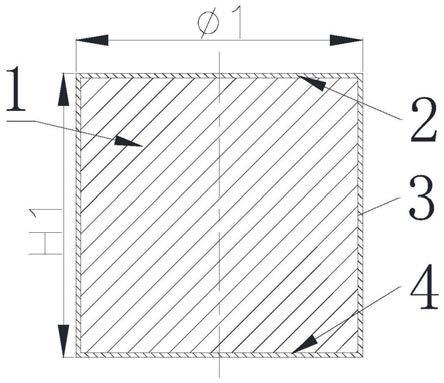
1.本发明是一种提高镍基难变形高温合金组织均匀性的方法,属于金属材料的热加工领域。
背景技术:
2.镍基难变形高温合金目前主要用于航空发动机涡轮盘的制备。由于材料合金化程度高,特别是al、ti含量高会导致合金塑性变形工艺区间窄,塑性变形能力差;且由于对该合金的熔炼工艺研究不足,铸锭内部极易形成疏松缺陷。上述现状导致该合金难以通过常规的铸锭自由锻或者是快锻的方法制备组织均匀的棒材。
技术实现要素:
3.本发明正是针对上述现有技术中存在的缺点而设计了一种提高镍基难变形高温合金组织均匀性的方法,其目的在于通过包套、镦锻和挤压工艺相结合的设计,低成本、简便的解决了难变形合金塑性变形能力差、组织不均匀的问题,获得组织均匀、表面完整的高质量棒材,为高性能锻件的制备奠定基础。
4.本发明的目的是通过以下技术方案来实现的:
5.本发明所述的提高镍基难变形高温合金组织均匀性的方法的步骤如下:
6.步骤一、制备合金铸锭
7.采用两联或者三联工艺制备合金铸锭1;
8.步骤二、制作包套锭
9.将合金铸锭1置于筒体3内,把前端盖2、后端盖4与筒体2封焊后制成包套锭5;
10.筒体3的直径为φ1,筒体3的高度为h1;
11.步骤三、制作包套前垫6
12.包套前垫6为向上一侧中心部分呈圆形凸起状的盘形件ⅰ,该盘形件ⅰ边缘部分的厚度为h2,该盘形件ⅰ的最大直径为φ2,呈圆形凸起的中心部分的直径为φ3、高度为h3;
13.步骤四、制作包套后垫7
14.包套后垫7为向下一侧中心部分呈圆形凸起状的盘形件ⅱ,该盘形件ⅱ边缘部分的厚度为h4,该盘形件的最大直径为φ4,呈圆形凸起的中心部分的直径为φ5、高度为h5;
15.步骤五、包套锭5的加热与保温
16.将包套锭5置于电阻加热炉中加热,在炉温<600℃时将包套锭5装入加热炉中,升温至800℃~950℃并保温,保温时间按0.6~0.8min/mm
×
φ
包套锭
计算,然后再随炉升温至1100℃并保温,保温时间按0.8~1min/mm
×
φ
包套锭
计算;
17.步骤六、制备镦锻坯12
18.在挤压机基座9外围安装挤压筒10,将实心模8置于挤压机基座9上,包套前垫6置于实心模8上,中心部分的圆形凸起向上,将挤压筒10加热到150℃~400℃,待包套锭5保温结束后取出迅速放入挤压筒10内,然后放入包套后垫7,中心部分的圆形凸起向下,开动挤
压机将挤压杆11推入挤压筒10进行镦锻,并在最大压力下保持30~50秒,保压结束后,得到镦锻坯12,然后将其出模并空冷;
19.步骤七、机加
20.对镦锻坯12进行机加精整表面并在其下端倒圆角r3,镦锻坯12的外径为φ6;
21.步骤八、制作与挤压筒10尺寸相匹配的挤压润滑玻璃垫13;
22.步骤九、镦锻坯12的加热与保温
23.将镦锻坯12放入电阻加热炉中加热,在炉温<600℃时将热压实坯料装入加热炉中,升温至800℃~950℃并保温,保温时间按0.4~0.6min/mm
×
φ
镦锻坯
