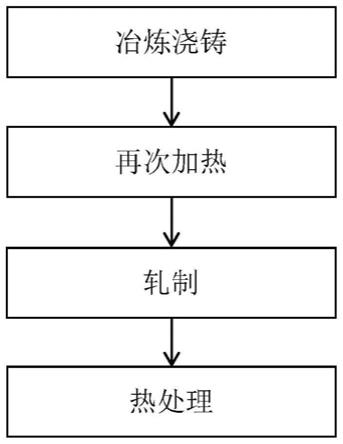
1.本发明涉及金属材料热处理领域,特别是涉及一种耐磨耐腐蚀亚共析钢轨及其生产方法。
背景技术:
2.自1964年7月25日,日本第一条东海道新干线建成通车以来,让世界领略了高速铁路舒适、快捷和高效的魅力及传统运输方式无法比拟的优势,在世界掀起了高速铁路建设的潮流。
3.由于高速铁路主要针对客运列车,尽管列车速度较快但轴重较轻,同时,高速铁路均为无缝连接,对钢轨焊接性能要求严格。因此,目前世界高速铁路均选用含碳量较低的热轧普通碳素钢轨,牌号主要以en260为主。
4.1994年,我国自行建造的第一条准高速铁路――广深线正式运营,设计时速160km;2002年,我国第一条高速铁路――时速200km秦沈客运专线建成,标志着我国进入高速铁路发展时代。从材质来说,我国设计时速350km客运专线均采用u71mn材质、设计时速250km客运专线或客货混运线路主要采用u75v材质。
5.为降低钢轨服役风险,需采用打磨方式去除轨头表层裂纹。高速铁路打磨主要分为理性打磨、保养性打磨和预防性打磨。目前,我国高速铁路除春运、法定节假日等客流高峰时段外,主要采用日间运行,朝发夕至的模式,打磨只能安排在夜间,为打磨的高效连续作业带来障碍;同时,打磨费用昂贵、成本高,随着我国高铁路网的不断完善,打磨作业将疲于奔命,无法为铁路的高效运输提供充足保障。因此,本发明采用接触疲劳性能优良及强韧性匹配更好的亚共析钢轨,对实现高速铁路的长寿化、低成本维护与高效运输具有十分重要的意义。
6.由于国内外铁路建设规模的不断扩大,钢轨的腐蚀问题一直是铁路线路维护中一个不容忽视的问题。钢轨的锈蚀主要发生在沿海及潮湿隧道内,每年国内外因钢轨锈蚀更换费用达数千万美元。国内外对耐蚀钢轨研究主要分为材质耐蚀,如添加耐蚀元素。以及涂覆耐蚀材料在表面,如有机耐蚀物质或是无机耐蚀物质。综合制造成本和线路服役使用分析,采用钢轨材质耐蚀,线路使用效果和经济性较高。
7.随着国内外高铁的发展,以及特殊路段,如川藏线特殊高温潮湿隧道环境铁路用钢轨的特殊需求,对钢轨内在和表面质量提出了更高的要求。因此,耐高温潮湿铁路用钢轨亟需一种耐蚀性能优良,轨头脱碳层深度较浅的钢轨生产方法。
技术实现要素:
8.针对现有技术中存在的不足,本发明的目的在于提供一种耐磨耐腐蚀亚共析钢轨及其生产方法,基于性能优越的亚共析钢轨,采用低碳耐蚀合金,结合微合金化或微合金化+热处理工艺,显著提高钢轨的耐磨性和耐腐蚀性能。
9.为了实现上述目的,本发明提供的技术方案是:
10.一种耐磨耐腐蚀亚共析钢轨,亚共析钢轨化学成分重量百分比为:碳:0.50-0.70%,铜:0.10-0.80%,镍:0.01-0.50%,铬:0.10-0.70%,钒:0.03-0.12%,磷:0.010-0.025%,硫:0.001-0.009%,硅和锰:0.8-2.0%,余量为铁和不可避免的杂质。
11.进一步地,亚共析钢轨还包含重量百分比0.006-0.050%的铌。
12.进一步地,亚共析钢轨还包含重量百分比0.01-0.10%的钼。
13.进一步地,亚共析钢轨还包含重量百分比0.0001-0.001%的硼。
14.进一步地,亚共析钢轨还包含重量百分比0.02-0.05%的稀土元素。
