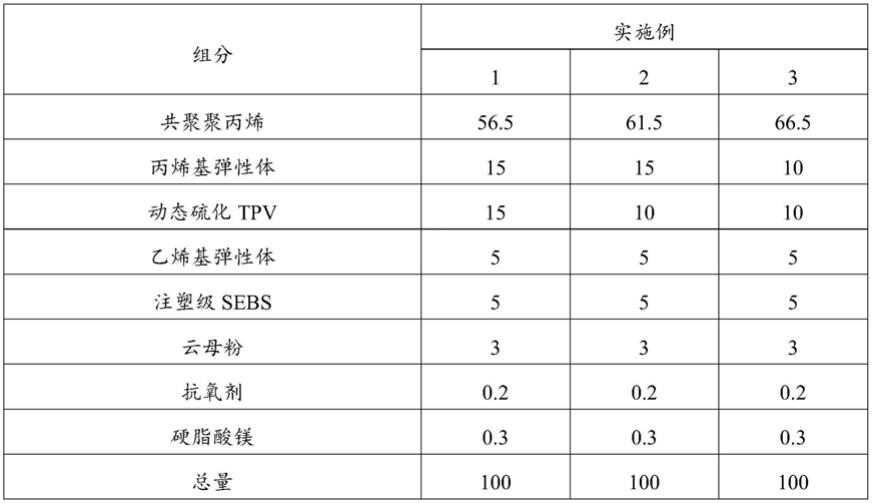
1.本发明涉及一种改性聚丙烯材料及其制备方法,尤其涉及一种适用于汽车内饰仪表板的低光泽软质基料及其制备方法,属于多功能改性高分子混合物技术领域。
背景技术:
2.目前汽车仪表板主要使用两种材料制备形成:一种为硬质聚丙烯材料,该种材料的光泽度较高,手感较差,人体感官较低档;另一种为软质的pvc搪塑材料,该种材料的触感较软有皮质感,光泽度低,但由于需要开多套模具且模具成本高,工艺线长且工艺复杂,不良率高,整体造价成本高,因此目前主要用于中高档车。
3.现有技术中常规的聚丙烯光泽度较高且冲击强度较低。汽车仪表板涉及到负40度下安全气囊的爆破,因此其使用的基料对冲击强度的要求较高;同时为了不影响行驶过程中驾驶员的视线,光泽度要求尽可能的低。
4.现有技术中为了达到低光泽,大多采用添加大量粉体添加剂的方式对混合物进行改性,但大量粉体的增加会劣化材料的力学性能,尤其是冲击强度;同时现有技术中为了改善冲击性能,也会使用其他树脂材料进行共混;但上述技术方案均不能同时达到汽车内饰板使用时光泽度和软质特性的需求,尤其是树脂基料方面难以达到相应的性能需求。
技术实现要素:
5.为解决上述技术问题,本发明提供了一种适用于汽车内饰仪表板的低光泽软质基料及其制备方法,由该制备方法制备所得的低光泽软质基料适用于作为汽车内饰仪表板材料的基料使用,其作为基料使用时,能够以成本低廉的聚丙烯材料实现一体注塑成型为软触感低光泽的汽车仪表板,合格率高,同时对不良品易于回用再加工,降低了产品整体的造价成本。
6.本发明的技术方案是:
7.本发明公开了一种适用于汽车内饰仪表板的低光泽软质基料,该低光泽软质基料主要由下述按重量份计的各组分制备形成:55-70份共聚聚丙烯、10-15份丙烯基弹性体、10-15份动态硫化tpv、5-10份乙烯基弹性体、5-10份注塑级sebs、3-5份云母粉、抗氧剂0.1-1份和润滑剂0.1-1份。
8.其进一步的技术方案是:
9.所述共聚聚丙烯在2.16kg且230℃条件下的熔融指数为3-5g/10min。
10.所述丙烯基弹性体的乙烯含量为10-15wt.%。
11.所述动态硫化tpv为pp/pe/epdm动态硫化共混制备形成的材料。
12.所述乙烯基弹性体的辛烯含量为40-42wt.%。
13.所述注塑级sebs的苯乙烯含量为29-31wt.%。
14.所述云母粉为高长径比云母粉,且该云母粉的长径比为(20-22):1。
15.本发明还公开了一种上述适用于汽车内饰仪表板的低光泽软质基料的制备方法,
该制备发方法主要包括下述步骤:
16.s1,将共聚聚丙烯、丙烯基弹性体、动态硫化tpv和乙烯基弹性体加入高速剪切挤出机中,进行挤出造粒,得到初级材料;
17.s2,将所得初级材料与注塑级sebs、云母粉、抗氧剂、润滑剂加入高速剪切挤出机中,进行挤出造粒,得到所述适用于汽车内饰仪表板的低光泽软质基料。
18.其进一步的技术方案是:
19.步骤s1中,进行挤出造粒的条件为300-500rpm的剪切速度且190-210℃的挤出造粒温度;步骤s2中,进行挤出造粒的条件为600-800rpm的剪切速度且190-210℃的挤出造粒温度。
20.本发明还公开了一种上述适用于汽车内饰仪表板的低光泽软质基料低光泽软质基料的应用,主要为用于汽车内饰仪表板用玻纤改性聚丙烯材料的制备。
21.本发明的有益技术效果是:
