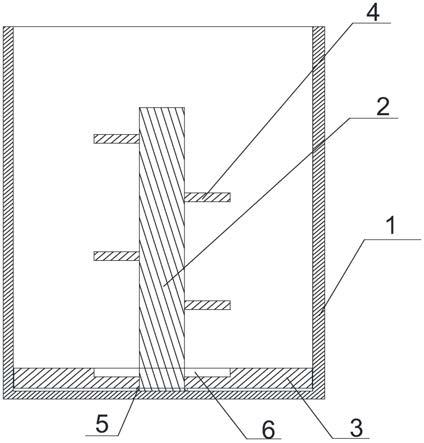
1.本发明涉及一种制备工艺,具体涉及一种含磷钒渣除磷工艺。
背景技术:
2.我国蕴藏大量的钒钛磁铁矿,钒钛磁铁矿主要是通过高炉或其它炼铁流程首先得到含钒铁水,然后在转炉中吹入氧气使铁水中的钒氧化富集到渣中,钒经过富集后进入渣相得到钒渣。冶炼钒钛磁铁矿后的钒渣含磷量为0.020~0.30%,钒渣氧化钠化提钒焙烧成熟料时,大量磷转化为可溶于水磷酸盐,熟料直接用水浸取后钒溶液含有大量磷离子。为确保五氧化二钒产品中磷含量合格(≤0.05%),通常对钒溶液采取净化方法脱除溶液中有害杂质磷。
3.目前,碱性含钒溶液常采用化学沉淀除p,该技术成熟稳定、操作简单。常用除磷剂为可溶性镁盐(适宜ph~10.0)、可溶性钙盐(适宜ph8~10),可溶性铝盐(适宜ph=8~9)或这几种盐的复合盐(如cacl+alcl3,适宜ph8.5~11.0)。其基本原理是在溶液中加入ca2+、mg2+、nh4+、al3+等阳离子,通过调节溶液的ph值,使之形成磷酸盐沉淀,达到除磷的目的。有时可加入聚丙烯酰胺(pam)以改善磷酸盐沉淀的沉降效果。除此之外基于碱性含钒溶液中p(
ⅴ
价)阴离子与v(
ⅴ
价)多核阴离子的半径和所带电荷的差异,可采用离子交换法分离碱性含钒溶液中v与p。若将碱性含钒溶液采用的化学沉淀除磷方法应用到酸性含钒溶液体系中,必须先调节溶液的ph值至碱性,而随着溶液ph升高,酸性钒溶液中ca2+、mn2+、mg2+、fe3+会与钒酸根形成钒酸盐沉淀,同时al3+、si4+发生水解作用而产生的胶体状沉淀会吸附大量的钒,导致钒损失较高。且后续沉钒又需将溶液调为酸性,导致操作过程繁琐、酸碱消耗大、处理费用高。
4.对于中性和酸性溶液介质中p的去除主要采用固体材料物理化学吸附法(木质颗粒、藻类、介孔硅质纳米颗粒、炉渣等)、生物法、电絮凝法、膜分离技术等。电絮凝的原理是在电流作用下使铝和铁水解、聚合转化为羟基络合物,多核羟基络合物使溶液中杂质p絮凝而沉淀分离,同时阴极析出的氢气起到浮选作用。在p浓度20mg/l,槽电压25v的条件下,对于ph为3和7的含p废水,p去除率分别为85%和95%。xudongzheng等制备的介孔掺la膜在p浓度200mg/l,溶液初始ph3.0~7.0范围内均表现出良好的除p性能,且在f-、so42-、cl-、no3-阴离子存在的条件下,对p仍表现出较强的选择性。
技术实现要素:
5.本发明的一个目的在于提供一种含磷钒渣除磷工艺,本发明通过采用弱酸溶液浸出,浸出完毕后固液分离得到脱磷钒渣和含钠含磷液体,同时得到的含钠含磷液体还可重复利用进行除磷,以提高使用效率,节约费用。
6.该目的采用以下技术方案实现:包括以下步骤:
7.步骤1将碳酸钠与钒渣混合,得到混合物;
8.步骤2研磨混合物,研磨后将混合物焙烧,得到焙烧固体;
9.步骤3使用弱酸溶液浸出焙烧固体,浸出完毕后进行固液分离得到脱磷钒渣和浸取液;
10.步骤4浸取液中加入氯化钙,得到底流与除磷后浸取液;
11.步骤5除磷后浸取液进行浓缩得到第一物质,底流压滤后得到第二物质,第一物质和第二物质加入步骤1中重复上述步骤。
12.进一步的,本发明将碳酸钠与钒渣混合,能够使得在弱酸环境中钒渣中的钒充分浸出,同时本发明所得第一物质和第二物质重新加入步骤1中以碳酸钠、钒渣混合,能够进一步的提高除磷效果,从而提高钒的回收效率;并且本发明利用第一物质和第二物质重复利用,不仅简化了操作流程,还降低了再钒渣中除磷的成本,避免了大量废渣与废液的产生。
