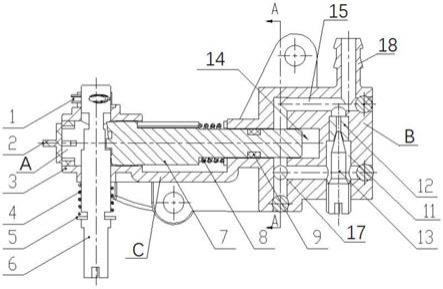
1.本实用新型涉及机油阀领域,具体是一种流量双调节机油阀。
背景技术:
2.油锯是以汽油机为动力、锯链为切削工具的手持式木材切削机械,主要用于伐木、打枝、造材等作业。其工作原理是依靠锯链上交错的l型刀片的横向运动来进行剪切。在森林工业发达国家中,尽管较为广泛采用了包含联合机在内的高效、先进的采运工艺和装备,但林业上专门用于伐木、打枝和造材作业的油锯仍占有重要地位。而对采运全盘机械化水平还比较低的发展中国家(包括中国在内)来说,油锯更是机械化采伐中的主要工具。
3.根据油锯工作原理,链条在导板上横向运动,带动链条的l型刀片横向运动。链条上有齿插入导板槽内,并在导板槽内滑动。由于链条运转速度较高,因而需要机油润滑。如用干燥的链条工作,没有机油润滑的导板链条会因摩擦产生大量的热,会导致导板变软,链条l型刀片退火而造成导板链条报废。因此在使用过程中链条上总有少许的油溅出才是正常的,而链条无润滑油是不能正常工作的。
4.在每次使用链锯之前,都需要检查链条的润滑和加满润滑油箱的机油。因为链锯润滑油会完全的排放到空气中,而普通润滑油是石油基的,不可降解,会污染环境。所以建议尽量使用可降解的环保链锯油,不少发达国家对此都有硬性的法规以避免环境污染。但环保链锯油往往价格较高,因而在使用油锯时应尽量减少锯链润滑油的消耗。即使不是环保链锯油,油锯的链锯油消耗量依然非常大,使用成本也较高。究其原因,伐木的情况是比较复杂的,有些树木需要较多机油供应,有些却只需要少量机油润滑即可。
5.比如切割松树之类的树木。由于其本身含有大量松脂,并且松脂是比较粘的。切割过程中,这些松脂会随着链条的转动带到导板上。如果机油量不够,不能将导板链条与松脂之间保持一层油膜,则松脂会直接附着在链条及导板滑槽上。此时,链条转动起来就异常困难。而如果将机油阀调到最大,供油充足,链条上就会有大量机油。切割时松脂就不能附着在链条上。但当切割杉木之类较软的树木时,由于切割阻力小,并且杉木含有水分,此时只要供极少量机油就行了。当切割干的杂木时,由于树木含水极低。切割时大量的机油会被树木带走,并且干的杂木较硬,负荷较大,产生的摩擦热较多,并且切割速度降低,发动机长时间高负荷工作,此时链条会产生较多的摩擦热,这种情况就需要供给大量机油,保证链条有足够多的机油来润滑,并且带走链条的热量。因此,实际操作中,油锯的使用情况还是比较复杂的,需要根据实际情况来对机油阀进行调节。
6.实际使用中,往往会出现这种情况:当切割较小的树时,或者切割较软的木材时,想将机油阀调小。结果发现,即使调至最小,出来的机油还是很大。这是因为,一般情况下,油锯机油阀出油量是按最恶劣的情况来设计的,是为了保证油锯在最恶劣的条件下也能正常使用。并且现在的机油阀调到最大时的出油量与调到最小时的出油量差别不大。一般情况,油锯机油箱的容积是这样确定的。当油锯燃油箱装满燃油,机油箱装满润滑机油;发动机燃油用尽时,机油箱还有少许机油。以免发生机油比燃油先用尽,导致烧坏导板链条。因
而平时使用机油往往是偏多的,会造成使用成本升高,并且对环境造成污染。在环境保护力度不断加大的今天,这种情况是应该尽量避免的。
