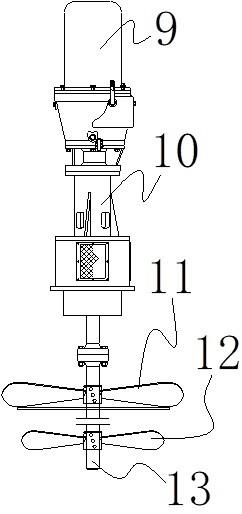
1.本发明涉及一种冷轧乳化液粒径尺寸的控制方法,属于冷轧技术领域。
背景技术:
2.目前冷轧工艺大都采用乳化液对轧辊和带钢进行润滑和冷却,乳化液系统的控制参数与设定的与轧制钢种、带钢规格、轧制速度、轧制力以及乳化液品质等因素(轧制条件)相适应。与热轧工艺润滑不同,冷轧过程中工艺润滑是轧制工艺中的尤为重要的环节,因为热轧过程中氧化膜、水也可以起到一部分的润滑作用,而且材料变形抗力较低,但是,在冷轧过程中由于材料加工硬化、变形抗力增加,导致轧制力升高,同时,随着轧制速度的升高,轧辊发热,必须采用兼有冷却作用的乳化剂进行工艺润滑以此来减少摩擦、降低轧制压力,冷却轧辊和控制板型。
3.冷轧工艺的发展趋势在于最大限度提高轧制速度、高速轧制薄料、降低轧辊磨损和延长轧辊寿命,减少换辊时间,提高生产率等方面,主要表现在提高板形控制能力、降低对来料板形的依赖性。因而冷轧工艺体现出对轧制液提出更高的要求,更高润滑能力以满足更薄、更硬的轧制要求,降低能耗并提高轧机及板面清净性。
4.通过对轧制油的润滑机理分析,一个涉及到粒径尺寸大小随时间增加的问题,这一般是由于被称作ostwald ripening 的过程引起的,在这个过程中乳化的低分子量的硅烷化合物在水中有足够的溶解度,就使得它通过水相由较小的颗粒扩散为较大的颗粒,就导致乳化液的平均颗粒大小随时间增加而增大。由于随着使用时间的增加,乳化液的粒径逐渐粗化长大,反映在轧制过程中便会出现咬入困难、轧件跑偏、打滑的现象。可见粒径越小,粘度越大,表现为摩擦系数越高,不易打滑。
5.实践证明,乳液粒径尺寸对轧制性能以及稳定性至关重要,偏大轧制性能好,而稳定性较差,严重的会使乳化液油水分离影响到乳化液的使用效果和使用周期;偏小稳定性较好,轧制性能较差,因此要在生产实际中必须找出晶粒大小与轧制性能、乳化液稳定性之间的最佳结合点。乳化液粒径的不同,除了表现出不同的外观外,主要还是对其润滑性能和热稳定性产生影响。较大粒径有利于乳化液受热时油水两相分离,但轧辊和轧件表面吸附油量增加,降低轧制变形区摩擦系数,然而,乳化液粒径过大,容易造成乳化液不稳定,严重的会使乳化液油水分离影响到乳化液的使用效果和使用周期.乳化液一旦分层必将导致原油浮于箱体上层,被除油机捕获并排放,造成原油的浪费和环境的污染,系统本身也会因为原油的丧失导致浓度下降,润滑性能不足,必须添加原油来增加浓度,造成原油的损耗。
6.轧机漏油(液压油、润滑油)现象是无法避免的,一旦产生泄漏,势必将有大量的矿物油,进入到乳化液系统当中,造成系统皂化值的下降,乳粒尺寸变大,润滑性能不足。
7.国内现有乳化液机械推进式搅拌器,采用的是单叶轮搅拌结构,但对于体积大、深度深的大箱体搅拌能力是不足的,乳液容易分层,技术人员进行了进一步的探究,也通过检索查找了现有相关业内通用技术,遂将机械搅拌器由原先的单层叶轮改进为双层叶轮,但
实际使用下来负载大,减速机损坏频率高,搅拌效果不良。为了解决分层问题,又将叶轮设置为大小不一的两种结构,为了保证整箱搅拌效果,采用上小下大的结构,由于受力不平衡导致叶轮离心力加大损坏折断,通过传动轴传递到另外一组叶轮上,使下叶轮偏心变大,从而增加了离心力,动作迟缓,下叶轮损坏的主要原因就是因为上叶轮先损坏造成的。
