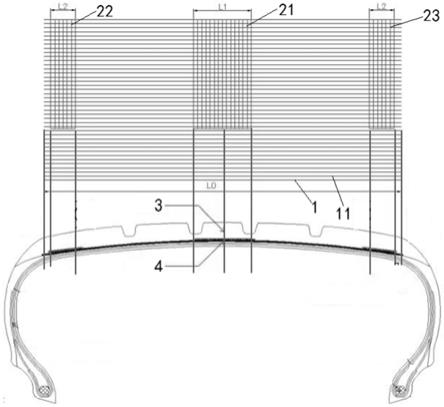
1.本实用新型属于乘用车轮胎领域,尤其涉及一种低滚阻轮胎。
背景技术:
2.随着欧洲轮胎标签法二阶段的实施,对轮胎滚动阻力、湿滑性能、噪音性能提出了更严格的要求,为应对欧洲制造的贸易技术壁垒,提高轮胎性能等级指标,提升产品技术附加值,国内轮胎企业纷纷开展对轮胎滚动、湿滑性能、噪音性能的研究。对于乘用车轮胎骨架材料设计,带束层主要设计目的是提高轮胎耐刺扎强度,当轮胎遇到尖锐物体时,提供抵抗冲击的力,避免轮胎被刺穿。冠带层设计目的是为了箍紧带束层。两种骨架材料用于实现两种不同目的,这种设计增加轮胎重量,使轮胎滚动阻力上升。
3.目前乘用车胎钢丝带束层大都使用至少两股单钢丝捻制而成,且钢丝直径不小于0.2mm,不大于0.5mm,钢丝排列密度不低于55epdm(epdm即钢丝平行排列,垂直于钢丝平行方向,10cm宽度内钢丝根数),不高于100epdm,单侧附胶厚度不小于0.3mm,较大的钢丝直径,为维持钢丝与胶料的粘合力,则带束层附胶厚度就必须提高,厚度大、钢丝粗,即单位面积内带束层的重量就会上升,成品轮胎重量也会增大,从而影响轮胎滚动阻力,导致滚动阻力系数变大。中国专利cn 110023104a公开了一种具有至少两层单钢丝带束层的充气轮胎,单钢丝直径0.33mm至0.37mm,优选直径0.35mm,epdm取值90至130,优化取值95epdm,该轮胎用带束层单位面积内钢丝消耗重量为827g/
㎡
,整体压延覆胶后带束层帘布重量约1589g/
㎡
,然而上述轮胎成品重量较重,不利于轮胎滚动阻力的降低。
4.综上所述,现有乘用车轮胎的带束层钢丝结构基本上都是由不小于1根的单钢丝组成,存在轮胎成品重量较重,不利于轮胎滚动阻力的降低的问题。
技术实现要素:
5.本实用新型的一个或多个实施例的细节在以下附图和描述中提出,以使本技术的其他特征、目的和优点更加简明易懂。
6.本实用新型提出一种低滚阻轮胎,解决了现有乘用车轮胎的带束层钢丝结构基本上都是由不小于1根的单钢丝组成,存在轮胎成品重量较重,不利于轮胎滚动阻力的的技术问题,具有既能保证轮胎的抗压穿强度,又可实现对带束层的箍紧作用,可实现轮胎重量的大幅度降低,实现乘用车轮胎轻量化目的,降低轮胎滚动阻力的特点。
7.本实用新型公开了一种低滚阻轮胎,带束层由钢丝及覆胶组成,所述带束层由胎里向轮胎接地面依次包括
8.第一钢丝带束层,包括沿轮胎胎面横向排列的第一钢丝,所述第一钢丝的长度与所述轮胎的胎面宽度l0相同;
9.第二钢丝带束层,采用三段间隔排列且沿轮胎胎面周向隔缠绕的钢丝组成;
10.所述第二钢丝带束层进一步包括
11.第一排列区,所述第一排列区的中心线与所述轮胎的胎面中心线重合;
12.第二排列区,位于所述第一排列区左侧,左侧边界与所述第一钢丝带束层的左侧边界的距离不小于3mm不大于15mm,右侧边界与所述第一排列区的中心线的距离不小于0.2
×
l0不大于0.45
×
l0;
13.第三排列区,与所述第二排列区沿所述轮胎的胎面中心线左右对称分布,位于所述第一排列区右侧。
14.在其中一些实施例中,所述第一排列区的宽度为l1,且满足0.1
×
l0≤l1≤0.4
×
l0;所述第二排列区和所述第三排列区的宽度相同均为l2,且满足0.05
×
l0≤l2≤0.2×
l0。
15.在其中一些实施例中,l2<l1≤1.5
×
l2。
