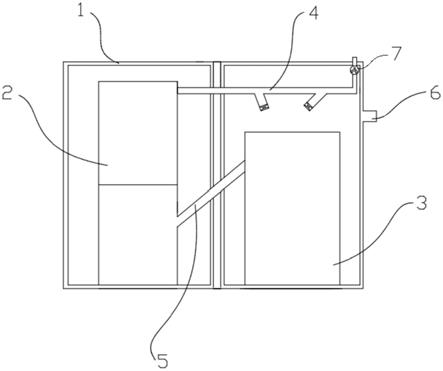
1.本实用新型涉及淬火炉技术领域,尤其涉及一种淬火回火一体炉。
背景技术:
2.淬火是将钢加热到临界温度ac3或ac1以上温度,保温一段时间,使之全部或部分奥氏体化,然后以大于临界冷却速度的冷速快冷到ms以下进行马氏体转变的热处理工艺;回火是将经过淬火的工件重新加热到低于下临界温度ac1的适当温度,保温一段时间后在空气或水、油等介质中冷却的金属热处理工艺,或将淬火后的合金工件加热到适当温度,保温若干时间,然后缓慢或快速冷却。淬火后的工件应及时回火,通过淬火和回火的相配合,才可以获得所需的力学性能。
3.例如,专利cn209685897u,提供了一种方便进料的铝合金淬火炉,包括淬火炉外壳,淬火炉外壳前后两侧均设有支架,淬火炉外壳顶面中心处开设有螺纹孔,淬火炉外壳前侧面靠近其底端的位置开设有穿孔,淬火炉外壳内设有加热仓,淬火炉外壳底面开设有进料口,淬火炉外壳底端设有淬火池,淬火池右侧设有推杆,淬火池底面四角处均设有移动轮,该方便进料的铝合金淬火炉通过打开关闭装置能够自动打开或关闭仓门,同时仓门能够翻转至淬火炉外壳右侧,在进料时仓门不会妨碍到进料。
4.目前,淬火炉和回火炉都是分开设置的,两个炉体通过不同的加热设备进行加热,尤其是淬火炉,需要将工件加热到较高的温度,能耗较高,而且产生的热量无法完全利用会排放到空气中,导致炉体附件的温度较高,使得工作人员操作设备时十分不方便,因此,需要一种可以结合淬火炉和回火炉的设备,使之可以充分利用淬火炉产生的热能,减少能耗。
技术实现要素:
5.有鉴于此,有必要提供一种淬火回火一体炉,解决现有技术中淬火炉和回火炉分开设置能耗较高的技术问题。
6.为达到上述技术目的,本实用新型的技术方案提供一种淬火回火一体炉,其包括:
7.箱体,所述箱体内部中空且竖直设置有隔热板,所述箱体经所述隔热板分割第一放置区和第二放置区;
8.淬火炉,包括有加热仓和淬火池,所述加热仓和所述淬火池均设置于所述第一放置区;
9.回火炉,所述回火炉设置于所述第二放置区且其顶部开口;
10.管道组件,包括通风管道、至少一个辅助管道及其电控阀,所述通风管道的一端连接于所述加热仓、另一端贯穿所述隔热板并穿过所述第二放置区延伸向外,所述辅助管道设置于所述第二放置区且其一端连接于所述通风管道,所述电控阀连接于所述辅助管道的另一端,用以开闭所述辅助管道,以供所述加热仓产生的热量传输至所述第二放置区。
11.进一步的,还包括输送机构,包括输送管、输送带、挡板及驱动件,所述输送管的一端连通至所述淬火池、另一端贯穿所述隔热板连通至所述回火炉,所述输送带内置于所述
输送管,所述挡板设置于所述输送管的另一端,用以封闭所述输送管,所述驱动件设置于所述输送管并连接于所述输送带,用以输送所述淬火池的零件至所述回火炉。
12.进一步的,所述挡板与所述输送管铰接。
13.进一步的,所述淬火池设置于所述加热仓的下方。
14.进一步的,所述第一放置区和所述第二放置区内壁还设置有保温层。
15.进一步的,还包括排气管,所述排气管设置于所述第二放置区。
16.进一步的,所述辅助管道的数量为两个,其对应的所述电控阀的数量也为两个,两个所述辅助管道间隔设置于所述通风管道并相对所述回火炉顶部开口设置,每一所述辅助管道上均设置有一电控阀。
17.进一步的,所述辅助管道倾斜设置。
18.进一步的,还包括风机,所述风机设置于所述第二放置区并连通至所述通风管道。
19.进一步的,还包括温度传感器,所述温度传感器内置于所述回火炉。
20.与现有技术相比,本实用新型的有益效果包括:本实用新型的一体炉将淬火炉和回火炉结合,两个炉体之间通过隔热板分割开,使之可以分别加热至不同的温度,通过通风管道使得淬火炉产生的热量可以传输到回火炉中,通过淬火炉加热产生的热能供零件加热至淬火所需的温度,然后将多余的热能传输至回火炉中,供回火炉中零件加热至回火所需的温度,无需回火炉加热,可以节省能耗。
附图说明
21.图1是本实用新型提供的实施例-淬火回火一体炉的结构示意图;
22.图2是本实用新型提供的实施例-淬火回火一体炉的剖视图;
23.图3是本实用新型提供的实施例-淬火回火一体炉中输送组件的结构示意图。
具体实施方式
24.下面结合附图来具体描述本实用新型的优选实施例,其中,附图构成本技术一部分,并与本实用新型的实施例一起用于阐释本实用新型的原理,并非用于限定本实用新型的范围。
25.参照图1,本实用新型提供了一种淬火回火一体炉,其包括箱体1、淬火炉2、回火炉3和通风组件4,所述淬火炉2和回火炉3间隔设置于所述箱体1内,所述通风组件4设置于所述箱体1内并连通至所述淬火炉1。
