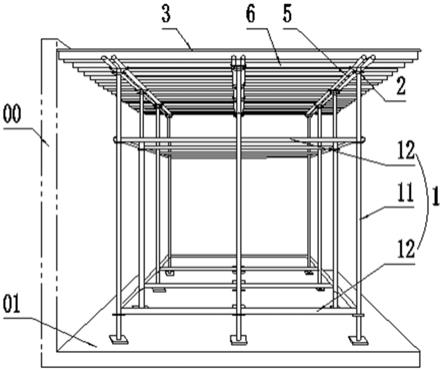
1.本发明属于建筑施工技术领域,尤其涉及一种绿色支模体系施工工法。
背景技术:
2.为实现社会的可持续发展,工业、建筑、交通等领域均在不断深入推进低碳转型。目前,建筑行业碳排放量主要集中在建筑材料的生产、运输、施工过程中,传统的木模板支撑体系标准化程度低,非标准模板不能循环利用,存在严重的木材浪费现象。因此,需要研发一种更绿色环保的新型支模体系,能够实现循环利用,以减少木材使用量。
技术实现要素:
3.本发明的目的是提供一种绿色支模体系施工工法,旨在解决现有技术中传统木模板支撑体系中模板不具备通用性,导致木材浪费严重的技术问题。
4.为解决上述技术问题,本发明所采取的技术方案是:一种绿色支模体系施工工法,包括以下步骤:s1:施工前准备:设计方案、加工模板,预先排布支模架体及模板位置、测量放线;s2:架设支模体系;首先搭设支模架体,在支模架体的顶部安装早拆柱头及龙骨,在龙骨上方间隔铺设并固定模板及板带,板带对应铺设在支模架体的立杆的上方,模板铺设在相邻立杆之间上方;s3:绑扎钢筋:在模板及板带上弹线,绑扎钢筋网;s4:浇筑混凝土:预先浇筑楼梯间后浇筑墙柱,最后浇筑模板内部形成楼板;s5:第一次拆模:拆除龙骨、模板及支模架体的横杆;s6:第二次拆模:拆除支模架体的立杆、早拆柱头及板带。
5.优选的,所述支模体系包括支模架体、早拆柱头、龙骨、模板及板带,所述支模架体由横杆及立杆搭设而成,所述早拆柱头间隔设置于支模架体的立杆顶部,所述龙骨架设于支撑柱头的顶部,所述模板及板带间隔铺设在龙骨的上方。
6.优选的,所述早拆柱头包括支撑杆、升降翼板及调节螺母,所述支撑杆为带有外螺纹的圆柱体,所述支撑杆的下端能够与立杆的顶部内孔螺纹连接;所述支撑杆的顶部设有用于校核标高的顶板,所述升降翼板及调节螺母的中部均设有用于与支撑杆配合的内螺纹;所述调节螺母设置于升降翼板的下方。
7.优选的,所述调节螺母为两个,上方调节螺母与升降翼板的下端抵接,下方调节螺母的下端与立杆的上端面抵接。
8.优选的,所述调节螺母的外圆上设有用于标定高度的标定块,所述标定块三角形,所述标定块的顶部平齐;每个调节螺母的外圆上设有两个标定块,且两个标定块对称设置于调节螺母的两侧。
9.优选的,所述升降翼板包括套筒、承托板和筋板,所述套筒能够与立杆螺纹配合,所述承托板设置于套筒的顶部,所述承托板为矩形、且在承托板的两侧对称设有用于对主
龙骨限位的凸檐,所述筋板对称设置于套筒的两侧,所述筋板的一侧与套筒外圆固定、顶部与承托板的下表面固定。
10.优选的,所述龙骨包括主龙骨和次龙骨,所述主龙骨并列设置于升降翼板上,所述主龙骨为钢管、且主龙骨两两成对设置于升降翼板的承托板上;所述次龙骨铺设在主龙骨的上方,所述次龙骨垂直主龙骨铺设。
11.优选的,所述次龙骨为长条方木,所述方木的横截面尺寸为40*90mm;所述钢管直径为48.3mm;所述模板及板带均为双面覆膜的木胶合板,所述模板的尺寸为1830*915*15mm。
12.优选的,所述步骤s1中,预先在楼板上弹设支模架体的横杆位置,横杆交叉的位置即为立杆位置,并喷漆标注立杆点位。
13.优选的,在步骤s4中,混凝土浇筑按照设计要求测量混凝土坍落度并留置同养、标养试块;步骤s5中,当混凝土浇筑完成后强度达到设计强度的50%或75%后,进行第一次拆模。