16.在其中一些实施例中,单根所述钢丝直径d不小于0.15mm不大于0.2mm;
17.单根所述钢丝破断强力不小于70n不大于150n;
18.各单根所述钢丝互相平行排列,排列密度不小于290epdm不大于350epdm,破断强度不小于30000n/dm。
19.在其中一些实施例中,在所述第一钢丝带束层及所述第二钢丝带束层上下两面用混合橡胶进行均匀覆盖,上下胶片厚度d相同,d的取值范围为不小于0.15mm不大于0.35mm。
20.在其中一些实施例中,对所述第一钢丝带束层及所述第二钢丝带束层进行压延覆胶时,锭子架放线张力控制在不大于250cn不小于600cn。
21.在其中一些实施例中,对所述第一钢丝带束层及所述第二钢丝带束层进行压延覆胶时,用于整理单钢丝平行并按照一定密度进行排列的整经辊和压力辊的凹槽圆弧直径设定为:d+(0.04-0.06)mm。
22.在其中一些实施例中,单根所述钢丝直径d为0.18mm;单根所述钢丝破断强力不小于80n不大于120n;排列密度不小于310epdm不大于330epdm。
23.在其中一些实施例中,d的取值范围为不小于0.15mm不大于0.25mm。
24.在其中一些实施例中,锭子架放线张力控制在不大于400cn不小于500cn。
25.与现有技术相比,本实用新型的有益效果在于:
26.本实用新型提供一种低滚阻轮胎,既能保证轮胎的抗压穿强度,又可实现对带束层的箍紧作用,同时,取消传统乘用车轮胎的冠带层构造,以上两种方式可实现轮胎重量的大幅度降低,实现乘用车轮胎轻量化目的,降低轮胎滚动阻力。
附图说明
27.此处所说明的附图用来提供对本实用新型的进一步理解,构成本实用新型的一部分,本实用新型的示意性实施例及其说明用于解释本实用新型,并不构成对本实用新型的不当限定。在附图中:
28.图1为本实用新型实施例所提供的轮胎断面切片视图;
29.图2为普通乘用车轮胎断面切片视图;
30.附图说明:1、第一钢丝带束层;11、第一钢丝;21、第一排列区;22、第二排列区;23、第三排列区;3、胎面;4、带束层;5、冠带层。
具体实施方式
31.为了使本实用新型的目的、技术方案及优点更加清楚明白,以下结合附图及实施
例,对本实用新型进行描述和说明。应当理解,此处所描述的具体实施例仅仅用以解释本实用新型,并不用于限定本实用新型。基于本实用新型提供的实施例,本领域普通技术人员在没有作出创造性劳动的前提下所获得的所有其他实施例,都属于本实用新型保护的范围。
32.显而易见地,下面描述中的附图仅仅是本实用新型的一些示例或实施例,对于本领域的普通技术人员而言,在不付出创造性劳动的前提下,还可以根据这些附图将本实用新型应用于其他类似情景。此外,还可以理解的是,虽然这种开发过程中所作出的努力可能是复杂并且冗长的,然而对于与本实用新型公开的内容相关的本领域的普通技术人员而言,在本实用新型揭露的技术内容的基础上进行的一些设计,制造或者生产等变更只是常规的技术手段,不应当理解为本实用新型公开的内容不充分。
33.在本实用新型中提及“实施例”意味着,结合实施例描述的特定特征、结构或特性可以包含在本实用新型的至少一个实施例中。在说明书中的各个位置出现该短语并不一定均是指相同的实施例,也不是与其它实施例互斥的独立的或备选的实施例。本领域普通技术人员显式地和隐式地理解的是,本实用新型所描述的实施例在不冲突的情况下,可以与其它实施例相结合。
