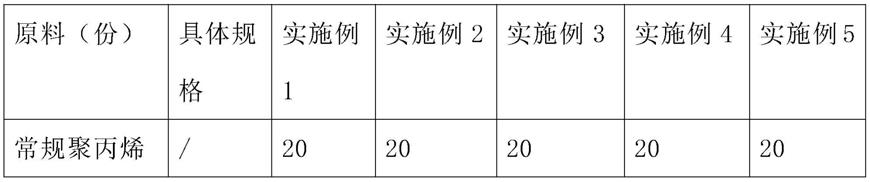
1.本发明涉及汽车内饰材料技术领域,尤其涉及一种汽车内饰用改性聚丙烯及其制备方法。
背景技术:
2.汽车是人们日常生活中常用的一种交通工具,汽车内饰通常由聚丙烯(pp)材质制作而成,为了改变聚丙烯的特性,通常往常规聚丙烯中添加其他的添加剂,使其具有更佳优良的特性,从而更好的满足人们的使用需求。汽车内饰用改性聚丙烯通常需要满足两个条件,即低光泽度,进而减小车内反光对驾驶者造成的影响;低挥发性有机物,进而减小对驾驶者的身体造成的不良影响。
3.为了减小聚丙烯材质本身的光泽度,通常在对改性聚丙烯进行制备时,会在原料里添加与聚丙烯基材相容性较差的橡胶来降低光泽度,如聚硫橡胶,丙烯酸酯橡胶,丁腈橡胶,三元乙丙橡胶以及马来酸酐接枝共聚物。这些橡胶添加物,虽然能够降低聚丙烯材质本身的光泽度,但是由于橡胶添加物的稳定性较差,在温度较高时,容易老化分解,进而产生挥发性有有机气体(voc),影响使用者的身体健康。
技术实现要素:
4.本发明的其中一个目的是提供一种汽车内饰用改性聚丙烯,具有良好的稳定性,在日常使用过程中相较于传统的汽车内饰用改性聚丙烯产生的挥发性有机物更少。
5.本发明的上述目的是通过以下技术方案实现的:
6.一种汽车内饰用改性聚丙烯,按质量份数计,包括20至50份常规聚丙烯、20至50份高抗冲聚丙烯、8至20份无机填料、5至20份低光泽材料母粒、0至5份除味剂、0至3份抗氧剂、0至3份光稳定剂、0至3份缚酸剂、0至3份润滑剂;
7.所述低光泽材料母粒,按质量份数计,包括30至70份常规聚丙烯、10至50份聚烯烃弹性体、1至20份茂金属催化聚乙烯、0至0.6份抗氧剂、0至1份润滑剂;
8.所述低光泽材料母粒按照以下方法进行制备:
9.将常规聚丙烯、聚烯烃弹性体、茂金属催化聚乙烯、抗氧剂以及润滑剂加入到高速混料机进行混合均匀,形成混合原料;
10.然后将混合原料放入密炼机中进行密炼,密炼机密炼温度设为180-200℃;
11.将密炼后的原料加入单螺杆挤出机,单螺杆挤出机的温度设置为180至190℃;通过单螺杆挤出机对密炼后的原料进行挤出、风冷、造粒,进而形成低光泽材料母粒。
12.通过上述技术方案,汽车内饰用改性聚丙烯的配方中通过制备低光泽材料母粒作为基础材料加入到改性聚丙烯的原料中,进而替换原有的橡胶添加物;
13.其中低光泽材料母粒的配方中聚烯烃弹性体和茂金属催化聚乙烯作为基材,通过密炼工艺使聚烯烃弹性体和茂金属催化聚乙烯与常规聚丙烯充分融合;聚烯烃热塑性弹性体是一种高性能聚烯烃,具有密度小、弯曲大、低温抗冲击性能高等特性;茂金属催化聚乙
烯具有良好的力学韧性以及减薄性能,并且聚烯烃弹性体和茂金属催化聚乙烯链状结构更加稳定,在外界环境下不易发生分解;通过上述分析,以低光泽材料母粒替换改性聚丙烯的原料中的橡胶添加物,不仅能够减少成品改性聚丙烯产生的挥发性有机物的发散,而且能够提高改性聚丙烯的抗冲击性能和韧性。
14.较佳的,所述聚烯烃弹性体由乙烯-辛烯共聚物和乙烯-丁烯共聚物组成,所述乙烯-辛烯共聚物与乙烯-丁烯共聚物质量份数的比为1:1。
15.通过上述技术方案,聚烯烃弹性体由乙烯-辛烯共聚物和乙烯-丁烯共聚物组成,进而能够融合乙烯-辛烯共聚物以及乙烯-丁烯共聚物的优点,使得到的聚烯烃弹性体能够综合两者的力学特性,进而使产生的改性聚丙烯力学性能更加均衡。
16.较佳的,所述常规聚丙烯,在230℃,2.16kg负荷下的熔体质量流动速率为10g/10min~70g/10min;
17.所述高抗冲聚丙烯,在230℃,2.16kg负荷下的熔体质量流动速率为1g/10min~40g/10min。
18.较佳的,所述无机填料为滑石粉、硅灰石、云母、空心玻璃微珠、矿粉纤维中的任意一种或几种。
19.本发明的另一个目的是提供一种汽车内饰用改性聚丙烯制备方法,本发明的上述目的是通过以下技术方案实现的:
20.一种汽车内饰用改性聚丙烯制备方法,包括以下步骤:
21.步骤s1,将按质量份数计,取材20至50份常规聚丙烯、20至50份高抗冲聚丙烯、8至20份无机填料、5至20份低光泽材料母粒、0至5份除味剂、0至3份抗氧剂、0至3份光稳定剂、0至3份缚酸剂、0至3份润滑剂;将原材料投入到双螺杆挤出机进行挤出造粒,双螺杆挤出机温度设置为180至220℃;双螺杆挤出机的转速设置为200至500转/分钟;双螺杆挤出机的真空度设置大于等于0.08mpa;
22.步骤s2,在完成步骤s1后,对双螺杆挤出机挤出的原料颗粒进行干燥处理,在90-120℃环境下持续烘干2-6小时;
