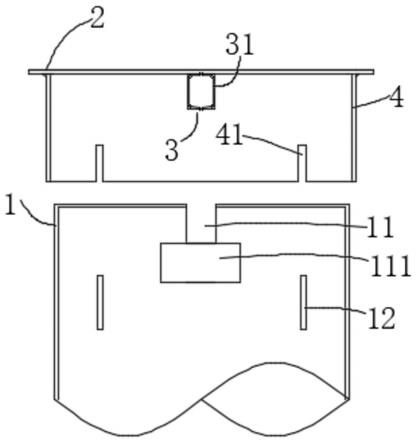
装配式的钢管桩顶部承重结构
【技术领域】
1.本发明涉及桥梁工程的技术领域,尤其涉及一种装配式的钢管桩顶部承重结构。
背景技术:
2.进入21世纪后,我国桥梁建设发展突飞猛进,大量跨山区峡谷、跨江河湖海的桥梁正在建设或规划中。由于桥梁施工时材料、设备运输和人员通行的需要,在桥梁施工期间需修建临时栈桥,在跨海桥梁的建设中,栈桥的长度往往达到了数公里甚至十几公里,应用非常广泛。
3.目前行业中对临时栈桥的装配化已有相关研究,但仍存在很大的提升空间。现有的钢管桩施工过程中,盖板均为焊接牛腿,其中盖板也可称为桩帽,均是为了增大钢管桩顶部的受力面积,提升钢管桩顶部的承重能力。当钢管桩振沉到位后,在对应标高后,现场焊接牛腿,牛腿焊接过程中多为竖向焊缝,焊接难度大,焊接时间长,不利于快速化施工,安全控制较难把握。
技术实现要素:
4.针对现有技术存在的不足,本技术的目的在于提供装配式的钢管桩顶部承重结构,具有提升施工工效,使得施工更为安全可控。
5.为实现上述目的,本发明提供了如下技术方案:
6.一种装配式的钢管桩顶部承重结构,包括钢管桩和盖板,包括有设于所述盖板底面的对扣件、与所述盖板连接的套管、开设于所述套管底端的限位槽、固定于所述钢管桩侧壁的限位板和开设于所述钢管桩顶部的槽口;所述套管的直径大于或小于所述钢管桩的直径;所述对扣件与所述槽口之间对应匹配,所述限位槽与所述限位板之间对应匹配,使得所述盖板与所述钢管桩顶部实现装配形成钢管桩顶部承重结构。
7.本发明进一步设置为:当所述套管的直径大于所述钢管桩的直径时,所述限位板焊接于所述钢管桩的外侧壁。
8.本发明进一步设置为:所述限位板和所述钢管桩之间的焊缝厚度等于或大于7mm。
9.本发明进一步设置为:若干所述限位板在所述钢管桩之中呈中心对称设置。
10.本发明进一步设置为:所述限位板的长边方向与所述钢管桩的轴向方向相一致设置,所述限位板的短边方向与所述钢管桩的径向方向相一致设置。
11.本发明进一步设置为:所述限位槽的槽深与所述限位板的长边长度相一致设置,所述限位槽的槽宽大于所述限位板的厚度。
12.本发明进一步设置为:所述钢管桩的内侧壁安装有防止所述槽口变形的加劲板。
13.本发明进一步设置为:所述对扣件包括有两组相互扣合的槽钢,两组所述槽钢的槽口之间相对设置。
14.本发明进一步设置为:所述槽钢的槽口朝向为水平方向设置。
15.本发明进一步设置为:所述对扣件横跨所述盖板布置,所述对扣件的中点与所述
盖板的中点对齐设置。
16.与现有技术相比,本发明具备如下优点:
17.1.由于桩帽结构简单,对桩帽的安装拆除过程中避免了焊接及切割工作量,无需采用螺栓进行连接,安装方便高效;
18.2.通过预制装配化的钢管桩顶部承重结构,在施工现场只需利用起吊设备进行装配化的钢管桩顶部承重结构装卸即可,一次性吊装完成,装卸过程简单方便,避免了水上或高空进行焊接工作,安全可控;
19.3.通过套管可套设于钢管桩之中,使得盖板的安装更易与钢管桩相对应,使得桩帽的安装更为简单可行;同时,限制了桩帽的周向运动,提升了桩帽安装的牢靠程度;
20.4.在施工过程中方便快捷,可大大缩短水面或高空作业时间,降低了长时间水上作业或高空作业的施工风险,安全可靠;
21.5.通过采用槽钢扣合为对扣件,既增大了对扣件与钢管桩之间的接触面积,使得桩帽安装更为牢固可靠;同时,对扣件设为中空结构,降低了桩帽的重量,以及节省了装配化桩帽的制造成本。
【附图说明】
22.图1为本实施例的装配式桩帽的结构示意图;
23.图2为本实施例的装配式桩帽的安装示意图;
24.图3为图2的a-a的剖视图;
25.图4为图2的b-b的剖视图。
26.附图标记:1、钢管桩;11、槽口;111、加劲板;12、限位板;2、盖板;3、对扣件;31、槽钢;4、套管;41、限位槽。
【具体实施方式】
27.下面结合附图和示例性实施例对本发明作进一步地描述,其中附图中相同的标号全部指的是相同的部件。此外,如果已知技术的详细描述对于示出本发明的特征是不必要的,则将其省略。
28.如图1和图2所示,本发明公开的一种装配式的钢管桩顶部承重结构,包括钢管桩1和盖板2,还包括有设于盖板2底面的对扣件3、与盖板2连接的套管4、开设于套管4底端的限位槽41、固定于钢管桩1侧壁的限位板12和开设于钢管桩1顶部的槽口11;套管4的直径大于或小于钢管桩1的直径;对扣件3与槽口11之间对应匹配,限位槽41与限位板12之间对应匹配,使得盖板2与钢管桩1顶部实现装配形成钢管桩顶部承重结构。通过预制装配化的钢管桩顶部承重结构,在施工现场只需利用起吊设备进行装配化桩帽的装卸即可,一次性吊装完成,装卸过程简单方便,避免了水上或高空进行焊接工作,安全可控。