13.优选的,步骤3中脱磷钒渣采用高温空白焙烧-酸浸的工艺提钒。
14.优选的,步骤2中,混合物球磨至100目。步骤2中,研磨后的混合物在450-600℃下煅烧60min。
15.在本发明工艺中,为了进一步的提高本工艺的使用效率,并降低成本,本发明工艺还配套了一种反应腔,该反应腔内设置有旋转杆,旋转杆上套装有分隔板,分隔板将反应腔的内部分为上下两个区域,分隔板能够在旋转杆上上下移动,分隔板上设置有若干过滤孔,在原始状态时,分隔板位于旋转杆的下端,步骤1和步骤2均在反应腔的分隔板的上方进行反应,即在上区域中进行反应,当在反应腔使用弱酸溶液浸出焙烧固体,浸出完毕后,分隔板在旋转杆上向上移动,分隔板在向上移动的过程中,浸取液通过分隔板上的过滤孔位于分隔板的下方,分隔板在向上移动的过程中将脱磷钒渣一起向上移动,进而进行固液分离,得到脱磷钒渣和浸取液。脱磷钒渣可从反应腔中快速取出。
16.具体的,本发明在使用时,分隔板在旋转杆上伸缩的具体结构为,旋转杆上套装有伸缩杆,伸缩杆的一端与反应腔内底部连接,伸缩杆的另一端与分隔板连接,伸缩杆带动分隔板在旋转杆上移动。伸缩杆在伸缩时带动分隔板在旋转杆上移动。
17.在本工艺中,碳酸钠与钒渣混合时,为了在反应腔中能够充分混合,反应腔中的旋转杆上设置有若干搅拌杆,搅拌杆能够在旋转杆上上下移动。旋转杆能够带动搅拌杆一起以旋转杆所在直线为轴线旋转,在使用时,旋转杆旋转时带动搅拌杆一起旋转,进而提高混合效率,并且搅拌杆能够在旋转杆上上下移动,因此当分隔板在旋转杆上上下移动时,搅拌杆不会阻碍分隔板的移动。
18.本发明中,浸出完毕后进行固液分离得到脱磷钒渣和浸取液;在浸取液中加入氯化钙,得到底流与除磷后浸取液;即通过分隔板向反应腔的下区域中加入氯化钙,本工艺中分隔板上具有可加入氯化钙的第一通孔,以及取出第二物质的第二通孔,在未使用时第一通孔和第二通孔均为关闭状态,当需要进行使用时,分别打开对应的第一通孔或第二通孔即可,提高使用效率。在本工艺中,在浸取液中加入氯化钙,得到底流与除磷后浸取液,除磷后浸取液进行浓缩得到第一物质,取出除磷后浸取液后,本工艺通过将分隔板向下移动,进而对底流进行压滤后得到第二物质,然后通过第二通孔取出第二物质,分隔板位于旋转杆的最下方即原始状态时,然后将第一物质和第二物质加入步骤1中的碳酸钠与钒渣进行混合,重复上述步骤。以便重复利用第一物质和第二物质,简化操作流程,降低了再钒渣中除磷的成本,并避免了大量废渣与废液的产生。
19.更进一步的,在本发明中,搅拌杆能够在旋转杆上上下移动是通过移动槽和分隔板进行实现的,旋转杆上设置有四个移动槽,每个移动槽与一个搅拌杆对应,并且每个移动槽的长度不同,搅拌杆能够在移动槽内上下移动,当分隔板向上移动时,接触到一个搅拌杆时,分隔板会带动该搅拌杆一起向上移动,搅拌杆在移动槽中一起向上移动,旋转杆上设置有四个搅拌杆,四个搅拌杆能够组成一个圆形,分隔板上设置有用于放置四个搅拌杆的放置槽。当分隔板移动到最上方的位置时,四个搅拌杆位于同一水平平面上,并且组成一个圆,位于分隔板上的放置槽中,当分隔板向下移动时,搅拌杆在重力的作用下自动在移动槽中向下移动,进而提高使用效率。
20.本发明与现有技术相比,具有如下的优点和有益效果:
21.本发明一种含磷钒渣除磷工艺,本发明通过采用弱酸溶液浸出,浸出完毕后固液分离得到脱磷钒渣和含钠含磷液体,能够使得在弱酸环境中钒渣中的钒充分浸出,同时本发明所得第一物质和第二物质重新加入步骤1中与碳酸钠、钒渣混合,能够进一步的提高除磷效果,从而提高钒的回收效率;本发明利用第一物质和第二物质重复利用,不仅简化了操作流程,还降低了再钒渣中除磷的成本,避免了大量废渣与废液的产生同时得到的含钠含磷液体还可重复利用进行除磷,以提高使用效率,节约费用;