14.采用上述技术方案所产生的有益效果在于: 与现有技术相比,本发明通过搭设尺寸规范化、模板标准化,提高支模体系的搭设效率及稳固性,标准模板周转快,投入少,只需配备1层用量可快速周边至上层,避免周转材料闲置,减少了材料的使用,有利于绿色施工、保护环境;该支模体系是通过在立杆顶部增加顶板早拆柱头,方便模板提前拆除,减少了模板及周转材料使用量。本发明适用于普通多层、高层现浇混凝土结构建筑物,尤其适用于单层面积较大,层数较少的地下车库、厂房等工程,亦可应用在后浇带支模。
附图说明
15.下面结合附图和具体实施方式对本发明作进一步详细的说明。
16.图1是本发明实施例中绿色支模体系的结构示意图;图2是本发明实施例中模板及板带的平面布置图;图3是图1中早拆柱头的结构示意图;图中:00-墙体,01-楼板;1-支模架体,11-立杆,12-横杆;2-早拆柱头,21-支撑杆,22-升降翼板,221-套筒,222-承托板,223-筋板;23-调节螺母,24-顶板,25-标定块;3-模板,4-板带,5-主龙骨,6-次龙骨。
具体实施方式
17.下面结合本发明实施例中的附图,对本发明实施例中的技术方案进行清楚、完整地描述,显然,所描述的实施例仅仅是本发明的一部分实施例,而不是全部的实施例。基于本发明中的实施例,本领域普通技术人员在没有做出创造性劳动前提下所获得的所有其他实施例,都属于本发明保护的范围。
18.本发明提供的一种绿色支模体系施工工法,包括以下步骤:s1:施工前准备:设计方案、加工模板,预先排布支模架体及模板位置、测量放线。预先在楼板上弹设支模架体1的横杆12位置,横杆12交叉的位置即为立杆11位置,并喷漆标注立杆点位。
19.s2:架设支模体系:如图1所示,首先搭设支模架体1,在支模架体1的顶部安装早拆
柱头2及龙骨,在龙骨上方间隔铺设并固定模板3及板带4,板带4对应铺设在支模架体1的立杆11的上方,模板3铺设在相邻立杆11之间上方,如图2所示。
20.如图1所示,所述支模体系包括支模架体1、早拆柱头2、龙骨、模板3及板带4,所述支模架体1由横杆12及立杆11搭设而成,所述早拆柱头2间隔设置于支模架体1的立杆11顶部,所述龙骨架设于支撑柱头2的顶部,所述模板3及板带4间隔铺设在龙骨的上方。
21.s3:绑扎钢筋:在模板3及板带4上弹线,绑扎钢筋网;模板拼缝处采用30宽
×
15厚海绵条胶粘。
22.s4:浇筑混凝土:预先浇筑楼梯间后浇筑墙柱,最后浇筑模板内部形成楼板;混凝土浇筑按照设计要求测量混凝土坍落度并留置同养、标养试块。
23.s5:第一次拆模:拆除龙骨、模板3及支模架体1的横杆12。当混凝土浇筑完成后强度达到设计强度的50%或75%后,进行第一次拆模。
24.s6:第二次拆模:拆除支模架体1的立杆11、早拆柱头2及板带4。
25.然后再将拆除后的材料周转至上一层,达到循环使用的目的。
26.本发明适用于普通多层、高层现浇混凝土结构建筑物,尤其适用于单层面积较大,层数较少的地下车库、厂房等工程,亦可用在后浇带支模。
27.在本发明的一个具体实施例中,如图3所示,所述早拆柱头2包括支撑杆21、升降翼板22及调节螺母23,所述支撑杆21为带有外螺纹的圆柱体,所述支撑杆21的下端能够与立杆11的顶部内孔螺纹连接;所述支撑杆21的顶部设有用于校核标高的顶板24,所述升降翼板22及调节螺母23的中部均设有用于与支撑杆21配合的内螺纹;所述调节螺母23设置于升降翼板22的下方。其中,所述调节螺母23为两个,上方调节螺母23与升降翼板22的下端抵接,下方调节螺母23的下端与立杆11的上端面抵接。利用两个调节螺母能够对升降翼板进行定位。
28.为了方便在施工过程中对标高进行复核标定,所述调节螺母23的外圆上设有用于标定高度的标定块25,所述标定块25三角形,所述标定块25的顶部平齐;每个调节螺母23的外圆上设有两个标定块25,且两个标定块25对称设置于调节螺母23的两侧。