技术实现要素:
7.本实用新型的目的是提供一种流量双调节机油阀,以解决现有技术油锯中机油阀难以改变输出机油量的问题。
8.为了达到上述目的,本实用新型所采用的技术方案为:
9.一种流量双调节机油阀,包括壳体3,所述壳体3包括调节仓、油仓和连接调节仓、油仓的内螺纹孔道;所述壳体3的油仓中设有油路孔道15以及连通于油路孔道15一侧的工作腔14,壳体3的内螺纹孔道内同轴转动安装有蜗杆7,所述蜗杆7外表面部分露出内螺纹孔道,蜗杆7的外径大于油路孔道15的孔径,蜗杆7一端穿过所述油路孔道15并堵入至工作腔14中,由蜗杆7将所述油路孔道15隔分为两段,且蜗杆7没入至工作腔14内的一端被切割出有配油缺口16,所述油路孔道15被隔分的一段连通有进油口17作为进油段,油路孔道15被隔分的另一段连通有出油口18作为出油段;
10.所述壳体3的调节仓内转动安装有第一调节轴6,第一调节轴6的轴向垂直于所述蜗杆7,位于调节仓内的第一调节轴6上有一段成型为相对于第一调节轴 6本体偏心的调节凸轮19,所述蜗杆7另一端穿入至调节仓内与第一调节轴6 的调节凸轮19或者调节凸轮19连接的第一调节轴6本体部分相接触,位于内螺纹孔道中的蜗杆7外还同轴环套有蜗杆复位弹簧8,所述蜗杆复位弹簧8轴向一端固定于内螺纹孔道的孔壁,蜗杆复位弹簧8轴向另一端固定于蜗杆7,且蜗杆复位弹簧8初始状态被压缩,由此使所述蜗杆7具有向第一调节轴方向运动的趋势;
11.所述壳体3的油仓内还设有回油通道11,回油通道11两端分别与油路孔道 15中的进油段、出油段连通,回油通道11靠近所述出油段的位置堵塞安装有量具12,量具12中具有连通回油通道11的量孔,回油通道11内还螺入安装有第二调节轴13,第二调节轴13一端同轴堵入至回油通道11的量孔中。
12.进一步的,所述蜗杆7穿入至调节仓内的另一端同轴连接有端面凸轮20,所述端面凸轮20的轮面设为斜面,端面凸轮20中心同轴设有圆孔,圆孔内同轴固定有调节圆柱21,所述蜗杆7另一端的端面凸轮20轮面或者调节圆柱21,与第一调节轴6的调节凸轮19或者调节凸轮19连接的第一调节轴6本体部分相接触。
13.进一步的,所述第一调节轴6可在调节仓内沿自身轴向方向滑动,第一调节轴6一端穿出调节仓形成第一穿出段,第一穿出段外同轴固定有轴用弹性挡圈5,所述轴用弹性挡圈5与调节仓外壁之间连接有套于第一穿出段外的弹簧4;第一调节轴6另一端穿出调节仓形成第二穿出段,第二穿出段中设有径向贯通的档位销孔22,销孔内贯穿有档位定位销1,所述第一调节轴6在弹簧4作用下使档位定位销1压于调节仓对应位置。
14.进一步的,所述调节仓外壁对应第一调节轴6第二穿出段穿出位置设有多个环绕第一调节轴6的指示档位。
15.进一步的,所述第二调节轴13堵入量孔的一端设为锥形头,所述回油通道 11量孔供第二调节轴13堵入的孔口设为匹配的锥形孔。
16.本实用新型中,第一调节轴通过自身调节凸轮部分与蜗杆对应端相接触,由此可
在转动调节第一调节轴时,使蜗杆沿自身轴向往复运动,并且蜗杆与内螺纹孔道是螺纹配合的,因此蜗杆在运动时能够自转。
