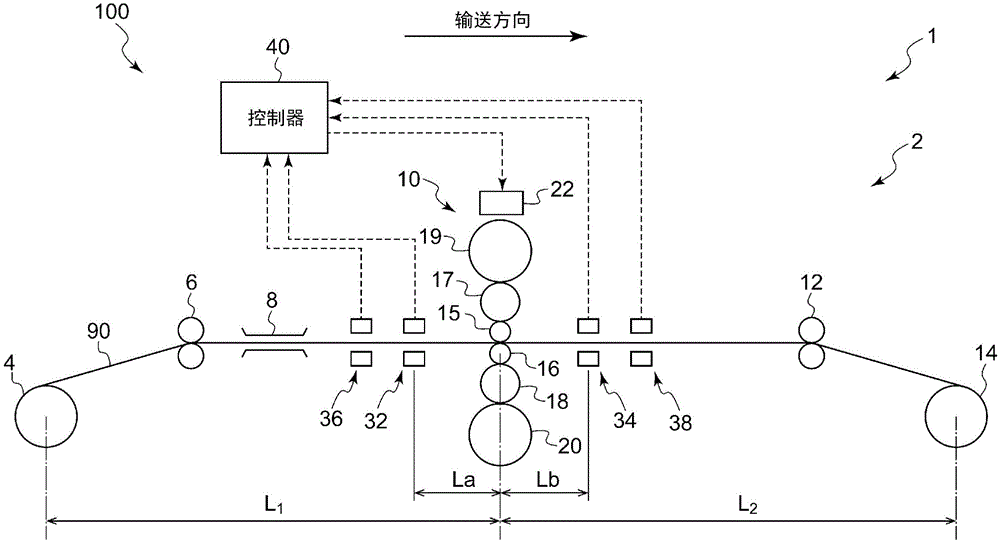
本公开涉及轧制装置的控制装置以及轧制设备及轧制装置的运转方法。
背景技术
在使用了包含一对轧制辊的轧制机的金属板的轧制中,有时在金属板的前端部分被收卷机收卷之前,在轧制机送出侧的张力不作用于金属板的状态下进行金属板的轧制(前端无张力轧制)。
例如,在专利文献1中记载有:使用包括轧制机(轧制辊)、以及设置于该轧制机的送出侧的张力卷筒(收卷机)的轧制装置,在轧制材料(金属板)被张力卷筒收卷而确立轧制机送出侧的张力之前进行轧制。另外,在专利文献1中记载有:在轧制机的送出侧处,在比张力卷筒靠上游侧设置蛇行检测器,基于由蛇行检测器检测出的位移量(轧制辊的轴向中央位置与轧制材料的板宽方向中央位置之差)进行轧制机的校平控制。由此,抑制由于在没有送出侧张力的状态下进行轧制而可能产生的轧制材料的蛇行以及单侧延展,从而谋求改善成品率。
在先技术文献
专利文献
专利文献1:日本特开平11-179414号公报
技术实现要素:
发明要解决的课题
如上述那样,在送出侧张力不作用于金属板的前端无张力的状态下,通过使用设置于轧制辊的送出侧的位置传感器(在专利文献1中为蛇行检测器),能够检测金属板的板宽方向的规定部位的位置(中央位置或板端位置),并基于该检测值来进行轧制机的控制。然而,即使成为检测对象的金属板的板宽方向的规定部位的位置在轧制机的位置上从规定位置偏移(例如,即使金属板的板宽方向中央位置从轧制辊的轴向中央位置偏移),由于某种原因,金属板从轧制辊的流出方向从轧制装置的输送方向倾斜时,也可能发生位置传感器的检测位置与上述的规定位置一致的情况。在该情况下,根据利用位置传感器进行的检测结果,无法适当地掌握金属板的流出方向倾斜。因此,若在该状态下继续轧制,则金属板的前端部在板宽方向上从轧制机的输送线分离,存在无法利用收卷装置适当地收卷轧制后的金属板的情况。
基于上述的情况,本发明的至少一实施方式的目的在于,提供能够利用收卷装置适当地收卷在前端无张力的状态下进行了轧制的金属板的轧制装置的控制装置以及轧制设备及轧制装置的运转方法。
用于解决课题的手段
本发明的至少一实施方式的轧制装置的控制装置,其用于控制包含以夹持金属板的方式设置的一对轧制辊的轧制装置的控制装置,
所述轧制装置的控制装置具备:
第一板端检测部,其构成为在所述金属板的输送方向上设置于所述一对轧制辊的送入侧,并且检测所述输送方向的第一位置处的所述金属板的板宽方向的板端位置;
第二板端检测部,其构成为在所述输送方向上设置于所述一对轧制辊的送出侧,并且检测所述输送方向的第二位置处的所述金属板的板宽方向的板端位置;以及
判定部,其构成为基于由所述第一板端检测部检测出的所述金属板的第一板端位置、以及由所述第二板端检测部检测出的所述金属板的第二板端位置,判定可否开始在所述金属板的送出侧张力为零的状态下利用所述一对轧制辊进行的所述金属板的轧制即前端无张力轧制。
发明效果
根据本发明的至少一实施方式,提供能够利用收卷装置适当地收卷在前端无张力的状态下进行了轧制的金属板的轧制装置的控制装置以及轧制设备及轧制装置的运转方法。
附图说明
图1是一实施方式的具备控制装置的轧制设备的概略结构图。
图2是一实施方式的具备控制装置的轧制设备的概略结构图。
图3是一实施方式的构成控制装置的控制器的概略结构图。
图4是表示一实施方式的轧制装置的运转方法的一个例子的流程图。
图5A是表示金属板的前端无张力轧制开始时的轧制辊及金属板的状态的示意图。
图5B是表示金属板的前端无张力轧制开始时的轧制辊及金属板的状态的示意图。
图5C是表示金属板的前端无张力轧制开始时的轧制辊及金属板的状态的示意图。
图6是用于说明由判定部进行的可否开始前端无张力轧制的判定的图。
图7是用于说明由判定部进行的可否开始前端无张力轧制的判定的图。
图8是表示由一实施方式的轧制设备轧制了的金属板的包括板宽方向及长度方向的局部截面的示意图。
图9是表示示出辊间间隙与时间的关系的曲线图的一个例子的曲线图。
图10是表示示出辊间间隙与时间的关系的曲线图的一个例子的曲线图。
图11是表示一实施方式的轧制装置的运转方法的一个例子的流程图。
图12A是表示根据图11所示的流程图进行轧制装置的运转时的、金属板的状态转变的图。
图12B是表示根据图11所示的流程图进行轧制装置的运转时的、金属板的状态转变的图。
图12C是表示根据图11所示的流程图进行轧制装置的运转时的、金属板的状态转变的图。
图12D是表示根据图11所示的流程图进行轧制装置的运转时的、金属板的状态转变的图。
图13是用于说明金属板的第一伸长差以及第二伸长差的计算方法的一个例子的曲线图。
图14是表示一实施方式的轧制装置的运转方法的一个例子的流程图。
图15A是表示根据图14所示的流程图进行轧制装置的运转时的、金属板的状态转变的图。
图15B是表示根据图14所示的流程图进行轧制装置的运转时的、金属板的状态转变的图。
图15C是表示根据图14所示的流程图进行轧制装置的运转时的、金属板的状态转变的图。
图15D是表示根据图14所示的流程图进行轧制装置的运转时的、金属板的状态转变的图。
具体实施方式
以下,参照附图来对本发明的几个实施方式进行说明。然而,作为实施方式而记载的或者附图所示的结构部件的尺寸、材质、形状及其相对的配置等并不将本发明的范围限定于此,只不过是单纯的说明例。
首先,对包括几个实施方式的轧制装置的轧制设备的整体结构进行说明。
图1及图2分别是一实施方式的具备控制装置的轧制设备的概略结构图。如图1及图2所示,轧制设备1具备轧制装置2、以及用于控制轧制装置2的控制装置100。在几个实施方式中,轧制装置2可以例如如图1所示包括一台轧制机10,也可以例如如图2所示包括两台轧制机10(10A、10B),或者还可以包括3台以上轧制机10。
图1所示的轧制装置2是使穿过一对轧制辊15、16间的金属板90往复而进行轧制的轧制装置(反向轧机)。图1所示的轧制装置2包括:轧制机10,其包括以夹持作为轧制材料的金属板90的方式设置的一对轧制辊(工件辊)15、16;放卷装置4,其在金属板90的行进方向上设置于轧制辊15、16的送入侧;以及收卷装置14,其在金属板90的行进方向上设置于轧制辊15、16的送出侧,并且轧制装置2构成为利用一对轧制辊15、16来轧制金属板90。
图2所示的轧制装置2是使穿过一对第一轧制辊15A、16A间以及一对第二轧制辊15B、16B的金属板90往复而进行轧制的轧制装置(反向轧机)。图2所示的轧制装置2包括:第一轧制机10A,其包括以夹持作为轧制材料的金属板90的方式设置的一对第一轧制辊(工件辊)15A、16A;第二轧制机10B,其包括以夹持金属板90的方式设置的一对第二轧制辊(工件辊)15B、16B;放卷装置4,其在金属板90的行进方向上设置于第一轧制辊15A、16A的送入侧;以及收卷装置14,其在金属板90的行进方向上设置于第二轧制辊15B、16B的送出侧,并且轧制装置2构成为利用一对第一轧制辊15A、16A以及一对第二轧制辊15B、16B来轧制金属板90。
图示的轧制机10、10A、10B具有相同的结构。以下,对轧制机10说明其结构,但对于轧制机10A、10B也适用相同的说明。需要说明的是,在图2中,作为轧制机10A、10B的结构要素(轧制辊等)的附图标记,记载了将图1所示的轧制机10的结构要素在相同的附图标记上分别标注“A”或“B”的附图标记。
轧制机10除了一对轧制辊(工件辊)15、16以外,还包括分别夹持一对轧制辊15、16而相对于金属板90分别设置于相反侧的一对中间辊17、18以及一对支承辊19、20。中间辊17、18以及支承辊19、20构成为支承轧制辊15、16。另外,轧制机10具备用于对一对轧制辊15、16赋予负载而将被一对轧制辊15、16夹持的金属板90压下的压下装置22。压下装置22也可以包括液压缸。
在轧制辊15、16经由主轴(未图示)等而连接有马达(未图示),轧制辊5、16由马达驱动旋转。在金属板90轧制时,一边由压下装置22压下金属板90一边利用马达使轧制辊15、16旋转,由此在轧制辊15、16与金属板90之间产生摩擦力,利用该摩擦力将金属板90向轧制辊15、16的送出侧输送。
