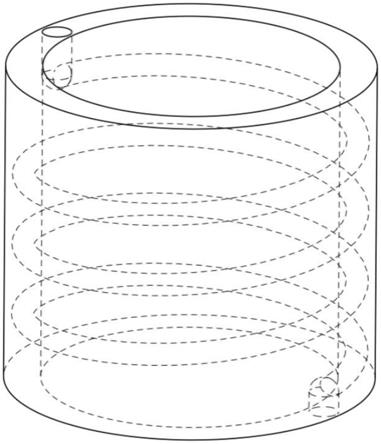
一种内置管道零件的3d打印工艺
技术领域
1.本发明涉及3d打印工艺技术领域,具体为一种内置管道零件的3d打印工艺。
背景技术:
2.slm(选择性激光熔化),是金属材料增材制造中的一种主要技术途径,该技术选用激光作为能量源,按照三维cad切片模型中规划好的路径在金属粉末床层进行逐层扫描,扫描过的金属粉末通过熔化、凝固从而达到冶金结合的效果,最终获得模型所设计的金属零件,slm技术克服了传统技术制造具有复杂形状的金属零件带来的困扰,它能直接成型出近乎全致密且力学性能良好的金属零件。
3.3d打印(slm工艺)产品的表面质量由材料、零件结构和工艺参数决定,3d打印(slm工艺)的工艺参数一般有填充光斑直径、填充扫描速度、填充激光功率、轮廓光斑直径、轮廓扫描功率、轮廓扫描速度、扫描策略等,设备提供商在设备出厂时调定的工艺参数,在打印具有内置管道的零件(参考图1)时会产生肉眼可见的缺陷,缺陷主要表面为:在图2所示的区域内会有大颗粒结构、凹坑、熔不透。
技术实现要素:
4.(一)解决的技术问题
5.针对现有技术的不足,本发明提供了一种内置管道零件的3d打印工艺,解决了以往设备出厂时参数不准导致零件有大颗粒结构、凹坑、熔不透的缺陷的问题。
6.(二)技术方案
7.为实现以上目的,本发明通过以下技术方案予以实现:一种内置管道零件的3d打印工艺,包括以下步骤:
8.s1、基础准备
9.首先对待打印零件进行尺寸测定,之后将待打印零件模型导入三维软件中,并利用三维软件对待打印零件进行切片分层以及优化支撑结构设计,在确定切片分层位置和厚度的同时规划好后续激光扫描路径,完成后进行切片导出,将数据导入到打印机中;
10.s2、激光熔融设备准备
11.打开选择性激光熔融设备的打印舱并清除内部杂质,将粉末状态的金属打印材料置于选择性激光熔融设备的料仓中,密封打印舱并设置选择性激光熔融设备参数,具体包括:轮廓光斑直径60-80um、填充光斑直径90-110um、轮廓激光功率150-170w、填充激光功率290-310w、轮廓扫描速度800-1000mm/s以及填充扫描速度1150-1350mm/s;
12.s3、3d打印
13.打印时选择性激光熔融设备的激光器射出一束激光,激光将照射区域的粉末状态的金属打印材料熔化,熔化后的金属将快速冷却凝固,打印完一层后,成型基板下降一个层厚高度,然后刮刀铺设一层新的粉末状态的金属打印材料,如此往复直到工件成型;
14.s4、零件修饰与测试
15.打印完成后将选择性激光熔融设备的基板上多余的粉末扫开,取出零件后再去除模型上的支撑结构,用研磨机对零件各部进行研磨和抛光并利用高压清洗机对零件进行清洁,最后利用气密测试台对零件的气密性品质进行测试,成功后得到合格产品。
16.优选的,所述s2中粉末状态的金属打印材料为alsi
10
mg。
17.优选的,所述s3中在密封选择性激光熔融设备的打印舱后,在打印舱中需充满惰性气体,惰性气体为氮气或氩气,防止金属在熔化成型时发生氧化。
18.(三)有益效果
19.本发明提供了一种内置管道零件的3d打印工艺。具备以下有益效果:
20.本发明通过优化分层厚度及支撑结构,利用多次打印试验对比,通过设定选择性激光熔融设备的参数,具体包括:轮廓光斑直径60-80um、填充光斑直径90-110um、轮廓激光功率150-170w、填充激光功率290-310w、轮廓扫描速度800-1000mm/s以及填充扫描速度1150-1350mm/s,实现了避免以往内置管道零件的3d打印工艺打印出的零件,具有大颗粒结构、凹坑、熔不透等肉眼可见的缺陷问题的效果,提高了产品的良品率。