17.初始时蜗杆的配油缺口完全没入工作腔内,此时蜗杆使油路孔道的进油段和出油段被隔断。当蜗杆向第一调节轴方向运动时,蜗杆没入工作腔的一端逐渐从工作腔脱出,工作腔内容积增大,因此形成真空空间,并且由于蜗杆是自转的,当蜗杆端部的配油缺口逐渐从工作腔脱出并转动至面向油路孔道的进油段时,工作腔可通过配油缺口与进油段连通,并通过真空作用将进油段的机油吸入工作腔中。当蜗杆继续向第一调节轴方向运动时,工作腔容积继续增大,但配油缺口随蜗杆逐渐转动至使工作腔和进油段之间逐渐断开。
18.当蜗杆向第一调节轴方向运动至极限后,会随着第一调节轴的转动向相反方向(即向工作腔方向)运动,此时蜗杆仍然继续自转,通过配油缺口使工作腔与油路孔道的出油段逐渐连通,并且由于蜗杆此时向着工作腔运动,使工作腔容积逐渐被压缩,由此可将工作腔内的机油挤入至出油段,最终通过出油口流出。
19.上述过程反复进行,由此可实现机油的输送。
20.在上述过程进行机油输送时,可通过第一调节轴转动调节,使工作腔容积增大至一定量时,保持第一调节轴不动,然后仅转动蜗杆,此时工作腔的容积变化至固定量,通过蜗杆的转动可实现输送定量的机油。
21.当机油输送量过多时,可旋转第二调节轴,使第二调节轴逐渐脱离量具的量孔,由此使油路孔道中出油段的机油通过量具回流至进油段,以避免排出过多的不必要的机油。
22.因此,与现有技术相比,本实用新型明显能够实现输送定量的机油,并且能够实现机油输送量的调节,并在输送过多机油时能够使机油回流。由此可避免机油消耗大的问题,降低机油对环境的污染。
附图说明
23.图1是本实用新型结构正剖视图。
24.图2是本实用新型结构俯视图。
25.图3是本实用新型右向剖视图。
26.图4是本实用新型蜗杆结构示意图。
27.图5是本实用新型第一调节轴结构示意图。
28.图6是本实用新型蜗杆转动调节原理图。
29.图7是本实用新型第二调节轴转动调节原理图。
具体实施方式
30.下面结合附图和实施例对本实用新型进一步说明。
31.如图1-图3所示,本实用新型一种流量双调节机油阀包括壳体3,该壳体3 包括左侧的调节仓a、右侧的油仓b和水平连接调节仓a、油仓b的内螺纹孔道c。
32.壳体3的油仓b中设有油路孔道15,该油路孔道15呈l型,油路孔道15 的l型竖直段端部向下延伸至壳体3油仓b的下部,油路孔道15的l型水平段位于油仓b的上部。壳体3的油仓b内位于油路孔道15的l型竖直段右侧设有工作腔14,该工作腔14与油路孔道15的l型竖直段右侧连通。
33.壳体3的内螺纹孔道c内同轴转动安装有蜗杆7,壳体3顶部对应内螺纹孔道c位置设有开口使蜗杆7对应位置上表面露出,蜗杆7的外径大于油路孔道 15的孔径,蜗杆7的右端穿过油路孔道15并堵入至工作腔14内左侧位置,由蜗杆7将油路孔道15隔分为两段,其中蜗杆7下方的油路孔道15一段为进油段,蜗杆7下方的油路孔道15一段为出油段,壳体3的背面对应于进油段位置设有与进油段内连通的进油口17,壳体3的顶部对应于出油段位置设有与出油段连通的出油口18。
34.如图4所示,蜗杆7没入至工作腔14内的右端被切割出有配油缺口16,初始时配有缺口16完全没入至工作腔14内。位于内螺纹孔道c露出位置的蜗杆7 外还同轴环套有蜗杆复位弹簧8,蜗杆复位弹簧8轴向右端固定于内螺纹孔道露出位置右端端面,蜗杆复位弹簧8轴向左端固定于蜗杆7。
