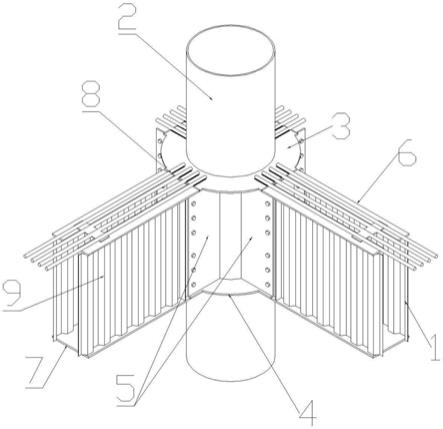
1.本实用新型涉及建筑、民用工程技术领域,具体涉及一种甲壳梁与各类钢柱的连接结构。
背景技术:
2.传统的钢柱与钢梁进行连接,大多采用栓焊法,即翼缘采用对接焊缝连接,腹板开孔后,用高强螺栓进行连接。所有剪力由连接板摩擦面在高强螺栓预拉力下压紧产生的摩擦力承担,所有弯矩由翼缘对接焊缝和腹板螺栓群共同承担。尤其是当腹板高度大的时候,腹板为了避免屈曲,腹板的厚度也必须很大,这时候,腹板惯性矩在整个截面中所占比例很大,腹板按惯性矩占比所分担的弯矩就很大,腹板螺栓群为了承担这部分弯矩,这个节点的螺栓数量就非常多,远超梁端抗剪所需的高强螺栓。例如一个12米*12米柱网,楼面荷载2吨/平米的物流仓库,一个主框架梁与柱连接的节点,就多达150颗m22的10.9级高强螺栓。仅螺栓部分的造价分摊到建筑面积,就超过60元/平米。
技术实现要素:
3.本实用新型的目的在于提出一种各板件分工明确,受力单一的甲壳梁与各类钢柱的连接结构,从而可以释放腹板弯矩的双腹板连接节点,以解决背景技术中传统节点中存在的螺栓孔数量多,对位困难,施工繁琐,浪费人力物力,经济性差的问题。
4.为达到上述目的,本实用新型提出一种甲壳梁与各类钢柱的连接结构,包括甲壳梁、钢柱、上环板、下环板和柱端双腹板;
5.所述钢柱的外周设有所述上环板和所述下环板;所述柱端双腹板设于所述上环板与所述下环板之间;
6.所述甲壳梁上翼缘的端部与所述上环板通过对接焊缝相连接,所述甲壳梁下翼缘的端部与所述下环板通过对接焊缝相连接;所述甲壳梁两侧波纹腹板的端部为梁端平腹板,两侧的所述梁端平腹板分别与所述柱端双腹板通过多个高强螺栓相紧固连接。
7.进一步的,还包括钢筋;所述钢筋顺着所述甲壳梁的长度方向,铺设于所述上环板和所述甲壳梁上翼缘表面,所述钢筋通过喇叭形焊缝与所述上环板焊接固定。
8.进一步的,所述柱端双腹板与所述梁端平腹板通过高强螺栓传递所述甲壳梁的全部剪力。
9.进一步的,所述甲壳梁上翼缘、所述甲壳梁下翼缘、上环板、下环板和所述钢筋,承担所述甲壳梁全部弯矩。
10.进一步的,所述甲壳梁和所述钢柱内均浇筑混凝土,所述柱端双腹板对所述甲壳梁内部的混凝土形成套箍约束。
11.进一步的,所述甲壳梁上翼缘为两块平腹钢板,两块所述平腹钢板之间预留有便于浇筑混凝土的间隙。
12.进一步的,所述钢柱为h形钢柱、箱形钢柱、圆形钢柱、矩形钢管混凝土柱或者圆形
钢管混凝土柱。
13.与现有技术相比,本实用新型的优势之处在于:
14.1、本实用新型甲壳梁与各类钢柱的连接结构适用于各类钢柱,甲壳梁的腹板为波纹腹板,具有折叠效应,波纹只有剪力,节点处高强螺栓只需传递剪力;上下翼缘和钢筋必须也只能传递全部弯矩,各板件分工明确,受力单一,节点计算与构造简单,施工方便。
15.2、柱端双腹板具有约束效应,里面可以浇筑混凝土,在节点上可以附加钢筋,通过调整钢筋数量,可以减少甲壳梁的种类,实现甲壳梁的构件规格化,简化生产。
16.3、经济性强,由于连接结构导致系统的受力分工明确,使得波纹腹板不用承担弯矩,导致高强螺栓数量为传统钢梁-钢柱框架结构的25~40%。跟相同承载力的传统钢梁-钢柱框架结构相比,这种这节点能够节省30~40%的造价。
17.4、钢筋、甲壳梁上翼缘均焊接于上环板,保证了拉力流在节点的连续;甲壳梁下翼缘与下环板焊接,该压力流在节点处连续;柱端双腹板内灌注混凝土,混凝土的压力流在节点处连续,拉压力流的连续,形成力偶,保证节点抗弯承载能力可靠,梁端平腹板通过高强螺栓和柱端双腹板把梁端剪力传给柱,安全可靠。
