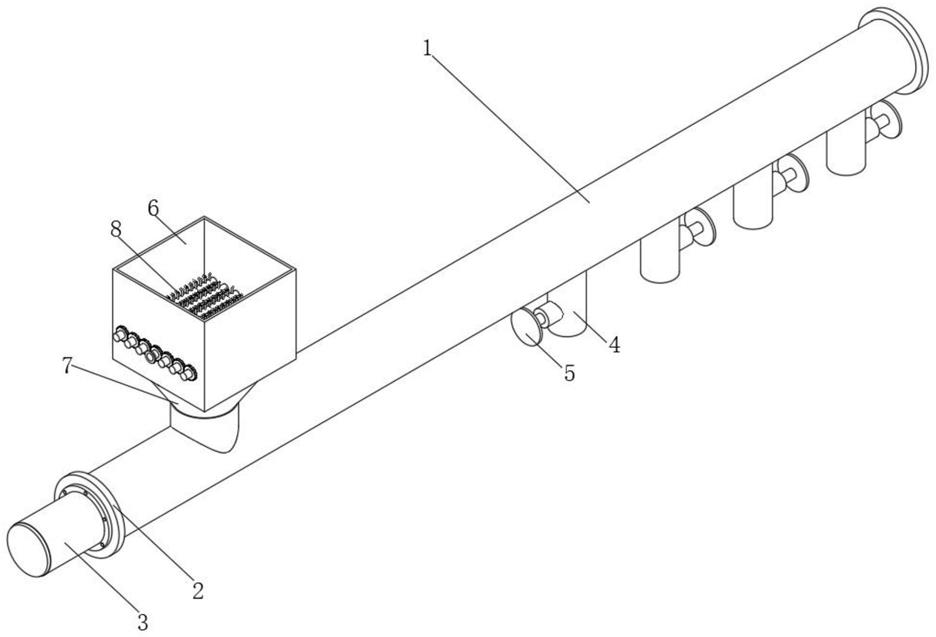
1.本实用新型涉及连铸设备领域,特别涉及一种连铸用自动加渣装置。
背景技术:
2.连铸用自动加渣装置是一种在连铸工作中添加保护渣的装置,通常有震动下料和螺旋下料的两种,震动下料是一种将保护渣放置在料筒内,然后由振动电机工作将保护渣振动下落,螺旋下料是由电机带动螺旋叶片转动,推动保护渣从下料管下落;
3.但是现有的连铸用自动加渣装置在使用时存在着一定的不足之处有待改善,首先,现有的连铸用自动加渣装置不具备捻料功能,因保护渣存在着因粘黏结块的现象,在下料的时候,成块的保护渣直接落入到连铸设备内会严重影响保护效果;其次,现有的连铸用自动加渣装置不具备分料功能,下料位置固定,无法适用于各种不同的连铸设备,也无法同时使用在多个连铸设备上。
技术实现要素:
4.本实用新型的主要目的在于提供一种连铸用自动加渣装置,可以有效解决背景技术中:现有的连铸用自动加渣装置不具备捻料功能,因保护渣存在着因粘黏结块的现象,在下料的时候,成块的保护渣直接落入到连铸设备内会严重影响保护效果;其次,现有的连铸用自动加渣装置不具备分料功能,下料位置固定,无法适用于各种不同的连铸设备,也无法同时使用在多个连铸设备上的技术问题。
5.为实现上述目的,本实用新型采取的技术方案为:
6.一种连铸用自动加渣装置,包括输送筒,所述输送筒的一端固定连接有连接法兰,所述连接法兰的前部安装有电机,所述输送筒的外部安装有下料管,所述下料管的外部安装有蝶阀,所述输送筒的外部靠近一端位置安装有下料斗,所述下料斗的上部安装有储料槽,所述储料槽的内部设有捻料结构,所述输送筒的内部转动连接有转轴,所述转轴的外部设有螺旋叶片。
7.作为本实用新型的进一步方案,所述捻料结构包括有第一旋轴、第二旋轴、捻料齿、主动齿轮、皮带盘和从动齿轮,所述第一旋轴和第二旋轴转动连接在储料槽的内部,所述捻料齿固定连接在第一旋轴的外部,所述主动齿轮固定安装在第一旋轴的外部,所述皮带盘固定连接在第一旋轴的外部一端位置,所述从动齿轮固定安装在第二旋轴的外部。
8.作为本实用新型的进一步方案,所述主动齿轮和从动齿轮齿合连接,所述第一旋轴和第二旋轴的捻料齿交错排列。
9.作为本实用新型的进一步方案,所述第二旋轴的数量为六个,所述第一旋轴位于六个第二旋轴中间位置。
10.作为本实用新型的进一步方案,所述储料槽的形状为矩形,所述储料槽与下料斗连通,且下料斗的形状为锥形。
11.作为本实用新型的进一步方案,所述捻料齿由六根圆柱杆组成,六根圆柱杆圆形
等距设置。
12.与现有技术相比,本实用新型具有如下有益效果:本实用新型中,通过设置捻料结构,利用外部动力装置通过皮带盘带动第一旋轴转动,第一旋轴带动捻料齿和主动齿轮转动,主动齿轮带动从动齿轮转动,从动齿轮带动其外部的捻料齿转动,使得成块的保护渣被破碎落入到下料斗的内部,解决了传统加渣装置不具备捻料功能,避免成块的物料落入到连铸设备内影响保护渣的保护效果,提高了使用性能;
13.通过设置下料管和蝶阀,解决了传统加渣装置下料位置固定单一的现象,一方面能够使得物料下落至不同位置的连铸设备,另一方面也能够同时将物料加入到多个连铸设备中,实用性更高。
附图说明
14.图1为本实用新型一种连铸用自动加渣装置的整体结构示意图;
15.图2为本实用新型一种连铸用自动加渣装置的输送筒的剖析图;
16.图3为本实用新型一种连铸用自动加渣装置的储料槽俯视图。
17.图中:1、输送筒;2、连接法兰;3、电机;4、下料管;5、蝶阀;6、储料槽;7、下料斗;8、捻料结构;9、转轴;10、螺旋叶片;11、第一旋轴;12、第二旋轴;13、捻料齿;14、主动齿轮;15、皮带盘;16、从动齿轮。