35.壳体3的油仓b内位于工作腔14右方位置还设有回油通道11,回油通道11 呈l型,回油通道11的l型水平段端部连通于油路孔道15的进油段(图1中油路孔道15的l型竖直段),回油通道11的l型竖直段端部连通于油路孔道15 的出油段(图1中油路孔道15的l型水平段)。回油通道11的l型竖直段内堵塞安装有量具12,量具12中具有轴向竖直的量孔,如图7所示,量孔下端孔口设有锥形孔。壳体3油仓b底部对应回油通道11的l型竖直段还设有轴向竖直的螺纹安装孔,螺纹安装孔内螺入安装有第二调节轴13,第二调节轴13上端设为量具12量孔下端孔口匹配的锥形头,且第二调节轴13的上端同轴堵入至量具 12的量孔下端孔口中。
36.壳体3左侧的调节仓a内右侧面开口并盖合固定有端盖2。调节仓a内转动安装有轴向竖直的第一调节轴6,同时第一调节轴6能够在调节仓a内上下滑动。位于调节仓内的第一调节轴6上有一段成型为相对于第一调节轴6本体偏心的调节凸轮19。第一调节轴6下端从调节仓a底部穿出后形成第一穿出段,第一穿出段外壁设有卡簧槽,卡簧槽内同轴固定有轴用弹性挡圈5,轴用弹性挡圈 5与调节仓底部之间连接有套于第一穿出段外的弹簧4,并且第一调节轴6下端设有调节槽23。第一调节轴6上端从调节仓a顶部穿出后形成第二穿出段,第二穿出段中设有径向贯通的档位销孔22,档位销孔22内贯穿有档位定位销1。第一调节轴6整体在弹簧4作用下下压,使档位定位销1压于调节仓a顶部对应位置形成定位。调节仓顶面对应设有多个环绕第一调节轴6第二穿出段的指示档位24,当转动第一调节轴6时可通过档位定位销1与指示档位24对照实现转动定位。
37.蜗杆7的左端穿入至调节仓a内,蜗杆7穿入至调节仓a内的左端同轴连接有端面凸轮20,端面凸轮20的轮面设为斜面,端面凸轮20中心同轴设有圆孔,圆孔内同轴固定有调节圆柱21。当蜗杆7转动时,蜗杆7左端的端面凸轮 20轮面或者调节圆柱21,与第一调节轴6的调节凸轮19轮缘或者调节凸轮19 上、下端连接的第一调节轴6本体部分圆周面相接触。并且,蜗杆复位弹簧8 初始状态被压缩,由此使蜗杆7具有向第一调节轴6方向运动的趋势。
38.如图1-图3结合图6所示,本实用新型工作过程如下:
39.当处于状态ⅰ时,蜗杆7相较于壳体3处于最右端,此时壳体3工作腔14 内容积最小。并且蜗杆7上配油缺口16并不连通工作腔14与油路孔道15的进油段、出油段,工作腔与进油口17、出油口18之间被切断。
40.随着蜗杆7逆时针旋转,蜗杆7的左端最远点逐渐离开第一调节轴6,在第一调节轴6、蜗杆复位弹簧8的联合作用下,蜗杆7边逆时针旋转,边向左运动,此时壳体3的工作腔14
容积逐渐增大。
41.到达状态ⅲ时,蜗杆7左端的端面凸轮20最近点与第一调节轴6接触,此时壳体3的工作腔14容积达到最大。与此同时,蜗杆7的配油缺口16逐渐旋转到了向下朝向油路孔道15的进油段,由此将壳体3工作腔14与进油口17之间连通度逐渐增大;增大了容积的壳体3工作腔14产生真空,将油路孔道15的进油段内油吸入。这一过程持续到状态ⅱ,到状态ⅲ时结束。