附图说明
18.图1为本实用新型实施例中甲壳梁与各类钢柱的连接结构的立体图;
19.图2为本实用新型实施例中甲壳梁与各类钢柱的连接结构的爆炸图;
20.图3为本实用新型实施例中甲壳梁与各类钢柱内部浇筑完混凝土后的立体图。
具体实施方式
21.为使本实用新型的目的、技术方案和优点更加清楚,下面将对本实用新型的技术方案作进一步地说明。
22.如图1和图2所示,本实用新型提出一种甲壳梁与各类钢柱2的连接结构,包括甲壳梁1、钢柱2、上环板3、下环板4和柱端双腹板5;
23.钢柱2的外周设有上环板3和下环板4;柱端双腹板5设于上环板3与下环板4之间;
24.甲壳梁上翼缘6的端部与上环板3通过对接焊缝相连接,甲壳梁下翼缘7的端部与下环板4通过对接焊缝相连接;甲壳梁1两侧波纹腹板9的端部为梁端平腹板10,两侧的梁端平腹板10分别与柱端双腹板5通过多个高强螺栓相紧固连接,柱端双腹板5与梁端平腹板10通过高强螺栓传递甲壳梁1的全部剪力到钢柱2,使得整体结构安全可靠。
25.在本实施例中,还包括钢筋8;钢筋8顺着甲壳梁1的长度方向,铺设于上环板3和甲壳梁上翼缘6表面,钢筋8通过喇叭形焊缝与上环板3焊接固定。甲壳梁上翼缘、甲壳梁下翼缘、上环板3、下环板4和钢筋8,承担甲壳梁全部弯矩,通过调整钢筋8数量,可以减少甲壳梁1的种类,实现甲壳梁1的构件规格化,简化生产。
26.如图3所示,甲壳梁1和钢柱2内均浇筑混凝土,柱端双腹板5对甲壳梁1内部的混凝土形成套箍约束。甲壳梁上翼缘为两块平腹钢板,两块平腹钢板之间预留有便于浇筑混凝土的间隙。
27.甲壳梁上翼缘6、钢筋8、甲壳梁下翼缘7构成一组合截面,在与钢柱2的连接节点处,钢筋8、甲壳梁上翼缘6均焊接于上环板3表面,保证了拉力流在节点的连续;甲壳梁下翼
缘7与下环板4焊接,该压力流在节点处连续;双腹板内灌注混凝土,混凝土的压力流在节点处连续,拉压力流的连续,形成力偶,保证节点抗弯承载能力可靠。
28.钢柱2的形状不做限定,可以为h形钢柱2、箱形钢柱2、圆形钢柱2、矩形钢管混凝土柱或者圆形钢管混凝土柱,在本实施例中为圆形钢管混凝土柱。
29.经济性方面,在本实用新型中,上环板3,伸出钢柱2截面之外,跟甲壳梁上翼缘6采取上述方式完成连接后,在外伸的上环板3上,还可以焊接甲壳梁1钢筋8。当梁内浇筑了混凝土之后,该节点形成钢外壳、里面为钢筋8混凝土的组合结构。里面的钢筋8混凝土梁,是不需要模板和脚手架就能施工完成的,而且能够分担的荷载占比很大(根据配筋情况而变化)。计算表明,如果里面的钢筋8混凝土造价、和外面的钢梁外壳造价占比各50%的话,那么,里面的钢筋8混凝土梁可以承担70%的节点负弯矩。波纹腹板9由于不承担弯矩,高强螺栓数量,只有传统钢梁-钢柱2框架结构的25~40%,这意味着,这种做法具有非常良好的经济性。跟相同承载力的传统钢梁-钢柱2框架结构相比,这种这节点大概能够节省30~40%的造价。采用该种甲壳梁1与钢柱2组合成的框架,同时采用这种新型连接做法,与相同条件的传统钢梁-钢柱2框架结构相比,整体造价可以节省10~20%
30.上述仅为本实用新型的优选实施例而已,并不对本实用新型起到任何限制作用。任何所属技术领域的技术人员,在不脱离本实用新型的技术方案的范围内,对本实用新型揭露的技术方案和技术内容做任何形式的等同替换或修改等变动,均属未脱离本实用新型的技术方案的内容,仍属于本实用新型的保护范围之内。