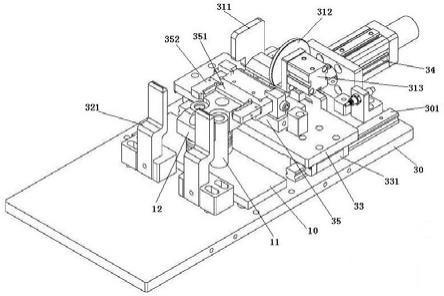
1.本实用新型涉及卡箍,尤其涉及卡箍箍带的铆接技术。
背景技术:
2.传统的卡箍主要由箍带、t型套管、t型螺栓、螺母组成,其中,箍带的两端分别设有一卷头,卷头与箍带之间采用点焊焊接连接。点焊过程中会产生噪音和火花,同时还伴有刺激性的烟气,此外还会在连接区域产生热压力,并对产品的表面美观度带来不利影响,为克服传统点焊工艺带来的不足,申请人提出通过无铆钉铆压的方式将箍带的卷头与箍带带身铆接连接。
技术实现要素:
3.本实用新型所要解决的技术问题在于提供一种用于无铆钉铆接箍带的定位装置及其无铆钉铆接系统,其能高效实现箍带的卷头与箍带带身的无铆钉铆压连接。
4.本实用新型实施例提供了一种用于无铆钉铆接箍带的定位装置,箍带的两端分别设有一卷头,其特点在于,定位装置包括底座、第一端部定位组件、第二端部定位组件、平移台、平移台驱动机构以及限位组件;第一端部定位组件和第二端部定位组件分别设置于底座,第一端部定位组件用于对箍带的一端两侧进行夹持定位,第二端部定位组件用于限制箍带的另一端左右横向移动;平移台位于第一端部定位组件与第二端部定位组件之间,并可纵向滑移地设置于底座上,平移台驱动机构用于驱动平移台纵向移动;限位组件设置于平移台,限位组件用于定位箍带的另一端的卷头的两个角;限位组件与第二端部定位组件之间的空间可容置对箍带进行无铆钉铆接的凹模组件。
5.本实用新型实施例还提供了一种箍带的无铆钉铆接系统,包括凹模组件、与凹模组件相配合的凸模组件、用于驱动凸模组件向下移动的压力设备以及上述的定位装置;凹模组件设置在定位装置的底座上,并位于限位组件与第二端部定位组件之间。
6.本实用新型至少具有以下优点和特点:
7.1、采用本实施例的定位装置及其无铆钉铆接系统,能够将卡箍的箍带的卷头通过无铆钉铆压的方式与箍带带身铆接连接,整个过程无污染,无噪音,并能保证良好的连接强度;
8.2、本实施例的定位装置及其无铆钉铆接系统自动化程度高,制造成本低。
附图说明
9.图1和图2分别示出了采用本实施例的无铆钉铆接系统铆接的卡箍的主视示意图和侧视示意图。
10.图3示出了根据本实用新型一实施例的箍带的无铆钉铆接系统的整体结构示意图。
11.图4至图7分别示出了根据本实用新型一实施例的用于无铆钉铆接箍带的定位装
置的立体示意图、俯视示意图、侧视示意图以及使用状态示意图。
具体实施方式
12.下面结合附图和具体实施例对本实用新型进行详细说明。
13.图1和图2分别示出了采用本实施例的无铆钉铆接系统铆接的卡箍的主视示意图和侧视示意图。如图1和图2所示,卡箍9包括箍带9a,箍带9a的两端分别设有一卷头91,每一卷头91与箍带带身通过4个凸起的铆压点93铆压连接在一起。
14.图3示出了根据本实用新型一实施例的箍带的无铆钉铆接系统的整体结构示意图。根据本实用新型一实施例的箍带的无铆钉铆接系统包括凹模组件1、与凹模组件1相配合的凸模组件2、定位装置3、以及用于驱动凸模组件2向下移动的压力设备4。
15.凹模组件1包括凹模座10、一对凹模11、下脱料块12以及下脱料弹簧13。凹模座10设置在定位装置3的底座30上,一对凹模11的底部与凹模座10相连,下脱料弹簧13的上端和下端分别抵接下脱料块12和凹模座10,下脱料块12的顶面高于一对凹模11的顶面。
16.凸模组件2包括凸模座20、一对凸模21、上脱料块22以及上脱料弹簧23。凸模座20与压力设备4相连,一对凸模21的底部与凸模座20相连,上脱料弹簧23的上端和下端分别抵接上脱料块22和凸模座20,上脱料块22的顶面位于一对凸模21的顶面的下方。
17.上脱料块22和下脱料块12分别用于将铆接时嵌入箍带中的凸模和凹模脱离开来,并且不会损伤箍带表面的涂层。上脱料块22和下脱料块12均由聚氨酯材质制成,上脱料块22的顶面和下脱料块12的顶面的弧度与待铆接的箍带的弧度一致。
18.在本实施例中,压力设备4采用气液增压缸。
19.请参阅图4至图7。定位装置包括底座30、第一端部定位组件、第二端部定位组件、平移台33、平移台驱动机构34以及限位组件35。
20.第一端部定位组件和第二端部定位组件分别设置于底座30,第一端部定位组件用于对箍带9a的一端两侧进行夹持定位,第二端部定位组件用于限制箍带9a的另一端左右横向移动。
