合釜进行抽真空处理,最终达到真空度为10~20pa的高真空状态;
28.c、高低速搅拌反应:在反应初期以99.9%的搅拌频率进行高速搅拌反应,待聚合釜内温度达到291~295℃时切换至45%的搅拌频率进行低速搅拌反应,当聚合釜的搅拌电力达到19kw及温度控制至291~295℃时,停止搅拌,得到聚酯熔体。
29.本发明的有益效果是:以废旧聚酯纺织品为原料,通过添加采用独特分散技术处理的纳米级sio2,合成具有高开口性能、低磨损性、优越的过滤性能、优异的光学性能等特点的再生膜级聚酯切片,适用于各种线速度的聚酯薄膜生产线,并实现了废旧资源的循坏利用,减少了环境污染。
附图说明
30.图1为本发明的切粒水净化装置的整体结构图;
31.图2为图1中a处的放大图;
32.图3为图2中c处的放大图;
33.图4为图1中b-b向的剖面图;
34.图5为本发明杂质排出机构中第二过滤网外移至杂质槽的俯视结构图;
35.图6为本发明图5中d处的放大图;
36.图7为本发明分散处理进样装置的结构图。
37.图中:第一箱体1、第一管道2、第一阀门21、第一过滤网22、第二管道3、第二阀门31、第二箱体4、过滤箱5、第二过滤网51、外框511、内网部512、转柱513、柱孔514、通孔515、第三阀门52、限位部53、气缸54、储杂槽6、第一抵接块61、第一电机62、第二电机63、连轴631、驱动轴632、分散处理进样装置7、二氧化硅搅拌罐71、胶体分散研磨泵72、成品罐73、屏蔽泵74、质量流量计75、喷淋系统76、第一蒸汽保温管道77、第二蒸汽保温管道78、第三蒸汽保温管道连通79、第四蒸汽保温管道连通791。
具体实施方式
38.下面结合附图和具体实施方式对本发明作进一步描述:
39.实施例1
40.一种化学循环再生法生产膜级共聚聚酯切片的工艺,包括以下步骤:
41.(a)将回收废旧涤纶纺织品经预处理后得到的涤纶泡料输送至解聚反应釜,加入eg、涤纶泡料、碳酸钾催化剂溶液进行解聚反应,生成bhet;
42.预处理具体步骤为:将废旧涤纶纺织品分拣去除拉链,通过螺杆挤压机熔融造粒,得到涤纶泡料。
43.eg、涤纶泡料、碳酸钾催化剂溶液的物料比为15m3:8.5吨:320kg;解聚反应温度为200℃,反应时间为3h,解聚反应釜压力控制为0.2mpa。碳酸钾催化剂的浓度为40%-60%。
44.(b)将所得bhet混合液进行涤棉分离、浓缩处理,然后输送至酯交换反应釜中与甲醇溶液、碳酸钾催化剂溶液进行酯交换反应,得到粗dmt溶液和eg;
45.涤棉分离、浓缩处理步骤具体为:将解聚所得bhet溶液过滤以分离出棉、麻等不溶于乙二醇的杂质,然后将涤棉分离后的bhet溶液进行加热浓缩,以提高体系中bhet的含量,且保证液体的流动性。
46.甲醇溶液、经浓缩处理的bhet溶液及碳酸钾催化剂溶液的物料比为20m3:15m3:300kg;酯交换反应的反应温度为120℃。碳酸钾催化剂的浓度为40%-60%。
47.(c)将粗dmt溶液进行脱色、精馏、冷却结晶处理,得到纯净的dmt晶体;
48.精制纯净dmt晶体的具体步骤为:通过甲醇对粗dmt溶液进行脱色,经过多次离心分离,得到较纯净的dmt,然后在6~13kpa、200~209℃条件下进行精馏,再降温至35~50℃进行真空冷却结晶,析出纯净的dmt晶体。期间用于脱色的甲醇进行回收利用。