8.为了确保轧材获得最优的板型和质量,设计时采用机械搅拌装置来控制乳化液系统平均粒径。原先采用机械推进式搅拌装置,粒径在【10、12um】比例占到90%以上,5~10um不足10%,2~5um为1%以下,是有效防止了乳化液分层、但润滑性能还是没有达到最佳状态,因粒径的大小直接影响到乳化液的润滑性能,要想保持稳定高效运行,2~5um粒径比例占达到50%以上,后期需要继续对主箱内搅拌器结构和控制方面继进行优化摸索实践。
技术实现要素:
9.本发明要解决技术问题是:克服上述技术的缺点,提供一种解决现有技术存在的现场乳化液粒径大小与轧制性能、乳化液稳定性之间难以调和的技术问题,尤其解决了粒径被控制在2-5um>50% 、5-10um <35%、10-15um<15%、大于15um<1%,有效防止乳化液分层的同时、润滑性能还处于最佳状态,满足了生产实际中粒径大小与轧制性能、乳化液稳定性之间的最佳结合点。
10.为了解决上述技术问题,本发明提出的技术方案是:一种冷轧乳化液粒径尺寸的控制方法,包括如下步骤:步骤1:配置乳化液;步骤2:运行中控制泵出口压力在0.7mpa至0.9mpa,喷嘴压力在6bar到8bar;步骤3:运行中控制乳化液中可溶性矿物离子含量;具体为控制乳化液的ph值在4.6至5.2;步骤4:搅拌;由搅拌器完成,所述搅拌器分为推进式搅拌装置和均匀混合式搅拌装置;所述推进式搅拌装置搅拌覆盖面积为3m
2 ,并根据乳化液箱的尺寸于布置在所述乳化液箱的不同位置,110m3的乳化液箱内设置3个推进式搅拌装置,且在箱体内以等边三角形排列;180m3的乳化液箱内设置4个推进式搅拌装置,且在箱体内以等边菱形排列;所述均匀混合式搅拌装置在每个乳化液箱内设置1个,且在110m3的乳化液箱内设置在等边三角形的中心,在180m3的乳化液箱内设置等边菱形的中心;步骤5:控制废油占乳化液重量的1.5%以下。
11.上述方案进一步的改进在于:所述步骤1中,配置乳化液包括配置大量乳化液和配置少量乳化液;配置少量乳化液时,使用预配液箱;所述预配液箱内设置有机械推进式搅拌器以及相应的蒸汽管道和蒸汽切断阀,所述预配液箱为圆柱状结构;所述搅拌器设置在所述预配液箱的中心;所述蒸汽管道沿所述预配液箱内壁环绕;所述蒸汽切断阀与所述预配液箱内温度传感器连锁;配置大量乳化液时,由原油箱和脱盐水箱经过补充泵向所述乳化液箱内补充,所述补充管道上设置有流量计,所述流量计为超声流量计。
12.上述方案进一步的改进在于:所述步骤3中,当乳化液的ph值小于4.6,且导电率上升;加强酸洗线漂洗,增加吹扫来降低带钢上cl-的夹带,在乳化液箱中采用奥氏不锈钢管
件吸附乳化液箱中多余含量的cl-残余;当乳化液的ph值为4.6至5.2,且导电率上升;采用沸石吸附乳化液中的ga2+、mg2+ 阳离子;当乳化液的ph值大于5.2时,且导电率上升;加强酸洗线漂洗。
13.上述方案进一步的改进在于:所述推进式搅拌装置包括,驱动电机,减速机,小叶轮,大叶轮;所述驱动电机通过所述减速机驱动所述大叶轮和小叶轮,所述大叶轮与所述小叶轮共轴,且所述大叶轮安装在所述小叶轮上方,所述小叶轮的下方具有伸出轴13;所述均匀混合式搅拌装置包括,轴套、配重调节板、基盘和传动轴;所述轴套套装在所述传动轴上,所述配重调节板套装在所述轴套上,所述基盘套装在所述配重调节板上,所述基盘上具有均匀设置的若干混液孔;所述基盘的外缘竖直设置有若干搅拌滑板。