放卷装置4构成为朝向轧制机10放卷金属板90。收卷装置14构成为将来自轧制机10的金属板90收卷。放卷装置4以及收卷装置14分别由马达(未图示)驱动。
放卷装置4构成为在金属板90轧制时对金属板90赋予送入侧张力。另外,收卷装置14构成为在金属板90轧制时对金属板90赋予送出侧张力。即,通过由马达适当地驱动放卷装置4以及收卷装置14,从而对金属板90赋予送入侧张力以及送出侧张力。通过对金属板90适当地赋予送入侧张力以及送出侧张力,能够抑制轧制时的金属板90的蛇行。
需要说明的是,在从放卷装置4放卷的金属板90的尾端紧前方停止轧制,在金属板90被轧制辊15、16压下的状态下奇数次(第一道次等)的轧制完成之后,接下来,从收卷装置14将金属板90朝向轧制机10放卷,并且一边由放卷装置4收卷金属板90,一边使金属板90向与之前相反的行进方向行进而进行偶数次(第二道次等)的轧制。即,根据金属板90的行进方向,而交换放卷装置4的作用和收卷装置14的作用。
图1及图2所示的轧制装置2还包括:送入侧夹辊6以及侧引导件8,它们用于引导从放卷装置4向轧制机10导入的金属板90;以及送出侧夹辊12,其用于引导从轧制机10向收卷装置14输送的金属板90。
如图1及图2所示,用于控制轧制装置2的控制装置100包括:第一板端检测部32以及第二板端检测部34,它们用于检测金属板90的板宽方向的板端位置;以及控制器40,其构成为根据第一板端检测部32以及第二板端检测部34的检测结果,对轧制装置2的运转进行控制。
第一板端检测部32构成为在金属板90的输送方向上设置于一对轧制辊15、16的送入侧,并且对输送方向的第一位置Y1处的金属板的板宽方向的板端位置即第一板端位置x1进行检测。第二板端检测部34构成为在输送方向上设置于一对轧制辊15、16的送出侧,并且对输送方向的第二位置Y2处的金属板的板宽方向的板端位置即第二板端位置x2进行检测。
需要说明的是,图2所示的控制装置100分别相对于第一轧制辊15A、16A、以及第二轧制辊15B、16B,在输送方向的送入侧设置有第一板端检测部32A、32B,并且在输送方向的送出侧设置有第二板端检测部34A、34B。
控制器40构成为,从第一板端检测部32以及第二板端检测部34接收表示计测结果的信号,根据这些的计测结果,对用于驱动压下装置22、轧制辊15、16的马达的动作进行控制。
控制器40可以包括CPU、存储器(RAM)、辅助存储部以及接口等。控制器40经由接口而接收来自第一板端检测部32以及第二板端检测部34的信号。CPU构成为对这样接收到的信号进行处理。另外,CPU构成为对在存储器展开的程序进行处理。
控制器40中的处理内容也可以作为由CPU执行的程序来安装,并存储于辅助存储部。在程序执行时,这些的程序在存储器展开。CPU从存储器读取程序,并执行程序中所含的命令。
图3是一实施方式的构成控制装置100的控制器40的概略结构图。如图3所示,控制器40包括判定部42、以及轧制控制部44。判定部42构成为,基于由第一板端检测部32检测出的金属板90的第一板端位置x1、以及由第二板端检测部34检测出的金属板90的第二板端位置x2,判定金属板90的送出侧张力为零的状态下的一对轧制辊15、16对金属板90的轧制(前端无张力轧制)可否开始。轧制控制部44构成为控制一对轧制辊15、16的动作。更具体而言,轧制控制部44构成为,进行用于驱动压下装置22、轧制辊15、16的马达控制,以调节轧制辊15、16的辊间间隙、旋转速度。
需要说明的是,关于控制器40的判定部42以外的各部分,在后叙述。
需要说明的是,控制装置100可以还具有用于显示判定部42的判定结果的显示部(显示器等;未图示)。
以下,对由控制装置100进行的轧制装置2的运转控制进行说明,但也可以通过手动进行以下说明的由控制装置100进行的处理的一部分或全部来运转轧制装置2。
图4是表示一实施方式的轧制装置2的运转方法的一个例子的流程图。需要说明的是,图4是表示开始金属板90的前端无张力轧制之前的运转方法的一个例子的流程图。关于金属板90的前端无张力轧制开始后的运转方法,一边参照图11及图14的流程图等一边在后面进行说明。
图5A~图5C分别是表示开始金属板90的前端无张力轧制时的、轧制辊15、16以及金属板90的状态的示意图。图6及图7分别是用于说明由判定部42进行的可否开始前端无张力轧制的判定的图。
在一实施方式中,如图4所示,首先,通过控制器40调节一对轧制辊15、16的位置,以使一对轧制辊15、16间的间隙(辊间间隙)成为比金属板90的板厚大的状态(步骤S102)。此时,也可以根据需要使压下装置22动作来调节一对轧制辊15、16的位置。然后,在维持辊间间隙比板厚大的状态下,使金属板90的包含前端91的前端部(参照图5A)穿过一对轧制辊15、16间(步骤S104)。
图5A是表示步骤S104完成时的轧制辊15、16以及金属板90的状态的示意图。如图5A所示,在步骤S104的完成时间点,在一对轧制辊15、16间的间隙d0比轧制前的金属板90的板厚H0大的状态下,金属板90的包含前端91的前端部穿过轧制辊15、16之间。另外,金属板90的包含前端91的前端部位于轧制辊15、16的送出侧,未到达收卷装置14。因此,作用于金属板90的送出侧张力Td为零。另外,在该时间点,由于不使送入侧张力Te作用于金属板90,因此送入侧张力Te也为零。
接下来,使用第一板端检测部32,对输送方向的第一位置Y1处的第一板端位置x1进行检测,并且使用第二板端检测部34,对输送方向的第二位置Y2处的第二板端位置x2进行检测(步骤S106)。
在此,图6及图7分别是俯视观察轧制开始前的轧制辊15、16以及金属板90的示意图。如图6及图7所示,金属板90具有板宽W,并具有作为板宽方向的两端缘的第一端缘92以及第二端缘93。在几个实施方式中,第一板端检测部32以及第二板端检测部34构成为,分别检测第一位置Y1以及第二位置Y2处的第一端缘92的位置来作为第一板端位置x1及第二板端位置x2(参照图6及图7)。或者,在其他实施方式中,第一板端检测部32以及第二板端检测部34构成为,分别检测第一位置Y1以及第二位置Y2处的第二端缘93的位置,来作为第一板端位置x1及第二板端位置x2。
然后,在步骤S106之后,通过判定部42,基于在步骤S106中检测出的第一板端位置x1及第二板端位置x2,判定可否开始金属板90的前端无张力轧制(步骤S108)。
在步骤S108中,例如,在金属板90的长度方向与由轧制装置2进行的金属板90的输送方向大致平行的情况下(参照图6),判定为能够开始金属板90的前端无张力轧制,在金属板90的长度方向相对于金属板90的输送方向的倾斜为规定程度以上的情况下(参照图7),判定为不能开始金属板90的前端无张力轧制。
更具体而言,在一实施方式中,在步骤S108中,在第一板端位置x1与第二板端位置x2之差|x1-x2|为阈值Δxth1以下时,判定为能够开始金属板90的前端无张力轧制,在上述差|x1-x2|比阈值Δxth1大时,判定为不能开始金属板90的前端无张力轧制。
或者,在一实施方式中,在步骤S108中,在金属板90的板宽方向上的基准位置xref与第一板端位置x1之差(x1-xref)以及基准位置xref与第二板端位置x2之差(x2-xref)分别在阈值xth2以下时,判定为能够开始金属板90的前端无张力轧制,在上述差(x1-xref)与(x2-xref)中的至少一方比阈值xth2大时,判定为不能开始金属板90的前端无张力轧制。
在此,上述的基准位置xref是金属板90的长度方向与利用轧制辊15、16(轧制机)进行的输送方向一致的情况下的板宽方向(即,轧制辊15、16的轴向(中心轴O的方向))上的规定位置。上述的基准位置xref例如也可以是轧制辊15、16的轴向上的中央位置(参照图6及图7)。需要说明的是,在图6中,金属板90的长度方向与利用轧制辊进行的输送方向一致,此时,沿着金属板90的长度方向的中心线Lc的位置在上述的板宽方向(即轧制辊15、16的轴向)上与基准位置xref一致。
在上述的步骤S108中,若判定为不能开始金属板90的前端无张力轧制(步骤S108的“否”),则修正金属板90的板宽方向位置(步骤S110),再次返回步骤S106,基于第一板端位置x1及第二板端位置x2的检测(步骤S106)以及在步骤S106中的检测结果进行可否开始金属板90的前端无张力轧制的判定(步骤S108)。