49.(d)dmt的酯交换:将纯净的dmt与eg、酯交换催化剂和deg抑制剂加入酯交换反应釜中,边升温边进行反应,并于反应过程中析出甲醇;反应完成后逐步升温至244~246℃,同时在该时间段内加入sio2粒径在10nm以下的sio2乙二醇分散液并搅拌均匀,更具体的,sio2乙二醇分散液在酯交换反应釜升温至235℃时并在蒸馏eg前的时段内加入;蒸馏出多余的eg,控制反应釜顶温在190℃以内,并向酯交换反应釜内添加聚合催化剂、稳定剂和补色剂。
50.该步骤中,dmt酯交换的具体步骤为:
51.(a)将eg、dmt、酯交换催化剂和deg抑制剂加入酯交换反应釜中进行升温搅拌,eg、dmt、酯交换催化剂和deg抑制剂的用量比1180kg:2050kg:32kg:100g;酯交换催化剂为醋酸锰,deg抑制剂为醋酸钠;
52.(b)当酯交换反应釜温度升至140~180℃时,反应开始并析出甲醇,通过回流控制反应釜顶温在70℃以内;
53.甲醇经过酯交换工艺塔、冷凝器冷凝后流入到甲醇接受罐;随着温度逐渐升高,甲醇不断析出,得到bhet和甲醇,所得甲醇经过酯交换工艺塔、冷凝器冷凝后流入甲醇接受罐;当温度达到222℃时确认反应完成。
54.(c)采用分散处理进样装置7制备sio2乙二醇分散液并将其喷淋输送至酯交换反应釜,继续均匀搅拌;sio2、乙二醇与dmt的质量比为10:400:2050。
55.步骤(c)中,分散处理进样装置7包括二氧化硅搅拌罐71、胶体分散研磨泵72、成品罐73、屏蔽泵74、质量流量计75和喷淋系统76,所述二氧化硅搅拌罐71与胶体分散研磨泵72间通过第一蒸汽保温管道77、第二蒸汽保温管道78连通成回路,所述胶体分散研磨泵72与成品罐73入口间通过第三蒸汽保温管道连通79连通,所述喷淋系统76设置于酯交换反应釜内,所述成品罐73出口与喷淋系统76间通过第四蒸汽保温管道连通791,所述第四蒸汽保温管道上依次安装屏蔽泵74和质量流量计75;
56.sio2乙二醇分散液的配制及喷淋输送的具体步骤为:于加有乙二醇的二氧化硅搅
拌罐71中加入sio2并搅拌分散3h,然后输送至胶体分散研磨泵72进行研磨后再回流至二氧化硅搅拌罐71中继续搅拌,通过二氧化硅搅拌罐71与胶体分散研磨泵72回路间的多次循环操作,制得分散均匀且sio2粒径在10nm以下的sio2乙二醇分散液,循环时间为3h。sio2乙二醇分散液配制完成后,经屏蔽泵74、质量流量计75后输送至喷淋系统76并喷出。
57.(d)待酯交换反应釜内温度升温至244~246℃时,将多余的eg采出至eg接受罐,通过回流控制反应釜顶温在190℃以内,并添加聚合催化剂、稳定剂和补色剂,其中聚合催化剂、稳定剂、补色剂与dmt的质量比为47kg:2.35kg:10g:2050kg。聚合催化剂为三氧化二锑,稳定剂为磷酸三甲酯,补色剂为醋酸钴。
58.(e)采用氮气加压方式将酯交换反应釜中的bhet溶液体系经25μm的过滤器过滤后输送至聚合釜中进行聚合反应,反应结束后向聚合釜中通入氮气并控制聚合釜内压力为0.32mpa,聚酯熔体经冷却、切粒、干燥,得到再生膜级聚酯切片。
59.该步骤中,聚合反应的具体步骤为:
60.a、加热:采用热媒加热方式对聚合釜内液体进行加热,待温度升温至268~270℃时断温;
61.b、抽真空:先后通过小阀抽吸、大阀抽吸、动力蒸汽方式对聚合釜进行抽真空处理,最终达到真空度为10~20pa的高真空状态;