34.除非另作定义,本实用新型所涉及的技术术语或者科学术语应当为本实用新型所属技术领域内具有一般技能的人士所理解的通常意义。本实用新型所涉及的“一”、“一个”、“一种”、“该”等类似词语并不表示数量限制,可表示单数或复数。本实用新型所涉及的术语“包括”、“包含”、“具有”以及它们任何变形,意图在于覆盖不排他的包含;例如包含了一系列步骤或模块(单元)的过程、方法、系统、产品或设备没有限定于已列出的步骤或单元,而是可以还包括没有列出的步骤或单元,或可以还包括对于这些过程、方法、产品或设备固有的其它步骤或单元。本实用新型所涉及的“连接”、“相连”、“耦接”等类似的词语并非限定于物理的或者机械的连接,而是可以包括电气的连接,不管是直接的还是间接的。本实用新型所涉及的“多个”是指两个或两个以上。“和/或”描述关联对象的关联关系,表示可以存在三种关系,例如,“a和/或b”可以表示:单独存在a,同时存在a和b,单独存在b这三种情况。字符“/”一般表示前后关联对象是一种“或”的关系。本实用新型所涉及的术语“第一”、“第二”等仅仅是区别类似的对象,不代表针对对象的特定排序。
35.本实用新型实施例提供了一种低滚阻轮胎,图1为根据本实用新型实施例的低滚阻轮胎的轮胎断面切片视图。参考图1所示,该低滚阻轮胎带束层4由钢丝及覆胶组成,带束层4由胎里向轮胎接地面依次包括第一钢丝带束层1和第二钢丝带束层4,其中,第一钢丝带束层1包括沿轮胎胎面3横向排列的第一钢丝11,第一钢丝11的长度与轮胎的胎面3宽度l0相同,第二钢丝带束层4采用三段间隔排列且沿轮胎胎面3周向隔缠绕的钢丝组成,第二钢丝带束层4进一步包括第一排列区21,第二排列区22以及第三排列区23,第一排列区21的中心线与轮胎的胎面3中心线重合,第二排列区22位于第一排列区21左侧,左侧边界与第一钢丝带束层1的左侧边界的距离不小于3mm不大于15mm,右侧边界与第一排列区21的中心线的距离不小于0.2
×
l0不大于0.45
×
l0,第三排列区23与第二排列区22沿轮胎的胎面3中心线左右对称分布,位于第一排列区21右侧,右侧边界与第一钢丝带束层1的右侧边界的距离不小于3mm不大于15mm,左侧边界与第一排列区21的中心线的距离不小于0.2
×
l0不大于0.45
×
l0。可选的,第一排列区21的宽度为l1,且满足0.1
×
l0≤l1≤0.4
×
l0;第二排列区22和第三排列区23的宽度相同均为l2,且满足0.05
×
l0≤l2≤0.2×
l0,l2<l1≤1.5
×
l2。
36.现有乘用车轮胎生产制造工艺中,使用的钢丝带束层4结构为至少1根及以上单钢丝构成,或通过多股捻制而成,这样做成的钢丝带束层4,强度高,在进行压延覆胶排线时,单位宽度内,需要较少钢帘线根数即可满足强度要求,但由于其钢丝帘线直径较大,为保证每根钢丝帘线拥有充足的粘合力及附胶率,需要加厚钢丝帘线的压延附胶厚度,对于乘用车轮胎而言,一条轮胎使用的带束层4的面积是固定的,也就意味着轮胎重量会增大。如图2所示,普通乘用车轮胎接地面骨架材料补强构造,由胎里向轮胎接地面依次是聚酯纤维胎体、钢丝带束层4、钢丝带束层4、冠带层5。冠带层5采用尼龙66纤维帘布,在承重受力时,会产生延展拉伸形变,随时间推移,这种形变会逐步变大的趋势,并趋于稳定,这种现象即为轮胎平点的产生过程,轮胎产生平点后,在行驶初期轮胎的均匀性会较差,驾乘舒适度差。该实施例提供的低滚阻轮胎将尼龙66冠带层5取消,改用钢丝帘线,两者相比,钢丝帘线具有更好的尺寸稳定性,受力后,更不容易产生平点,即驾乘会更加舒适。