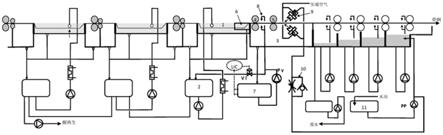
1.本实用新型涉及带钢表面清洗技术领域,尤其涉及一种降低酸洗机组盐酸和脱盐水消耗的机构。
背景技术:
2.现有技术中,运行的带钢在酸洗槽去除氧化铁皮,在漂洗槽去除残留酸液。循环的热酸液
→
注入酸洗槽
→
漫过围挡石
→
溢流槽
→
酸罐
→
酸泵
→
加热器
→
酸洗槽。进入漂洗槽的酸量越多,补充的脱盐水就越多。现有的挤干法,通过4#挤干辊、5#挤干辊的挤干,进入漂洗槽的酸液量可减少到40ml/
㎡
。全年进入漂洗槽的酸液量为6365m3,耗用脱盐水63648m3。现有技术无法减少带钢向漂洗槽带酸,以及减小酸耗和水耗。
技术实现要素:
3.根据上述提出的技术问题,而提供一种降低酸洗机组盐酸和脱盐水消耗的机构。本实用新型主要通过设置的相对独立的预漂洗系统,利用返回法将预漂洗环节漂洗下来的盐酸返回酸洗段,大幅度减少了带钢带入漂洗槽的盐酸量,减少酸耗和水耗。本实用新型采用的技术手段如下:
4.一种降低酸洗机组盐酸和脱盐水消耗的机构,包括1#酸洗槽、2#酸洗槽、3#酸洗槽、1#酸罐、2#酸罐、3#酸罐、1#挤干辊、2#挤干辊、3#挤干辊、4#挤干辊、5#挤干辊、脱盐水罐、冲洗水罐,每个酸洗槽的左右两侧均设有溢流槽,分别为1#溢流槽、2#溢流槽、3#溢流槽、4#溢流槽,连接顺序依次为:1#溢流槽、1#酸洗槽、2#溢流槽、2#酸洗槽、3#溢流槽、3#酸洗槽、4#溢流槽依次相互连接;每个酸洗槽与两侧的溢流槽间均设有围挡石,1#酸洗槽和2#酸洗槽出口的溢流漫过围挡石,分别流入2#溢流槽和3#溢流槽;1#酸罐、2#酸罐、3#酸罐各通过酸泵和酸液加热器分别与1#酸洗槽、2#酸洗槽、3#酸洗槽相连,1#酸洗槽两侧的溢流槽均与1#酸罐相连,2#酸洗槽两侧的溢流槽均与2#酸罐相连,3#酸洗槽进口侧的3#溢流槽与3#酸罐相连,1#酸洗槽、2#酸洗槽、3#酸洗槽中分别设有1#挤干辊、2#挤干辊、3#挤干辊,4#溢流槽中设有4#挤干辊、5#挤干辊;其特征在于,
5.所述3#酸洗槽出口侧的两个槽壁各开设一个侧壁溢流口,通过管线将2个侧壁溢流口并联,共同连接入3#酸罐,3#酸洗槽出口的溢流不再漫过围挡石,而是通过侧壁溢流口,直接流入3#酸罐;
6.所述4#溢流槽分别连接3#酸罐、预漂洗罐,所述预漂洗罐通过管线一分别与3#酸罐、多个预漂洗喷嘴相连,其中管线一分叉为管线二和管线三,管线二与多个预漂洗喷嘴相连,管线三与3#酸罐相连;多个预漂洗喷嘴设置在所述4#挤干辊与所述5#挤干辊之间,向带钢喷射预漂洗水;所述预漂洗水罐中储存预漂洗水,为预漂洗喷嘴喷射预漂洗水提供循环,预漂洗水罐的容积为5m3;管线一上靠近预漂洗水罐的位置设有预漂洗循环泵,为预漂洗喷射提供动能,其输送的流量为20m3/h;管线三上设有控制阀;
7.预漂洗循环泵将预漂洗罐内的预漂洗水抽出,经管线一和管线二输送到预漂洗喷
嘴中,再喷射到带钢表面,经5#挤干辊的挤干后落入4#溢流槽中,之后,再落入预漂洗罐中;通过预漂洗降低3#酸洗槽出口带钢板面盐酸浓度;
8.预漂洗循环泵还将预漂洗罐内的部分预漂洗水抽出,经管线一和管线三输送回3#酸罐中,3#酸罐内的酸液经酸泵和酸液加热器处理后再经上方的侧喷口输送到3#酸洗槽中对带钢进行酸洗。
9.进一步地,所述预漂洗喷嘴在带钢的上下各设置一排,每排设置30个预漂洗喷嘴;预漂洗喷嘴压力为0.2mpa。
10.进一步地,所述预漂洗罐的液位高于60%时,控制阀打开,向3#酸罐中输送预漂洗水;液位低于50%时,控制阀关闭,停止输送预漂洗水。