62.c、高低速搅拌反应:在反应初期以99.9%的搅拌频率进行高速搅拌反应,待聚合釜内温度达到291~295℃时切换至45%的搅拌频率进行低速搅拌反应,当聚合釜的搅拌电力达到19kw及温度控制至281~286℃时,停止搅拌,得到聚酯熔体。
63.实施例2
64.按实施例1的方法生产切片,不同之处在于:步骤(a)中,解聚反应温度为180℃,反应时间为4h;步骤(b)中,甲醇溶液、经浓缩处理的bhet溶液及碳酸钾催化剂溶液的物料比为25m3:20m3:200kg;酯交换反应的反应温度为100℃。
65.实施例3
66.按实施例1的方法生产切片,不同之处在于:步骤(a)中,解聚反应温度为220℃,反应时间为3h;步骤(b)中,甲醇溶液、经浓缩处理的bhet溶液及碳酸钾催化剂溶液的物料比为18m3:10m3:300kg;酯交换反应的反应温度为70℃。
67.实施例4
68.按实施例1的方法生产切片,不同之处在于:步骤(a)中,解聚反应温度为250℃,反应时间为2h,解聚反应釜压力控制为0.2mpa;步骤(b)中,甲醇溶液、经浓缩处理的bhet溶液及碳酸钾催化剂溶液的物料比为30m3:20m3:400kg;酯交换反应的反应温度为100℃。
69.各实施例主要不同之处在于步骤(b)中甲醇溶液、经浓缩处理的bhet溶液及碳酸钾催化剂溶液的物料比,其余工艺参数根据需要选择合适值,所得切片性能如表1所示。
70.表1
[0071][0072]
按照现有方法将实施例1-4制备的切片制成薄膜后的性能如表2所示。
[0073]
表2
[0074][0075]
切粒操作需要采用切粒系统进行,若供给切粒系统内切粒机的切粒水中夹带的粉尘和杂质过多,会导致切粒机启动板上的溢流水出口部分堵塞,被堵塞的地方对应的铸带板部分得不到充分冷却,使熔体通过这一部分铸带板后进行切粒时易出现毛边和长短不一的切片,切片成型质量不佳,导致后续纺丝阶段的连续生产出现质量问题,因此需要及时将切粒水进行净化处理,而传统的切粒水在净化时往往需要停止切粒操作并停止切粒水的循环,才能进行清理,影响了切片的生产效率。
[0076]
如图1~图6所示,本发明切粒时采用的切粒水净化装置包括依次连通的第一箱体1、第一管道2、第二管道3和第二箱体4及连接在第一管道2下方的杂质排出机构,所述第一箱体1高度高于第二箱体4,所述第一管道2、第二管道3均为横向设置,所述第二管道3的管高高于第一管道2的管高且低于第二箱体4的高度,所述第一管道2通过第一阀门21控制连通或隔断,所述第二管道3通过第二阀门31控制连通或隔断,所述第一管道2和第二管道3之间固装有第一过滤网31,所述杂质排出机构包括过滤箱5和设于过滤箱5内的可伸出过滤箱5的第二过滤网51,所述过滤箱5与第一管道2间通过第三阀门52控制连通或隔断,所述第二过滤网51用于过滤流入过滤箱5内的切粒水杂质并将残留的杂质排出。
[0077]
所述第一箱体1的高度为第二箱体4的高度的两倍以上,所述第二管道3的管高为第一管道2管高的两倍以上。
[0078]
所述第一箱体1用于暂存含杂质的切粒水,所述第一箱体1内的切粒水经第一过滤网31过滤后流向第二管道3和第二箱体4;当第二箱体4内储满切粒水时,所述第一管道2和第二管道3内储满切粒水,所述第一箱体1内切粒水液位高大于等于第二箱体4内的液位高,所述第二管道3内的液位高高于第一管道2的液位高;当第二箱体4内储满切粒水且第一阀门21和第二阀门31均关闭、第三阀门52开启时,所述第二管道3内的切粒水进入第一管道2