计算,然后再随炉升温至1100℃并保温,保温时间按0.6~0.8min/mm
×
φ
镦锻坯
计算;
24.步骤十、制备合金挤压棒材
25.将空心模14安装在挤压机基座9上,将挤压润滑玻璃垫13置于空心模14上并在其外围安装挤压筒10,将挤压筒10加热到150℃~400℃,待镦锻坯12保温结束后取出迅速放入挤压筒10内,顺次放入挤压垫15,开动挤压机将挤压杆11推入挤压筒10进行挤压,获得带金属包套的挤压棒材,待其冷却至室温后,去除金属包套,获得合金挤压棒材。
26.在一种实施中,步骤二中,包套的材料为45号钢或304不锈钢,包套的厚度按以下公式计算:
27.δ=(5%~10%)
×
φ
铸锭
ꢀꢀꢀ
式1
28.式1中:δ为包套的厚度,φ
铸锭
为合金铸锭1的直径。
29.在一种实施中,步骤三、四中,盘形件ⅰ、盘形件ⅱ的外缘与挤压筒10的内璧的单边距离为1~3mm。
30.在一种实施中,步骤三、四中,盘形件ⅰ、盘形件ⅱ的边缘部分的厚度h2、h4为50~100mm。
31.在一种实施中,步骤三、四中,盘形件ⅰ、盘形件ⅱ的材料为45号钢或304不锈钢。
32.在一种实施中,步骤七中所述圆角r3为50~100mm。
33.在一种实施中,步骤七中所述镦锻坯12的外径为φ6比挤压筒10的内径小2~6mm。
34.在实施中,所述镍基难变形高温合金的化学成分及重量百分比为:
35.cr 16.50~19.50,co 13.50~16.0,al 2.0~3.0,ti 4.50~5.50,w 1.0~2.0,mo 2.50~3.50,b 0.01~0.03,c≤0.10,si≤0.15,fe≤0.1,zr≤0.06,mn≤0.15,s≤0.01,cu≤0.1,ag≤0.0005,bi≤0.0001,pb≤0.001,余量为ni。
36.本发明技术方案采用三向应力的镦锻/挤压复合工艺,同时结合包套的设计,将一定规格的合金铸锭首先在挤压筒内进行三向应力镦锻,由于在挤压筒内镦锻,避免了常规的单一方向镦粗的缺点,包括:避免了疏松缺陷在单向拉伸力下应力集中,产生裂纹,同时靠着多向压应力,压实焊合疏松缺陷,同时实现对铸锭心部区域大变形,使铸锭内外晶粒趋于一致;然后再进行带包套挤压,使合金铸锭进一步细化晶粒,焊合疏松缺陷,为合金涡轮盘的制备奠定组织基础。
37.从铸锭切取低倍片,观察整个低倍组织,确定心部粗晶区的晶粒度等级g
粗
和所占据的中心区域(以直径φ
粗晶区
表示),确定粗晶区以外的细晶区晶粒度等级g
细
。
38.根据粗晶占据的中心区域直径φ
粗晶区
来确定包套前垫φ3和后垫φ5的数值:φ3=φ5=φ
粗晶区
。
39.采用10%、20%、30%、40%锻造试验法确定合金铸锭变形量与晶粒度的关系,10%=g
10
、20%=g
20
、30%=g
30
、40%=g
40
40.确定铸锭粗晶区和细晶区的晶粒度等级差:g
差
=g
粗-g
细
。
41.根据粗晶区和细晶区的晶粒度等级差g
差
对比变形量与晶粒度的关系,确定变形量y,根据变形量y确定包套前垫h3和后垫h5的数值:h3=h5=h1
×
y/2.