另一方面,在步骤S108中,若判定为能够开始金属板90的前端无张力轧制(步骤S108的“是”),则通过轧制控制部44开始金属板90的前端无张力轧制(步骤S112)。
在步骤S112中,在施加于金属板90的送出侧张力Td为零的状态下,利用一对轧制辊15、16压下金属板90,开始一对轧制辊15、16的旋转,由此开始金属板90的前端无张力轧制(参照图5B)。
在利用一对轧制辊15、16压下金属板90时,如图5B所示,使压下装置22动作,以使辊间间隙成为与目标板厚对应的值d1。此时间点的辊间间隙d1比轧制前的金属板90的板厚H0小。另外,在轧制辊15、16的旋转开始时以及旋转开始后,通过用于驱动轧制辊15、16的马达的电流值的调节,将轧制辊15、16的旋转速度调节为适当的值。
若开始金属板90的前端张力轧制,则金属板90朝向图5B所示的箭头的方向行进。然后,如图5C所示,在轧制开始后,金属板90中的、被轧制辊15、16压下而向轧制辊15、16的送出侧行进的部分具有比轧制前的板厚H0薄的板厚H1。
这样,通过进行金属板90的前端无张力轧制,与在将金属板的前端收卷于收卷装置而赋予送出侧张力的状态下开始轧制的情况相比,能够从接近金属板90的前端的部分开始轧制,能够改善金属板90的成品率。
而且,如上述那样,在步骤S108中判定为能够开始金属板90前端无张力轧制之后,在步骤S112中开始前端无张力轧制,由此能够利用收卷装置14适当地收卷进行了前端无张力轧制的金属板90。
假设,在仅在轧制辊15、16的送出侧的一处设置板端位置检测部的情况下,会产生以下所述的问题。即,例如如图7所示,即使在轧制开始前金属板90的长度方向相对于由轧制辊15、16(轧制机10)输送的金属板90的输送方向倾斜,根据输送方向上的仅1点的板端位置检测结果,也不清楚金属板90的长度方向是否相对于上述的输送方向倾斜。在这样的情况下,若开始前端无张力轧制,则金属板90从轧制辊15、16流出的流出方向相对于利用轧制机10输出的输送方向保持倾斜。因此,由配置于送出侧的板端位置检测部检测出的板端位置(例如,图7中的第二板端位置x2)在轧制开始后也大致恒定。因此,即使进行基于检测出的板端位置的控制,也无法纠正相对于金属板90的输送方向的倾斜,若在该状态下继续轧制,则金属板90的前端部在板宽方向上从轧制机10的输送线分离,存在无法利用收卷装置14适当地收卷轧制后的金属板90的情况。
关于这一点,根据上述的实施方式,在步骤S106中,在一对轧制辊15、16的送入侧的第一位置Y1以及送出侧的第二位置Y2的每一个处,检测金属板90的板宽方向的板端位置(第一板端位置x1及第二板端位置x2)。因此,根据这些的检测结果,能够掌握前端无张力轧制开始前的金属板90的长度方向相对于输送方向的倾斜的程度,即,能够掌握前端无张力轧制开始时间点的金属板90的流出方向相对于输送方向的倾斜的程度。而且,在步骤S108中,根据第一板端位置x1及第二板端位置x2的检测结果,判定可否开始前端无张力轧制,因此,例如,在根据上述的检测结果判断为金属板90的长度方向(即,轧制开始时的金属板90的流出方向)相对于输送方向大致平行时,能够判定为可以开始金属板90的前端无张力轧制。
因此,根据上述的实施方式,由于能够在金属板90的流出方向与输送方向大致平行的状态下开始前端无张力轧制,因此能够抑制金属板90的前端部从轧制机10的输送线向板宽方向偏离。因此,容易利用收卷装置14适当地收卷被轧制的金属板90。
另外,根据上述的实施方式,由此能够在金属板90的流出方向与输送方向大致平行的状态下开始前端无张力轧制,因此将在前端无张力轧制开始时取得的第二板端位置x2用作基准,由此根据在前端无张力轧制中检测出的第二板端位置,能够适当地进行金属板90的蛇行控制等轧制机10的压下校平控制。
因此,能够利用收卷装置14适当地收卷进行了前端无张力轧制的金属板90。
另外,在图2所示的包括2台轧制机10(第一轧制机10A以及第二轧制机10B)的轧制设备1的情况下,控制装置100构成为,判定可否开始一对第一轧制辊15A、16A(第一轧制机10A)上的金属板90的第一次的前端无张力轧制,判定为能够开始第一次的前端无张力轧制,在利用一对第一轧制辊15A、16A开始前端无张力轧制之后,判定可否开始一对第二轧制辊15B、16B处的金属板90的第二次的前端无张力轧制。
即,对第一轧制机10A进行上述的步骤S102~步骤S112,金属板90的前端无张力轧制开始后,对第二轧制机10B进行上述的步骤S102~步骤S112。
这样,在沿输送方向排列的第一轧制辊15A、16A(第一轧制机10A)以及第二轧制辊15B、16B(第二轧制机10B)的每一个处,在步骤S108中进行可否开始前端无张力轧制的判定,根据该判定结果,在步骤S112中开始前端无张力轧制,因此一边能够收卷装置适当地收卷由这些的轧制辊15、16进行了前端无张力轧制的金属板90,一边能够使用一对轧制辊15A、16A以及一对轧制辊15B、16B,更高效地进行轧制。
第一板端检测部32以及第二板端检测部34优选在利用轧制辊15、16输送的金属板90的输送方向上尽量设置于轧制辊15、16的附近。由此,这是因为,能够在将金属板90的前端部配置于轧制辊15、16附近的状态下通过第一板端检测部32以及第二板端检测部34检测第一板端位置x1及第二板端位置x2,并且根据该检测结果,能够在将金属板90的前端91配置于轧制辊15、16附近的状态下开始轧制,能够有效地改善金属板90的成品率。
在几个实施方式中,在将一对轧制辊15、16与收卷装置14在输送方向上的距离设为L2(参照图1及图2)时,一对轧制辊15、16与第二板端检测部34在输送方向上的距离Lb(参照图1及图2)为0.1×L2以下。在几个实施方式中,上述的距离Lb为0.5×L2以下。
在此,一对轧制辊15、16与收卷装置14在输送方向上的距离是一对轧制辊15、16的中心轴O与收卷装置14的中心轴在输送方向上的距离。另外,一对轧制辊15、16与第二板端检测部34在输送方向上的距离是一对轧制辊15、16的中心轴与第二板端检测部34的中心位置、或第二板端检测部34的板端检测位置(第二位置Y2)在输送方向上的距离。需要说明的是,轧制辊15、16的中心轴O的方向、放卷装置4的中心轴的方向、以及收卷装置14的中心轴的方向相互大致平行。
这样,在输送方向上,由于使第二板端检测部34与轧制辊15、16间的距离Lb比较短,因此能够一边使无张力轧制开始时的金属板90的前端91比较接近轧制辊,一边在无张力轧制开始时以及无张力轧制中检测第二板端位置x2。因此,能够缩短金属板90中的未被轧制的前端部的长度,并且能够适当地进行前端无张力轧制,由此能够有效地提高金属板90的成品率。
在几个实施方式中,在将一对轧制辊15、16与放卷装置4在输送方向上的距离设为L1(参照图1及图2)时,一对轧制辊15、16与第一板端检测部32在输送方向上的距离La为0.1×L1以下。在几个实施方式中,上述的距离La为0.5×L1以下。
在此,一对轧制辊15、16与放卷装置4在输送方向上的距离L1是一对轧制辊15、16的中心轴O与放卷装置4的中心轴在输送方向上的距离。另外,一对轧制辊15、16与第一板端检测部32在输送方向上的距离是一对轧制辊15、16的中心轴O与第一板端检测部32的中心位置或第一板端检测部32的板端检测位置(第一位置Y1)在输送方向上的距离。
在使穿过一对轧制辊15、16间的金属板90往复且进行轧制的轧制装置(反向轧机)的情况下,在第一道次结束后的第二道次中,金属板90的输送方向反转,从金属板90的后端侧开始由轧制辊15、16进行的轧制。关于这一点,根据上述的实施方式,在第二道次中的输送方向(与第一道次的输送方向相反的方向)上,由于使第一板端检测部32与轧制辊15、16间的距离比较短,因此能够一边使第二道次的无张力轧制开始时的金属板90的后端位置比较接近轧制辊,一边在无张力轧制开始时以及无张力轧制中检测第一板端位置x1。因此,能够缩短金属板90中的未被轧制的后端部的长度,并且能够适当地进行前端无张力轧制,由此能够提高金属板90的成品率。