并可反向冲洗第一过滤网22。
[0079]
所述过滤箱5内壁设有环状限位部53,所述第二过滤网51包括外框511和铰接在外框511内的可翻转的内网部512,所述外框511和内网部512一并压接在限位部53上。
[0080]
所述外框511的一端连接有用于推动第二过滤网51水平移出过滤箱5的气缸54。所述内网部512两侧通过转柱513与外框511转动连接,远离气缸54的所述转柱513内设有多边形柱孔514,远离气缸54的所述外框511内开设有通孔515,所述通孔515与柱孔514连通且同中心轴设置。
[0081]
所述杂质排出机构还包括设于过滤箱5一侧的储杂槽6,当第二过滤网51被推出过滤箱5后,所述第二过滤网51伸入储杂槽6内并可沿着储杂槽6滑动。以图1为参照,储杂槽6左右两侧部上端面与第二过滤网51下端面齐平,储杂槽6前后两侧部高出储杂槽6左右两侧部,储杂槽6前后两侧部对第二过滤网51具有移动导向作用。
[0082]
所述储杂槽6一内壁上设有可周向转动的第一抵接块61,第一抵接块61通过第一电机62驱动转动。当第二过滤网51被完全推出过滤箱5后,所述外框511和内网部512一并搁置在第一抵接块61上。当第一抵接块61转动至水平时,所述内网部512可进行翻转。
[0083]
所述储杂槽6远离过滤箱5的一侧设有第二电机63,所述第二电机63轴端连接有圆柱形连轴631,所述连轴631前端连接有多边形驱动轴632,所述连轴631的直径尺寸小于通孔515的直径尺寸,所述驱动轴632可与柱孔514配合卡合。
[0084]
本装置的工作过程是;初始时,带杂质切粒水进入第一箱体1内并暂存,第一管道2、第二管道3、第二箱体4为空,第一阀门21、第二阀门31、第三阀门52均关闭;当第一箱体1储满时,打开第一阀门21、第二阀门31,切粒水自动流向第二箱体4直至第二箱体4内充满切粒水;然后关闭第一阀门21、第二阀门31,开启第三阀门52,靠近第一过滤网22一侧的第一管道2内的切粒水进入过滤箱5并经第二过滤网51过滤,靠近第一过滤网22一侧的第二管道3内的切粒水反冲洗第一过滤网22后流入过滤箱5并经第二过滤网51过滤,排水完毕即关闭第三阀门52,切粒水中的杂质残留在第二过滤网51上,在此过程中,第一箱体1内一直持续注入含杂质切粒水且第二箱体4内逐步排出过滤后的切粒水;在关闭第三阀门52后,气缸54推动第二过滤网51移出至储杂槽6,驱动轴632卡入柱孔514内,第一电机62驱动第一抵接块61转动至水平状态,然后第二电机63通过驱动轴632带动内网部512翻转而将杂质排出,之后翻转内网部512至水平,第一电机62驱动第一抵接块61回复至竖直状态,气缸54带动第二过滤网51回复至过滤箱5内。本装置通过合理的结构实现切粒水的持续除杂净化,即在排出杂质时完全不影响切粒水的循环,保证了切粒水的洁净状态,确保了切片的成型质量,同时每次流入过滤箱5的切粒水为极少一部分且时间较短,可进行切粒水回收利用的同时并不影响切粒水的持续循环。
[0085]
以上所述仅为本发明的较佳实施例,并不用以限制本发明,凡在本发明的精神和原则之内,所作的任何修改、等同替换、改进等,均应包含在本发明的保护范围之内。