冠带层5的取消使轮胎重量得到大幅度降低,普通轮胎205/55r16型号,冠带层5重量约0.5kg,单胎重量约8.7kg,取消冠带层5结构,可实现降重约6%,轮胎重量越轻,轮胎的滚动阻力值越低。另外,为了保证轮胎的整体性能,轮胎胎面3接地部位骨架材料由三层(钢丝带束层4、钢丝带束层4、冠带层5)优化为两层(第一钢丝带束层1和第二钢丝带束层4),其中第一钢丝带束层1采用横向排列的钢丝帘线,第二钢丝带束层4采用三段间隔且周向隔缠绕的钢丝帘线,并具体限定了第一钢丝带束层1和第二钢丝带束层4的钢丝排列方式,这种设计既可以保证轮胎抵抗地面带来的冲击力,满足国标对轮胎强度性能的要求,又可以箍紧第一层带束层4(轮胎在高速行走时会产生离心力),满足国标对轮胎高速、耐久性能的要求,同时达到了轮胎轻量化,降低轮胎滚动阻力的目的。
37.可选的,第一排列区21,第二排列区22以及第三排列区23每段的宽度不大于100mm不小于10mm,优选的,每段的宽度不大于80mm,不小于20mm。
38.在其中一些实施例中,单根钢丝直径d不小于0.15mm不大于0.2mm,直径较细,压延附胶厚度则更薄,带束层4更轻,乘用车轮胎更轻,有利于降低轮胎滚动助力,降低车辆油耗;单根钢丝破断强力不小于70n不大于150n;各单根钢丝互相平行排列,排列密度不小于290epdm不大于350epdm,其中,epdm即垂直于钢丝平行方向,10cm宽度内钢丝根数,破断强度不小于30000n/dm。为平衡重量与强度,避免单钢丝帘布压延大卷在后工序加工中出现异常,优选的,单根钢丝直径d为0.18mm;单根钢丝破断强力不小于80n不大于120n;优化单钢丝带束层4排列密度,确保满足整体强度的同时,降低单钢丝带束层4重量,排列密度不小于310epdm不大于330epdm。
39.可选的,在第一钢丝带束层1及第二钢丝带束层4上下两面用混合橡胶进行均匀覆盖,上下胶片厚度d相同,d的取值范围为不小于0.15mm不大于0.35mm。为实现乘用车轮胎轻量化,对单钢丝带束层4覆胶厚度进行优化,优选的,d的取值范围为不小于0.15mm不大于0.25mm。
40.在其中一些实施例中,对第一钢丝带束层1及第二钢丝带束层4进行压延覆胶时,锭子架放线张力控制在不大于250cn不小于600cn。为保证单钢丝带束层4压延工艺质量,避免出现并线或稀疏不均的问题,优选的,锭子架放线张力控制在不大于400cn不小于500cn。
41.在其中一些实施例中,对第一钢丝带束层1及第二钢丝带束层4进行压延覆胶时,用于整理单钢丝平行并按照一定密度进行排列的整经辊和压力辊的凹槽圆弧直径设定为:
d+(0.04-0.06)mm。为确保单钢丝带束层4在压延附胶时的稳定,避免在压延生产过程中发生跳线、并线以及表面镀铜刮伤等工艺质量问题,优选的,凹槽圆弧直径设定为:d+0.05mm。
42.可选的,钢丝材质为特高强(ut),相比于普通强度(nt)、高强度(ht)、超高强度(st)、巨高强度(mt),该钢丝带束层4具有更高的强度及耐疲劳性能。另外,覆胶包含(以生胶为100重量份计):天然橡胶65-95份;环氧率为5%-15%的环氧化天然橡胶5-35份;n326炭黑25-50份;高分散白炭黑5-25份;n-(β-氨乙基)-γ-氨丙基三乙氧基硅烷0.5-2.5份;间苯二甲酰肼0.2-1份;不含有癸酸钴或硼酰化钴等钴盐。单钢丝带束层4覆胶门尼粘度ml(1+4)@100℃为80-90,硫化胶动态损耗tanδ@70℃不大于0.09。e’@70℃不小于15mpa。