在几个实施方式中,轧制设备1具备在输送方向上设置于一对轧制辊15、16的送入侧或送出侧中的至少一方且构成为对金属板90的板厚进行计测的板厚计。在一实施方式中,第一板端检测部32或第二板端检测部34在输送方向上位于一对轧制辊15、16与板厚计之间。或者,在一实施方式中,第一板端检测部32或第二板端检测部34也可以在输送方向上配置于与板厚计相同的位置。在该情况下,第一板端检测部32或第二板端检测部34也可以作为与板厚计一体化的构件而设置。
在图1及图2所示的实施方式中,在输送方向上在一对轧制辊15、16的送入侧设置有板厚计36,第一板端检测部32在输送方向上位于一对轧制辊15、16与板厚计36之间。另外,在图1及图2所示的实施方式中,在输送方向上在一对轧制辊15、16的送出侧设置有板厚计38,第二板端检测部34在输送方向上位于一对轧制辊15、16与板厚计38之间。
为了良好地响应控制,用于控制金属板90的板厚的板厚计36、38优选在输送方向上设置于轧制辊15、16的附近。关于这一点,根据上述的实施方式,在输送方向上,在与板厚计36、38相同的位置或比其更靠近轧制辊15、16的位置设置第一板端检测部32或第二板端检测部34,因此能够一边使无张力轧制开始时的金属板90的前端位置更靠近轧制辊15、16,一边在无张力轧制开始时以及无张力轧制中检测第一板端位置x1或第二板端位置x2。因此,能够缩短金属板中的未被轧制的前端部的长度,并且能够适当地进行前端无张力轧制,由此能够提高金属板的成品率。
在几个实施方式中,第一板端检测部32或第二板端检测部34构成为使用放射线(例如X射线、伽马射线)来检测第一板端位置x1或第二板端位置x2。
轧制辊15、16的附近多为轧制油、烟尘大量飞散,轧制辊15、16有振动、黑暗等严酷的环境。关于这一点,根据上述的实施方式,由于使用利用放射线检测板端位置的第一板端检测部32或第二板端检测部34,因此即使配置于严酷的环境下的轧制辊15、16的附近,也能够适当地检测板端位置。
图8是表示由一实施方式的轧制设备1轧制的金属板90的包括板宽方向及长度方向的局部截面的示意图。如图8所示,金属板90具有在板厚方向上位于轧制辊15侧的第一表面94、以及在板厚方向上位于轧制辊16侧的第二表面95。
图9以及图10分别是表示示出在包括金属板90的轧制开始时的期间中的、一对轧制辊15、16间的间隙(辊间间隙)与时间的关系的曲线图的一个例子的曲线图。
在几个实施方式中,控制器40的轧制控制部44在上述的步骤S108中由判定部42判定为金属板90的前端无张力轧制能够开始时,在上述的步骤S120中,使一对轧制辊15、16与金属板90接触(图9的时间点t0)。在该时间点,金属板90还未被压下,轧制辊15、16与金属板90的接触位置(输送方向上的轧制辊15、16的中心轴O的位置)是比前端91靠后游侧的位置94a、95a(参照图8),该位置94a、95a处的板厚为H0(初始值)。然后,一边使一对轧制辊15、16旋转,一边调节一对轧制辊15、16的转速以及压下量,以使一对轧制辊15、16间的间隙随着金属板90的输送而逐渐减少到与金属板90的目标板厚HC对应的管理值dc(图9的从时间点t1到t2),直到比上述的位置94a、95a更靠后游侧的位置94b、95b(参照图8)。需要说明的是,在时间点t2以后,辊间间隙维持在目标板厚HC对应的管理值dc,以使通过了轧制辊15、16的金属板90的板厚成为目标板厚HC。
其结果为,包含金属板90的前端91的部分成为图8中实线所示的形状。即,金属板90具有:包含前端91且板厚为H0的前端部90a、板厚维持为目标板厚HC的后续部90c、以及在金属板的长度方向上位于前端部90a与后续部90c之间的转变部90b。在转变部90b中,从位置94a、95a到位置94b、95b,板厚从H0逐渐减少到HC。
在使金属板90的前端部(图8中的附图标记90a所示的部分)通过一对轧制辊15、16间的状态下,开始由轧制辊15、16进行的金属板90的压下以及前端无张力轧制的情况下,有时在金属板90中的、未被轧制辊15、16轧制的前端部90a与被轧制的后续部90c之间板厚之差变大。例如,假设,如图10所示,使一对轧制辊15、16间的间隙变窄至与目标板厚HC对应的管理值dc(图10的时间点t1),在该状态下开始轧制辊15、16的旋转(图10的时间点t1),金属板90的形状如图8中的双点划线所示,成为板厚在比开始轧制的位置94a、95a靠前方的前端部90a(板厚为H0)、以及比上述的位置94a、95a靠后方的后续部90c(板厚为Ht)急剧变化的形状。
在该情况下,在利用收卷装置14收卷金属板90时等,有时应力集中于上述的前端部90a与后续部90c的边界,并且导致金属板90在该边界被切断。
关于这一点,在上述的实施方式中,在金属板90的前端无张力轧制开始时,调节轧制辊15、16的转速以及压下量,以使一对轧制辊15、16与金属板90接触之后,一边使轧制辊15、16旋转,一边使轧制辊15、16间的间隙随着金属板90的输送而逐渐地减少至与金属板90的目标板厚Ht对应的管理值dc。因此,在具有与轧制前相同的板厚H0的前端部90a、以及轧制成目标板厚HC的后续部90c之间,形成板厚逐渐减少的转变部90b(参照图8)。由此,能够缓和在利用收卷装置14收卷金属板时等的、在上述的前端部90a与后续部90c的边界可能产生的应力集中。由此,能够利用收卷装置14适当地收卷轧制后的金属板90。
在几个实施方式中,如上述那样,在一对轧制辊15、16间的间隙随着金属板90的输送逐渐减少至与金属板90的目标板厚HC对应的管理值dc时,调节一对轧制辊15、16的转速以及压下量,以使上述的转变部90b中的第一表面94相对于金属板90的长度方向的倾斜角度α1、或者上述的转变部90b中的第二表面95相对于金属板90的长度方向的倾斜角度α2为20度以下。
由此,转变部90b(参照图8)中的板厚变化不会变得过于急剧,因此有效地缓和在利用收卷装置14收卷金属板时等的、在上述的前端部90a与后续部90c的边界可能产生的应力集中,能够利用收卷装置14适当地收卷轧制后的金属板90。
接下来,如上述那样,进一步说明开始金属板90的前端无张力轧制后的轧制装置2的运转方法(接着图4的流程图的部分)以及用于执行该运转方法的轧制设备1的控制装置100的结构。
在几个实施方式中,控制装置100具备检测部,该检测部构成为,在施加于金属板90的送出侧张力为零的状态下,一边利用一对轧制辊15、16轧制金属板90(即,一边进行金属板90的前端无张力轧制),一边在一对轧制辊15、16的送出侧的位置处检测金属板90的板宽方向的板端位置xB。在图1及图2所示的实施方式中,设置于轧制辊15、16的送出侧的第二板端检测部34作为上述的检测部而作为发挥功能。
另外,在几个实施方式中,控制装置100的控制器40(参照图3)具备第一校平部46、以及第二校平部48。
第一校平部46构成为,作为上述的检测部的第二板端检测部34(以下,也简称为“第二板端检测部34”。)的板端位置的检测结果从基准位置向板宽方向的一侧(第一端缘92或第二端缘93的一侧;参照图12A等)偏离时,进行一对轧制辊15、16的压下校平控制,以使金属板90从轧制辊15、16的流出方向沿着轧制装置2中的金属板90的输送方向。
第二校平部48构成为,在由第一校平部46进行的压下校平控制之后,进行一对轧制辊15、16的压下校平控制,以使在使金属板90从轧制辊15、16的流出方向相对于输送方向向板宽方向的另一侧(第一端缘92或第二端缘93的另一侧;参照图12A等)偏移之后,金属板90的流出方向返回输送方向。
在上述的控制装置100中,一边在前端无张力的状态下进行金属板90的轧制,一边利用第二板端检测部34(检测部)在轧制辊15、16的送出侧的位置处检测金属板90的板宽方向的板端位置xB,因此,基于检测出的板端位置xB从基准位置向板宽方向的一侧偏离的情况,能够检测出产生了金属板90的流出方向向板宽方向的一侧的偏移(金属板90的前端弯曲)。而且,在检测出金属板90的前端弯曲时,通过由第一校平部46进行的压下校平控制,使金属板90的流出方向沿着轧制装置2中的金属板90的输送方向,然后,通过由第二校平部48进行的压下校平控制,使金属板90的流出方向相对于输送方向板宽方向的另一侧偏移,然后,使金属板90的流出方向沿着输送方向,因此能够纠正金属板90的前端弯曲,使金属板90的前端缘(前端91)与收卷装置14的轴向接近平行的状态下,继续进行前端无张力轧制。因此,根据上述结构,能够利用收卷装置14适当地收卷进行了前端无张力轧制的金属板90。
