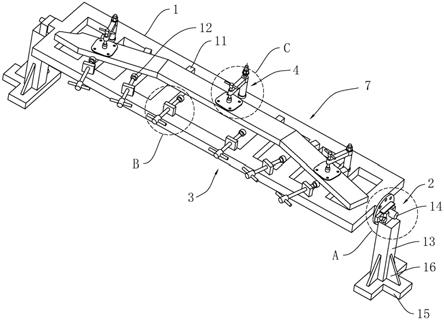
1.本技术涉及轨道车辆加工的领域,尤其是涉及一种轨道车辆司机室骨架焊胎。
背景技术:
2.轨道车辆是一种统称,泛指有专用轨道的车辆.包括传统的火车,此外动车组,地铁车辆,轻轨车辆,磁浮车辆也都属于轨道车辆范畴。轨道车辆司机室骨架是组成司机室的重要组成部分,使得司机室具有良好的结构强度,轨道车辆司机室骨架通常为金属焊接构件。
3.如图1,焊接构件7包括主骨架71和副骨架72,副骨架72设置有两个并设置在主骨架71的两端,两个所述副骨架72在背离主骨架71的一端均朝向主骨架71宽度方向的一侧倾斜。
4.发明人认为相关技术中对构件进行焊接时,往往是通过手动对齐的方式对两个构件进行定位或者通过重物压持进行辅助定位,在焊接过程中,金属受热会使得构件出现一定的形变,从而导致构件位置偏移,所以通过手持或重物压持的方式对构件进行定位,会严重影响焊接后构件之间的位置精度,进而影响焊接质量。
技术实现要素:
5.为了实现提高司机室骨架的焊接精度目的,本技术提供一种轨道车辆司机室骨架焊胎。
6.本技术提供的一种轨道车辆司机室骨架焊胎采用如下的技术方案:
7.一种轨道车辆司机室骨架焊胎,包括用于固定焊接构件的基板和限位块,所述限位块设置在安装座上,所述基板上设置有锁紧组件,所述锁紧组件将焊接构件抵紧在限位块上。
8.通过采用上述技术方案,操作者将焊接钩件放置在基板上,并使得焊接构件与限位块抵接,然后操作者通过锁紧组件将焊接构件压紧限位块上,实现对焊接构件的主骨架和副骨架分别进行固定,从而减少操作者在对焊接钩件进行焊接固定的时候,焊接构件的主骨架和副骨架出现位置倾斜的情况,进而提高司机室骨架的焊接精度。
9.可选的,所述锁紧组件包括支板、第一抵紧块以及锁紧螺栓,所述支板固定连接在基板上,且锁紧螺栓与支板螺纹连接,所述第一抵紧块固定连接在锁紧螺栓朝向焊接构件的一端。
10.通过采用上述技术方案,操作者通过转动锁紧螺栓,使得锁紧螺栓朝向焊接钩件移动的同时带动第一抵紧块移动,当第一抵紧块移动至将焊接钩件的各个位置均压紧在对应的限位块上时,实现焊接钩件的位置固定。
11.可选的,所述基板上设置有限位组件,所述限位组件包括安装架和限位螺栓,所述安装架固定连接在基板上,所述限位螺栓螺纹连接在安装架上,所述限位螺栓朝向焊接构件的一侧固定连接有压块,且压块压紧在焊接构件背离基板的一侧。
12.通过采用上述技术方案,操作者通过转动限位组件带动压块下压,从而使压块将焊接构件压紧在基板上,减少焊接钩件出现上翘的情况以至于影响焊接精度。
13.可选的,所述基板上固定连接有立柱,且立柱上固定连接有螺柱,所述安装架上开设有通孔,且螺柱穿设在通孔内,所述螺柱上螺纹连接有锁紧螺母,且锁紧螺母压紧在安装架上。
14.通过采用上述技术方案,操作者在放置焊接构件的时后需要先拧松锁紧螺栓,解除对安装架的位置固定,然后操作者翻转安装架,以方便操作者放置焊接构件。
15.可选的,所述基板两侧均设置有支座,所述基板在对应支座位置均固定连接有转轴,且转轴转动连接在对应的安装座上,所述支座上设置有用于调节基板角度的调节组件。
16.通过采用上述技术方案,操作者通过调节组件带动基板翻转至一定角度,以方便操作者对焊接构件不同位置进行焊接。
17.可选的,所述调节组件包括限位盘、耳板以及卡接螺栓,所述耳板固定连接在支座上,所述限位盘固定连接在基板上,所述限位盘上开设有若干限位孔,所述卡接螺栓螺纹连接在耳板上并贯穿耳板,所述卡接螺栓穿出耳板的一端插接在其中一个限位孔内。
