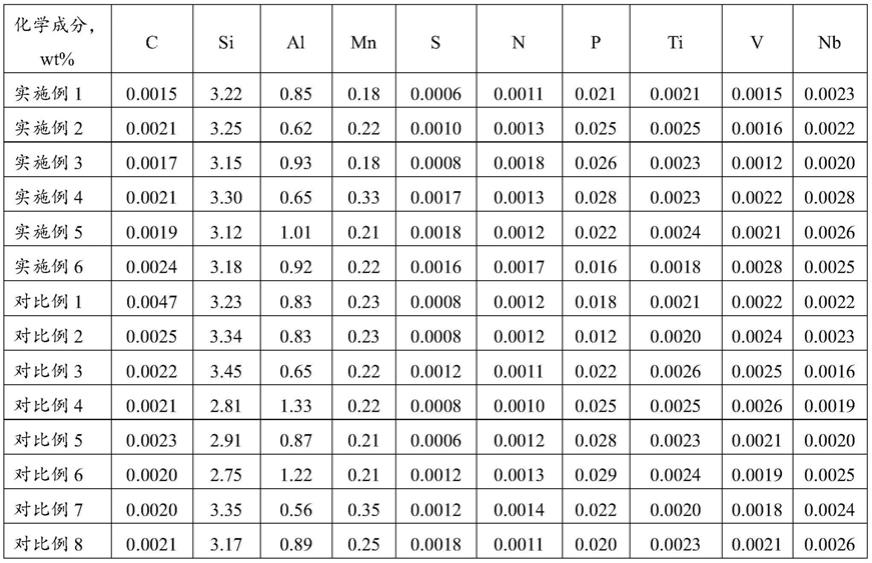
1.本发明属于钢铁冶炼技术领域,涉及一种超低铁损无取向硅钢的生产方法,还涉及一种采用所述生产方法制备得到的超低铁损无取向硅钢。
背景技术:
2.无取向硅钢是广泛应用于马达、变压器的铁芯材料,因此需要具有良好的磁性能,包括更低的铁损和更高的磁感应强度。近年来,随着电机能效的不断提升和节能环保意识的加强,对电器效率的要求也越来越高,而提高电器效率的其中一个措施就是改善铁芯材料的磁性能,制备出更低铁损的无取向硅钢。
3.为得到更低铁损的无取向硅钢,高牌号无取向硅钢中的硅、铝合金元素含量不断提高。然而,随着硅、铝合金元素含量的提高,钢带的韧性急剧下降而脆性增加,在冷轧过程中极易出现断带事故,影响冷轧的轧制效率和成材率。
4.现有的超低铁损无取向硅钢的生产过程中,为了降低轧制断带率,通常在轧前增设加热系统以提高轧件温度,增加轧件塑性,然而这种方式的加热设备投入大,能耗高,成本大幅提高。
技术实现要素:
5.本发明的目的在于提供一种超低铁损无取向硅钢及其生产方法,以解决现有技术中在制备低铁损无取向硅钢时冷轧断带率高、成材率低的技术问题。
6.为实现上述目的之一,本发明一实施方式提供了一种高牌号无取向硅钢的生产方法,所述生产方法包括以下工序,
7.冶炼:依次采用铁水脱硫、转炉冶炼、rh炉精炼进行冶钢,最终所得钢水化学成分以质量百分比计为:c≤0.003%、si:2.8~3.4%、mn:0.1~0.5%、al:0.6~1.3%、s≤0.0015%、n≤0.0020%、p≤0.03%、ti≤0.003%、v≤0.003%、nb≤0.003%,且同时满足3.80%≤si+al≤4.15%,其余为fe以及不可避免的杂质;
8.连铸:将冶炼所得钢水连铸成连铸坯;
9.热轧:对连铸坯加热后经过多道次轧制得到热轧卷板;
10.切边:对热轧卷板的两侧边部进行剪切;
11.常化酸洗:常化温度为900~930℃,常化时间为30~60s;
12.冷轧:经多道次冷轧成厚度为0.35~0.5mm的无取向硅钢,其中,第一道次冷轧时的压下率≥37%,轧制速率为70~180m/min。
13.优选地,所述冶炼工序中,最终所得钢水化学成分以质量百分比计为:c≤0.003%、si:2.8~3.4%、mn:0.1~0.5%、al:0.6~1.3%、s≤0.0010%、n≤0.0015%、p≤0.03%、ti≤0.003%、v≤0.003%、nb≤0.003%,且同时满足3.80%≤si+al≤4.15%,其余为fe以及不可避免的杂质。
14.优选地,所述热轧工序中,制备得到的热轧卷板的厚度为1.9~2.3mm,热轧卷板的
中部与边部的厚度之差为20~40μm,热轧卷板的两个边部之间的厚度之差≤22μm。
15.优选地,所述热轧工序中,将所得连铸坯加热到1080~1130℃并保温30~50min。
16.优选地,所述热轧工序中,热轧的终轧温度为830~870℃,卷取温度为620~680℃。
17.优选地,所述切边工序中,单侧的剪切宽度≥20mm。
18.优选地,常化后的钢带的平均晶粒直径为130~150μm。
19.优选地,所述生产方法还包括:将冷轧所得的冷硬钢卷采用连续退火炉进行成品退火,成品退火温度为950~1000℃,退火时间为20~30s;退火后的钢带经冷却、涂层和精整得到无取向硅钢成品。