23.步骤s3,在完成步骤s2后,将干燥处理后的原料颗粒投入注塑机中进行注射成型加工。
24.通过上述技术方案,通过双螺杆挤出机将各种原材料进行混合,进而使各种原料能够充分混合,进而良好的挤出造粒;成型的塑料颗粒经过恒温区温度进行干燥,进而高效良好的去除塑料颗粒中的水分,从而进一步保证成品改性聚丙烯产品的质量。
具体实施方式
25.下面将结合本发明的具体实施例对本发明的技术方案进行清楚、完整地描述,显然,所描述的实施例仅仅是本发明的一部分实施例,而不是全部的实施例。基于本发明中的实施例,本领域普通技术人员在没有作出创造性劳动前提下所获得的所有其他实施例,都属于本发明保护的范围。
26.制备例
27.一种低光泽材料母粒制备方法,包括以下步骤,
28.1)按照如下重量份称取原料:常规聚丙烯50份,10份聚烯烃弹性体,0.3份抗氧化
剂,0.5份润滑剂,
29.聚烯烃弹性体、茂金属催化聚乙烯、抗氧剂以及润滑剂加入到高速混料机进行混合均匀,形成混合原料;
30.2)将上述原料放入密炼机中进行密炼,密炼机密炼温度设为190℃;
31.3)将密炼后的原料加入单螺杆挤出机,单螺杆挤出机的温度设置为185℃;通过单螺杆挤出机对密炼后的原料进行挤出、风冷、造粒,进而形成低光泽材料母粒。
32.实施例
33.实施例1:
34.一种汽车内饰用改性聚丙烯制备方法,包括以下方法步骤:
35.步骤s1,按照以下质量份数称取原料:常规聚丙烯20份、高抗冲聚丙烯20份、无机填料8份、低光泽材料母粒5份、除味剂5份、抗氧剂3份、光稳定剂3份、缚酸剂3份、润滑剂3份。
36.将上述原料加入到双螺杆挤出机进行挤出造粒;双螺杆挤出机温度设置为200℃;双螺杆挤出机的转速设置为400转/分钟;双螺杆挤出机的真空度设置为0.1mpa;
37.步骤s2,对双螺杆挤出机挤出的原料颗粒进行干燥处理,在100℃环境下持续烘干4小时;
38.步骤s3,将干燥处理后的原料颗粒投入注塑机中进行注射成型加工。
39.包括20至50份常规聚丙烯、20至50份高抗冲聚丙烯、8至20份无机填料、5至20份低光泽材料母粒、0至5份除味剂、0至3份抗氧剂、0至3份光稳定剂、0至3份缚酸剂、0至3份润滑剂;
40.实施例2至5与实施例1制备方法与实施例1的相同,区别仅在于如表1所示:
41.表1实施例1-5汽车内饰用改性聚丙烯的原料组成及用量
42.[0043][0044]
对比例
[0045]
对比例1
[0046]
对比例1与实施例1的制备方法相同,其区别仅在于原料中不包含高抗冲聚丙烯。
[0047]
对比例2
[0048]
对比例2与实施1中的制备方法相同,其区别仅在于原料中不包含低光泽材料母粒。
[0049]
对比例3
[0050]
对比例3与实施1中的制备方法相同,其区别仅在于原料中的5份低光泽材料母粒替换为5份聚硫橡胶。
[0051]
试验方法
[0052]
对实施例1-5制备的5种改性聚丙烯以及对比例1-3制备的3种改性聚丙烯分别进行性能测试实验,包括简支梁缺口冲击强度、弯曲模量、tvoc、气味等级以及光泽度。其中,简支梁缺口冲击强度参照iso179-1-2010规定的方法进行;弯曲模量采用iso178-2010规定的方法进行;tvoc采用气相色谱法;耐刮擦参照gmw14688规定的方法进行,气味等级使用美国华瑞型号为pgm-7320mini3000voc的气体检测仪上进行测试;光泽度测试按照gb8807用光泽度仪从光面60度角进行测试。
[0053]
表2实施例1-5和对比例1-3的测试结果
[0054][0055]
由表1和表2的数据可得,从实施例1至实施例3的测试数据可以看出,随着改性聚丙烯中低光泽材料母粒份数的占比的增加,改性聚丙烯的光泽度明显下降,并且挥发性有机物的发散量以及气味均有所下降。通过实施例1至3的测试数据,结合对比例和对比例3中的测试数据,可得到,在配合中加入低光泽材料母粒能够有效的降低成品改性聚丙烯的挥发性有机物的发散量以及气味,并且其抗冲击性能和抗弯曲性能较常规改性聚丙烯(实施例3)还有所提升。
[0056]
从实施例1、实施例4、实施例5以及对比例1和对比例3,可得,改性聚丙烯的中高抗冲聚丙烯的添加,对挥发性有机物的发散量以及气味产生影响减小,但是能够有效提高成品改性聚丙烯的抗冲击强度。
[0057]
虽然已经通过示例对本发明的一些特定实施例进行了详细说明,但是本领域的技术人员应该理解,以上示例仅是为了进行说明,而不是为了限制本发明的范围。本领域的技术人员应该理解,可在不脱离本发明的范围和精神的情况下,对以上实施例进行修改。本发明的范围由所附权利要求来限定。