18.通过采用上述技术方案,操作者翻转基板时,限位盘跟随基板一起进行翻转,当需要对基板角度进行固定时,操作者通过拧紧螺栓,使得螺栓插入限位盘对应的限位孔内,限制限位盘的转动,从而对基板的翻转角度进行固定。
19.可选的,所述锁紧组件包括安装座、套筒、第二抵紧块以及抵紧杆,所述安装座固定连接在基板上,所述套筒沿自身轴线方向滑移贯穿安装座,所述抵紧杆沿套筒轴线方向滑移穿设在套筒内,所述套筒上转动连接有套环,且套环与抵紧杆螺纹连接,所述安装座上固定连接有限位板,所述套环上固定连接有把手,且把手抵接在限位板上,所述抵紧杆朝向焊接构件一端与第二抵紧块固定连接。
20.通过采用上述技术方案,操作者推动手柄连同第二抵紧块和抵紧杆一起朝向焊接构件方向移动,当第二抵紧块与焊接构件抵接,且焊接构件抵接在限位块上时,操作者翻转手柄,使得手柄卡接在限位板上,由于套环与抵紧杆螺纹连接,所以操作者转动手柄带动套环转动,从而带动抵紧杆连同第二抵紧块朝向焊接构件方向移动,使得第二抵紧块将焊接钩件抵紧在限位块上,实现固定焊接构件的目的。
21.可选的,所述安装座上固定连接有支杆,且支杆上开设有限位槽,所述限位板上开设有调节孔,所述支杆穿设在调节孔内,且调节孔在孔壁对应限位槽位置固定连接有卡块,所述支杆在限位板的两侧均螺纹连接有限位螺母。
22.通过采用上述技术方案,操作者通过拧松其中一个限位螺母,使得限位板靠近或远离安装座,然后操作者拧紧另外一个限位螺母实现对限位板的位置固定,通过调节限位板的位置,以适应不同规格的焊接构件,从而提高该结构的灵活性。
23.综上所述,本技术包括以下至少一种有益技术效果:
24.1.通过锁紧组件对焊接构件进行水平方向的位置固定,通过限位组件对焊接构件进行竖直方向的位置固定;从而对焊接构件主骨架和两个副骨架的位置限定,减少焊接过程中焊接构件各个骨架出现位移的情况,有利于提高对焊接构件的焊接精度。
25.2.操作者拧松卡接螺栓解除对限位盘以及基板的位置固定,操作者可将基板调节至合适的角度,然后再拧紧卡接螺栓实现对基板的位置固定,方便操作者对焊接构件不同
位置进行焊接,有利于提高操作者在焊接过程中的便捷性。
附图说明
26.图1是本技术实施例1用于体现焊接构件的结构示意图。
27.图2是本技术实施例1的整体结构示意图。
28.图3是图2中a部分的放大示意图。
29.图4是图2中b部分的放大示意图。
30.图5是图2中c部分的放大示意图。
31.图6是本技术实施例2用于体现锁紧组件的爆炸图。
32.图7是本技术实施例2用于体现导向块和导向槽的剖视图。
33.附图标记说明:1、基板;11、限位块;12、第一抵紧块;13、支座;14、转轴;15、底板;16、加强筋;2、调节组件;21、限位盘;22、耳板;23、卡接螺栓;24、限位孔;3、锁紧组件;31、支板;32、锁紧螺栓;33、第一手柄;4、限位组件;41、安装架;42、限位螺栓;421第二手柄;43、压块;431、垫板;44、立柱;441、螺柱;442、通孔;443、锁紧螺母;5、安装座;51、贯穿孔;511、滑槽;52、套筒;521、凸棱;522、导向块;53、抵紧杆;531、导向槽;54、套环;541把手;55、第二抵紧块;6、限位板;61、调节孔;611、卡块;62、支杆;621、限位槽;63、限位螺母;7、焊接构件;71主骨架;72、副骨架。
具体实施方式
34.以下结合附图2-7对本技术作进一步详细说明。
35.实施例1