26.淬火炉2用于完成零件的加热和淬火,回火炉3用于完成零件的淬火,通风组件4连通至淬火炉2的加热端,用于淬火炉通风散热,还可以将淬火炉2产生的热量传输至回火炉3,用于回火炉3加热,则可以省去回火炉3的加热装置,减少能耗,还可以充分利用淬火炉2产生的热量,减少淬火炉2排放至空气中的热量,以此降低设备周围的温度,方便工作人员操作设备。其中,淬火的温度一般在950-1150℃之间,而回火的温度在150-650℃之间,采用淬火炉产生的热量可以加热回火炉至需要的温度。
27.所述1箱体内部中空且竖直设置有隔热板11,所述箱体1经所述隔热板11分割第一放置区111和第二放置区112,分别用于放置淬火炉2和回火炉3,其中,所述第一放置区111和所述第二放置区112内壁还设置有保温层,使得两个放置区域可以保持不同的温度。
28.所述淬火炉2包括有加热仓21和淬火池22,所述加热仓21和所述淬火池22均设置于所述第一放置区111,分别用于零件的加热和淬火加工,其中,加热仓21内设置有用于零件加热的加热设备,淬火池22内存放有淬火油,所述淬火池22设置于所述加热仓21的下方,加热仓21产生的热空气可以从上方排出,不会影响淬火池22的淬火。
29.所述回火炉3设置于所述第二放置区112且其顶部开口,回火炉3中设置有存放零件的支撑台,回火炉3的壳体采用导热材料制作,便于吸收淬火炉2传输至第二放置区112热量。
30.参照图2,所述管道组件4包括通风管道41、辅助管道42及其电控阀43,所述通风管道的41一端连通至所述加热仓21、另一端贯穿所述隔热板11并穿过所述第二放置区112延伸向外,所述辅助管道42设置于所述第二放置区112且其一端连接于所述通风管道41,所述电控阀43连接于所述辅助管道42的另一端,用以开闭所述辅助管道42,以供所述加热仓21产生的热量传输至所述第二放置区112。其中,辅助管道42的数量为两个,其对应的所述电控阀43的数量也为两个,两个所述辅助管道42间隔设置于所述通风管道41并相对所述回火炉3顶部开口设置,每一所述辅助管道42上均设置有一电控阀43,所述辅助管道42倾斜设置,可以减少对流,方便通风管道41内的热空气传输至第二放置区112中。
31.参照图3,作为优选的实施例,该一体炉还包括输送机构5,所述输送机构5包括输送管51、输送带52、挡板53及驱动件54,所述输送管51的一端连通至所述淬火池22、另一端贯穿所述隔热板11连通至所述回火炉3,所述输送带52内置于所述输送管51,所述挡板53设置于所述输送管51的另一端,用以封闭所述输送管51,所述驱动件54设置于输送管51并连接于所述输送带52,用以输送所述淬火池22的零件至所述回火炉3。其中,所述挡板53与所述输送管51铰接,使得挡板53可以沿输送管53转动,初始状态时,挡板53盖住输送管51,防止回火炉3中的热空气回流至淬火池,零件从淬火池22从传输至回火炉3中时,零件可以推开挡板53,零件下落至回火炉3中后,挡板53则恢复原位重新盖住输送管;驱动件采用电机,电机设置在第二放置区域,用于驱动输送带转动。
32.该一体炉还包括排气管6,所述排气管6设置于所述第二放置区112,用于排出回火炉3中的气体,以此形成气体的循环流通系统。
33.该一体炉还包括风机7,所述风机7设置于所述第二放置区并连通至所述通风管道41,用于加快空气的流通。
34.该一体炉还包括温度传感器(图中未示出),所述温度传感器内置于所述回火炉3,温度传感器和电控阀均连接至控制端,温度传感器可以监测回火炉3中的温度,从而反馈至控制端,使得控制端及时关闭电控阀。
35.本实用新型提供的实施例的工作原理为:本实用新型的一体炉结合了淬火炉和回火炉,可以充分利用淬火炉产生的热量,两个炉体分别设置在箱体的两个放置区域,并通过隔热板和保温层进行隔热,使得两个放置区域可以根据需要分别加热至不同的温度,通过通风管道连通两个放置区域,可以将淬火炉加热产生的热空气引导至回火炉处,利用淬火炉加热至高温产生的热量给回火炉升温,不仅可以节省回火炉加热所需的能耗,还可以减少淬火炉排放至空气的的热量,降低设备周围空气的温度,淬火炉和回火炉之间还设置有运输机构,可以将淬火完的零件快速运输至回火炉,结构简单,使用方便。
36.以上所述,仅为本实用新型较佳的具体实施方式,但本实用新型的保护范围并不
局限于此,任何熟悉本技术领域的技术人员在本实用新型揭露的技术范围内,可轻易想到的变化或替换,都应涵盖在本实用新型的保护范围之内。