42.本发明技术方案的有益效果为:
43.1、经过挤压筒内多向镦锻,在实现合金铸锭包套的同时,使铸锭受到多向压应力变形焊合疏松缺陷;
44.2、采用凸形分离的前后垫设计,精确的对铸锭中心粗大组织进行大变形,进行细化组织,平衡了铸锭晶粒具有的有外到内由细变粗的规律,使其向中心细外缘粗的规律发展,为挤压做好了组织准备;
45.3、在边缘粗、中间细的镦锻坯条件准备下,根据挤压会造成外缘细,中心粗的特点,经挤压后,正好可以获得边缘与心部平衡的组织状态;挤压的同时还会进一步细化晶粒、焊合疏松缺陷;获得组织均匀的高质量棒材,为高性能合金涡轮盘的制备奠定基础。
附图说明
46.图1是本发明所述包套的结构示意图
47.图2是本发明所述包套前垫的结构示意图
48.图3是本发明所述包套后垫的结构示意图
49.图4是本发明方法制备镦锻坯的模具组合结构示意图
50.图5是本发明方法制备的镦锻坯的结构示意图
51.图6是本发明方法制备合金挤压棒材的模具组合结构示意图
具体实施方式
52.以下将结合附图和实施例对本发明技术方案作进一步地详述:
53.参见附图1~6所示,采用本发明所述的提高镍基难变形高温合金组织均匀性的方法的步骤如下:
54.步骤一、采用两联或者三联工艺制备的合金铸锭1,化学成分见表1;
55.表1合金化学成分
[0056][0057]
步骤二、制作包套锭,由合金铸锭1、前端盖2、筒体3、后端盖4组成,将合金铸锭1置于筒体3内,把前端盖2、后端盖4与筒体2封焊后制成包套锭5,根据合金铸锭1的直径、高度确定前端盖2、筒体3、后端盖4的最大直径φ1=270mm以及筒体2的高度h1=700mm,根据合金铸锭直径确定前端盖2、筒体3、后端盖4的厚度,厚度为δ=15mm,前端盖2、筒体3、后端盖4的材料304不锈钢;
[0058]
步骤三、制作包套前垫6,包套前垫6为凸形结构,最大直径φ2=310mm与挤压筒璧单边距离2.5mm,根据铸锭低倍观察晶粒度时所确定的心部粗晶区确定直径φ3=120mm、h3=20mm,厚度h2为50mm,包套前垫6的材料为304不锈钢;
[0059]
步骤四、制作包套后垫7,包套后垫7为凸形结构,最大直径φ4=310mm与挤压筒璧单边距离2.5mm,根据铸锭低倍观察晶粒度时所确定的心部粗晶区直径φ5=120mm、h5=20mm,厚度h4为50mm,包套后垫7的材料为304不锈钢;
[0060]
步骤五、将包套锭5在电阻加热炉中加热,室温时将包套锭5装入加热炉中,升温至900℃,包套锭5在恒温下进行保温,保温时间180min,然后再随炉升温至1100℃,包套锭5在恒温下继续保温,保温时间180min;
[0061]
步骤六、将实心模8置于挤压机基座9上,包套前垫6置于实心模8上,将挤压筒10加热到300℃,待包套锭5保温结束后取出迅速放入挤压筒10内,顺次放入包套后垫7,开动挤压机将挤压杆11推入挤压筒10进行镦锻,并在最大压力下保持30秒,保压结束后,镦锻坯12出模并空冷;
[0062]
步骤七、镦锻坯12机加精整表面并在前端倒圆角,其中φ6小于所需挤压筒尺寸6mm,r3为50mm;
[0063]
步骤八、制作挤压润滑玻璃垫13,挤压玻璃垫与挤压模尺寸匹配;
[0064]
步骤九、将镦锻坯12放入电阻加热炉中加热,室温时将镦锻坯装入加热炉中,升温至900℃,镦锻坯12在恒温下进行保温,保温时间按180min,然后再随炉升温至1100℃,镦锻坯12在恒温下继续保温,保温时间按180min;
[0065]
步骤十、将空心模14置于挤压机基座9上,将玻璃垫13置于空心模上,将挤压筒10加热到300℃,待镦锻坯12保温结束后取出迅速放入挤压筒10内,顺次放入挤压垫15,开动挤压机将挤压杆11推入挤压筒10进行挤压,获得带金属包套的挤压棒材,待其冷却至室温后,去除金属包套,获得合金挤压棒材。