11.进一步地,所述5#挤干辊的后面设置有多个雾化喷嘴,在带钢的上下各设置一排雾化喷嘴,均连接压缩空气和脱盐水罐,脱盐水罐经脱盐水泵、脱盐水管路向雾化喷嘴中输送脱盐水,对带钢进行雾化喷洗;雾化喷洗水对带钢表面雾化喷洗后,落入3#酸洗槽出口侧的4#溢流槽中,之后,再落入预漂洗罐,作为预漂洗的循环水。
12.进一步地,每排所述雾化喷嘴各设置30个,喷洗总水量为600l/h,喷嘴压力为5mpa;单个雾化喷嘴喷雾量为10l/h;脱盐水的水源压力为0.1~0.3mpa,压缩空气的气源压力为0.5~1mpa。
13.进一步地,所述雾化喷嘴进行雾化喷洗时喷出扇形高压小流量喷洗水。
14.进一步地,所述脱盐水管路上设有节流阀。
15.进一步地,所述预漂洗水的水源来自雾化喷洗带钢板面后的雾化喷洗水,为1.02m3/h的盐酸+0.64m3/h的脱盐水,脱盐水的ph值≥7。
16.进一步地,所述侧壁溢流口的高度h为80mm,长度l为1000mm。
17.较现有技术相比,本实用新型具有以下优点:
18.1、本实用新型提供的降低酸洗机组盐酸和脱盐水消耗的机构,设置的相对独立的预漂洗系统与现有的漂洗技术存在本质区别,利用返回法将预漂洗环节漂洗下来的盐酸返回酸洗段,大幅度减少了带钢带入漂洗槽的盐酸量,减少酸耗和水耗。
19.2、本实用新型提供的降低酸洗机组盐酸和脱盐水消耗的机构,通过吹扫法,进一步净化了进入漂洗槽的带钢板面。
20.3、本实用新型提供的降低酸洗机组盐酸和脱盐水消耗的机构,利用稀释法,通过预漂洗环节稀释了带钢板面的酸液浓度。通过预漂洗水的返回,对85℃热酸液的蒸发进行了补充。
21.4、本实用新型提供的降低酸洗机组盐酸和脱盐水消耗的机构,通过上述方法,将带入漂洗槽的酸液量从40ml/
㎡
减少到10ml/
㎡
;带入漂洗槽的酸液浓度从200g/l降到120g/l。漂洗耗水从10.2m3/h降到2.2m3/h。
22.基于上述理由本实用新型可在降低酸洗机组盐酸和脱盐水消耗等领域广泛推广。
附图说明
23.为了更清楚地说明本实用新型实施例或现有技术中的技术方案,下面将对实施例或现有技术描述中所需要使用的附图做以简单地介绍,显而易见地,下面描述中的附图是本实用新型的一些实施例,对于本领域普通技术人员来讲,在不付出创造性劳动性的前提
下,还可以根据这些附图获得其他的附图。
24.图1为现有技术的结构示意图。
25.图2为现有技术的回酸路线示意图。
26.图3为本实用新型的结构示意图。
27.图4为本实用新型的局部放大图。
28.图5为本实用新型的回酸路线示意图。
29.图6为本实用新型的侧壁溢流槽侧视示意图。
30.图中:1、3#酸洗槽;2、3#酸罐;3、4#溢流槽;4、4#挤干辊;5、5#挤干辊;6、侧壁溢流口;7、预漂洗罐;8、预漂洗喷嘴;9、雾化喷嘴;10、节流阀;11、脱盐水罐;v1、控制阀;pv、预漂洗循环泵;pp、脱盐水泵。
具体实施方式
31.为使本实用新型实施例的目的、技术方案和优点更加清楚,下面将结合本实用新型实施例中的附图,对本实用新型实施例中的技术方案进行清楚、完整地描述,显然,所描述的实施例是本实用新型一部分实施例,而不是全部的实施例。基于本实用新型中的实施例,本领域普通技术人员在没有做出创造性劳动前提下所获得的所有其他实施例,都属于本实用新型保护的范围。