29.在本实施例中,当套管4的直径大于钢管桩1的直径时,限位板12焊接于钢管桩1的外侧壁,限位板12和钢管桩1之间的焊缝厚度等于或大于7mm,若干限位板12在钢管桩1之中呈中心对称设置。限位板12的长边方向与钢管桩1的轴向方向相一致设置,限位板12的短边方向与钢管桩1的径向方向相一致设置。
30.套管4的顶端焊接于盖板2的内侧面之中,套管4和盖板2之间的焊缝厚度等于或大
于7mm,其中盖板2的厚度选为16mm,其焊缝长度为接触长度的50%。使得套管4与盖板2之间实现无缝连接,套管4可套设于钢管桩1之中,使得盖板2的安装更易与钢管桩1相对应,使得盖板2的安装更为简单可行;同时,提升了桩帽安装的牢靠程度。
31.限位槽41的槽深与限位板12的长边长度相一致设置,限位槽41的槽宽大于限位板12的厚度,使得限位板12可插入至限位槽41的槽顶,限位板12对桩帽起到了轴向的支撑作用,由于桩帽自身重力作用下,使得限位槽41和限位板12之间的配合更为紧密。
32.钢管桩1的内侧壁安装有防止槽口11变形的加劲板111,加劲板111焊接于槽口11的槽底和槽底下方,起到了增强槽口11的抗剪能力,提升桩帽安装的稳定性。
33.如图3和图4所示,对扣件3包括有两组相互扣合的槽钢31,两组槽钢31的槽口11之间相对设置,槽钢31的槽口11朝向为水平方向设置。对扣件3焊接于盖板2的内侧面上,对扣件3和盖板2之间的焊缝厚度等于或大于5mm,其焊接长度为接触长度的50%,且对扣件3横跨盖板2布置,对扣件3的中点与盖板2的中点对齐设置。
34.在另一实施例中,当套管4的直径小于钢管桩1的直径时,套管4的直径小于盖板2的直径,盖板2的直径大于钢管桩1的直径;其中,限位板12焊接于钢管桩1的内侧壁之中,在桩帽的安装过程中,套管4插入至钢管桩1之中,限位槽41与限位板12之间一一对应配合,对桩帽的周向运行进行限位,提升了桩帽安装的稳定性。
35.对扣件3横跨盖板2布置,对扣件3的两端分别从套管4侧壁中延出,使得对扣件3可与槽口11之间一一对应,保障了桩帽安装的稳定性。
36.在另一实施例中,限位板12可设为多块,其形状为条状设置,多块限位板12在盖板2的中心交叉固定,使得多块限位板12连接为一个整体,提升限位板12的抗剪能力,使得桩帽在钢管桩1的安装更为稳定;同时,多块限位板12在盖板2上呈环形排布并向远离盖板2中心延伸,限位板12的两侧面分别焊接有角钢,角钢的轴向方向与限位板12的轴向方向相一致设置,角钢的长度小于或等于限位板12的长度,起到了防止限位板12变形的作用,增强了限位板12的抗剪能力。
37.本实施例的工况及原理如下:
38.在预定地点将钢管桩1振沉就位后,按设计标高修平钢管桩1的顶端,并在钢管桩1的外边顶端均匀开设四组槽口11,四组槽口11之间关于钢管桩1中心对称设置,然后在钢管桩1的内侧壁焊接上四组加劲板111,四组加劲板111分别与四组槽口11之间一一对应,起到了增强槽口11的抗剪能力,防止槽口11在桩帽安装过程之中发生变形。再在钢管桩1的外侧壁分别焊接上四组形状为块状设置的限位板12,四组限位板12在钢管桩1之中呈中心对称布置。
39.提前预制厚度为16mm的盖板2,将两组槽钢31扣合形成对扣件3,再将对扣件3焊接于盖板2的内侧面上,对扣件3和盖板2之间的焊缝厚度大于5mm,其焊接长度为接触长度的50%,使得对扣件3横跨盖板2布置。将盖板2放置于套管4的上端面,对盖板2和套管4之间的连接处进行焊接固定,盖板2和套管4之间的焊缝厚度大于7mm,其焊缝长度为接触长度的50%,使得盖板2和套管4之间连接为一体,然后在套管4的外边底端开设四组用于与限位板12相对应的限位槽41,预制完成桩帽。
40.吊装上述装配式桩帽,使得对扣件3卡进槽口11之中,同时限位板12卡进限位槽41之中,完成桩帽安装,在施工现场只需利用起吊设备进行装配化桩帽的装卸即可,一次性吊
装完成,装卸过程简单方便,避免了水上或高空进行焊接工作,安全可控。
41.发明的一些示例性实施例,但是本领域的技术人员将理解,在不脱离本发明的原理或精神的情况下,可以对这些示例性实施例做出改变,本发明的范围由权利要求及其等同物限定。