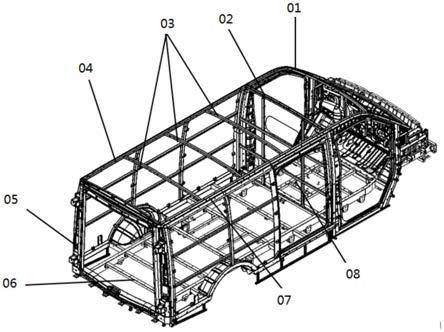
1.本实用新型属于汽车技术领域,更具体地说,涉及一种新能源物流车骨架结构。
背景技术:
2.电动汽车作为一种新能源汽车,与传统汽车相比,具有节能环保的优势,因此,电动汽车越来越成为汽车领域研究的热点。然而,在电动汽车领域,电动汽车蓄电池续航里程有限为普遍存在的难题,这一点限制了电动汽车的推广应用。现有的车身骨架多为钢结构,其自身重量大,不利于电动汽车轻量化,也不利于有效延长电动汽车续航里程的问题;另一方面,车身骨架连接大多采用冲压钢板焊接方式,存在装配及维护成本较高,生产周期长的问题。
技术实现要素:
3.本实用新型的目的是解决现有技术存在的问题,提供一种结构简单,实现轻量化,节省装配及维修成本的新能源车b柱结构。
4.为了实现上述目的,本实用新型采取的技术方案为:所提供的这种新能源物流车骨架结构,其特征在于:包括下车身骨架,布置在两侧的侧围骨架,所述侧围骨架上方设有顶盖骨架,所述侧围骨架的前端和后端分别布置有前舱骨架和后背门框骨架,在所述侧围骨架之间靠近前舱一侧设有隔板骨架,所述侧围骨架、顶盖骨架、后背门框骨架及隔板骨架均由中空结构的铝材制成。
5.为使上述技术方案更加详尽和具体,本实用新型还提供以下更进一步的优选技术方案,以获得满意的实用效果:
6.所述下车身骨架包括两侧的左纵梁和右纵梁,左右纵梁之间设有车架横梁,所述左右纵梁的两侧设有边梁。
7.所述左右纵梁的前方设有前防撞梁。
8.所述侧围骨架包括前侧围骨架和后侧围骨架。
9.所述前侧围骨架由a柱、上边梁、b柱及前门门槛梁首尾相连组成。
10.所述后背门框骨架包括后背门上横梁和后背门门槛梁、后背门上横梁和后背门门槛梁之间设有后背门止口梁。
11.所述隔板骨架包括隔板本体及设于所述隔板本体上的隔板横梁和隔板纵梁。
12.本实用新型与现有技术相比,具有以下优点:本实用新型新能源物流车骨架结构,结构简单,实现轻量化,节省装配及维修成本,具有较强的实用性和较好的应用前景。
附图说明
13.下面对本说明书的附图所表达的内容及图中的标记作简要说明:
14.图1为本实用新型本发明物流车身骨架结构的结构示意图;
15.图2为本实用新型物流车身骨架左侧围结构的结构示意图;
16.图3为本实用新型物流车身骨架右侧围骨架的结构示意图;
17.图4为本实用新型物流车身骨架的下车身骨架结构示意图;
18.图5为本实用新型物流车身骨架结构的后侧围骨架结构示意图;
19.图6为本实用新型物流车身骨架结构的隔板骨架结构示意图。
20.图中标记为:
21.01前顶横梁;02第二横梁;03货箱顶横梁;04左侧围骨架;05后背门框骨架;06下车身骨架;07右侧围骨架;08隔板骨架;1左a柱;2左上边梁;3左b柱;4货箱第一横梁;5货箱上边梁;6货箱第二横梁;7货箱第三横梁;8货箱后边梁;9货箱下后横梁;10货箱右侧第二纵梁;11货箱第一纵梁;12货箱下前横梁;13左前门门槛梁;14左侧围前端总成;15右a柱;16右上边梁;17右b柱;18取货门铰链安装梁;19取货门后边梁;20货箱右第一纵梁;21货箱右后纵梁;22货箱右前下横梁;23取货门下横梁;24车架第三边梁;25货箱第二边梁;26左纵梁;27货箱第一边梁;28前防撞梁;29右纵梁;30车架横梁;31后背门上横梁;32后背门上止口;33后顶盖连接板;34后背门铰链安装板;35后背门门槛梁;36后背门下止口;37后背门止口梁;38隔板第一纵梁;39隔板横梁;40隔板下连接板;41隔板下纵梁;42隔板中纵梁。
具体实施方式
22.下面对照附图,通过对实施例的描述,对本实用新型的具体实施方式作进一步详细的说明。
23.在本实用新型的描述中,需要说明的是,术语“上”、“下”、“前”、“后”、“左”、“右”、“竖直”、“内”、“外”等指示的方位或位置关系为基于附图所示的方位或位置关系,仅是为了便于描述本发明和简化描述,而不是指示或暗示所指的装置或元件必须具有特定的方位、以特定的方位构造和操作,因此不能理解为对本发明的限制。
24.本实用新型提供一种新能源物流车身骨架结构,一方面解决了现有技术中车身骨架结构由于自身重量大,而导致汽车在行驶过程中消耗大量能源,不利于有效延长电动汽车续航里程的问题;另一方面解决了现有技术中车身骨架结构由于采用冲压钢板焊接方式,而导致装配及维护成本较高,生产周期长的问题。
25.本实用新型中,车身骨架结构,包括下车身骨架06、前舱骨架、侧围骨架及后背门框骨架05、隔板骨架08、顶盖骨架。侧围骨架下边梁通过螺栓连接接于下车身骨架06,侧围骨架通过上边梁焊接于顶横梁,侧围骨架、隔板骨架08、后背门框骨架05及顶盖骨架均由中空结构的铝材制成;侧围骨架为框形结构,按前后方向分为驾驶室前侧围骨架和后侧围骨架;侧围骨架设置于顶盖骨架结构的两个相对侧,分别为左侧围骨架04和右侧围骨架07,隔板骨架08设置于左右侧围框形结构的中间位置,顶盖骨架的两侧分别连接于左右侧围骨架,两个侧围骨架呈平行设置,且均垂直于隔板骨架08。