36.本技术实施例公开一种轨道车辆司机室骨架焊胎。如图2,轨道车辆司机室骨架焊胎包括长方形的基板1,基板1沿自身长度方向的两端均设置有支座13,两个支座13下端均水平固定连接有底板15,支座13与底板15之间固定连接有若干加强筋16。基板1在对应支座13位置均固定连接有转轴14,两个转轴14同轴设置,且两个转轴14均转动连接在对应的支座13上,其中一个支座13上设置用于限制基板1转动角度的调节组件2,焊接构件7放置在基板1上,且基板1上表面对应焊接构件7位置设置有六个限位块11,六个限位块11位于焊接构件7的同一侧,且主骨架71与两个副骨架72均对应两个限位块11。基板1上表面设置有若干用于将焊接构件7抵紧在各个限位块11上的锁紧组件53,且锁紧组件53与限位块11一一对应;基板1上表面还设置有若干用于将焊接构件7压紧在基板1上的限位组件4,且主骨架71与两个副骨架72上均对应一个限位组件4。
37.如图2和图3,调节组件2包括固定连接在支座13沿基板1宽度方向一侧的耳板22,且耳板22位于支座13上端,基板1在朝向耳板22一端焊接有限位盘21,且限位盘21与转轴14共轴线,限位盘21沿转轴14的轴线方向开设有若干贯穿限位盘21的限位孔24,耳板22上螺纹连接有卡接螺栓23,且卡接螺栓23穿出耳板22的一端穿设在对应的限位孔24内。
38.操作者先拧松卡接螺栓23,使得卡接螺栓23完全脱离其所在的限位孔24,解除对限位盘21的位置限定,然后操作者转动基板1并带动限位盘21转动,当基板1转动至一定角度后,操作者拧紧卡接螺栓23,使得卡接螺栓23卡接对应位置限位孔24,从而限制限位盘21以及基板1的位置,实现基板1的角度调节。
39.如图2和图4,锁紧组件53包括竖直固定连接在基板1上的支板31,支板31上螺纹连接有水平设置的锁紧螺栓32,锁紧螺栓32朝向焊接构件7的一端固定连接有圆柱形的第一抵紧块12,锁紧螺栓32在远离焊接构件7的一端固定连接有第一手柄33。操作者先将焊接构件7放置在基板1上,并使焊接构件7与各个限位块11抵接,然后操作者转动各个锁紧螺栓32,使得各个第一抵紧块12朝向焊接构件7方向移动,并将焊接构件7抵紧在各个限位块11上,从而实现对焊接构件7的固定。
40.如图2和图5,限位组件4包括竖直固定连接在基板1上表面的圆柱形立柱44,且立柱44上端同轴固定连接有螺柱441,螺柱441的最大直径小于立柱44的直径,螺柱441水平设置有长条形的安装架41,且安装架41沿自身长度方向的一端开设有通孔442,螺柱441穿设在通孔442内,通孔442的直径小于立柱44的直径,螺柱441上螺纹连接有锁紧螺母443,且锁紧螺母443将安装架41压紧在立柱44的上端面上。安装架41在远离立柱44的一侧螺纹连接有限位螺栓42,且限位螺栓42竖直设置,限位螺栓42的上端固定连接有第二手柄421,限位螺栓42下端螺纹连接有压块43,压块43下端设置有垫板431,以减少压块43对焊接构件7的压力过大时导致焊接构件7损坏。
41.操作者在基板1上放置焊接构件7之前,先拧松锁紧螺栓32解除对安装架41的限位效果,然后操作者转动安装架41,以方便操作者放置焊接构件7,安装完焊接构件7后操作者翻转安装架41,使得限位螺栓42位于焊接构件7的正上方,操作者在焊接构件7上表面对应限位螺栓42位置放置垫板431,然后操作者通过转动第二手柄421带动限位螺栓42连同压块43下移,从而压紧垫板431,并使得焊接构件7在压块43的压力作用下抵紧在基板1上。