20.为实现上述发明目的,本发明一实施方式还提供了一种超低铁损无取向硅钢,采用如上所述的生产方法制备而成。
21.优选地,所得超低铁损无取向硅钢成品的厚度为0.5mm,其铁损p
1.5/50
≤2.35w/kg,磁感应强度b
5000
≥1.66t;或者,所得超低铁损无取向硅钢成品的厚度为0.35mm,其铁损p
1.5/50
≤2.10w/kg,磁感应强度b
5000
≥1.65t。
22.与现有技术相比,本发明的有益效果为:
23.(1)在化学成分设计方面,通过si、al含量增加,可以最大限度降低铁损,同时配合s和n等元素含量的控制,降低热轧工序中析出细小mns、aln的几率,以及结合对n、ti、v、nb元素含量的管控,保证磁性能,实现低铁损和高磁感应强度。
24.(2)通过组分配比,结合工艺设计,不仅可以使制备得到的无取向硅钢组织均匀、具有较低的铁损和优异的磁感应性能,满足其在马达、变压器等产品中的应用能效,而且通过优化热轧、切边、常化以及冷轧工序等加工工艺,提高制备的无取向硅钢的韧性,避免硅钢在冷轧工序中由于脆性高而导致的频繁断带,大幅提高了无取向硅钢的轧制效率和生产成材率,降低生产成本。
25.(3)通过无取向硅钢化学成分的设计,结合热轧工序的低温轧制和高温卷取,以及对连铸坯加热温度和加热时长的控制,在保证生产效率、有利于后续精轧的高温终轧的同时,降低析出细小的mns、aln的几率,防止钢中mns、aln等析出物在加热过程的固溶,有利于组织晶粒的长大,进而使得后续制得的无取向硅钢成品具有优异的磁性能;同时将精轧的终轧温度控制在高温铁素体区,有利于形成高温铁素体而避免形成变形纤维组织。
26.(4)在前述无取向硅钢化学成分设计的基础上,通过在常化前对热轧卷板进行切边处理,不仅将热轧卷板的边部缺陷切掉,切除热轧导致的钢板边部的厚度陡降区,这里的陡降区指钢板边部厚度有较大变化的区域,避免冷轧时钢板边部与中部的变形程度的较大差异,以利于板形的控制,有效避免边部裂纹在冷轧过程中扩展,避免热轧卷板的两侧边部在常化后由韧性变成脆性,保证切边后热轧卷板的边部质量,减少冷轧过程中的边损边裂,而且可将切边产生的剪切应力经常化后释放,降低冷轧过程中钢板两侧边部应力集中,将引起冷轧边裂的内在原因根除,完全消除冷轧边部裂口。
27.(5)进一步通过常化工序,可以改善无取向硅钢热轧钢板的组织和产品磁性,使热轧卷板组织更均匀,提高有利织构(100)和(110)组分以及减弱不利织构(111)组分,改善头中尾磁性能不一致的情况,进一步在前述无取向硅钢的化学组分的基础上,通过控制常化温度和时间,有利于合金含量高的无取向硅钢中的晶粒长大,从而将经过上述常化退火后
的钢带的平均晶粒尺寸控制在130~150μm,从而保持钢带的韧性,降低冷轧时的断带风险。
28.(6)进一步结合冷轧工序及参数设置,可利于增加钢带边部的变形量,降低钢带边部的边裂趋势,同时大的压下率可以增加带钢的变形热,提高钢带的轧制温度,将粗大晶粒压碎,细化晶粒,提高钢带的韧性和塑性,提高轧制成材率。结合对冷轧第一道次的轧制速率的控制,更有利于冷轧过程的稳定顺行,降低轧制过程中的断带风险,同时提高加工发热带来的钢带的高温化效果。