26.侧围骨架、顶盖骨架、隔板骨架及后围骨架均采用中空结构的铝材制成,有利于汽车减轻自重,满足整车轻量化的需求,进而有效地延长电动汽车续航里程,同时,避免了自身重量大的汽车在行驶过程中需要消耗大量能源的情况,进而达到节能环保的目的。
27.本实施例提供一种车身骨架结构,如图1所示,该车身骨架结构包括:前顶横梁01;第二横梁02;货箱顶横梁03;左侧围骨架04;后背门框骨架05;下车身骨架06;右侧围骨架07;隔板总成08,且左右侧围骨架、后背门框骨架05及隔板骨架08均由中空结构的铝材制
成。通过将车身骨架结构划分为左侧围骨架04、右侧围骨架07、后背门框骨架05及下车身骨架06和顶盖骨架,与现有技术采用焊接相比,左右侧围和后背门框与车架之间可采用螺接和铆接的连接方式,装配工艺简单,缩短生产周期,进而降低装配及维护成本。另外,采用中空结构的铝材制成,满足整车轻量化的需求,进而有效地延长电动汽车续航里程。同时有利于汽车减轻自重,避免自身重量大的汽车在行驶过程中需要消耗大量能源的情况,进而达到节能环保的目的。
28.如图2所示,上述左侧围骨架总成04,包括左a柱1;左上边梁2;左b柱3;货箱第一横梁4;货箱上边梁5;货箱第二横梁6;货箱第三横梁7;货箱后边梁8;货箱下后横梁9;货箱右侧第二纵梁10;货箱第一纵梁11;货箱下前横梁12;左前门门槛梁13;左侧围前端总成14。左a柱1和左b柱3、左上边梁2、左前门门槛梁13组成前侧围骨架,与左侧围前端总成14拼接构成前侧围总成,后侧围骨架由两个货箱第一横梁4和货箱上边梁5、两个货箱第二横梁6、两个货箱第三横梁7、货箱后边梁8、货箱下后横梁9、货箱右侧第二纵梁10、货箱第一纵梁11、货箱下前横梁12等拼焊而成,保证了侧围骨架04的强度,增强了碰撞安全性能,避免在碰撞中驾驶员受到较大伤害的情况。
29.如图3所示,上述右侧围骨架07包括右a柱15;右上边梁16;右b柱17;取货门铰链安装梁18;取货门后边梁19;货箱右第一纵梁20;货箱右后纵梁21;货箱右前下横梁22;取货门下横梁23;车架第三边梁24;货箱第二边梁25;左纵梁26;货箱第一边梁27。右a柱15和右b柱17均与右上边梁16连接,右侧的后侧围骨架由取货门铰链安装梁18、取货门后边梁19、两个货箱第一横梁20和货箱上边梁5、两个货箱第三横梁7、货箱后边梁5、货箱下后横梁9、货箱右侧第二纵梁21、货箱第一纵梁10、货箱下前横梁22等拼焊而成,保证了侧围骨架07的强度,增强了碰撞安全性能,避免在碰撞中驾驶员受到较大伤害的情况。
30.如图6所示,上述下车身骨架06包括车架第三边梁24;车架第二边梁25;左纵梁26;车架第一边梁27;前防撞梁28;右纵梁29;车架横梁30;车架零部件材料均为方形钢q235,左纵梁26、右纵梁29和横梁30组成车架后总成结构,以提高其位置度,以便和骨架装配。
31.如图5所示,上述后背门框总成05包括后背门上横梁31、后背门上止口32、后顶盖连接板33、后背门铰链安装板34、后背门门槛梁35、后背门下止口36、后背门止口梁37。同时,后背门框骨架05分别连接于侧围骨架。后背门上横梁31与后背门上止口32连接、后背门门槛梁35与后背门止口梁37连接,使得整体货箱骨架的强度更高。
32.如图6所示,上述隔板骨架08包括隔板第一纵梁38;隔板横梁39;隔板下连接板40;隔板下纵梁41;隔板中纵梁42;同时,两个横梁39呈平行间隔设置于隔板本体上,两个第一纵梁38呈平行间隔设置于隔板本体上,第一纵梁38与横梁39呈垂直分布,隔板中纵梁42两端连接于横梁39。另外,两个隔板下纵梁与隔板下连接板40铆接。两个第一纵梁和横梁形成驾驶员观察窗,通过观察窗可以查看货箱的情况,便于及时检查、监护及管理。
33.本实用新型新能源物流车骨架结构,结构简单,实现轻量化,节省装配及维修成本,具有较强的实用性和较好的应用前景。
34.在本实用新型的描述中,需要说明的是,除非另有明确的规定和限定,术语“安装”、“相连”、“连接”应做广义理解,例如,可以是固定连接,也可以是可拆卸连接,或一体地连接;可以是机械连接,也可以是电连接;可以是直接相连,也可以通过中间媒介间接相连。对于本领域的普通技术人员而言,可以具体情况理解上述术语在本发明中的具体含义。
35.上面结合附图对本实用新型进行了示例性描述,但是本实用新型并不受限于上述方式,只要采用本实用新型的方法构思和技术方案进行的各种非实质性的改进或直接应用于其它场合的,均落在本实用新型的保护范围内。