32.如图所示,本实用新型提供了一种降低酸洗机组盐酸和脱盐水消耗的机构,包括1#酸洗槽、2#酸洗槽、3#酸洗槽1、1#酸罐、2#酸罐、3#酸罐2、1#挤干辊、2#挤干辊、3#挤干辊、4#挤干辊4、5#挤干辊5、脱盐水罐11、冲洗水罐等,每个酸洗槽的左右两侧均设有溢流槽,分别为1#溢流槽、2#溢流槽、3#溢流槽、4#溢流槽3,连接顺序依次为:1#溢流槽、1#酸洗槽、2#溢流槽、2#酸洗槽、3#溢流槽、3#酸洗槽1、4#溢流槽3依次相互连接;每个酸洗槽与两侧的溢流槽间均设有围挡石,1#酸洗槽和2#酸洗槽出口的溢流漫过围挡石,分别流入2#溢流槽和3#溢流槽;1#酸罐、2#酸罐、3#酸罐2各通过酸泵和酸液加热器分别与1#酸洗槽、2#酸洗槽、3#酸洗槽1相连,1#酸洗槽两侧的溢流槽均与1#酸罐相连,2#酸洗槽两侧的溢流槽均与2#酸罐相连,3#酸洗槽1进口侧的3#溢流槽与3#酸罐2相连,1#酸洗槽、2#酸洗槽、3#酸洗槽1中分别设有1#挤干辊、2#挤干辊、3#挤干辊,4#溢流槽3中设有4#挤干辊4、5#挤干辊5;其特征在于,
33.所述3#酸洗槽1出口侧的两个槽壁各开设一个侧壁溢流口6,通过管线将2个侧壁溢流口6并联,共同连接入3#酸罐2,3#酸洗槽1出口的溢流不再漫过围挡石,而是通过侧壁溢流口6,直接流入3#酸罐2;
34.所述4#溢流槽3分别连接3#酸罐2、预漂洗罐7,所述预漂洗罐7通过管线一分别与3#酸罐2、多个预漂洗喷嘴8相连,其中管线一分叉为管线二和管线三,管线二与多个预漂洗喷嘴8相连,管线三与3#酸罐2相连;多个预漂洗喷嘴8设置在所述4#挤干辊4与所述5#挤干辊5之间,向带钢喷射预漂洗水;所述预漂洗水罐中储存预漂洗水,为预漂洗喷嘴8喷射预漂洗水提供循环,预漂洗水罐的容积为5m3;管线一上靠近预漂洗水罐的位置设有预漂洗循环泵pv,为预漂洗喷射提供动能,其输送的流量为20m3/h;管线三上设有控制阀v1;
35.预漂洗循环泵pv将预漂洗罐7内的预漂洗水抽出,经管线一和管线二输送到预漂洗喷嘴8中,再喷射到带钢表面,经5#挤干辊5的挤干后落入4#溢流槽3中,之后,再落入预漂
洗罐7中;即预漂洗水循环回路为:预漂洗罐7-预漂洗喷嘴8-4#溢流槽3-预漂洗罐7;通过预漂洗降低3#酸洗槽1出口带钢板面盐酸浓度;
36.预漂洗循环泵pv还将预漂洗罐7内的部分预漂洗水抽出,经管线一和管线三输送回3#酸罐2中,3#酸罐2内的酸液经酸泵和酸液加热器处理后再经上方的侧喷口输送到3#酸洗槽1中对带钢进行酸洗;预漂洗水向3#酸罐2的输送,实际上是将3#酸洗槽1带出的酸液返回到3#酸洗槽1,返回酸液的作用为:一是对按现有技术被带入漂洗槽的酸液进行了转移;二是对酸液的蒸发补充。
37.作为优选的实施方式,所述预漂洗喷嘴8在带钢的上下各设置一排,每排设置30个预漂洗喷嘴8;预漂洗喷嘴8压力为0.2mpa。
38.作为优选的实施方式,所述预漂洗罐7的液位高于60%时,控制阀v1打开,向3#酸罐2中输送预漂洗水;液位低于50%时,控制阀v1关闭,停止输送预漂洗水。
39.作为优选的实施方式,所述5#挤干辊5的后面设置有多个雾化喷嘴9,在带钢的上下各设置一排雾化喷嘴9,均连接压缩空气和脱盐水罐11,脱盐水罐11经脱盐水泵pp、脱盐水管路向雾化喷嘴9中输送脱盐水,对带钢进行雾化喷洗;雾化喷洗水(来自脱盐水罐(11)的脱盐水,ph值≥7)对带钢表面雾化喷洗后,落入3#酸洗槽1出口侧的4#溢流槽3中,之后,再落入预漂洗罐7,作为预漂洗的循环水。雾化喷洗的作用:用较少的水及较高的压力对带钢板面清洗和吹扫,进一步减少带出量并降低板面微量残余酸的浓度。
40.作为优选的实施方式,每排所述雾化喷嘴9各设置30个,喷洗总水量为600l/h,喷嘴压力为5mpa;单个雾化喷嘴9喷雾量为10l/h;脱盐水的水源压力为0.1~0.3mpa,压缩空气的气源压力为0.5~1mpa。