附图说明
29.图1是本发明实施例7的钢带边部的显微金相组织照片;
30.图2是本发明实施例8的钢带边部的显微金相组织照片;
31.图3是本发明对比例17的钢带边部的显微金相组织照片;
32.图4是本发明对比例18的钢带边部的显微金相组织照片。
具体实施方式
33.以下将结合附图所示的具体实施方式对本发明进行详细描述。但这些实施方式并不限制本发明,本领域的普通技术人员根据这些实施方式所做出的结构、方法、或功能上的变换均包含在本发明的保护范围内。
34.本发明一实施方式提供了一种超低铁损无取向硅钢的生产方法,以及一种采用所述生产方法制得的超低铁损无取向硅钢。
35.下面对所述超低铁损无取向硅钢的生产方法进行具体介绍,包括依序进行的冶炼、连铸、热轧、切边、常化酸洗、冷轧、退火、冷却、涂层和精整等工序。
36.在本实施方式中,所述超低铁损无取向硅钢的化学成分设计方案如下,其化学成分以质量百分比计为:c≤0.003%、si:2.8~3.4%、mn:0.1~0.5%、al:0.6~1.3%、s≤0.0015%、n≤0.0020%、p≤0.03%、ti≤0.003%、v≤0.003%、nb≤0.003%,且同时满足3.80%≤si+al≤4.15%,,其余为fe以及不可避免的杂质。
37.以下对所述超低铁损无取向硅钢的化学成分设计方案中各个元素的作用作出说明。
38.c:在无取向硅钢中,通常认为c为有害元素,c含量增加,会导致成品晶粒细小、铁损高、引起磁时效问题、导致磁特性变差,故本实施方式中,控制c含量(以质量百分比计)≤0.003%。
39.si:是提高电磁钢板电阻率的元素,能有效降低铁损,且能提高钢带的强度,但si的添加量过多会导致钢带脆化,会显著增加轧制时的断裂风险,因此在本实施方式中,控制si含量(以质量百分比计)为2.8~3.4%。
40.mn:mn易与s发生反应生成mns,有利于降低热轧板坯加热时固溶的s,适量添加mn,可以抑制s引起的热脆性,而且,mns在奥氏体中的固溶度比在铁素体相中低,适量的mn可以促进mn的析出物粗化,促进晶粒生长,还具有增加电阻、降低铁损的作用;在本实施方式中,控制mn含量(以质量百分比计)为0.1~0.5%。
41.al:也是提高电磁钢板电阻率、降低铁损的有效添加元素,其含量过高会降低磁感应强度,并大幅增加钢板的脆性,增大冷轧等加工难度;其含量过低会导致电阻率降低,以
及aln等氮化物微细地析出,使晶粒生长变差,甚至增大铁损,在本实施方式中,控制al的含量(以质量百分比计)为0.6~1.3%。同时,控制3.80%≤si+al≤4.15%,以兼顾高电阻率、低铁损和钢板脆性,以免增加冷轧等工序的加工难度。
42.s:为有害元素,是钢中夹杂物的重要组成元素,特别是在钢坯进行热轧前加热时钢中析出物mns会大量固溶,随后在热加工过程弥散析出,会阻碍成品退火过程中晶粒的长大,降低成品磁性,因此其含量增加会导致磁感应强度降低且铁损升高,在本实施方式中,为避免热轧过程中析出细小的mns,控制s的含量(以质量百分比计)≤0.0015%。
43.n:也是钢中夹杂物的重要组成元素,钢坯中形成的aln在热轧加热过程中会大量固溶,随后在热加工过程弥散析出,阻碍成品退火过程中晶粒的长大,降低成品磁性,因此控制n的含量(以质量百分比计)≤0.0020%。