14.上述方案进一步的改进在于:根据公式,rcf=11.18*(rpm/1000)*2*r*rpm=299*√rcf/r;可换算:r/min=1000*[g/(11.08*r)]*1/2,式中:r为推进式搅拌装置的旋转半径,rcf为相对离心力,rpm为转速,r为离心机轴中心到水平离心机底座的距离;所述推进式搅拌装置输出最大转速300 rpm,所述均匀混合式搅拌装置输出最大转速180rpm。
[0015]
上述方案进一步的改进在于:所述步骤5中,使用归拢装置和弃除装置;所述归拢装置设置在乳化液箱的一侧,包括,曲管;所述曲管上均匀分布有若干吹口,所述吹口朝向一点,形成扇形气刀结构;所述曲管能够通入压缩空气,并自所述吹口喷出并 沿着所述乳化液箱内液面吹扫,将乳化液表面的废油吹向所述弃除装置;所述弃除装置包括有废油输出泵,浆状废油输送器,所述废油输出泵为气动隔膜泵;所述浆状废油输送器具有桨板,能够降废油集中至所述废油输出泵入口。
[0016]
上述方案进一步的改进在于:所述步骤5之后,还包括使用激光粒度分布仪测量乳化液的粒度。
[0017]
本发明提供的冷轧乳化液粒径尺寸的控制方法,从预配乳化液开始,到搅拌、废油集拢、弃除,再到可溶性矿物离子的含量控制,整体设计巧妙,结构简单紧凑,利用多种措施并巧妙的结合起来,有效改善了乳化液系统的粒径比例,在稳定粒径尺寸的同时,优化了轧制变形区摩擦系数,基本杜绝了咬入困难、轧件跑偏、打滑的现象,有效的形成乳化液系统治理和企业经济发展相互协调的良性循环;本发明提供的方法简便易制作,充分利用乳化液箱体的空间,快捷高效的完成搅拌、吹扫、集拢、收集、排放以及可溶性矿物离子的吸附,比较好的实现预期的目标;在保证生产工艺需要的前提下,具有简单易行、不受场地限制的优点;通过对乳化液粒径有效控制后,提高了稳定性,避免了分层以及延长了乳化液的使用寿命,将原先的设备进行改进,并对搅拌装置结构和除油装置结构进行优化;在乳化液的稳定性和可靠度是现有技术所无法比拟的,能很好的适应冷轧高速连续性生产板形控制的要求。
附图说明
[0018]
图1是本发明的均匀混合式搅拌装置结构示意图。
[0019]
图2为图1的仰视结构示意图。
[0020]
图3为本发明推进式搅拌装置结构示意图。
[0021]
图4为本发明废油归拢装置结构示意图。
[0022]
图5为本发明废油弃除装置结构示意图。
[0023]
图6为图5具体结构示意图。
[0024]
图7为本发明运行中压力控制结构示意图。
具体实施方式实施例
[0025]
本实施例提供的冷轧乳化液粒径尺寸的控制方法,包括如下步骤:步骤1:配置乳化液;配置乳化液包括配置大量乳化液和配置少量乳化液;少量用于对系统的零星补充;大量用于系统的乳化液排放后的补充。
[0026]
配置少量乳化液时,使用预配液箱;预配液箱内设置有机械推进式搅拌器以及相应的蒸汽管道和蒸汽切断阀,预配液箱为圆柱状结构;搅拌器设置在预配液箱的中心;蒸汽管道沿预配液箱内壁环绕;蒸汽切断阀与预配液箱内温度传感器连锁;在plc 中根据温度设定范围进行控制,温度超过设定值关蒸汽切断阀,温度低于设定值开启蒸汽切断阀,从而保持预配液温度在工艺设定值范围内。
[0027]
配置大量乳化液时,由原油箱和脱盐水箱经过补充泵向乳化液箱内补充,补充管道上设置有流量计,流量计为超声流量计;流量计信号在hmi 上显示实时值的同时参与预配液槽原油配比批量控制和循环箱一次充填时的原油配比批量控制;在开机初次充填时,将原油直接投加入循环箱内,关闭切断阀,在plc 中根据工艺设定值,对原油流量进行配比批量控制,通过流量计的单位累计流量控制原油投加泵;便于一定比例的配比,达到所需浓度,流量计与乳化液箱内液位计联锁,大流量补充有远程/本地、手动/自动的切换开关控制;便于浓度检测异常,原油和脱盐水的单独补充用。