附图说明
21.图1为本发明的内置管道的零件示意图;
22.图2为本发明的零件缺陷部位示意图;
23.图3为本发明的试验零件示意图。
具体实施方式
24.下面将结合本发明实施例中的附图,对本发明实施例中的技术方案进行清楚、完整地描述,显然,所描述的实施例仅仅是本发明一部分实施例,而不是全部的实施例。基于本发明中的实施例,本领域普通技术人员在没有做出创造性劳动前提下所获得的所有其他实施例,都属于本发明保护的范围。
25.实施例:
26.如图1-3所示,本发明实施例提供一种内置管道零件的3d打印工艺,包括以下步骤:
27.s1、基础准备
28.首先对待打印零件进行尺寸测定,之后将待打印零件模型导入三维软件中,并利用三维软件对待打印零件进行切片分层以及优化支撑结构设计,好的支撑结构设计可便于后续的支撑结构与零件的分离,在确定切片分层位置和厚度的同时规划好后续激光扫描路径,不同的分层位置和分层厚度会影响3d打印的效率,完成后进行切片导出,将数据导入到打印机中;
29.s2、激光熔融设备准备
30.打开选择性激光熔融设备的打印舱并清除内部杂质,避免金属成型时杂质残留在其内部,影响零件的质量,将粉末状态的金属打印材料置于选择性激光熔融设备的料仓中,密封打印舱并设置选择性激光熔融设备参数,具体包括:轮廓光斑直径60-80um、填充光斑直径90-110um、轮廓激光功率150-170w、填充激光功率290-310w、轮廓扫描速度800-1000mm/s以及填充扫描速度1150-1350mm/s;
31.s3、3d打印
32.打印时选择性激光熔融设备的激光器射出一束激光,激光将照射区域的粉末状态的金属打印材料熔化,熔化后的金属将快速冷却凝固,打印完一层后,成型基板通过激光熔融设备的升降机构下降一个分层的层厚高度,然后刮刀将料仓中的粉末刮至成型基板上,进而即可铺设一层新的粉末状态的金属打印材料,激光再次将照射区域的粉末状态的金属打印材料熔化,熔化后的金属将快速冷却凝固,如此往复直到工件成型;
33.s4、零件修饰与测试
34.打印完成后将选择性激光熔融设备的基板上多余的粉末扫开,取出零件后再去除模型上的支撑结构,支撑结构能利用线切割方式去除,在设计支撑结构时,在确保支撑结构具有稳定的支撑功能的前提下,应使得支撑结构与零件的接触面积尽量小,以便于后续的与零件之间的分离,用研磨机对零件各部进行研磨和抛光并利用高压清洗机对零件进行清洁,最后利用气密测试台对零件的气密性品质进行测试,成功后得到合格产品。
35.s2中粉末状态的金属打印材料为alsi
10
mg。
36.s3中在密封选择性激光熔融设备的打印舱后,在打印舱中需充满惰性气体,惰性气体为氮气或氩气,防止金属在熔化成型时发生氧化。
37.本实施例中,为了探寻选择性激光熔融设备在内置管道零件的3d打印工艺中的最佳使用参数设定,通过多次反复的实验对比(打印图3零件),得到一组参数:具体包括:轮廓光斑直径60-80um、填充光斑直径90-110um、轮廓激光功率150-170w、填充激光功率290-310w、轮廓扫描速度800-1000mm/s以及填充扫描速度1150-1350mm/s,该参数设定使得零件的产品质量得到了提升,实现了避免以往内置管道零件的3d打印工艺打印出的零件,具有大颗粒结构、凹坑、熔不透等肉眼可见的缺陷问题的效果,提高了产品的良品率。
38.尽管已经示出和描述了本发明的实施例,对于本领域的普通技术人员而言,可以理解在不脱离本发明的原理和精神的情况下可以对这些实施例进行多种变化、修改、替换和变型,本发明的范围由所附权利要求及其等同物限定。