另外,在几个实施方式中,控制器40具备伸长差计算部50、偏移角度计算部52、以及剩余时间计算部54中的至少一个。
伸长差计算部50构成为,由第二板端检测部34检测出的板端位置xB从基准位置朝向所述一侧分离后,由第一校平部46进行的压下校平控制,计算板端位置xB返回至基准位置为止的金属板90的所述另一侧相对于所述一侧的相对的第一伸长差d1。
偏移角度计算部52构成为,取得由第一校平部46进行的压下校平控制的开始时间点的金属板90的流出方向相对于输送方向的所述一侧的第一偏移角度θ1,基于该第一偏移角度θ1,决定由第二校平部进行的压下校平控制的执行中的金属板90的流出方向相对于输送方向朝向所述另一侧的第二偏移角度θ2。
剩余时间计算部54构成为,计算金属板90的前端91到达设置于一对轧制辊15、16的下游侧的收卷装置14为止的剩余时间Tc。
以下,参照图1~图3以及图11~图15,对几个实施方式的由控制装置100进行的轧制装置2的运转方法进行说明,但也可以通过手动进行以下说明的由控制装置100进行的处理的一部分或全部来运转轧制装置2。
图11以及图14分别是表示一实施方式的轧制装置2的运转方法的一个例子的流程图。图12A~图12D是表示根据图11所示的流程图进行轧制装置2的运转时的、金属板90的状态转变的图。图13是用于说明金属板90的第一伸长差以及第二伸长差的计算方法的一个例子的曲线图,在该曲线图中,横轴表示时间,纵轴表示后述的偏移量Δe。图15A~图15D是表示根据图14所示的流程图进行轧制装置2的运转时的、金属板90的状态转变的图。
在图11所示的流程图的实施方式中,首先,在施加于金属板90的送出侧张力为零的状态下,一边利用一对轧制辊15、16轧制金属板90(即,一边进行金属板90的前端无张力轧制),一边使用第二板端检测部34,在一对轧制辊15、16的送出侧的位置(图12A~图12D所示的“板端检测位置”)处检测金属板90的板宽方向的板端位置xB(步骤S202;检测步骤)。需要说明的是,在图13的曲线图中,时间点t20是开始金属板90的前端无张力轧制的时间点。
接下来,计算由步骤S202检测出的板端位置xB的、从板宽方向上的基准位置向板宽方向的一侧(第一端缘92或第二端缘93的一侧)的偏移量Δe(步骤S204),对计算出的偏移量Δe与阈值Δe_th进行比较(步骤S206)。
在此,基准位置是金属板90的长度方向与轧制装置2的输送方向(与轧制辊15、16的中心轴正交的方向)平行时的、板宽方向上的特定的位置。在图12A~图12D所示的例子中,将金属板90的长度方向与轧制装置2的输送方向平行时的金属板90的第一端缘92的位置设为“基准位置”。需要说明的是,也可以将金属板90的长度方向与轧制装置2的输送方向平行时的金属板90的板宽方向中央位置(中心线Lc的位置)作为“基准位置”。
在图12A所示的阶段中,在板宽方向上,基准位置与板端位置xB一致,在步骤S204中计算出的偏移量Δe为零。因此,在步骤S206中,判定为偏移量Δe小于阈值(步骤S206的否),返回步骤S202,再次由第二板端检测部34进行板端位置xB的检测。
图12B是表示从图12A所示的状态,由于某种外部干扰(例如,金属板90的板宽方向上的板厚的不均匀性)而发生金属板90的前端弯曲的阶段。在图12B所示的例中,由步骤S202检测出的板端位置xB从基准位置向板宽方向的第一端缘92侧(一侧)偏离。即,金属板90从轧制辊15、16的流出方向相对于轧制辊15、16的输送方向向板宽方向的第一端缘92侧(一侧)偏移。此时,在步骤S204中计算出的偏移量Δe大于零。需要说明的是,在图13所示的曲线图中,在时间点t21偏移量Δe开始大于零,在时间点t23偏移量Δe为极大(图12B所示的状态)。
在步骤S204中计算出的偏移量Δe为阈值Δe_th以下时(步骤S206的否),返回步骤S202,再次由第二板端检测部34进行板端位置xB的检测。另一方面,若在步骤S204中计算出的偏移量Δe比阈值Δe_th大(步骤S206的是,图13的曲线图的时间点t23),则在步骤S208中,以使偏移量Δe为零的方式,由压下装置22进行轧制辊15、16的校平控制(步骤S208)。即,在步骤S208中,进行一对轧制辊15、16的压下校平控制,以使金属板90从轧制辊15、16的流出方向沿着轧制装置2处的金属板90的输送方向(第一校平步骤)。图12C是表示在步骤S208结束时(上述的偏移量Δe为零时;图13的曲线图的时间点t24)的阶段的图。
接下来,由第二板端检测部34检测出的板端位置xB从基准位置向板宽方向的所述一侧(在此为第一端缘92侧)分离后(图12B所示的状态),在上述的第一校平步骤(步骤S208)中计算由第二板端检测部34检测出的板端位置xB返回基准位置为止(成为图12C所示的状态为止)的金属板90的所述另一侧(在此为第二端缘93侧)相对于所述一侧(第一端缘92侧)的相对的第一伸长差E1(步骤S210;伸长差计算步骤)。在此,在图12B以及图12C所示的例中,第二端缘93侧的金属板90的伸长为E1,与此相对,第一端缘92侧处的金属板90的伸长为零。因此,上述的第一伸长差为E1。
在伸长差计算步骤(步骤S210)中,基于由第二板端检测部34检测出的板端位置xB从基准位置向一侧(在此为第一端缘92侧)分离后(图13的曲线图的时间点t21),直至在第一校平步骤中板端位置xB返回基准位置(图13的曲线图的时间点t24)为止的、板端位置xB相对于基准位置的偏移量Δe的时间积分(曲线图图13所示的面积S1B’),计算第一伸长差E1。在此,基于曲线图图13所示的面积S1B’而能够计算第一伸长差E1是因为在图12B中附图标记S1A所示的三角形与附图标记S1B所示的三角形相似,在图12B中附图标记S1B所示的三角形与图13的曲线图的面积S1B’具有特定的相关关系。
接下来,计算金属板90的前端91到达设置于一对轧制辊15、16的下游侧的收卷装置14为止的剩余时间Tc(步骤S212;剩余时间计算步骤)。剩余时间Tc的起算点例如也可以是在第一校平步骤中上述的偏移量Δe为零的时间点(步骤S208的结束时间点;图13的曲线图的时间点t24),或者第二校平步骤的开始时间点(后述的步骤S214~S218的开始时间点;图13的曲线图的时间点t25)。需要说明的是,在图13的曲线图中,从第二校平步骤的开始时间点(时间点t25)到时间点t27的时间是剩余时间Tc。需要说明的是,剩余时间Tc能够基于金属板90的前端91、收卷装置14之间的距离、以及金属板90的输送速度而计算。
接下来,进行一对轧制辊15、16的压下校平控制,以使金属板90从轧制辊15、16的流出方向相对于输送方向向板宽方向的另一侧(在此为第二端缘93侧)偏移之后,金属板90的流出方向返回输送方向(步骤S214~S218;第二校平步骤)。在此,图12D表示第二校平步骤结束的时间点的状态(即,步骤S218的结束时间点的状态)
在步骤S214中,以在剩余时间Tc内将与第一伸长差E2相等的大小的第二伸长差E2(参照图12D)赋予金属板90的方式,计算对于压下装置22以及轧制辊15、16的驱动马达的控制指令值。在此,第二伸长差E2是金属板90的所述一侧(在此为第一端缘92侧)相对于所述另一侧(在此为第二端缘93侧)的相对的第二伸长差。
即,通过进行第二校平步骤,如图12D及图13所示,板端位置xB向第二端缘93侧偏移而产生偏移量Δe。而且,通过使该第二端缘93侧的Δe的时间积分值(图13的曲线图处的面积S2B’)与图13的曲线图处的面积S2A’相等的方式进行轧制辊15、16的校平控制,能够以形成图12D中附图标记S2B所示的三角形的方式对金属板90赋予第二伸长差E2(参照图12D)。这是因为,在图12D中附图标记S2B所示的三角形与图13的曲线图的面积S2B’具有特定的相关关系,并且图12D中附图标记S2A所示的三角形与附图标记S2B所示的三角形相似。