15.一种耐磨耐腐蚀亚共析钢轨的生产方法,包括以下步骤:
16.步骤一:按重量百分比将铜、镍、铬、钒、磷、硫、硅和锰添加到含碳的亚共析钢轨中,冶炼浇铸成亚共析钢轨钢坯,亚共析钢轨钢坯的化学成分重量百分比为:碳:0.50-0.70%,铜:0.10-0.80%,镍:0.01-0.50%,铬:0.10-0.70%,钒:0.03-0.12%,磷:0.010-0.025%,硫:0.001-0.009%,硅和锰:0.8-2.0%,余量为铁和不可避免的杂质;
17.步骤二:再次加热步骤一的亚共析钢轨钢坯,亚共析钢轨钢坯加热温度为1200-1280℃,均热段时间为25-80min;
18.步骤三:轧制步骤二的再次加热后的亚共析钢轨钢坯,生产出亚共析钢轨。
19.进一步地,在步骤一中还按重量百分比添加铌、钼、硼和稀土元素中的一种,铌、钼、硼和稀土元素在亚共析钢轨钢坯中的化学成分重量百分比分别为0.006-0.050%、0.01-0.10%、0.0001-0.001%和0.02-0.05%。
20.进一步地,在步骤三之后采用热轧进行在线热处理,其中热轧态的亚共析钢轨中合金含量在2.5-4.0%之间,合金包括铜、镍、铬、钒、硅和锰。
21.更进一步地,在步骤三之后采用热轧进行在线热处理,其中热轧态的亚共析钢轨中合金含量在2.5-4.0%之间,合金包括铜、镍、铬、钒、硅和锰,以及铌、钼中的一种。
22.更进一步地,在步骤三之后利用轧制余热进行在线热处理,其中开冷温度为650-950℃,强制冷却速率为1-8℃/s,终冷温度为400-600℃。
23.碳(c)是钢中最重要的合金元素,其含量、分布形态对钢的显微组织和力学性能具有重要影响。c元素是奥氏体稳定元素,随着c含量的増加,过冷奥氏体稳定性增大,c曲线的位置向右移动,马氏体相变的临界开始温度降低,贝氏体的孕育期变长。c还是很强的间隙固溶强化元素,能强烈提高钢的强度。
24.硅(si)以置换固溶体形式存在于铁素体或高温奥氏体中,缩小奥氏体相区,si的添加减缓c原子的扩散,阻碍碳化物的析出。提高铁素体和奥氏体的硬度和强度,较锰(mn)、镍(ni)、铬(cr)、钨(w)、铝(al)和钒(v)更强,显著提高钢的弹性极限、屈服强度和屈强比,并提高疲劳性能。
25.锰(mn)能够提高钢的淬透性,改善其热加工性能。mn作为弱碳化物形成元素和奥氏体稳定元素,在基体中对碳化物的扩散阻碍能力较弱,但mn在相界面富集产生溶质“拖曳”及强烈的溶质“类拖曳”效应,会阻碍富碳奥氏体的进一步分解。mn元素扩大奥氏体相区。但mn在钢中扩散速度远小于铁(fe)和c,使过冷奥氏体发生珠光体转变的领先相(fe,mn)3c成核困难,导致相变孕育期加长,从而使钢的c曲线右移。mn还可通过固溶强化来提高铁素体基体的强度,对提高低合金钢的强度是有利的。
26.磷(p)是钢中有害元素之一,优质钢中磷重量百分比含量在0.04%或0.03%以下。
27.硫(s)以硫化物状态存在于钢中,它易使钢产生热脆,使钢的机械性能降低,同时对钢的耐蚀性、可焊性也不利,故硫也是钢中有害元素之一;高级优质钢中硫重量百分比含量不超过0.02%;硫在钢中易偏析。