41.作为优选的实施方式,所述雾化喷嘴9进行雾化喷洗时喷出扇形高压小流量喷洗水,对已经降低了酸液浓度和带出量的带钢板面再次清洗和清扫,进一步减少了带入漂洗槽的酸量和浓度。
42.作为优选的实施方式,所述脱盐水管路上设有节流阀10。
43.作为优选的实施方式,所述预漂洗水的水源来自雾化喷洗带钢板面后的雾化喷洗水,为1.02m3/h(200g/l)的盐酸+0.64m3/h的脱盐水,脱盐水的ph值≥7。
44.作为优选的实施方式,所述侧壁溢流口6的高度h为80mm,长度l为1000mm。
45.实施例1
46.如图1和图2所示,为现有技术,现有技术中的回酸路线是经溢流槽流回3#酸罐2中,无法减少带钢向漂洗槽带酸,减少酸耗和水耗。
47.为了解决现有技术的问题,如图3-6所示,本实用新型3#酸洗槽1出口两边(传动侧和操作侧)的槽壁,各开一个侧壁溢流口6。通过管线将2个侧壁溢流口6并联,再接入3#酸罐2。断开3#酸洗槽1出口的4#溢流槽3到3#酸罐2的连通管路。设置侧壁溢流口6起到的作用:生产时,3#酸洗槽1出口的溢流不再漫过围挡石,而是通过侧壁溢流口6,直接进入3#酸罐2。3#酸洗槽1出口的4#溢流槽3,不再经流3#酸洗槽1的酸液。
48.本实施例中,在4#挤干辊4的后面设置预漂洗喷嘴8,在带钢的上、下方各设置一排,每排设置30个预漂洗喷嘴8,向带钢喷射预漂洗水。喷嘴压力为0.2mpa。还设置有预漂洗水罐7,储存预漂洗水,为预漂洗喷射提供循环。容积为5m3。同时设置有预漂洗循环泵pv,为预漂洗喷射提供动能,其输送的流量为20m3/h。预漂洗的作用:降低3#酸洗槽出口带钢板面
盐酸浓度。
49.本实施例中,在5#挤干辊5的后面设置雾化喷嘴9,在带钢的上、下方各设置一排,每排设置30个雾化喷嘴9,接压缩空气和脱盐水。喷嘴压力为5mpa;单个喷嘴喷雾量为10l/h;水源压力为0.1~0.3mpa;气源压力为0.5~1mpa。脱盐水管路连接脱盐水泵pp出口端。喷洗总水量为600l/h。雾化喷洗的作用:用较少的水及较高的压力对带钢板面清洗和吹扫,进一步减少带出量并降低板面微量残余酸的浓度。
50.一、雾化喷洗水
51.1.雾化喷洗水的来源。来自脱盐水罐的脱盐水,ph值≥7。
52.2.雾化喷洗水的去向。雾化喷洗水对带钢表面雾化喷洗后,落入3#酸洗槽出口的4#溢流槽,再落入预漂洗罐,作为预漂洗的循环水。
53.二、预漂洗水
54.1.预漂洗水的水源。来自雾化喷洗带钢板面后的雾化喷洗水。
55.2.预漂洗水的成分。1.02m3/h(200g/l)的盐酸+0.64m3/h(ph值≥7)的脱盐水。
56.3.预漂洗水的去向。预漂洗循环泵pv将预漂洗罐内的预漂洗水抽出,喷射到带钢表面,经5#挤干辊的挤干后落入4#溢流槽,再落入预漂洗罐。预漂洗水循环回路:预漂洗罐-预漂洗喷嘴-4#溢流槽-预漂洗罐。
57.三、雾化喷洗
58.雾化喷洗喷出扇形高压小流量喷洗水,对已经降低了酸液浓度和带出量的板面再次清洗和清扫,进一步减少了带入漂洗槽的酸量和浓度。
59.四、预漂洗水的输送
60.1.预漂洗罐的液位控制。液位高于60%时,控制阀vl打开,向3#酸罐输送预漂洗水;液位低于50%时,控制阀vl关闭,停止输送。控制阀v1的开闭状态由液位检测控制器lic控制。
61.2.返回酸液。预漂洗水向3#酸罐的输送,实际上是将3#酸洗槽带出的酸液返回到3#酸洗槽。
62.3.返回酸液的作用。一是对按现有技术被带入漂洗槽的酸液进行了转移;二是对酸液的蒸发补充。
63.五、原理
