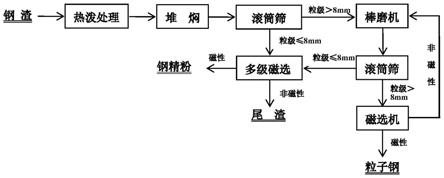
1.本发明涉及钢渣生产应用技术领域,具体涉及一种钢渣处理工艺及其所得尾渣的应用。
背景技术:
2.钢铁冶金废渣是钢铁行业炼钢工序产出的含钙、镁、铝、硅等元素的固态渣。近年来,随着我国经济的发展,钢铁产能增加,钢渣的排放量也随之增加。从国内钢企生产情况来看,目前钢渣年产量超过1.2亿吨,加之受钢渣利用率低的影响,目前钢渣堆存量巨大,造成严重的土地占用、污染与资源浪费。针对钢渣堆存严重的情况,于2018年1月1日正式实施《环境保护税法》,明确指出对钢铁企业产生且未处置的钢渣每吨征收25元的环保税,使钢铁企业钢渣资源化利用迫在眉睫。
3.目前钢渣利用方面存在利用率低的问题,钢渣尾渣的利用更是存在利用方向单一、收益低等问题,大量的钢渣尾渣仅用于水泥生产。近年来,随着水泥行业低标号水泥的取消,实现钢渣、尾渣深度处理、高效利用,成为各大钢企亟待解决的问题。
4.现有钢渣湿法选别工艺,如图1所示:钢渣进入球磨机进行破碎、粉磨,经粉磨后的钢渣经滚筒筛分离出粒子钢和钢渣粉,粒子钢为终产品,钢渣粉经磁选机分离出钢精粉和尾泥。所得粒子钢、钢精粉用于炼钢、炼铁配料,但尾泥下一步销售及处理困难,造成资源浪费、效益流失及环保风险。此外该工艺中,为了杜绝出现可视性污染现象,并为钢渣在磨内的运行提供动力,在球磨机破碎、粉磨过程中加入大量的水,加入的水可经三级沉淀后循环使用;为了提升钢渣粉中磁性物与非磁性物的分离效果,在磁选过程中加入循环水。全过程使用水,容易受地区气候季节性变化影响,冬季运行困难,并且造成水资源浪费,选别过程中溶入重金属,易污染地下水。
5.现有干磨干选选别工艺,如图2所示:钢渣经粗破、细破、圆锥破及棒磨机等多级破碎后,经滚筒筛对金属铁进行筛分,将粒级在8mm以上物料进行磁选,磁性物为终产品粒子钢,非磁性物为渣块,渣块二次进入破碎设备破碎后选别。粒级≤8mm物料经多级磁选选别,磁性物为终产品钢精粉,非磁性物为终产品尾渣。但是该工艺中,对尾渣中游离氧化钙控制指标高,利用方向单一,造成效益流失;物料粒级控制不均匀,渣铁分离效果差,磁性物回收率低;干磨干选现场可视性污染控制困难。
技术实现要素:
6.针对现有技术存在的上述不足,本发明的目的在于提供一种钢渣处理工艺及其所得尾渣的应用。
7.为实现以上目的,本发明采用如下技术方案:
8.一种钢渣处理工艺,包括以下步骤:
9.1)将钢渣进行预处理,所述预处理包括热泼处理和堆焖;
10.2)将步骤1)预处理后所得钢渣,经三级破碎后筛分:
11.将粒级≤8mm物料直接进行多级磁选选别,磁性物为终产品钢精粉,非磁性物为终产品尾渣;
12.粒级>8mm物料进入棒磨机进行再次破碎,经破碎的物料再次筛分,粒级>8mm的物料采用磁选机进行选别,磁性物为终产品粒子钢,非磁性物循环进入棒磨机。
13.进一步地,发明人在研究过程中发现,将堆焖时间和钢渣水分均严格控制在一定范围内,可以促进钢渣中渣、铁分离,降低游离氧化钙,从而杜绝现场可视性污染。因此,在本发明的一种优选实施方式中,堆焖过程中,将堆焖时间控制在1个月以上,同时将钢渣水分控制在3
±
0.5%区间内。
14.在本发明的另一种实施方式中,堆焖过程,采用短期焖渣5~10天,再将多级磁选选别剩余的尾渣置于相对湿度高于80%潮湿环境的方法,以水化反应降低游离氧化钙。
15.进一步地,控制棒磨机出料中粒级≤1mm物料占比在10%以内。
16.进一步地,所述筛分使用的是滚筒筛。
17.进一步地,上述过程中得到的尾渣在高寒地区道路面层中的应用。
18.本发明中:
19.钢渣:指用电炉、转炉、精炼炉冶炼金属过程中排出的固体废物。
20.尾渣:指原渣中提取钢渣铁素铁后的产物,粒级在8mm以下。
21.尾泥:湿法选别中,钢渣粉经筛分、磁选提取铁素铁后剩余的产物。
22.钢渣铁素铁:指原渣经焖渣、破碎后磁选出的磁性物质,tfe含量在52%以上,其中粒级20mm以上的为磁选铁,8-20mm的为粒子钢,0-8mm的为钢精粉。
23.与现有技术相比,本发明具有以下有益效果:
24.(1)本发明工艺过程不产生污水和可视性污染,生产不受地区性、季节性影响,提升了钢精粉tfe品位和磁性物回收率,减少了磷、铋等有害元素富集,降低了铁水中有害元素含量;