28.铌(nb)是钢中常用的微合金元素,主要起细化晶粒和析出强化作用。固溶在钢中的nb和含nb的碳氮化物(nbc、nb(c,n))对奥氏体的再结晶行为均有强烈的抑制作用。nb通过抑制高温奥氏体的再结晶,扩大未再结晶区范围,细化奥氏体晶粒。奧氏体晶粒的细化在提高钢的强度的同时还可优化钢的韧性。nb的碳氮化物的析出温度相对较高,可在高温下钉扎晶界,延缓晶界迁移。在普通低合金钢中加nb,还可提高大气腐蚀能力,防止晶间腐蚀,改善焊接性能。
29.硼(b)作为痕量合金元素,在高强度低合金钢中发挥越来越重要的作用。痕量的b使钢的淬透性明显增加,可显著地抑制多边形铁素体在奥氏体晶界上形核。在较高的保温温度下,受晶粒粗化和非平衡偏析机制影响,b沿奥氏体晶界的偏析倾向加重,使大量m
23
(c,b)6过早地析出。b在晶界的偏聚和含b析出相的析出强化了含b钢奥氏体晶界的协调性和体晶格的流动性,使钢的热塑性提高。钢中添加一定量的b能够提高淬透性,提高钢的强度、硬度和耐磨性。b易与钢中的n元素结合生成nb,导致有效b降低。
30.含b钢中如果添加一定量的nb,钢的显微组织和力学性能将得到极大的改善。钢中nb的加入和nb(c,n)形成,抑制fe
23
(b,c)6粗大组织的出现。这在降低c扩散、提髙b的利用效率的同时,还能促进组织的均匀化。b对推迟贝氏体相变不明显,但b+nb能显著推迟贝氏体相变,在高温下作用更加明显。
31.在含nb的钢中,b还会与nb、c、n结合生成nb(c,n,b)类析出。在热变形后,送类析出相会在奥氏体中通过应变诱导效应在位错线上析出,可阻碍变形奥氏体的再结晶行为。在连续冷却过程中,痕量的b的添加对推迟过冷奥氏体相变作用不大,而b和nb的共同作用却能极大推迟过冷奥氏体相变。
32.铬(cr)在奥氏体相中扩散速度比较小,并阻碍c在奥氏体中的扩散。但是,cr是强烈的铁素体形成和稳定元素,缩小奥氏体相区。cr使钢的c曲线右移,临界冷却速度降低,淬透性提高。cr不是固溶强化元素,其强化作用主要与cr对奥氏体转变温度的影响有关。cr能够提高奥氏体相变温度,推迟高温相变反应。
33.钼(mo)与cr均能抑制先共析铁素体和珠光体的转变,扩大针状铁素体形成冷速范围,并能显著细化组织。在相同的冷速下,不含mo、cr的钢中主要以针状铁素体+少量多边形铁素体+少量m/a岛组成;添加了mo、cr的钢均由针状铁素体+m/a岛组成,且m/a岛的尺寸更加细小,分布也更加弥散。这种类型的组织细化有利于在提高钢的强度和韧性。cr能提高钢的硬度、强度和耐磨性能。
34.镍(ni)是奥氏体稳定元素,但不是碳化物形成元素,广泛应用于奥氏体不诱钢或双相不铸钢中。ni提高相变形核功,提高两相自由能差而降低临界转变温度。ni可降低钢中各元素的扩散速率,延缓奥氏体的分解转变,使c曲线右移,提高钢的淬透性,但ni添加过多,会因淬透性过强而恶化韧性。随着ni含量的增加,铁素体含量降低,抵消cr对铁素体相变的促进作用。此外,ni还抑制cr在铁素体中的析出。ni可稳定焊接热影响区母材基体的韧性,对韧性要求较高的钢中可添加一定量的ni。高韧性海洋结构厚板生产实践中,ni的用量一般为1%左右。合适的ni含量有利于提高钢的低温冲击功,降低韧脆转变温度。添加一定
量的ni,有利于汽车大梁在低温下的力学稳定性。