22.本发明所述软质基料以共聚聚丙烯为基体树脂,按照特定比例添加具有不同特性的多种橡胶组分,如丙烯基弹性体、动态硫化tpv、乙烯基弹性体和注塑级sebs,来改善聚丙烯基体的冲击强度,使得该基料的软质特性增强;同时在组成中添加了特定比例和长径比的云母粉,结合多种橡胶组分的折光特性,使该基料具有较低的光泽度。该基料在能够同时满足低光泽和软质的基础上,同时具有制备简单且成本较低,及可回收利用的特性,能够大大降低生产成本。
具体实施方式
23.为了能够更清楚了解本发明的技术手段,并可依照说明书的内容予以实施,下面结合具体实施例,对本发明的具体实施方式作进一步详细描述,以下实施例用于说明本发明,但不用来限制本发明的范围。
24.下述实施例中记载了适用于汽车内饰仪表板的低光泽软质基料,该基料主要由下述按重量份计的各组分制备形成:55-70份共聚聚丙烯、10-15份丙烯基弹性体、10-15份动态硫化tpv、5-10份乙烯基弹性体、5-10份注塑级sebs、3-5份云母粉、抗氧剂0.1-1份和润滑剂0.1-1份。
25.其中共聚聚丙烯在2.16kg且230℃条件下的熔融指数为3-5g/10min。
26.其中丙烯基弹性体的乙烯含量为10-15wt.%。
27.其中动态硫化tpv为pp/pe/epdm动态硫化共混制备形成的材料,本具体实施例中优选美孚121-65m300。
28.其中乙烯基弹性体的辛烯含量为40-42wt.%。
29.其中注塑级sebs的苯乙烯含量为29-31wt.%。
30.其中云母粉为高长径比云母粉,且该云母粉的长径比为(20-22):1。
31.其中抗氧剂可采用抗氧剂168、抗氧剂1010等,本具体实施例中采用抗氧剂168和抗氧剂1010按照质量比为2:1混合形成。
32.其中润滑剂采用硬脂酸盐,本具体实施例中采用硬脂酸镁。
33.使用上述组分以下述表1中所示配方按照下述方法进行适用于汽车内饰仪表板的低光泽软质基料的制备,主要包括下述步骤:
34.s1,将共聚聚丙烯、丙烯基弹性体、动态硫化tpv和乙烯基弹性体加入高速剪切挤出机中,以300-500rpm的剪切速度且190-210℃的挤出造粒温度进行挤出造粒,得到初级材料;
35.s2,将所得初级材料与注塑级sebs、云母粉、抗氧剂、润滑剂加入高速剪切挤出机中,以600-800rpm的剪切速度且190-210℃的挤出造粒温度进行挤出造粒,得到所述适用于汽车内饰仪表板的低光泽软质基料。
36.表1实施例所述低光泽软质基料的配方组成(单位:重量份)
[0037][0038]
对上述制备所得的低光泽软质基料进行力学性能和光泽度的测试,测试标准及测试方法如下,测试结果参见表2中所述。
[0039]
拉伸强度:测试方法参照iso 527;
[0040]
弯曲强度:测试方法参照iso 178;
[0041]
邵氏硬度shored;测试方法参照gb 2411-1980;
[0042]
热变形温度hdt:gb/t 1634.1-2004和gb/t 1634.2-2004;
[0043]
光泽度:astm_d2457-2013。
[0044]
表2实施例各项性能测试结果
[0045][0046][0047]
从上述测试结果中可以看出,使用本技术所述配方及制备方法制备所得得基料,
其质软和光泽度较低,可用于汽车内饰仪表板用玻纤改性聚丙烯材料的制备使用。
[0048]
以上所述仅是本发明的优选实施方式,并不用于限制本发明,应当指出,对于本技术领域的普通技术人员来说,在不脱离本发明技术原理的前提下,还可以做出若干改进和变型,这些改进和变型也应视为本发明的保护范围。