在步骤S216中,基于在步骤S214中计算出的控制指令值,进行轧制辊15、16的校平控制。需要说明的是,在第一伸长差E1与第二伸长差E2之差|E1-E2|在未落入规定范围内的期间反复进行步骤S216的控制(步骤S218的否)。而且,若上述之差|E1-E2|在规定范围内(步骤S218的是),则步骤S202~S206中检测出的金属板90的前端弯曲被纠正,因此再次返回步骤S202,进行接下来可能产生金属板90的前端弯曲的检测。
由于金属板90的前端弯曲而产生的第一伸长差E1表示金属板90的流出方向向板宽方向一侧偏移的大小。关于这一点,根据上述的实施方式,计算由于金属板90的前端弯曲而产生的第一伸长差E1,并且进行轧制辊15、16的压下校平控制,以使上述的第二伸长差E2与上述的第一伸长差E1相等。即,以将与由于金属板90的前端弯曲而在金属板90的一端侧(在此为第一端缘92侧)产生的伸长(与第一伸长差E1对应的伸长)相同的大小的伸长(与第二伸长差E2对应的伸长)向金属板90的另一端侧(在此为第二端缘93侧)赋予的方式进行压下校平控制,因此能够适当地纠正金属板90的前端弯曲,使金属板90的前端缘(前端91)与收卷装置14的轴向接近平行。由此,能够利用收卷装置适当地收卷进行了前端无张力轧制的金属板。
另外,由于金属板90的前端弯曲而在金属板90上产生的上述的第一伸长差E1与上述的板端位置xB相对于基准位置的偏移量Δe的时间积分具有相关关系,典型地第一伸长差E1与前述的偏移量Δe的时间积分具有比例关系。关于这一点,根据上述的实施方式,基于前述的偏移量Δe的时间积分,能够适当地计算第一伸长差E1。因此,在第二校平步骤中,通过以将与这样计算出的第一伸长差E1相等的第二伸长差E2赋予金属板90的方式进行压下校平控制,能够适当地纠正金属板90的前端弯曲。
另外,在上述的实施方式中,在金属板90的前端弯曲产生后,计算金属板90的前端91到达收卷装置14为止的剩余时间Tc,在计算出的剩余时间Tc内对金属板90赋予第二伸长差E2,因此金属板90在开始收卷前适当地纠正金属板90的前端弯曲。
在上述的实施方式中,实施方式中,基于检测出的板端位置xB的相对于基准位置的偏移量Δe的时间积分,计算第一伸长差E1,基于该第一伸长差E1,进行轧制辊15、16的压下校平控制。与此相对,在图14的流程图的实施方式中,基于金属板90的前端弯曲产生时的、金属板90的流出方向相对于输送方向的偏移角度,进行轧制辊15、16的压下校平控制。更具体而言,在图14的流程图的实施方式中,基于第一校平步骤的开始时间点的金属板90的流出方向相对于输送方向的一侧(在此为第一端缘92侧)的第一偏移角度θ1(参照图15B),决定第二校平步骤执行中的流出方向相对于输送方向的另一侧(在此为第二端缘93侧)的第二偏移角度θ2(参照图15C)。
在图14的流程图中,步骤S302、S304、S306、S312、S316、S318的内容与图11所示的步骤S202、S204、S206、S212、S216、S218相同,因此详细的说明省略。
在图14所示的流程图的实施方式中,在基于由步骤S302(检测步骤)检测出的板端位置xB由步骤S304计算出的偏移量Δe比阈值大的情况下(步骤S306的是),取得此时间点(第一校平步骤的开始时间点;图15B所示的阶段)的、金属板90的流出方向相对于输送方向的一侧(在此为第一端缘92侧)的第一偏移角度θ1(参照图15B)(步骤S308)。第一偏移角度θ1也可以基于偏移量Δe、输送方向上的轧制辊15、16的中心轴O与由第二板端检测部34进行的板端检测位置之间的距离m来取得(tanθ1=Δe/m)。或者,也可以根据拍摄装置等捕获的图像,取得第一偏移角度θ1。
接下来,基于由步骤S308取得的第一偏移角度θ1,决定在第二校平步骤中应赋予金属板90的第二偏移角度θ2、即决定金属板90的流出方向相对于输送方向的另一侧(在此为第二端缘93侧)的第二偏移角度θ2(步骤S310;参照图15C)。
而且,由在步骤S312计算出的剩余时间Tc以内,计算使金属板90的另一侧(在此为第二端缘93侧)的偏移角度成为上述的第二偏移角度θ2那样的、针对压下装置22及轧制辊15、16的驱动马达的控制指令值(步骤S314)。而且,基于这样计算出的控制指令值,进行轧制辊15、16的校平控制(第一校平步骤以及第二校平步骤)(步骤S316)。而且,若向金属板90的另一侧(在此为第二端缘93侧)的偏移角度成为上述的第二偏移角度θ2(步骤S318的是),则在步骤S302~S306中检测出的金属板90的前端弯曲被纠正,因此再次返回步骤S302,进行接下来可能产生金属板90的前端弯曲的检测。
由于金属板90的前端弯曲而产生的金属板90的流出方向相对于输送方向的一侧(在此为第一端缘92侧)的第一偏移角度θ1与前述的第一伸长差E1相同,表示金属板90的流出方向的板宽方向所述一侧(第一端缘92侧)的偏移的大小。关于这一点,在上述的实施方式中,基于前述的第一偏移角度θ1,能够适当地决定第二校平步骤执行中的流出方向相对于输送方向的另一侧的第二偏移角度θ2。因此,通过以将这样决定的第二偏移角度θ2赋予金属板90的方式进行压下校平控制,能够适当地纠正金属板90的前端弯曲,使金属板90的前端缘与收卷装置14的轴向接近平行。由此,能够利用收卷装置14适当地收卷进行了前端无张力轧制的金属板90。
需要说明的是,由步骤S310决定的第二偏移角度θ2可以在步骤S316的第二校平步骤中一次赋予金属板90(参照图15C),或者也可以分割为多次赋予金属板90(参照图15D)。在图15D中,作为向金属板90的另一侧(第二端缘93侧)的偏移角度,第一次赋予角度θ2a、第二次赋予角度θ2b、第三次赋予角度θ2c。在此,θ2a、θ2b以及θ2c之和为θ2(θ2a+θ2b+θ2c=θ2)。
在该情况下,与对金属板90的另一侧(第二端缘93侧)一次赋予较大的第二偏移角度θ2的情况下(参照图15C)相比,分割少量的第二偏移角度θ2a、θ2b以及θ2c而赋予金属板90,因此能够更稳定地纠正金属板90的前端弯曲。
在几个实施方式中,在第一校平步骤结束后,在第一校平步骤所需的时间以下的时间内,开始第二校平步骤。
例如,在参照图11~图12D说明的实施方式中,第一校平步骤的所需时间(从图11的步骤S206的是的判定至步骤S208的结束时间点为止)是从图13的曲线图中的时间点t22至时间点t24为止。而且,在第一校平步骤结束后,到第二校平步骤开始为止的时间是从图13的曲线图中的时间点t24至t25,比上述的第一校平步骤的所需时间短。
另外,在参照图14~15D说明的实施方式中,在步骤S316中无区别地(连续地)进行第一校平步骤以及第二校平步骤,第一校平步骤结束后,到第二校平步骤开始的时间实质上为零,比第一校平步骤(金属板90的流出方向偏移到一侧(第一端缘92侧)开始,直至返回到与输送方向相同的方向为止)的所需时间小。
在该情况下,在第一校平步骤中使金属板90的流出方向沿着输送方向之后,在第一校平步骤所需的时间以下的时间内,开始第二校平步骤,使金属板90的流出方向向另一侧(第二端缘93侧)偏移。即,在第一校平步骤结束后,通过无需太多时间而使金属板90的流出方向向另一侧(第二端缘93侧)偏移,能够减小第二校平步骤结束时间点的、金属板30的前端弯曲部上的板宽方向的中心位置、轧制辊15、16处的金属板90的板宽方向的中心位置的板宽方向上的偏移量(图12D所示的Δd)。(换言之,能够尽量减小图12C、图12D所示的矩形部A1的面积。)例如,如图15C所示,通过连续地进行第一校平步骤与第二校平步骤,上述的偏移量Δd几乎为零。由此,能够利用收卷装置14更适当地收卷进行了前端无张力轧制的金属板90。
以下,对几个实施方式的轧制装置的控制装置以及轧制设备及轧制装置的运转方法记载概要。
(1)本发明的至少一实施方式的轧制装置的控制装置用于控制包含以夹持金属板的方式设置的一对轧制辊的轧制装置,
所述轧制装置的控制装置具备:
第一板端检测部,其构成为在所述金属板的输送方向上设置于所述一对轧制辊的送入侧,并且检测所述输送方向的第一位置处的所述金属板的板宽方向的板端位置;
第二板端检测部,其构成为在所述输送方向上设置于所述一对轧制辊的送出侧,并且检测所述输送方向的第二位置处的所述金属板的板宽方向的板端位置;以及
判定部,其构成为基于由所述第一板端检测部检测出的所述金属板的第一板端位置、以及由所述第二板端检测部检测出的所述金属板的第二板端位置,判定可否开始在所述金属板的送出侧张力为零的状态下利用所述一对轧制辊进行的所述金属板的轧制即前端无张力轧制。
根据上述(1)的结构,在一对轧制辊的送入侧的第一位置以及送出侧的第二位置的每一个处,检测金属板的板宽方向的板端位置(第一板端位置及第二板端位置)。因此,根据这些的检测结果,能够掌握前端无张力轧制开始前的金属板的长度方向相对于输送方向的倾斜的程度,即,能够掌握前端无张力轧制开始时间点的金属板的流出方向相对于输送方向的倾斜的程度。而且,在上述(1)的结构中,根据第一板端位置及第二板端位置的检测结果,判定可否开始前端无张力轧制,因此,例如,在根据上述的检测结果,判断为金属板的长度方向(即,轧制开始时的金属板的流出方向)相对于输送方向大致平行时,能够判定为可以开始金属板的前端无张力轧制。
因此,根据上述(1)的结构,由于能够在金属板的流出方向与输送方向大致平行的状态下开始前端无张力轧制,因此能够抑制金属板的前端部从轧制机的输送线向板宽方向偏离。因此,容易利用收卷装置适当地收卷进行了轧制的金属板。
另外,根据上述(1)的结构,能够在金属板的流出方向与输送方向大致平行的状态下开始前端无张力轧制,因此将在前端无张力轧制开始时取得的第二板端位置用作基准,由此根据在前端无张力轧制中检测出的第二板端位置,能够适当地进行金属板的蛇行控制等轧制机的压下校平控制。
因此,能够利用收卷装置适当地收卷进行了前端无张力轧制的金属板。
(2)在几个实施方式中,上述(1)的结构中,
所述判定部构成为在所述第一板端位置与所述第二板端位置之差在规定范围内时,判定为能够开始所述金属板的所述前端无张力轧制。
第一板端位置与第二板端位置之差表示连结第一板端位置与第二板端位置的方向、即金属板的长度方向相对于轧制机的金属板的输送方向的倾斜的程度。另外,第一板端位置与第二板端位置之差为零是表示金属板的长度方向与输送方向平行。
关于这一点,根据上述(2)的结构,在第一板端位置与第二板端位置之差在规定范围内时,即金属板的长度方向相对于输送方向的倾斜较小、且接近平行时,判定为可以开始金属板的前端无张力轧制。因此,通过按照该判定开始金属板的前端无张力轧制,如上述(1)所示,能够利用收卷装置适当地收卷轧制后的金属板。
(3)在几个实施方式中,上述(1)的结构中,
所述判定部构成为,在所述金属板的板宽方向上的基准位置与所述第一板端位置之差、以及所述基准位置与所述第二板端位置之差在规定范围内时,判定为能够开始所述金属板的所述前端无张力轧制。
板宽方向上的基准位置与第一板端位置之差、以及相同的基准位置与第二板端位置之差分别表示输送方向上的第一位置以及第二位置处的板端位置相对于基准位置的偏移的大小。
关于这一点,根据上述(3)的结构,在第一板端位置相对于基准位置的偏移以及第二板端位置相对于基准位置的偏移相对较小时,即,金属板的长度方向相对于输送方向的倾斜较小、且接近平行时,判定为能够开始金属板的前端无张力轧制。因此,通过按照该判定开始金属板的前端无张力轧制,如上述(1)所述,能够利用收卷装置适当地收卷轧制后的金属板。
(4)在几个实施方式中,上述(1)至(3)任个的结构中,
所述轧制装置的控制装置还具备用于控制所述一对轧制辊的动作的轧制控制部,
所述轧制控制部构成为,在由所述判定部判定为能够开始所述金属板的所述前端无张力轧制时,调节所述一对轧制辊的转速以及压下量,以使所述一对轧制辊与所述金属板接触之后,一边使所述一对轧制辊旋转,一边所述一对轧制辊间的间隙随着所述金属板的输送而逐渐减少至与所述金属板的目标板厚对应的管理值。
在使金属板的前端部穿过一对轧制辊之间的状态下,开始由轧制辊进行的金属板的压下及前端无张力轧制的情况下,有时在金属板中的、未被轧辊轧制的前端部与被轧制的后续部之间板厚之差变大。在该情况下,在利用收卷装置收卷金属板时等,有时应力集中于上述的前端部与后续部的边界,并且导致金属板在该边界被切断。
关于这一点,根据上述(4)的结构,在金属板的前端无张力轧制开始时,调节轧制辊的转速以及压下量,以使一对轧制辊与金属板接触之后,一边使轧制辊旋转,一边轧制辊间的间隙随着金属板的输送而逐渐地减少至与金属板的目标板厚对应的管理值。因此,在具有与轧制前相同的板厚的前端部、以及轧制成目标板厚的后续部之间,形成板厚逐渐减少的转变部。由此,能够缓和在利用收卷装置收卷金属板时等的、在上述的前端部与后续部的边界可能产生的应力集中。由此,能够利用收卷装置适当地收卷轧制后的金属板。
(5)在几个实施方式中,上述(1)至(4)任一个的结构中,
所述轧制装置的控制装置具备:
第一校平部,其构成为在所述金属板的所述前端无张力轧制开始后,在由所述第二板端检测部进行的所述第二板端位置的检测结果从基准位置向板宽方向的一侧偏离时,进行所述一对轧制辊的压下校平控制,以使所述金属板从所述轧制辊的流出方向沿着所述轧制装置中的所述金属板的输送方向;以及
第二校平部,其构成为在由所述第一校平部进行的压下校平控制之后,进行所述一对轧制辊的压下校平控制,以使所述金属板从所述轧制辊的流出方向相对于所述输送方向向所述板宽方向的另一侧偏移之后,使所述金属板的所述流出方向返回所述输送方向。
根据上述(5)的结构,由于一边在前端无张力的状态下进行金属板的轧制,一边在轧制辊的送出侧的位置处检测金属板的板宽方向的板端位置,因此基于检测出的板端位置从基准位置向板宽方向的一侧偏离的情况,能够检测出产生了金属板的流出方向向板宽方向一侧的偏移(金属板的前端弯曲)的情况。而且,在检测出金属板的前端弯曲时,通过压下校平控制,在使金属板的流出方向沿着轧制装置中的金属板的输送方向之后,使金属板的流出方向相对于输送方向向板宽方向的另一侧偏移,然后以使流出方向沿着输送方向的方式进行压下校平控制,因此在纠正金属板的前端弯曲,使金属板的前端缘与收卷装置的轴向接近平行的状态下,能够继续进行前端无张力轧制。因此,根据上述(5)的结构,能够利用收卷装置适当地收卷进行了前端无张力轧制的金属板。
(6)本发明的至少一实施方式的轧制设备具备:以夹持金属板的方式设置的一对轧制辊、以及上述(1)至(5)中任一项所述的控制装置。
根据上述(6)的结构,在一对轧制辊的送入侧的第一位置以及送出侧的第二位置的每一个处,检测金属板的板宽方向的板端位置(第一板端位置及第二板端位置)。因此,根据这些的检测结果,能够掌握前端无张力轧制开始前的金属板的长度方向相对于输送方向的倾斜的程度,即,能够掌握前端无张力轧制开始时间点的金属板的流出方向相对于输送方向的倾斜的程度。而且,在上述(6)的结构中,根据第一板端位置及第二板端位置的检测结果,判定可否开始前端无张力轧制,因此,例如,在根据上述的检测结果判断为金属板的长度方向(即,轧制开始时的金属板的流出方向)相对于输送方向大致平行时,能够判定为可以开始金属板的前端无张力轧制。
因此,根据上述(6)的结构,由于能够在金属板的流出方向与输送方向大致平行的状态下开始前端无张力轧制,因此能够抑制金属板的前端部从轧制机的输送线向板宽方向偏离。因此,容易利用收卷装置适当地收卷进行了轧制的金属板。
另外,根据上述(6)的结构,能够在金属板的流出方向与输送方向大致平行的状态下开始前端无张力轧制,因此将在前端无张力轧制开始时取得的第二板端位置用作基准,由此根据在前端无张力轧制中检测出的第二板端位置,能够适当地进行金属板的蛇行控制等轧制机的压下校平控制。
因此,能够利用收卷装置适当地收卷进行了前端无张力轧制的金属板。
(7)在几个实施方式中,上述(6)的结构中,
所述轧制设备还具备在所述输送方向上设置于比所述第二板端检测部靠下游侧的收卷装置,
所述一对轧制辊和所述收卷装置在所述输送方向上的距离为L2时,所述一对轧制辊与所述第二板端检测部在所述输送方向上的距离为0.1×L2以下。