44.p:可有效改善铁损,其含量增加可有效提高钢带强度、提升冲片性,但p含量过高会显著恶化钢的冷延性,因此控制p含量(以质量百分比计)≤0.03%。
45.ti:由于本发明的化学成分中al含量较高,精炼过程中添加合金时渣中的tio会被al还原,ti又进入钢水中,导致钢中ti含量增加,但ti作为钢中的碳化物、氮化物的形成元素,其细小的析出物会阻碍退火过程中成品晶粒的长大,恶化无取向硅钢的磁性能,导致铁损增大和磁感应强度降低,因此控制ti含量(以质量百分比计)≤0.003%。
46.v、nb:v、nb作为碳化物、氮化物的形成元素,也是主要的杂质元素,将二者的含量均控制为不超过0.003%。
47.总体来讲,本发明在化学成分设计方面,通过si、al含量增加,可以最大限度降低铁损,同时配合s和n等元素含量的控制,降低热轧工序中析出细小mns、aln的几率,以及结合对n、ti、v、nb元素含量的管控,保证磁性能,实现低铁损和高磁感应强度。
48.具体地,本实施方式的所述超低铁损无取向硅钢的生产方法,包括以下工序。
49.(1)冶炼
50.依次采用铁水脱硫、转炉冶炼、rh炉精炼按照前述的化学成分进行冶钢,也即,最终所得钢水的化学成分以质量百分比计为:c≤0.003%、si:2.8~3.4%、mn:0.1~0.5%、al:0.6~1.3%、s≤0.0015%、n≤0.0020%、p≤0.03%、ti≤0.003%、v≤0.003%、nb≤0.003%,且同时满足3.80%≤si+al≤4.15%,其余为fe以及不可避免的杂质。
51.该铁水脱硫、转炉冶炼、rh炉精炼工序的具体操作采用现有的对应技术均可以实现,不再多加赘述。
52.优选地,最终所得钢水化学成分以质量百分比计为:c≤0.003%、si:2.8~3.4%、mn:0.1~0.5%、al:0.6~1.3%、s≤0.0010%、n≤0.0015%、p≤0.03%、ti≤0.003%、v≤0.003%、nb≤0.003%,且同时满足3.80%≤si+al≤4.15%,其余为fe以及不可避免的杂质。这样更有利于成品退火过程中晶粒长大,提高产品磁性能,降低产品中的夹杂物数量,降低夹杂物尺寸。
53.(2)连铸
54.具体地,将rh炉精炼所得钢水出钢后采用连铸设备制备成厚度为210~230mm的连铸坯,该连铸工序可采用现有的可行连铸技术以实现,于此不再赘述。
55.(3)热轧
56.将连铸工序所得的连铸坯依次经过加热、多道次粗轧、多道次精轧、冷却和卷取,
制备得到热轧卷板。
57.优选地,控制制备得到的热轧卷板的厚度为1.9~2.3mm,热轧卷板的中部与边部的厚度之差为20~40μm,热轧卷板的两个边部之间的厚度之差≤22μm。这样,将热轧卷板的厚度控制在1.9~2.3mm,可以利于有利织构(100)和(110)的形成和热轧板形的控制,通过控制热轧钢板中部与边部的厚度之差以及两个边部之间的厚度差,可以降低热轧卷板的中部和两个边部之间的轧制压力不均匀、以及两个边部之间的轧制压力不均,有效减少边部裂纹和边损。
58.优选地,在热轧工序中,将连铸工序所得连铸坯先加热到1080~1130℃并保温30~50min,而后经过多道次粗轧、多道次精轧、冷却和卷取,制备得到厚度为1.9~2.3mm的热轧卷板。