21.第一端部定位组件包括静夹持件311、动夹持件312以及动夹持件驱动机构313,静夹持件311与动夹持件312彼此间隔相对设置,动夹持件驱动机构313用于驱动动夹持件312朝靠近或远离静夹持件311的方向移动。第二端部定位组件包括一对限位柱321,一对限位柱321彼此间隔相对设置,一对限位柱321的下端与底座30连接。
22.在本实施例中,动夹持件驱动机构313由第一气缸构成,第一气缸313由一脚踏开关控制。
23.平移台33位于第一端部定位组件与第二端部定位组件之间,并可纵向滑移地设置于底座30上。平移台驱动机构34用于驱动平移台33纵向移动。
24.在本实施例中,平移台驱动机构34由第二气缸构成,第二气缸34由一按钮开关控制。在底座30上设有沿纵向延伸的导轨301,平移台33设有与导轨301滑动配合的滑块331。
25.限位组件35设置于平移台33,可以跟随平移台33一起移动。限位组件35用于定位箍带9a的另一端的卷头91的两个角。前述的凹模组件位于限位组件35与第二端部定位组件之间。限位组件35包括限位台351和一对限位块352,限位台351设置于平移台33,一对限位块352与限位台351相连,且彼此间隔相对设置,各限位块352靠近第二端部定位组件的一端
设有l形定位缺口353。
26.在本实施例中,限位台351由绝缘材料制成,一对限位块352由导电材料制成,且一对限位块352通过导电线5彼此相连。第一端部定位组件只有在检测到一对限位块352之间有电流流过时才能对箍带9a的一端两侧进行夹持定位。
27.进一步地,限位组件包括基座354、复位弹簧355和缓冲弹簧356。基座354设置在平移台33上。限位台351枢接于基座354,在受到向下的压力时会由初始的水平位置向下旋转。复位弹簧355安装在限位台351与第一端部定位组件之间,用于在压力撤销后将限位台351复位至水平位置。缓冲弹簧356设置在基座354的底面与平移台33的顶面之间。缓冲弹簧356可防止限位块352受压过大而被压坏。
28.根据本实用新型实施例的箍带的无铆钉铆接系统的工作过程大致如下。
29.在对箍带9a进行铆接时,人工将箍带9a放在凹模组件1以及限位组件35上。箍带9a的另一端的卷头91的两个角分别抵住一对限位块352的l形定位缺口353的拐角部位。此时,一对限位块352由断路状态转变为导通状态,说明产品放置到位。接下来,人工踩下控制第一气缸313的脚踏开关,第一气缸313推动动夹持件312朝靠近静夹持件311的方向移动,对箍带9a的一端两侧夹持定位,防止箍带9a在铆压过程中移动。若一对限位块352未导通,即便踩下脚踏开关,第一气缸313和压力设备4也不会启动,此时需要重新定位箍带9a。随后,控制压力设备4运行下压,设置在压力设备4上的一对凸模21和上脱料块22随着压力设备下压将一对凸模21压进箍带9a,在一对凹模11的配合下,铆接形成两个具有一定抗拉和抗剪强度的内部镶嵌连接点。当两个点铆接完毕,第一气缸313复位,在压力设备4复位的同时,上脱料块22和下脱料块12分别将凸模21和凹模11自动脱出。其中,在铆压的过程中,上脱料块22先于凸模21压住箍带9a,随着压力设备4下降,凸模21铆压进入箍带9a直至凸模21、箍带9a和凹模11扣合形成内部镶嵌连接点。铆压完毕压力设备4上升,上脱料块22受到上脱料弹簧23的弹簧力作用后于凸模21脱离箍带9a。下脱料块12在铆压完毕后的回升过程中将箍带9a顶出凹模11的模腔。
30.之后,人工按下第二气缸34按钮开关,启动第二气缸34,第二气缸34将平移台33移动预定的铆接点距离,人工将箍带9a的另一端的卷头91的两个角分别抵住一对限位块352的l形定位缺口353的拐角部位,重复上述步骤直至第一气缸313和压力设备4复位。当铆接完第2排铆压点93后,第二气缸34自动复位,回到初始位置。然后人工将箍带9a取出,调换箍带9a的一端继续铆接。本实施例的无铆钉铆接系统每次铆接两个点,一条箍带9a总共需要铆接4次。
31.本实施例的无铆钉铆接系统能够将卡箍的箍带的卷头通过无铆钉铆压的方式与箍带带身铆接连接,整个过程无污染,无噪音,并能保证良好的连接强度,具有自动化程度高、制造成本低等优点。
32.显然,本领域的技术人员可以对本实用新型进行各种改动和变型而不脱离本实用新型的精神和范围。这样,倘若本实用新型的这些修改和变型属于本实用新型权利要求及其等同技术的范围之内,则本实用新型也意图包含这些改动和变型在内。