[0028]
步骤2:运行中控制泵出口压力在0.7mpa至0.9mpa,喷嘴压力在6bar到8bar;泵出口压力控制环节由变频调节,供液泵采用多级离心泵,变频控制,马达转速与泵出口总管上的压力变送器联锁,形成闭环控制。
[0029]
喷嘴压力调整环节,系统上机架管道采用压力控制模式,压力闭环控制模式, 由压力变送器与气动压力调节阀形成闭环,使各相关喷射梁的入口乳化液压力达到设定值,流量计作为闭环控制的补充。压力变送器采用信号:4~20madc两线制制式。气动压力调节阀采用输入信号4~20ma、气开模式。喷嘴压力6-8bar;大于10bar过高,过度反弹、小于4bar,油品分离不足;运行中压力控制涉及到的设备如图7,包括有:压力传感器25,压力调节器26,气源调节装置27,电气阀门定位器28,喷嘴29,继动器30,调节阀31,行程调节件32,挡板33,压力信号转换器34,弹簧35,反馈杆36,供液管道37。
[0030]
在轧制过程中需要对乳化液的喷射压力和流量进行调节,流量要适应喷射控制装置的要求,并且压力一旦设定,无论喷射流量如何变化,压力仍稳定,为此,在压力控制环节中设置了压力控制装置和旁路控制装置以满足上述要求,压力控制装置主要起到调整和控制压力的作用,而旁路控制装置主要起到稳压和调整流量的作用。压力调节装置主要由调
节阀31、电器阀门定位器28、压力传感器25和压力调节器26所组成。
[0031]
喷嘴压力调整动作过程为:首先通过压力调节器26设定上机架的喷射压力,压力调节器26输出信号同压力传感器25测得的阀的压力,并由压力信号转换器34将出口压力转换的电信号进行比较,输出压力信号至电器阀门定位器28,将电信号转换为气压信号来控制电器阀门定位器28的相应元件,包括有喷嘴29,继动器30,行程调节件32,挡板33,压力信号转换器34,弹簧35,反馈杆36等,输出气压信号控制调节阀31的开度,只要调节阀31出口压力同设定的压力值不同,电气阀门定位器28中输出的气压信号就不同,即增大或减小,从而使调节阀31的开度发生变化,直到p1同压力设定值相等为止。改控制阀的特点是使用方便,可根据实际情况进行无级调压,而且可以通过显示器观察到喷射油压,实现比闭环控制,为了避免该调节装置对流量以及压力变化调节的滞后时间。加大了供液管道37的通径尺寸,由原先的dn300改进为dn420。
[0032]
步骤3:运行中控制乳化液中可溶性矿物离子含量;具体为控制乳化液的ph值在4.6至5.2;当乳化液的ph值小于4.6时;而电导率上升,酸洗线cl-,盐酸的挟带,降低了乳化液稳定性;通过加强酸洗线漂洗,来控制酸洗线漂洗水电导率;再通过增加吹扫的方法来降低带钢上cl-的夹带,后在乳化液箱中采用隔箱填充内奥氏不锈钢管件的办法吸附乳液中多余含量的cl-残余。
[0033]
当乳化液的ph值为4.6至5.2时,而电导率上升,由于水的挥发,残留中性盐增加及冷却水泄漏,也将降低乳化液的稳定性,通过采用沸石的吸附ga2+、mg2+ 阳离子的方法来保证含量,其特征:内部表面积大,每克沸石的比表面积可达355~1000
㎡
,对离子吸附量很大,沸石内部通道大小较为均匀、固定,孔径大小为0.3~1.0nm,小于其直径的物质被牢牢吸附,考虑到离子与分子之间的直径差异,吸附具有选择性,沸石晶体大量孔穴和孔道,使沸石具有很大的比表面积,加上独特的晶体结构从而形成静电引力,使得沸石具有很大的应力场,产生较强的吸附性能;当乳化液的ph值大于5.2时,而电导率也上升,碱性清洗剂进入到乳化液中并污染了乳化液,考虑到酸轧线几乎不存在此类问题,只需加强酸洗线漂洗,控制酸洗线电导率。