22.其次,本发明提供了与本工艺配套的反应腔,不仅能进一步的提高使用效率,简化所需装置和步骤,并且本装置结构简单,便于长期使用,提高使用效率。
附图说明
23.此处所说明的附图用来提供对本发明实施例的进一步理解,构成本技术的一部分,并不构成对本发明实施例的限定。在附图中:
24.图1为本装置结构示意图;
25.图2为分隔板进行固液分离时本装置结构示意图;
26.图3为旋转杆结构示意图;
27.图4为旋转杆及其上的搅拌片的结构示意图;
28.图5为分隔板、放置槽之间的结构示意图;
29.图6为搅拌片位于分隔板内时本装置结构示意图;
30.图7为分隔板、搅拌片的俯视图。
31.附图中标记及对应的零部件名称:
32.1-反应腔,2-旋转杆,3-分隔板,4-搅拌片,5-伸缩杆,6-放置槽,7-移动槽,8-连接杆。
具体实施方式
33.为使本发明的目的、技术方案和优点更加清楚明白,下面结合实施例和附图,对本发明作进一步的详细说明,本发明的示意性实施方式及其说明仅用于解释本发明,并不作为对本发明的限定。
34.在本发明的描述中,需要理解的是,术语“前”、“后”、“左”、“右”、“上”、“下”、“竖直”、“水平”、“高”、“低”“内”、“外”等指示的方位或位置关系为基于附图所示的方位或位置关系,仅是为了便于描述本发明和简化描述,而不是指示或暗示所指的装置或元件必须具
有特定的方位、以特定的方位构造和操作,因此不能理解为对本发明保护范围的限制。
35.【实施例1】
36.本发明包括以下步骤:
37.步骤1将碳酸钠与钒渣混合,得到混合物;
38.步骤2研磨混合物,研磨后将混合物焙烧,得到焙烧固体;
39.步骤3使用弱酸溶液浸出焙烧固体,浸出完毕后进行固液分离得到脱磷钒渣和浸取液;
40.步骤4浸取液中加入氯化钙,得到底流与除磷后浸取液;
41.步骤5除磷后浸取液进行浓缩得到第一物质,底流压滤后得到第二物质,第一物质和第二物质加入步骤1中重复上述步骤。
42.其中,步骤3中脱磷钒渣采用高温空白焙烧-酸浸的工艺提钒。步骤2中,混合物球磨至100目。步骤2中,研磨后的混合物在450-600℃下煅烧60min。在本实施例中,钒的回收率99.8%。
43.【实施例2】
44.在实施例1的基础上,如图1所示,包括反应腔1,反应腔1内设置有旋转杆2,旋转杆2上套装有分隔板3,分隔板3将反应腔1的内部分为上下两个区域,分隔板3能够在旋转杆2上上下移动,分隔板3上设置有若干过滤孔,分隔板3在旋转杆2上上下移动能够使脱磷钒渣和浸取液固液分离。
45.在使用时,如图1所示,分隔板位于反应腔的内底部,即旋转杆的下端上,将碳酸钠与钒渣加入反应腔中,并位于分隔板的上方,旋转杆上设置有若干搅拌片4,搅拌片4能够在旋转杆2上上下移动。旋转杆带动搅拌片一起旋转,进而使碳酸钠与钒渣充分混合,得到混合物;得到混合物后在反应腔中对混合物进行研磨,研磨后将混合物焙烧,得到焙烧固体;在本实施例中,研磨时,混合物球磨至100目;研磨后的混合物在450-600℃下煅烧60min得到焙烧固体。然后使用弱酸溶液浸出焙烧固体,浸出完毕后进行固液分离得到脱磷钒渣和浸取液;其中,脱磷钒渣采用高温空白焙烧-酸浸的工艺提钒。浸取液中加入氯化钙,得到底流与除磷后浸取液,具体的,当在反应腔1使用弱酸溶液浸出焙烧固体,浸出完毕后,分隔板3在旋转杆2上向上移动,分隔板在向上移动的过程中,浸取液通过分隔板上的过滤孔位于分隔板的下方,分隔板在向上移动的过程中将脱磷钒渣一起向上移动,进而进行固液分离,得到脱磷钒渣和浸取液,分隔板在向上移动的过程中,旋转杆上的搅拌片也向上移动,最终如图2所示,固液分离得到脱磷钒渣和浸取液。脱磷钒渣可从反应腔中快速取出。