29.进一步优化上述技术方案,如图3所示,所述升降翼板22包括套筒221、承托板222和筋板223,所述套筒221能够与立杆11螺纹配合,所述承托板222设置于套筒221的顶部,所述承托板222为矩形、且在承托板222的两侧对称设有用于对主龙骨5限位的凸檐224,所述筋板223对称设置于套筒221的两侧,所述筋板223的一侧与套筒221外圆固定、顶部与承托板222的下表面固定。其中,所述龙骨包括主龙骨5和次龙骨6,所述主龙骨5并列设置于升降翼板22上,所述主龙骨5为钢管、且主龙骨5两两成对设置于升降翼板22的承托板222上;所述次龙骨6铺设在主龙骨5的上方,所述次龙骨6垂直主龙骨5铺设。
30.具体制作时,所述次龙骨6为长条方木,所述方木的横截面尺寸为40*90mm;所述钢管直径为48.3mm;所述模板3及板带4均为双面覆膜的木胶合板,所述模板3的尺寸为1830*915*15mm。
31.以下为一个具体实施例中,绿色支模体系的施工内容:一、模板及支模架体的排布深化设计:1、施工前技术人员根据图纸对标准层内各房间进行模板配模、架体排布等深化设计。
32.2、对楼层各个户型、房间进行编号,模板配模时尽量采用标准模板,减少模板的规格,对统一规格的模板进行统一编号,最后出具模板配模平面布置图及用料清单。
33.3、根据模板排布,深化架体排布,绘制架体排布平面布置图及各房间施工(支模)大样图,最后出具总材料用量清单。
34.4、以a户型客厅为示意,架体排布及模板排布如图1、2所示。
35.二、模板加工:1、模板集中加工前应对班组进行详细交底、发放集中加工模板下料单,班组应严格按照模板深化详图和构造要求制作。
36.2、模板加工采用集中加工,加工车间尺寸根据项目尺寸确定,一般为8m*6m*5m。
37.3、模板切割采用精密电锯加工,严禁现场手持电锯切割,加工完成后模板按照编号打包,集中吊运。
38.三、测量放线:1、由防线员放出纵横主控轴线,施工员配合劳务班组墙柱轴线、边线、200控制线。
39.2、根据墙柱边线及架体排布深化图在楼板上弹设架体水平横杆位置线,架体水平横杆交叉位置即为立杆位置,用自喷漆喷φ50mm点为站杆点。喷漆保持清晰一致,严禁污染楼板其他位置或钢筋。
40.3、放线完成后,由施工员报质检员、技术员对测量放线及架体位置进行复核。
41.四、铺设模板:1、按支模体系深化设计图安装早拆柱头,布置主龙骨之前,将所有早拆柱头的顶板、升降翼板整至设计标高并紧固调节螺母固定牢固。
42.2、将φ48.3mm*3.0mm主龙骨放置于升降翼板内,再次根据顶板标高校核,通过升降翼板调整主龙骨高度,钢管两端头超出距墙第一排立杆>250mm ;双钢管长度正常可为短跨净长度-200mm。
43.3、主龙骨安装并调整到位后,开始搭配从板的一端向另一端布置40mm*60mm放木, 顺次龙骨方向模板拼缝处全部采用40mmx60mm方木压缝处理,防止漏浆。方木长度尽量根据楼板跨度选择定尺长度,如需搭接,接头设置在主龙骨处,且均超过钢管主龙骨>200mm。
44.4、次龙骨铺设完毕后,将裁切并标注编号的模板吊装至作业面,在保证两侧梁(或墙体)截面尺寸的情况下,按照模板编号,首先对支撑顶板中心定位,一次向两边铺设顶模板, 铺设完一块模板后四角及拼缝处均用铁钉与底部方木钉牢固。模板铺设完成后重新复核版面标高。
45.注意:模板铺设完成后,项目部施工员将竖向板顶及50标高线测设在墙柱竖向钢筋上,并用红漆标识,标高点分布范 围间距≤3m。