42.本技术实施例实施原理为:操作者先拧松锁紧螺母443,解除对安装架41的限制作用,并拨转安装架41的位置,以方便放置焊接构件7,然后操作者移动焊接构件7的主骨架71和两个副骨架72,使得主骨架71和两个副骨架72均抵接在对应的限位块11上,然后操作者通过转动各个第一手柄33,使得第一抵紧块12压紧在对应的焊接构件7骨架上,实现对焊接构件7各个骨架的初步固定。
43.操作者翻转安装架41,使得各个安装架41均翻转到焊接构件7的上方,然后操作者拧紧锁紧螺母443,以限制安装架41的位置,操作者再通过拧紧各个第二手柄421从而带动各个限位螺栓42向下移动从而带动各个压块43向下移动,操作者在焊接构件7对应各个压块43位置设置垫板431,压块43下压抵紧垫板431,并将焊接构件7的各个骨架均压紧在基板1上,从而完成第一焊接构件7的固定。
44.操作者通过拧松卡接螺栓23,以解除对限位盘21的限位效果,然后操作者翻转基板1至合适的角度,操作者再通过拧紧卡接螺栓23,使得卡接螺栓23穿设再对应的限位孔24内,从而实现对限位盘21以及基板1的位置固定,以方便操作者对焊接构件7的不同位置进行焊接。
45.通过锁紧组件53和限位组件4对焊接构件7的主骨架71和两个副骨架72进行位置限定,减少在焊接过程中,主骨架71与副骨架72之间出现位置偏移而影响加工精度的情况。
46.实施例2
47.如图6和图7,本实施例其余都与实施例1相同,不同的是本实施例中的锁紧组件53包括固定连接在基板1上表面的安装座5,且安装座5上开设有贯穿孔51,且贯穿孔51内穿设有圆柱形套筒52,圆柱形套筒52的外圆周面上固定连接有凸棱521,且凸棱521的长度方向
与套筒52的轴线方向平行,贯穿孔51的槽壁上开有滑槽52,且凸棱521滑移连接在滑槽52内。套筒52内穿设有抵紧杆53,抵紧杆53在朝向焊接构件7一端固定连接有第二抵紧块55,抵紧杆53外圆周面上沿抵紧杆53的轴线方向开设有导向槽531,套筒52内圆周面上固定连接有导向块522,且导向块522滑移连接在导向槽531,抵紧杆53外圆周面设置有螺纹,套筒52在背离焊接构件7的一端同轴转动连接有套环54,且套环54与抵紧杆53螺纹连接。套环54在外圆周面上固定连接有圆柱形的把手541。安装座5在背离焊接构件7的一侧固定连接有支杆62,支杆62沿自身长度方向开设有限位槽621;安装座5在对应支杆62位置设置有限位板6,且限位板6上开设有调节孔61,支杆62穿设在调节孔61内。调节孔61的孔壁上对应限位槽621位置固定连接有卡块611,且卡块611滑移连接在限位槽621内,支杆62在外圆周面上设置有螺纹,且支杆62在限位板6两侧均螺纹连接有限位螺母63。
48.操作者安装完焊接构件7后,操作者推动把手541带动套筒52朝向焊接构件7方向移动直至第二抵紧块55抵接在焊接构件7上,然后操作者翻转把手541并带动套环54转动,从而带动抵紧杆53朝向焊接构件7方向移动,使得第二抵紧块55抵紧在焊接构件7上,该过程中套筒52在焊接构件7的反作用力下会朝背离焊接构件7方向移动,使得把手541抵接在限位板6朝向安装座5的一侧,实现对焊接构件7的固定效果。操作者可根据焊接构件7的大小调节其中一个限位螺母63的位置,然后移动限位板6使其远离或靠近安装座5,再调节另外一个限位螺母63将限位板6固定到合适的位置,已满足实际操作过程中不同的加工需求。
49.以上均为本技术的较佳实施例,并非依此限制本技术的保护范围,故:凡依本技术的结构、形状、原理所做的等效变化,均应涵盖于本技术的保护范围之内。