59.其中,精轧的终轧温度为830~870℃,卷取温度为620~680℃。
60.这样,在前述化学成分的设计基础上,结合热轧工序的低温轧制和高温卷取,以及对连铸坯加热温度和加热时长的控制,在保证生产效率、有利于后续精轧的高温终轧的同时,降低析出细小的mns、aln的几率,防止钢中mns、aln等析出物在加热过程的固溶,有利于组织晶粒的长大,进而使得后续制得的无取向硅钢成品具有优异的磁性能;同时将精轧的终轧温度控制在高温铁素体区,有利于形成高温铁素体而避免形成变形纤维组织。
61.(4)切边
62.采用圆盘剪对热轧卷板的两侧边部进行剪切。
63.其中,单侧的剪切宽度≥20mm。
64.在前述化学成分设计的基础上,通过切边工序,不仅将热轧卷板的边部缺陷切掉,切除热轧导致的钢板边部的厚度陡降区,这里的陡降区指钢板边部厚度有较大变化的区域,避免冷轧时钢板边部与中部的变形程度的较大差异,以利于板形的控制,有效避免边部裂纹在冷轧过程中扩展,避免热轧卷板的两侧边部在常化后由韧性变成脆性,保证切边后热轧卷板的边部质量,减少冷轧过程中的边损边裂,而且可将切边产生的剪切应力经常化后释放,降低冷轧过程中钢板两侧边部应力集中,将引起冷轧边裂的内在原因根除,完全消除冷轧边部裂口。
65.(5)常化酸洗
66.对切边后的钢带进行常化、酸洗。
67.常化工序在常化炉中完成,其中,常化温度为900~930℃,常化时间为30~60s;
68.常化工序可以改善无取向硅钢热轧钢板的组织和产品磁性,使热轧卷板组织更均匀,提高有利织构(100)和(110)组分以及减弱不利织构(111)组分,改善头中尾磁性能不一致的情况,进一步在前述无取向硅钢的化学组分的基础上,通过控制常化温度和时间,有利于合金含量高的无取向硅钢中的晶粒长大,从而将经过上述常化退火后的钢带的平均晶粒尺寸控制在130~150μm,从而保持钢带的韧性,降低冷轧时的断带风险。
69.(6)冷轧
70.在冷轧线经多道次冷轧成厚度为0.35~0.5mm的无取向硅钢。
71.其中,第一道次冷轧时的压下率≥37%,轧制速率为70~180m/min。
72.通过控制冷轧第一道次采用较大的压下率,可利于增加钢带边部的变形量,降低钢带边部的边裂趋势,同时大的压下率可以增加带钢的变形热,提高钢带的轧制温度,将粗
大晶粒压碎,细化晶粒,提高钢带的韧性和塑性,提高轧制成材率。结合对冷轧第一道次的轧制速率的控制,更有利于冷轧过程的稳定顺行,降低轧制过程中的断带风险,同时提高加工发热带来的钢带的高温化效果。
73.具体地,在本实施方式中,所述冷轧工序中共采用4个道次轧制,将钢带自1.9~2.3mm的厚度轧制成厚度为0.5mm规格的超低铁损无取向硅钢,以满足高牌号无取向硅钢的尺寸要求。在其它实施例中,所述冷轧工序中也可以采用5个道次轧制,将钢带自1.9~2.3mm的厚度轧制成厚度为0.35mm规格的超低铁损无取向硅钢,以满足高牌号无取向硅钢的尺寸要求。
74.(7)成品退火
75.将冷轧所得的冷硬钢卷采用连续退火炉进行成品退火,成品退火温度为950~1000℃,退火时间为20~30s。
76.(8)涂层、精整、分卷包装
77.退火后的钢带经冷却、在成品表面涂布绝缘层和精整得到无取向硅钢成品,使成品具有优良的绝缘性。