[0034]
步骤4:搅拌;由搅拌器完成,搅拌器分为推进式搅拌装置和均匀混合式搅拌装置;推进式搅拌装置搅拌覆盖面积为3m
2 ,并根据乳化液箱的尺寸于布置在乳化液箱的不同位置,110m3的乳化液箱内设置3个推进式搅拌装置,且在箱体内以等边三角形排列;180m3的乳化液箱内设置4个推进式搅拌装置,且在箱体内以等边菱形排列;均匀混合式搅拌装置在每个乳化液箱内设置1个,且在110m3的乳化液箱内设置在等边三角形的中心,在180m3的乳化液箱内设置等边菱形的中心;推进式搅拌装置如图3所示,包括,驱动电机9,减速机10,小叶轮12,大叶轮11;驱动电机9通过减速机10驱动大叶轮11和小叶轮12,大叶轮11与小叶轮12共轴,且大叶轮11安装在小叶轮12上方,小叶轮12的下方具有伸出轴13;使其伸出起到定心作用。这样小叶轮12、大叶轮11和伸出轴13在空间形成一种陀螺状的空间结构,降低了装置运转时的振动量,保证了其运转时的稳定性;大叶轮11和小叶轮12之间通过锁紧螺母与传动轴连接,传动轴又与联轴器联结,其目的是便于叶轮拆卸。
[0035]
均匀混合式搅拌装置如图1和图2所示,包括,轴套1、配重调节板3、基盘4和传动轴
7;轴套1套装在传动轴7上,配重调节板3套装在轴套1上,基盘4套装在配重调节板3上,基盘4上具有均匀设置的若干混液孔5;基盘4的外缘竖直设置有若干搅拌滑板8。
[0036]
根据公式,rcf=11.18*(rpm/1000)*2*r*rpm=299*√rcf/r;可换算:r/min=1000*[g/(11.08*r)]*1/2,式中:r为推进式搅拌装置的旋转半径,rcf为相对离心力,rpm为转速,r为离心机轴中心到水平离心机底座的距离;推进式搅拌装置输出最大转速300 rpm,均匀混合式搅拌装置输出最大转速180rpm。
[0037]
步骤5:控制废油占乳化液重量的1.5%以下;废油包括有液压油、轴承润滑油等,废油在系统运行中无法避免,但含量必须控制在1.5%以内,否则会造成乳化液的皂化值明显降低,乳粒尺寸变大,降低了乳化液的润滑能力,不仅如此,皂化值与乳化液中粒径大小及颗粒度分布关系很大,特别是随着乳化液的使用,颗粒度的分布会发生变化,导致润滑性能的变化,最终使得轧制过程中轧制力、张力等因素的发生波动。
[0038]
使用归拢装置和弃除装置清除废油。
[0039]
归拢装置设置在乳化液箱的一侧,如图4所示,包括,曲管20;曲管20上均匀分布有若干吹口19,吹口朝向一点,也即是折转吹扫点21,形成扇形气刀结构;曲管20能够通入压缩空气,并自吹口19喷出并沿着乳化液箱内液面吹扫,将乳化液表面的废油吹向弃除装置;曲管20通入压缩空气后,空气经过折转吹扫放大板18,面积被放大,沿着液面吹扫,废油15再经过废油集拢区17收集到弃除装置16。
[0040]
弃除装置16如图5和图6,包括有废油输出泵23,浆状废油输送器24,废油输出泵23为气动隔膜泵;浆状废油输送器24具有桨板,能够降废油集中至废油输出泵入口。
[0041]
步骤5之后,还包括使用激光粒度分布仪测量乳化液的粒度;以便对粒度进行监控。
[0042]
本发明不局限于上述实施例。凡采用等同替换形成的技术方案,均落在本发明要求的保护范围。