43.传统带束层4覆胶在混炼胶中加入钴盐改善与钢丝的粘合,但此种方案钴利用率低,耐老化性能差,动态损耗高;本方案将钴加入钢丝镀层,并取消带束层4覆胶中的钴盐,同时利用环氧化天然橡胶-白炭黑-氨基偶联剂体系及天然橡胶-炭黑-间苯二甲酰肼体系进一步改善粘合性能并兼顾耐老化性能及降低胶料滞后损失,有利于降低轮胎滚动阻力。
44.上述带束层4覆胶配方方案相较传统方案主要缺点在于胶料门尼粘度较高,不利于对钢丝帘线的浸润,因此无法在多股钢丝带束层4中使用,因此该该带束层4覆胶配方方案是一种单钢丝带束层4专用配方,具有极低的滞后损失,有利于降低轮胎滚动阻力。
45.实施例1
46.选取单钢丝直径(d)不小于0.15mm,不大于0.20mm,在本实例具体实施中,经过测算及匹配轮胎生产制造工艺过程,优化选取直径(d)为0.18mm的单钢丝作为带束层4骨架材料,该直径(d)下,具有优化的强度、成本及工艺过程。
47.目前,轮胎带束层4用钢丝帘线种类较多,根据强度大小,有小到大分为:普通强度(nt)、高强度(ht)、超高强度(st)、特高强度(ut)、巨高强度(mt),为实现带束层4轻量化,同时兼顾钢丝的耐屈挠及疲劳性能,本发明单钢丝选用特高强度(ut)材质。
48.单钢丝破断力优选不小于80n,不大于120n,依据上述材质(特高强度ut)、直径(d取0.18mm),优化选用带束层4选用的单钢丝破断力取值为95n
±
10n。
49.为保证带束层4帘线单位宽度内强度不小于30000n/dm,根据已确立的单钢丝破断强度,优化选取320根/dm的压延排列密度,带束层4帘线单位宽度内强度约30400n/dm,符合带束层4帘线单位宽度内强度不小于30000n/dm的要求。
50.对于带束层4上下附胶厚度,优化选取设定为0.2mm,这样既能保证橡胶与单钢丝粘合力,又不会因过渡交联而导致早起损坏。
51.压延附胶过程中,牵引张力进行优化控制在(450
±
20)cn,已确保钢丝有足够的牵引力,而不至于发生跳线、并线等质量问题,且不能过大而导致钢丝断裂。
52.为实现钢丝有序排列,在压延过程中,需要用的排线工装:整经辊、压力辊,为确保单钢丝在压延附胶时的稳定,避免在压延生产过程中发生跳线、并线以及表面镀铜刮伤等工艺质量问题,优化上述设备工装凹槽圆弧直径为单钢丝直径(d)+0.05mm,即0.23mm。
53.该实例选用205/55r16规格型号轮胎,基于以上技术参数的成品试验轮胎(0.18ut),与普通轮胎产品(0.35ut),进行室内外机床对比测试结果如表1。
54.表1测试结果
[0055][0056]
通过成品轮胎室内测算数据对比可以看出,本发明做出的成品轮胎的滚动阻力优于正常轮胎,且性能满足法规标准要求。
[0057]
以上所述实施例的各技术特征可以进行任意的组合,为使描述简洁,未对上述实施例中的各个技术特征所有可能的组合都进行描述,然而,只要这些技术特征的组合不存在矛盾,都应当认为是本说明书记载的范围。
[0058]
以上所述实施例仅表达了本实用新型的几种实施方式,其描述较为具体和详细,但并不能因此而理解为对实用新型专利范围的限制。应当指出的是,对于本领域的普通技术人员来说,在不脱离本实用新型构思的前提下,还可以做出若干变形和改进,这些都属于本实用新型的保护范围。因此,本实用新型专利的保护范围应以所附权利要求为准。