78.本发明一实施方式的超低铁损无取向硅钢,采用上述生产方法制备而成,并且,如前所述,其化学成分以质量百分比计包括:c≤0.003%、si:2.8~3.4%、mn:0.1~0.5%、al:0.6~1.3%、s≤0.0015%、n≤0.0020%、p≤0.03%、ti≤0.003%、v≤0.003%、nb≤0.003%,且同时满足3.80%≤si+al≤4.15%,其余为fe以及不可避免的杂质。
79.该超低铁损无取向硅钢的厚度为0.50mm时,其铁损p
1.5/50
≤2.35w/kg,磁感应强度b
5000
≥1.66t,磁感应性能优异,能够满足其在马达、变压器等产品中的应用能效的需求,而且轧制过程中的断带率为2%以下。
80.该超低铁损无取向硅钢的厚度为0.35mm时,其铁损p
1.5/50
≤2.10w/kg,磁感应强度b
5000
≥1.65t,磁感应性能优异,能够满足其在马达、变压器等产品中的应用能效的需求,而且轧制过程中的断带率为2%以下。
81.与现有技术相比,本发明的有益效果在于:
82.(1)在化学成分设计方面,通过si、al含量增加,可以最大限度降低铁损,同时配合s和n等元素含量的控制,降低热轧工序中析出细小mns、aln的几率,以及结合对n、ti、v、nb元素含量的管控,保证磁性能,实现低铁损和高磁感应强度。
83.(2)通过组分配比,结合工艺设计,不仅可以使制备得到的无取向硅钢组织均匀、具有较低的铁损和优异的磁感应性能,满足其在马达、变压器等产品中的应用能效,而且通过优化热轧、切边、常化以及冷轧工序等加工工艺,提高制备的无取向硅钢的韧性,避免硅钢在冷轧工序中由于脆性高而导致的频繁断带,大幅提高了无取向硅钢的轧制效率和生产成材率,降低生产成本。
84.(3)通过无取向硅钢化学成分的设计,结合热轧工序的低温轧制和高温卷取,以及对连铸坯加热温度和加热时长的控制,在保证生产效率、有利于后续精轧的高温终轧的同时,降低析出细小的mns、aln的几率,防止钢中mns、aln等析出物在加热过程的固溶,有利于组织晶粒的长大,进而使得后续制得的无取向硅钢成品具有优异的磁性能;同时将精轧的终轧温度控制在高温铁素体区,有利于形成高温铁素体而避免形成变形纤维组织。
85.(4)在前述无取向硅钢化学成分设计的基础上,通过在常化前对热轧卷板进行切
边处理,不仅将热轧卷板的边部缺陷切掉,切除热轧导致的钢板边部的厚度陡降区,这里的陡降区指钢板边部厚度有较大变化的区域,避免冷轧时钢板边部与中部的变形程度的较大差异,以利于板形的控制,有效避免边部裂纹在冷轧过程中扩展,避免热轧卷板的两侧边部在常化后由韧性变成脆性,保证切边后热轧卷板的边部质量,减少冷轧过程中的边损边裂,而且可将切边产生的剪切应力经常化后释放,降低冷轧过程中钢板两侧边部应力集中,将引起冷轧边裂的内在原因根除,完全消除冷轧边部裂口。
86.(5)进一步通过常化工序,可以改善无取向硅钢热轧钢板的组织和产品磁性,使热轧卷板组织更均匀,提高有利织构(100)和(110)组分以及减弱不利织构(111)组分,改善头中尾磁性能不一致的情况,进一步在前述无取向硅钢的化学组分的基础上,通过控制常化温度和时间,有利于合金含量高的无取向硅钢中的晶粒长大,从而将经过上述常化退火后的钢带的平均晶粒尺寸控制在130~150μm,从而保持钢带的韧性,降低冷轧时的断带风险。