为了通过配置于轧制辊的送出侧的第二板端检测部来检测金属板的板端位置(第二板端位置),需要将输送方向上的金属板的前端的位置配置于与第二板检测部相同或比其靠下游侧。关于这一点,根据上述(7)的结构,在输送方向上,由于第二板端检测部与轧制辊之间的距离相对较短,因此能够一边使无张力轧制开始时的金属板的前端位置比较接近轧制辊,一边在无张力轧制开始时以及无张力轧制中检测第二板端位置的检测。因此,能够缩短金属板中未被轧制的前端部的长度,并且能够适当地进行前端无张力轧制,由此能够提高金属板的成品率。
(8)在几个实施方式中,在上述(6)或(7)的结构中,
所述轧制设备还具备在所述输送方向上设置于比所述第一板端检测部靠上游侧的放卷装置,
在将所述一对轧制辊与所述放卷装置的所述输送方向上的距离设为L1时,所述一对轧制辊与所述第一板端检测部在所述输送方向上的距离为0.1×L1以下。
在使穿过一对轧制辊间的金属板往复且进行轧制的轧制装置(反向轧机)的情况下,在第一道次结束后的第二道次中,金属板的输送方向反转,从金属板的后端侧开始由轧制辊进行的轧制。关于这一点,根据上述(8)的实施方式,在第二道次中的输送方向(与第一道次的输送方向相反的方向)上,由于使第一板端检测部与轧制辊间的距离比较短,因此能够一边使第二道次的无张力轧制开始时的金属板的后端位置比较接近轧制辊,一边在无张力轧制开始时以及无张力轧制中检测第一板端位置。因此,能够缩短金属板中的未被轧制的后端部的长度,并且能够适当地进行前端无张力轧制,由此能够提高金属板的成品率。
(9)在几个实施方式中,上述(6)至(7)任一个的结构中,
所述轧制设备具备板厚计,该板厚计构成为在所述输送方向上设置于所述一对轧制辊的送入侧或送出侧中的至少一方,并用于计测所述金属板的板厚,
所述第一板端检测部或所述第二板端检测部在所述输送方向上位于所述一对轧制辊与所述板厚计之间。
为了良好地响应控制,用于控制金属板的板厚的板厚计优选在输送方向上设置于轧制辊的附近。关于这一点,根据上述(9)的结构,与用于计测金属板的板厚的板厚计相比,在输送方向上进一步在轧制辊的附近设置第一板端检测部或第二板端检测部,因此能够一边使无张力轧制开始时的金属板的前端位置更靠近轧制辊,一边在无张力轧制开始时以及无张力轧制中检测第一板端位置或第二板端位置。因此,能够缩短金属板中的未被轧制的前端部的长度,并且能够适当地进行前端无张力轧制,由此能够提高金属板的成品率。
(10)在几个实施方式中,上述(6)至(9)任一个的结构中,
所述第一板端检测部或者第二板端检测部构成为使用放射线检测所述第一板端位置或所述第二板端位置。
轧制辊的附近多为轧制油、烟尘大量飞散,轧制辊有振动、黑暗等严酷的环境。关于这一点,根据上述(10)的结构,由于使用利用放射线检测板端位置的第一板端检测部或第二板端检测部,因此即使配置于严酷的环境下的轧制辊的附近,也能够适当地检测板端位置。
(11)在几个实施方式中,上述(6)至(10)任一个的结构中,
所述轧制设备具备:
作为所述一对轧制辊的一对第一轧制辊;
作为所述一对轧制辊的一对第二轧制辊,它们在所述输送方向上设置于比所述一对第一轧制辊靠下游侧的位置;
放卷装置,其设置于比所述一对第一轧制辊靠上游侧的位置;以及
收卷装置,其设置于比所述一对第二轧制辊靠下游侧的位置,
所述控制装置构成为,判定可否开始所述一对第一轧制辊中的所述金属板的第一次的前端无张力轧制,在判定为能够开始所述第一次的前端无张力轧制,并且在开始利用所述一对第一轧制辊进行的前端无张力轧制之后,判定可否开始所述一对第二轧制辊中的所述金属板的第二次的前端无张力轧制。
根据上述(11)的结构,在沿输送方向排列的第一轧制辊以及第二轧制辊的每一个处,如上述(1)所述进行可否开始前端无张力轧制的判定,根据该判定结果,开始前端无张力轧制,因此一边能够利用收卷装置适当地收卷由这些的轧制辊进行了的前端无张力轧制的金属板,一边能够使用两对轧制辊更高效地进行轧制。
(12)本发明的至少一实施方式的轧制装置的运转方法是包含以夹持金属板的方式设置的一对轧制辊的轧制装置的运转方法,其中,
所述轧制装置的运转方法包括:
第一板端检测步骤,在所述第一板端检测步骤中,检测在所述金属板的输送方向上所述一对轧制辊的送入侧的第一位置处的所述金属板的板宽方向的板端位置即第一板端位置;
第二板端检测步骤,在所述第二板端检测步骤中,检测在所述输送方向上所述一对轧制辊的送出侧的第二位置处的所述金属板的板宽方向的板端位置即第二板端位置;以及
判定步骤,在所述判定步骤中,基于由所述第一板端检测步骤检测出的所述第一板端位置以及由所述第二板端检测步骤检测出的所述第二板端位置,判定可否开始在所述金属板的送出侧张力为零的状态下的利用所述一对轧制辊进行的所述金属板的轧制即前端无张力轧制。
根据上述(12)的方法,在一对轧制辊的送入侧的第一位置以及送出侧的第二位置的每一个处,检测金属板的板宽方向的板端位置(第一板端位置及第二板端位置)。因此,根据这些的检测结果,能够掌握前端无张力轧制开始前的金属板的长度方向相对于输送方向的倾斜的程度,即,能够掌握前端无张力轧制开始时间点的金属板的流出方向相对于输送方向的倾斜的程度。而且,上述(12)的方法中,根据第一板端位置及第二板端位置的检测结果,判定可否开始前端无张力轧制,因此,例如,根据上述的检测结果,判断为金属板的长度方向(即,轧制开始时的金属板的流出方向)相对于输送方向大致平行时,能够判定为可以开始金属板的前端无张力轧制。
因此,根据上述(12)的方法,由于能够在金属板的流出方向与输送方向大致平行的状态下开始前端无张力轧制,因此能够抑制金属板的前端部从轧制机的输送线向板宽方向偏离。因此,容易利用收卷装置适当地收卷进行了轧制的金属板。
另外,根据上述(12)的方法,能够在金属板的流出方向与输送方向大致平行的状态下开始前端无张力轧制,因此将在前端无张力轧制开始时取得的第二板端位置用作基准,由此根据在前端无张力轧制中检测出的第二板端位置,能够适当地进行金属板的蛇行控制等轧制机的控制。
因此,能够利用收卷装置适当地收卷进行了前端无张力轧制的金属板。
以上,对本发明的实施方式进行了说明,但本发明并不限定于上述的实施方式,还包括对上述的实施方式施加了变形的方式、将这些方式适当组合而得到的方式。
在本说明书中,“在某一方向上”、“沿着某一方向”、“平行”、“正交”、“中心”、“同心”或“同轴”等表示相对或绝对的配置的表述不仅严格地表示这样的配置,也表示具有公差、或具有可获得相同功能的程度的角度、距离而相对位移的状态。
例如,“相同”、“相等”以及“均质”等表示事物相等的状态的表述不仅表示严格相等的状态,还表示存在公差、或者能够得到相同功能的程度的差的状态。
另外,在本说明书中,表示四边形、圆筒形状等形状的表现不仅表示几何学上的严格意义的四边形、圆筒形状等形状,还表示在获得相同效果的范围内包括凹凸部、倒角部等的形状。
另外,在本说明书中,“具备”、“包含”或者“具有”一个构成要素这样的表现并非排除其他构成要素的存在的排他性表现。
附图标记说明
1 轧制设备
2 轧制装置
4 放卷装置
5 轧制辊
6 送入侧夹辊
8 侧引导件
10 轧制机
10A 第一轧制机
10B 第二轧制机
12 送出侧夹辊
14 收卷装置
15 轧制辊
15A 第一轧制辊
15B 第二轧制辊
16 轧制辊
16A 第一轧制辊
16B 第二轧制辊
17 中间辊
18 中间辊
19 支承辊
20 支承辊
22 压下装置
30 金属板
32 第一板端检测部
32A 第一板端检测部
32B 第一板端检测部
34 第二板端检测部
34A 第二板端检测部
34B 第二板端检测部
36 板厚计
38 板厚计
40 控制器
42 判定部
44 轧制控制部
46 第一校平部
48 第二校平部
50 伸长差计算部
52 偏移角度计算部
54 剩余时间计算部
90 金属板
90a 前端部
90b 转变部
90c 后续部
91 前端
92 第一端缘
93 第二端缘
94 第一表面
95 第二表面
100 控制装置
A1 矩形部
Lc 中心线
O 中心轴
S2A’ 面积
S2B’ 面积
Y1 第一位置
Y2 第二位置
m 距离
x1 第一板端位置
x2 第二板端位置
xB 板端位置
xref 基准位置
Δe 偏移量
θ1 第一偏移角度
θ2 第二偏移角度。