25.(2)拓宽了钢渣尾渣的使用渠道,可用于高寒地区道路面层,提升了尾渣的效益,实现了冶金固废资源的循环利用;
26.(3)生产过程无循环污水,避免污染地下水;全程经粒级控制和水份控制,现场无扬尘,改善了工作环境。
附图说明
27.通过阅读参照以下附图对非限制性实施例所作的详细描述,本发明的其它特征、目的和优点将会变得更明显:
28.图1为钢渣湿法选别工艺流程图;
29.图2为钢渣干磨干选选别工艺流程图;
30.图3为本发明用于高寒地区道路面层钢渣生产工艺流程图。
具体实施方式
31.下面结合具体实施例对本发明进行详细说明。以下实施例将有助于本领域的技术人员进一步理解本发明,但不以任何形式限制本发明。应当指出的是,对本领域的普通技术人员来说,在不脱离本发明构思的前提下,还可以做出若干变形和改进。这些都属于本发明
的保护范围。
32.实施例1
33.一种用于高寒地区道路面层钢渣生产工艺,包括以下步骤:
34.1)将钢渣进行预处理,所述预处理包括热泼处理和堆焖;
35.2)将步骤1)预处理后所得钢渣,经三级破碎后使用滚筒筛筛分:
36.将粒级≤8mm物料直接进行多级磁选选别,磁性物为终产品钢精粉,非磁性物为终产品尾渣;
37.粒级>8mm物料进入棒磨机进行再次破碎,经破碎的物料再次使用滚筒筛筛分,粒级>8mm的物料采用磁选机进行选别,磁性物为终产品粒子钢,非磁性物循环进入棒磨机。
38.本实施例中,堆焖过程中,将堆焖时间控制在1个月以上,同时将钢渣水分控制在3
±
0.5%区间内。
39.在过程工艺三级破碎后设计滚筒筛,尽量杜绝粒级≤8mm物料进入棒磨机进行二次破碎后出现过粉磨现象,严控粒级≤1mm物料占比在10%以内。
40.将上述过程中得到的尾渣,应用于高寒地区道路面层。
41.经预处理、过程物料粒级控制后的尾渣游离氧化钙、粒级等重要指标符合高寒地区道路面层中钢渣的使用指标。
42.尾渣在高寒地区道路面层中的应用,按级配进行配料基础上需严控钢渣中f
(cao)
含量及无侧限抗压指标,保证路面耐久性。本实施例中通过热泼、焖渣的方式控制钢渣中f
(cao)
含量。并且钢渣是经冶金废渣高温条件下形成,无侧限抗压实验数据高于碎石,应用于道路后无侧限抗压指标符合道路建设标准。
43.实施例2
44.一种用于高寒地区道路面层钢渣生产工艺,包括以下步骤:
45.1)将钢渣进行预处理,所述预处理包括热泼处理和堆焖;
46.2)将步骤1)预处理后所得钢渣,经三级破碎后筛分:
47.将粒级≤8mm物料直接进行多级磁选选别,磁性物为终产品钢精粉,非磁性物为终产品尾渣;
48.粒级>8mm物料进入棒磨机进行再次破碎,经破碎的物料再次筛分,粒级>8mm的物料采用磁选机进行选别,磁性物为终产品粒子钢,非磁性物循环进入棒磨机。
49.本实施例中,堆焖过程,采用短期焖渣5~10天,再将多级磁选选别剩余的尾渣置于相对湿度高于80%潮湿环境的方法,以水化反应降低游离氧化钙。
50.在过程工艺三级破碎后设计滚筒筛,尽量杜绝粒级≤8mm物料进入棒磨机进行二次破碎后出现过粉磨现象,严控粒级≤1mm物料占比在10%以内。
51.将上述过程中得到的尾渣,应用于高寒地区道路面层,其游离氧化钙、粒级等重要指标符合高寒地区道路面层中钢渣的使用指标,应用于道路后无侧限抗压指标符合道路建设标准,无侧限抗压实验数据高于碎石。
52.发明人在研究过程中发现,将堆焖时间控制在1个月以上,同时将钢渣水分控制在3
±
0.5%区间内,是实现本发明方案非常重要的一点,旨在控制尾渣中游离氧化钙含量和tfe含量,以保证道路使用寿命,在整个过程管控中以上关键指标控制不当将造成以下现象。
53.如果堆焖时间低于1个月时,游离氧化钙水化时间不足,导致尾渣应用于高寒地区路面时出现游离氧化钙含量超标,路面在后续使用中随着使用期的不断增长出现裂纹现象,道路后期使用寿命难以保证。
54.钢渣水份高于3
±
0.5%时,受钢渣粘附性强的影响,生产过程粒级控制困难,一方面影响钢渣在路面使用中的粒级,使无侧限抗压强度难以达标;另一方面造成钢渣中tfe流失至尾渣,影响道路后期质量;钢渣水份低于3
±
0.5%时,影响堆焖效果,易造成游离氧化钙超标现象,影响路面使用寿命。
55.以上对本发明的具体实施例进行了描述。需要理解的是,本发明并不局限于上述特定实施方式,本领域技术人员可以在权利要求的范围内做出各种变形或修改,这并不影响本发明的实质内容。