46.浸取液位于分隔板的下方,在浸取液中加入氯化钙,得到底流与除磷后浸取液;即通过分隔板向反应腔的下区域中加入氯化钙,在本装置中分隔板上具有可加入氯化钙的第一通孔,以及取出第二物质的第二通孔,在未使用时第一通孔和第二通孔均为关闭状态,当需要进行使用时,分别打开对应的第一通孔或第二通孔即可,提高使用效率。
47.在浸取液中加入氯化钙,得到底流与除磷后浸取液,除磷后浸取液进行浓缩得到第一物质,取出除磷后浸取液后,本装置通过将分隔板向下移动,进而对底流进行压滤后得到第二物质,然后通过第二通孔取出第二物质,分隔板位于旋转杆的最下方即原始状态时,然后将第一物质和第二物质加入碳酸钠与钒渣进行混合,重复上述步骤。以便重复利用第一物质和第二物质,简化操作流程,降低了再钒渣中除磷的成本,并避免了大量废渣与废液
的产生。
48.【实施例3】
49.在实施例2的基础上,旋转杆2上套装有伸缩杆5,伸缩杆5的一端与反应腔1内底部连接,伸缩杆5的另一端与分隔板3连接,伸缩杆5带动分隔板3在旋转杆2上上下移动。
50.如图3所示,旋转杆2上设置有四个移动槽7,四个移动槽7与四个搅拌片4一一对应,搅拌片4能够在移动槽7内上下移动。如图4所示,搅拌片4与连接杆8的一端连接,连接杆8的另一端与对应的移动槽7连接,搅拌片4通过连接杆8在移动槽7内上下移动。每个移动槽7的上端位于同一水平直线上。每个移动槽7的下端不位于同一水平直线上,即每个移动槽的长度不同,当分隔板位于原始状态即旋转杆的最下方时,四个搅拌片位于旋转杆的不同高度上,进而能够提高搅拌效率。旋转杆2上设置有四个搅拌片4,四个搅拌片4能够组成一个圆形,分隔板3上设置有用于放置四个搅拌片4的放置槽6,如图5所示。放置槽6的形状与四个搅拌片4组成的圆形的形状相同。
51.在使用时,分隔板向上移动,接触到一个搅拌片时,分隔板会带动该搅拌片一起向上移动,搅拌片在移动槽中一起向上移动,当分隔板移动到最上方的位置时,四个搅拌片位于同一水平平面上,并且组成一个圆,位于分隔板上的放置槽中,如图6所示。当分隔板向下移动时,搅拌片在重力的作用下自动在移动槽中向下移动,即恢复到原始状态中,在本实施例中,这样的结构设置不需要使用其他结构调节搅拌片的位置,能进一步的简化结构,提高使用效率。其中,搅拌片、分隔板、放置槽的结构的俯视图如图7所示,即使旋转杆带动搅拌片旋转也不会影响搅拌片放置在放置槽中。本装置的旋转杆2的长度为反应腔1内部高度的四分之三。移动槽的上端与旋转杆的上端之间的距离为5cm,分隔板与反应腔均为圆形,分隔板与反应腔内壁之间通过凹槽和固定杆连接,并且固定杆可在凹槽内沿竖直方向上下移动。搅拌片为扇形。
52.本文中所使用的“第一”、“第二”等只是为了描述清楚起见而对相应部件进行区别,不旨在限制任何次序或者强调重要性等。此外,在本文中使用的术语“连接”在不进行特别说明的情况下,可以是直接相连,也可以使经由其他部件间接相连。
53.以上所述的具体实施方式,对本发明的目的、技术方案和有益效果进行了进一步详细说明,所应理解的是,以上所述仅为本发明的具体实施方式而已,并不用于限定本发明的保护范围,凡在本发明的精神和原则之内,所做的任何修改、等同替换、改进等,均应包含在本发明的保护范围之内。