87.(6)进一步结合冷轧工序及参数设置,可利于增加钢带边部的变形量,降低钢带边部的边裂趋势,同时大的压下率可以增加带钢的变形热,提高钢带的轧制温度,将粗大晶粒压碎,细化晶粒,提高钢带的韧性和塑性,提高轧制成材率。结合对冷轧第一道次的轧制速率的控制,更有利于冷轧过程的稳定顺行,降低轧制过程中的断带风险,同时提高加工发热带来的钢带的高温化效果。
88.上文所列出的详细说明仅仅是针对本发明的可行性实施方式的具体说明,它们并非用以限制本发明的保护范围,凡未脱离本发明技艺精神所作的等效实施方式或变更均应包含在本发明的保护范围之内。
89.下面通过6个实施例和10个对比例来进一步说明本发明的有益效果,当然,这6个实施例仅为本发明所含众多变化实施例中的一部分,而非全部。6个实施例和10个对比例分别提供了一种无取向硅钢,其生产方法具体如下。
90.(1)冶炼
91.依次采用铁水脱硫、转炉冶炼、rh炉精炼按照如表1所述的化学成分进行冶钢。
92.[表1]
[0093][0094][0095]
(2)连铸
[0096]
将冶炼所得钢水采用连铸设备制备成连铸坯,连铸坯的厚度为220mm。
[0097]
(3)热轧
[0098]
将连铸工序所得连铸坯先在加热炉中加热到1110℃并保温40min后出炉,经6道次粗轧、7道次精轧、冷却和卷取,制备得到厚度为2.1mm的热轧卷板。其中,终轧温度为850℃,卷取温度为650℃,热轧板的中部与边部的厚度之差为32μm,热轧卷板的两个边部之间的厚度之差为6μm。
[0099]
(4)切边
[0100]
采用圆盘剪对热轧卷板的两侧边部进行剪切,单侧的剪切宽度为25mm。
[0101]
(5)常化酸洗
[0102]
将切边后的热轧卷板送入常化炉中进行常化,常化温度为910℃,常化时间为60s,之后酸洗。
[0103]
(6)冷轧
[0104]
在冷轧线经4道次冷轧成厚度为0.5mm的无取向硅钢。
[0105]
其中,第一道次冷轧时的压下率为40%,轧制速率为80~120m/min。
[0106]
(7)成品退火
[0107]
将冷轧所得的冷硬钢卷在连续退火炉中进行成品退火,成品退火温度为1000℃,退火时间为30s。
[0108]
(8)涂层、精整、分卷包装
[0109]
退火后的钢带经冷却、在成品表面涂布绝缘层和精整得到无取向硅钢成品。
[0110]
对实施例1~6和对比例1~10所得的无取向硅钢成品的爱泼斯坦方圈试样进行检
测,得到铁损p
1.5/50
、磁感应强度b
5000
的数据如表2所示。
[0111]
[表2]
[0112][0113][0114]
从表2可以看出,化学成分满足:c≤0.003%、si:2.8~3.4%、mn:0.1~0.5%、al:0.6~1.3%、s≤0.0015%、n≤0.0020%、p≤0.03%、ti≤0.003%、v≤0.003%、nb≤0.003%,且同时满足3.80%≤si+al≤4.15%,其余为fe以及不可避免的杂质时,制备得到厚度为0.5mm的无取向硅钢的铁损p
1.5/50
≤2.35w/kg,磁感应强度b
5000
≥1.66t,具有超低的铁损和优异的磁性能,而且不会在冷轧时断带,大大提高了轧制成材率。
[0115]