具体实施方式
18.为使本实用新型实现的技术手段、创作特征、达成目的与功效易于明白了解,下面结合具体实施方式,进一步阐述本实用新型。
19.如图1-3所示,一种连铸用自动加渣装置,包括输送筒1,输送筒1的一端固定连接有连接法兰2,连接法兰2的前部安装有电机3,输送筒1的外部安装有下料管4,下料管4的外部安装有蝶阀5,输送筒1的外部靠近一端位置安装有下料斗7,下料斗7的上部安装有储料槽6,储料槽6的内部设有捻料结构8,输送筒1的内部转动连接有转轴9,转轴9的外部设有螺旋叶片10。
20.本实施例中,为了解决传统加渣装置不具备捻料功能,在下料时易出现成块现象的问题设置了捻料结构8,捻料结构8包括有第一旋轴11、第二旋轴12、捻料齿13、主动齿轮14、皮带盘15和从动齿轮16,第一旋轴11和第二旋轴12转动连接在储料槽6的内部,捻料齿13固定连接在第一旋轴11的外部,主动齿轮14固定安装在第一旋轴11的外部,皮带盘15固定连接在第一旋轴11的外部一端位置,从动齿轮16固定安装在第二旋轴12的外部,解决了传统加渣装置无法对粘接成块的物料进行破碎,避免成块的保护渣影响保护效果。
21.此外,主动齿轮14和从动齿轮16齿合连接,第一旋轴11和第二旋轴12的捻料齿13交错排列,通过主动齿轮14带动从动齿轮16转动,使得第一旋轴11和第二旋轴12转动。
22.本实施例中,第二旋轴12的数量为六个,第一旋轴11位于六个第二旋轴12中间位置。
23.本实施例中,储料槽6的形状为矩形,储料槽6与下料斗7连通,且下料斗7的形状为锥形。
24.此外,捻料齿13由六根圆柱杆组成,六根圆柱杆圆形等距设置,圆柱杆在捻碎成块
保护渣的同时避免损伤保护渣。
25.需要说明的是,本实用新型为一种连铸用自动加渣装置,在使用时,将保护渣放置到储料槽6的内部,利用外部动力装置通过皮带盘15带动第一旋轴11转动,第一旋轴11带动捻料齿13和主动齿轮14转动,主动齿轮14带动从动齿轮16转动,从动齿轮16带动其外部的捻料齿13转动,使得成块的保护渣被破碎落入到下料斗7的内部,随之保护渣落入到输送筒1的内部,电机3工作,其输出轴带动转轴9转动,转轴9带动螺旋叶片10转动,使得保护渣被输送至下料管4的位置,人们通过打开不同下料管4的蝶阀5,使得保护罩通过不同的下料管4落下,进入到不同的连铸设备内,也可以通过控制蝶阀5不同的开合度,使得物料可以同时从两个以上的下料管4落下。
26.本实用新型通过设置捻料结构8,利用外部动力装置通过皮带盘15带动第一旋轴11转动,第一旋轴11带动捻料齿13和主动齿轮14转动,主动齿轮14带动从动齿轮16转动,从动齿轮16带动其外部的捻料齿13转动,使得成块的保护渣被破碎落入到下料斗7的内部,解决了传统加渣装置不具备捻料功能,避免成块的物料落入到连铸设备内影响保护渣的保护效果,提高了使用性能;通过设置下料管4和蝶阀5,解决了传统加渣装置下料位置固定单一的现象,一方面能够使得物料下落至不同位置的连铸设备,另一方面也能够同时将物料加入到多个连铸设备中,实用性更高。
27.以上显示和描述了本实用新型的基本原理和主要特征和本实用新型的优点。本行业的技术人员应该了解,本实用新型不受上述实施例的限制,上述实施例和说明书中描述的只是说明本实用新型的原理,在不脱离本实用新型精神和范围的前提下,本实用新型还会有各种变化和改进,这些变化和改进都落入要求保护的本实用新型范围内。本实用新型要求保护范围由所附的权利要求书及其等效物界定。