64.1.挤干法。现有技术用挤干方法减少带出量。由于辊面与酸液的粘带,不能彻底去除带钢表面盐酸。挤干辊具有周期性,上机后磨损不断增加,带出量也不断增加。
65.2.稀释法。本实用新型用雾化喷洗的脱盐水稀释从带钢板面的酸液浓度,使进入漂洗槽的酸浓度降低。
66.3.返回法。在挤干法中,将带钢表面挤干后的残余酸,直接带入漂洗槽。本实用新型对带钢表面挤干后的残余酸进行预漂洗、雾化喷洗,再将预漂洗水返回酸洗段,一方面减少了酸液的损失;另一方面大幅度降低了带入漂洗槽的酸液量。
67.4.吹扫法。通过雾化喷洗,再次净化了带钢表面。
68.5.公式法。每平方米带钢的耗水量公式为:
69.f=q
×
(c0/c4)
1/4
;
70.式中,q为带入漂洗槽的酸量;c0为带入漂洗槽的酸浓度;c4为末级漂洗水的酸浓
度。
71.本实用新型通过稀释法降低了c0;通过吹扫法和返回法,降低了q,因而大大降低了漂洗段脱盐水的消耗。
72.5、比较例
73.现有技术与本实用新型比较表:
74.方法/比较项带酸量酸损/年耗水费用现有技术40ml/m26364.8m363648m3420.24万实施例110ml/m21591.2m314003m3101.56万节省30ml/m24773.6m349645m3318.11万
75.附:相关数据和概念。
76.1.机组产能:200万吨。
77.2.带钢宽度:900-1900mm。
78.3.年净作业时间:260天。
79.4.带钢带入漂洗槽的酸浓度(c0):现有技术为200g/l;实施例1为120g/l。
80.5.带钢带入漂洗槽的酸液量(q):现有技术为40ml/
㎡
;实施例1为10ml/
㎡
。
81.6.第4级漂洗槽要求的酸浓度(c4):20mg/l。
82.7.f-每平方米带钢消耗的新鲜脱盐水量,m3/
㎡
。
83.8.一般的酸洗速度为170m/min。
84.9.中间规格带钢宽度为1250mm。
85.10.现有技术年均酸液损耗:
86.40ml/
㎡×
1.25m
×
170m/min
×2×
60min
×
24h
×
260天=6364.8m3。
87.11.实施例1年均酸液损耗:
88.10ml/
㎡×
1.25m
×
170m/min
×2×
60min
×
24h
×
260天=1591.2m3。
89.12.现有技术每平方米带钢消耗脱盐水:
90.f=q
×
(c0/c4)1/n=0.00004m3/
㎡×
(200g/l
÷
0.02g/l)1/4=0.0004m3。
91.13.实施例1每平方米带钢消耗脱盐水:
92.f=q
×
(c0/c4)1/n=0.00001m3/
㎡×
(120g/l
÷
0.02g/l)1/4=0.000088m3。
93.14.现有技术漂洗槽年均消耗脱盐水:
94.t=1.25m
×
170m/min
×2×
60min
×
24h
×
260天
×
0.0004m3/
㎡
=63648m3。
95.15.实施例1漂洗槽年均消耗脱盐水:
96.t=1.25m
×
170m/min
×2×
60min
×
24h
×
260天
×
0.000088m3/
㎡
=14003m3。
97.最后应说明的是:以上各实施例仅用以说明本实用新型的技术方案,而非对其限制;尽管参照前述各实施例对本实用新型进行了详细的说明,本领域的普通技术人员应当理解:其依然可以对前述各实施例所记载的技术方案进行修改,或者对其中部分或者全部技术特征进行等同替换;而这些修改或者替换,并不使相应技术方案的本质脱离本实用新型各实施例技术方案的范围。