46.同时,在铺设模板过程中重点加强模板拼缝的处理,在模板标准板和非标板下边放置一道40mm*90mm方木,并用铁钉进行固定,确保模板拼缝平整、严密,防止砼漏浆。模板拼缝处采用30宽
×
15厚海绵条胶粘,防止漏浆。
47.五、绑扎钢筋:1、模板铺设完成后,清理模板上面杂物,用墨线在模板上弹好主筋、分布筋间距线。扎过程中,注意保护层垫块放置数量和间距应符合相应规范要求。绑扎完成后设置防踩踏措施注意成品保护。
48.六、浇筑混凝土:1、混凝土采用预拌混凝土、采用地泵配合布料机浇筑,混凝土浇筑顺序由远到近,先浇筑楼梯间后浇筑墙柱,最后浇筑顶板,不同标号混凝土要有阻拦措施。
49.2、混凝土浇筑按照要求测量混凝土坍落度并留置同养、标养试块。
50.七、第一次拆模:1、根据该支模体系设计要求当混凝土浇筑完成后强度达到设计强度的50%(<2米);75%(>2,≤8)后方可拆除顶部模板,一般情况下48个小时以后可以拆除顶模。第一次模板拆除前,需要发起拆模申请,评定顶板混凝土等级为本层同养试块强度是否达到50%以上,强度等级达到且经技术负责人审批后可拆除,未达到或未经审批不能私自拆除。
51.2、混凝土达到规定强度后,调节早拆柱头的调节螺母,使升降翼板缓慢下降,主龙骨下降,其上支撑的次龙骨及模板也随之下降,模板同混凝土脱开,实行模板第一次拆除。拆除顶部模板时确保支撑杆保持原样,不得松动。模板的第一次拆除,应确保施工荷载不大于保留支撑的设计承载力;其拆除,应严格执行专项施工方案。拆模后,应对模板进行全面清理上油保养以备用,模板堆放应可靠,防止变形而影响其周转次数。
52.注意:模板清理干净后采用旋转拖把涂刷成品水性脱模剂,涂刷后用干抹布拭擦,以免模板表面刷脱模剂过多。
53.八、第二次拆模:1、第二次模板拆除应符合《混凝土工程施工质量验收规范》gb50204-2015关于底模拆除时的混凝土强度要求,根据留置的拆模试块来确定支撑杆的拆除时间。
54.2、拆除早拆柱头和支撑杆的立杆时,用一只手抓住支撑杆另一只手用锤锤击底部支点,即可拆除支撑杆和早拆柱头。
55.综上所述,本发明具有以下优点:1.通过采用规范化操作及标准化模板形成的支模体系,彻底解决了木模板高效周转施工难题,使工程能够顺利进行,加快了工程进度,减少周转材料、人工的使用,同时工程质量、安全有了更可靠的保证,并取得了较好地社会效益。本发明与传统支模方式比较,材料周转快,投入少,模板及主次龙骨可比常规的投入减少1/3-2/3,同时,降低了材料进出场运输费、租赁费用,有利于降低项目成本。
56.2.通过提前对支模架体进行深化排布,解决了后拆板带与标准板模块支撑问题,各部件搭设尺寸及模板标准化,避免操作工人随意搭设而出现节点不稳定的现象,形成的支模体系安全可靠,受力稳定。使支撑立杆全部排布在后拆板带之下,能实现快速安拆并组装快捷,大大降低了模板拼装的劳动力投入。
57.3.通过标准化设计、模板高效周转,模板可采用集中下料、集中加工得方式,施工过程中能实现快速安拆并组装方便,能提高效率、节省工期。施工中只需要配备1层用量,拆除后能够快速周边至上层,避免周转材料闲置,减少了材料的消耗量,有利于绿色施工、保护环境。本发明体现了工程建设标准化的理念,大大提高了模板的周转使用率,减少了能源和环境破坏。
58.4. 在施工标准化、质量管理及安全文明施工方面取得了良好效果,从而为业主和自身单位树立了良好企业形象,也为该项技术在建筑行业广泛推广提供了最直接的经验借鉴。
59.在上面的描述中阐述了很多具体细节以便于充分理解本发明,但是本发明还可以采用其他不同于在此描述的其它方式来实施,本领域技术人员可以在不违背本发明内涵的情况下做类似推广,因此本发明不受上面公开的具体实施例的限制。