35.稀土是很强的脱氧剂、脱硫剂,它能消除或减弱钢中许多有害杂质的影响,钢中加入少量稀土,能提高钢的流动性,从而改善钢的质量,能显著提高不锈耐热钢的热加工塑性,结构钢中加入稀土能提高塑性和韧性,减弱可逆回火脆性等。
36.本发明的有益效果为:
37.基于耐磨钢轨、以及沿海和隧道用轨的特殊要求,本发明对碳含量为0.50-0.70%的亚共析钢轨中添加铜、镍、铬、钒、硅、锰、磷、硫,或是添加铌、钼、硼和稀土元素中的一种或几种,冶炼浇铸后,亚共析钢轨钢坯经过再次加热和轧制,采用热轧或是利用轧制余热进行在线热处理。在保证强度的同时,通过微合金化+低夹杂物控制,综合提高钢轨的耐蚀性能。钢中的夹杂物与基体钢之间极易形成微电池,形成腐蚀坑,所以耐蚀钢轨中夹杂含量应尽量的低。本发明所生产的亚共析钢轨相比u71mn热轧钢轨,耐磨性能提高10-50%,耐腐蚀性能提高5-60%。采用本发明方法可以有效提高钢轨的防腐效果,生产的钢轨提高了钢轨表层耐蚀性能,对于潮湿线路环境,具有良好的耐磨和耐蚀性能,满足高温潮湿隧道环境下的防腐效果。
38.本发明方法,避免国内钢轨生产厂家进行耐蚀的钢轨在实际使用过程及生产过程中存在耐蚀时间短、耐蚀性能不足等影响,可有效生产一种耐高温潮湿隧道环境下耐蚀高铁铁路用钢轨,可大幅提高钢轨使用寿命。对线路运行及维护,也有显著影响。
39.根据国贸公司2020年12月统计数据,钢轨边际效益达1000元/吨,以成功推广后年产1万吨计算,可至少新增经济效益1000万元以上。同时,将带动攀钢高速铁路用钢轨的推广和应用。
附图说明
40.图1显示本发明的耐磨耐腐蚀亚共析钢轨的生产方法的流程简图。
具体实施方式
41.为了使本发明的目的、技术方案及优点更加清楚明白,下面结合实施例及附图,对本发明进行进一步详细说明。应当理解,此处所描述的具体实施例仅用以解释本发明,并不用于限定本发明。
42.本发明提供的耐磨耐腐蚀亚共析钢轨,亚共析钢轨化学成分重量百分比为:碳:0.50-0.70%,铜:0.10-0.80%,镍:0.01-0.50%,铬:0.10-0.70%,钒:0.03-0.12%,磷:0.010-0.025%,硫:0.001-0.009%,硅和锰:0.8-2.0%,余量为铁和不可避免的杂质。
43.本发明的耐磨耐腐蚀亚共析钢轨中还可以包含化学成分重量百分比如下中的一种元素:0.006-0.050%的铌、0.01-0.10%的钼、0.0001-0.001%的硼以及0.02-0.05%的稀土元素。
44.本发明的耐磨耐腐蚀亚共析钢轨的生产方法的流程为:铁水预处理—转炉增碳法冶炼—无铝脱氧—包内合金化—lf+rh精炼—方坯连铸—连铸坯缓冷、检查和清理—铸坯加热—万能轧制—在线热处理—矫直—检测中心—检查,其中轧制之后可以采用热轧的方式处理,其中热轧态的亚共析钢轨中合金含量在1.04-4.12%之间,合金含量优选在2.5-4.0%之间,合金包括铜、镍、铬、钒、硅和锰;热轧态的亚共析钢轨中合金含量也可以在
1.046-4.17%之间,合金含量优选在2.5-4.0%之间,合金包括铜、镍、铬、钒、硅和锰以及铌。热轧态的亚共析钢轨中合金含量也可以在1.05-4.22%之间,合金含量优选在2.5-4.0%之间,合金包括铜、镍、铬、钒、硅和锰以及钼。也可以采用利用轧制余热进行在线热处理的方式。