以下再通过另外2个实施例7~8和8个对比例11~18来进一步说明本发明的有益效果,当然,这2个实施例仅为本发明所含众多变化实施例中的一部分,而非全部。2个实施例和8个对比例分别提供了一种无取向硅钢,其生产方法具体如下。
[0116]
(1)冶炼
[0117]
依次采用铁水脱硫、转炉冶炼、rh炉精炼按照如下化学成分进行冶钢,钢水的化学成分以质量百分比计包括:c 0.0015%、si 3.22%、mn 0.18%、al 0.85%、s 0.0006%、n 0.0011%、p 0.021%、ti 0.0021%、v 0.0015%、nb 0.0023%,其余为fe以及不可避免的杂质。
[0118]
(2)连铸
[0119]
将冶炼所得钢水采用连铸设备制备成连铸坯,连铸坯的厚度为220mm。
[0120]
(3)热轧
[0121]
将连铸工序所得连铸坯先在加热炉中加热到1110℃并保温40min后出炉,经6道次
粗轧、7道次精轧、冷却和卷取,制备得到厚度为2.1mm的热轧卷板。其中,终轧温度为850℃,卷取温度为650℃,热轧板的中部与边部的厚度之差为20~40μm,热轧卷板的两个边部之间的厚度之差为22μm以下。
[0122]
(4)切边
[0123]
采用圆盘剪对热轧卷板的两侧边部进行剪切,单侧的剪切宽度为25mm。
[0124]
(5)常化酸洗
[0125]
将切边后的热轧卷板送入常化炉中进行常化,常化温度、常化时间见表3,之后酸洗。
[0126]
(6)冷轧
[0127]
在冷轧线经4道次冷轧成厚度为0.5mm的无取向硅钢,断带情况如表3所示。
[0128]
其中,第一道次冷轧时的压下率和轧制速率见表3。
[0129]
(7)成品退火
[0130]
将冷轧所得的冷硬钢卷在连续退火炉中进行成品退火,成品退火温度为1000℃,退火时间为30s。
[0131]
(8)涂层、精整、分卷包装
[0132]
退火后的钢带经冷却、在成品表面涂布绝缘层和精整得到无取向硅钢成品。
[0133]
对实施例7~8和对比例11~18所得的无取向硅钢成品的爱泼斯坦方圈试样进行检测,得到铁损p
1.5/50
、磁感应强度b
5000
的数据如表3所示。
[0134]
[表3]
[0135][0136][0137]
从表3可以看出,在前述无取向硅钢化学成分设计的基础上,通过在常化前对热轧卷板进行切边处理,并控制常化工序中的工艺参数,可以使常化后钢带的平均晶粒尺寸控制在139~150μm,进一步结合对冷轧的工艺参数的控制,可以防止冷轧断带,而且制备得到厚度为0.5mm的无取向硅钢的铁损p
1.5/50
≤2.30w/kg,磁感应强度b
5000
≥1.67t,具有超低的
铁损和较高的磁感应强度。
[0138]
另外,对实施例7、8以及对比例17、18的冷轧前的钢板采用扫描电子显微镜观察,得到如图1~4所示的边部图片。自图1~2可以看出:在常化工序前切边制备得到的钢板的边部经剪切产生的微裂纹在经高温常化后钝化,边部的尖锐部分完全钝化成圆形,在冷轧过程中难以扩展成为裂纹源,因此冷轧时不易断裂,大大提高了轧制成材率。自图3~4可以看出:在常化酸洗工序后切边制备得到的钢板的边部具有较多尖锐的剪切微裂纹,在冷轧过程中,这些微裂纹在应力作用下极易扩展成更长的裂纹,经多道次轧制后极易断带。