45.本发明实施例1~16的耐磨耐腐蚀亚共析钢轨的生产方法,如图1所示,包括以下步骤:
46.步骤一:按重量百分比将铜、镍、铬、钒、磷、硫、硅和锰添加到含碳的亚共析钢轨中,冶炼浇铸成亚共析钢轨钢坯,亚共析钢轨钢坯的化学成分重量百分比为:碳:0.50-0.70%,铜:0.10-0.80%,镍:0.01-0.50%,铬:0.10-0.70%,钒:0.03-0.12%,磷:0.010-0.025%,硫:0.001-0.009%,硅和锰:0.8-2.0%,余量为铁和不可避免的杂质;
47.步骤二:再次加热步骤一的亚共析钢轨钢坯,亚共析钢轨钢坯加热温度为1200-1280℃,均热段时间为25-80min;
48.步骤三:轧制步骤二的再次加热后的亚共析钢轨钢坯,生产出亚共析钢轨。
49.本发明实施例6-16的耐磨耐腐蚀亚共析钢轨的生产方法,在步骤一中还按重量百分比添加铌、钼、硼和稀土元素中的一种,铌、钼、硼和稀土元素在亚共析钢轨钢坯中的化学成分重量百分比分别为0.006-0.050%、0.01-0.10%、0.0001-0.001%和0.02-0.05%。
50.本发明实施例4、6、9-14和16的耐磨耐腐蚀亚共析钢轨的生产方法,在步骤三之后采用热轧进行在线热处理,其中实施例4中热轧态的亚共析钢轨中合金含量在3.19%,合金包括铜、镍、铬、钒、硅和锰。实施例6中热轧态的亚共析钢轨中合金含量在2.676%,合金包括铜、镍、铬、钒、硅和锰以及铌。实施例12-14和16中热轧态的亚共析钢轨中合金含量在2.67%,合金包括铜、镍、铬、钒、硅和锰。实施例9-11中热轧态的亚共析钢轨中合金含量在2.68-2.77%,合金包括铜、镍、铬、钒、硅和锰以及钼。
51.本发明实施例1-3、5、7-8、15的耐磨耐腐蚀亚共析钢轨的生产方法,在步骤三之后利用轧制余热进行在线热处理,其中开冷温度为650-950℃,强制冷却速率为1-8℃/s,终冷温度为400-600℃。开冷温度是指钢轨进入热处理机组开始热处理时的温度,终冷温度是指钢轨退出热处理机组终止热处理时的温度。
52.本发明实施例的对比例采用与实施例1~5相同的化学成分、以及相同的加热、轧制或热处理工艺,其中对比例1~12中的化学成分重量百分比为:碳:0.45-0.75%,铜:0.05-0.85%,镍:0.005-0.55%,铬:0.05-0.75%,钒:0.02-0.15%,磷:0.008-0.009%,硫:0.012-0.016%,硅和锰:0.75-2.2%,余量为铁和不可避免的杂质。
53.本发明实施例和对比例的化学成分如表1所示,其中u71mn作为本发明实施例和对比例1~12的比较而列于表1中的对比例中。
54.表1化学成分
[0055][0056][0057]
本发明实施例1~16的亚共析钢轨化学成分重量百分比中硫含量≤0.009%,磷含量≤0.025%,对比例1~12的钢轨化学成分重量百分比中硫含量≤0.016%,磷含量≤0.009%。u71mn的化学成分重量百分比中硫含量0.011%,磷含量0.009%。
[0058]
对本发明的实施例和对比例的钢轨分别进行非金属夹杂物、脱碳层深度、氧化皮厚度和气体含量检验,检验结果如表2所示。
[0059]
表2非金属夹杂物、脱碳层深度、氧化皮厚度和气体含量
[0060][0061][0062]
本发明实施例1~16的亚共析钢轨的a类夹杂物≤0.5级,b类夹杂物≤0.5级,c类夹杂物≤0.5级,d类夹杂物≤0.5级,亚共析钢轨脱碳层深度≤0.15mm,氧化皮厚度≤0.25mm,氢含量≤0.8ppm,氧含量≤7ppm,氮含量≤59ppm。对比例1~12的钢轨的a类夹杂物≤2.5级,b类夹杂物≤1.0级,c类夹杂物≤1.0级,d类夹杂物≤1.0级,钢轨脱碳层深度≤0.45mm,氧化皮厚度≤0.90mm,氢含量≤1.6ppm,氧含量≤16ppm,氮含量≤67ppm。u71mn的a类夹杂物2.0级,b类夹杂物1.0级,c类夹杂物1.0级,d类夹杂物1.0级,钢轨脱碳层深度0.35mm,氧化皮厚度0.58mm,氢含量1.2ppm,氧含量11ppm,氮含量61ppm。
[0063]
本发明在保证强度的同时,通过微合金化+低夹杂物控制,综合提高亚共析钢轨的耐蚀性能。钢中的夹杂物与基体钢之间极易形成微电池,形成腐蚀坑,所以本发明的耐磨耐腐蚀亚共析钢轨中夹杂含量应尽量的低。
[0064]
对热态和在线热处理态的本发明的实施例和对比例的钢轨分别进行拉伸性能和
踏面硬度检验,检验结果如表3所示,并分别在本发明的实施例和对比例的钢轨轨头处取磨损试样,进行钢轨轨头磨损试验,试验参数和测试结果如表3所示。
[0065]
分别按照gb/t 19746和tb/t 2375标准在实施例和对比例钢轨中进行周期浸润加速腐蚀试验,腐蚀剂为2%的nacl溶液,腐蚀时间200h,试验结果如表3所示。
[0066]
本发明实施例1~16的钢轨的拉伸性能rm为1043~1196mpa,断后延伸率a为14~17%,踏面硬度为301~347hbw10/3000,钢轨轨头磨损量为0.71~0.82g,腐蚀率为1.9~3.0g/m2·
h。对比例1~12的钢轨的拉伸性能rm为1012~1165mpa,断后延伸率a为11~15%,踏面硬度为293~338hbw10/3000,钢轨轨头磨损量为0.73~0.85g,腐蚀率为3.2~3.4g/m2·
h。u71mn的拉伸性能rm为950mpa,断后延伸率a为13%,踏面硬度为275hbw10/3000,钢轨轨头磨损量为0.90g,腐蚀率为5.0g/m2·
h。
[0067]
本发明提出适用于潮湿环境特殊环境—耐高温潮湿环境下的钢轨及其生产方法,生产的亚共析钢轨相比u71mn热轧钢轨,耐磨性能提高9~21%,耐腐蚀性能提高40-62%。采用该方法生产的钢轨,对于潮湿线路环境,具有良好的耐磨和耐蚀性能。
[0068]
表3拉伸性能、踏面硬度、钢轨轨头磨损、腐蚀试验
[0069][0070][0071]
本发明的耐磨耐腐蚀亚共析钢轨,所生产的亚共析钢轨耐磨性能和耐蚀性能均提高。本发明提供的用于耐高温潮湿环境下的耐磨耐腐蚀亚共析钢轨也可用于其它铁路线路,提高钢轨耐蚀性能。
[0072]
以上所述实施例仅表达了本发明的实施方式,其描述较为具体和详细,但并不能因此而理解为对本发明专利范围的限制。应当指出的是,对于本领域的普通技术人员来说,在不脱离本发明构思的前提下,还可以做出若干变形和改进,这些都属于本发明的保护范
围。因此,本发明专利的保护范围应以所附权利要求为准。