42.当到达状态ⅲ时,蜗杆7刚好旋转了180度。在这一过程中,蜗杆7的配油缺口16将工作腔14与油路孔道15的进油段从一开始的关闭,到逐渐打开、开度最大、逐渐关闭、完全关闭。蜗杆7在这一过程中边旋转边向左移动,边将壳体3工作腔14与油路孔道15的进油段连通;壳体3工作腔14产生的真空吸力将油路孔道15的进油段的机油吸到工作腔14内,完成吸油过程。
43.从状态ⅲ到状态
ⅴ
是排油过程,状态ⅲ中:蜗杆7左端端面凸轮20最近点与第一调节轴6接触,蜗杆7在最左端,此时壳体3工作腔14容积达到最大。蜗杆7旋转,蜗杆7的配油缺口16逐渐将壳体3工作腔14与油路孔道15的进油段连通;与此同时,蜗杆7左端端面凸轮20的最远点逐渐离开第一调节轴6,端面凸轮20最远点渐渐接近第一调节轴6。由于调第一节轴6可以固定,蜗杆7 只能边旋转边向右移动。壳体3内工作腔14内的机油受到压缩,从油路孔道15 的进油段排出到出油口18。这一过程一直持续到状态
ⅴ
为止。
44.到达状态
ⅴ
,蜗杆7达到最右端,工作腔容积14达到最小,同时蜗杆7的配油缺口16将壳体3工作腔14与油路孔道15的进油段关闭,机器进入下一循环。
45.如图5、图6所示,第一调节轴6调节原理:
46.当蜗杆7左端端面凸轮最近点与第一调节轴6接触时,此时蜗杆7达到最左端位置。其上的调节圆柱21也达到最左端位置。此时转动第一调节轴6,其上加工的调节凸轮19会一起旋转。由于调节凸轮19与第一调节轴6的本体部分是不同轴的。当调节凸轮19外表面与第一调节轴6的旋转轴最近点在蜗杆7左端调节圆柱21侧时,蜗杆7的调节圆柱21与调节凸轮19表面不接触,蜗杆7通达到最左端位置,此时吸油量最大。当用小起子转动第一调节轴6时,调节凸轮 19外表面与调节圆柱21接触处到第一调节轴6轴线的距离逐渐增大,旋转的蜗杆7在最近点到达第一调节轴6的圆柱面之前,调节圆柱21与调节凸轮19首先进行接触,蜗杆7的端面凸轮20的最近点就不能与第一调节轴6圆柱面接触。也就是说,当蜗杆7左移到调节圆柱21与调节凸轮19接触时,蜗杆7不再左移,只有空转。直到端面凸轮20与第一调节轴6圆柱面接触后,蜗杆7开始右移,进入排油阶段。当旋转到调节凸轮19外表面与调节圆柱20接触处的直径达到增大值时,蜗杆7左移距离达到最小值,吸入的油达到最小值,从而达到调节机油阀流量的目的。总之,第一调节轴6就是通过调节蜗杆7最左端的位置从而达到改变工作腔排量的目的。
47.为确保第一调节轴6调节好的位置在机器振动的情况下保持不变,其上还安装有防档位定位销1、弹簧4、轴用弹性挡圈5。轴用弹性挡圈5卡在第一调节轴6的卡簧槽内,弹簧4弹力使第一调节轴6始终下压。档位定位销1过盈安装在第一调节轴6档位销孔内。当机油阀调节油量时,需用小一字起将第一调节轴 6往上顶,克服弹簧4的弹力,然后就可左右旋转调整机油阀的流量。当调好后,弹簧4将第一调节轴6往下压,带动档位定位销1压紧在壳体3的档位槽内,从而防止第一调节轴6转动。
48.第二调节轴调节原理如图7所示:
49.第一调节轴6是通过改变机油阀的排量来达到改变出油量的目的,而第二调节轴13则是在第一调节轴6仍无法满足要求的情况下使用的。当调节凸轮外表面与调节圆柱接触处的点到第一调节轴6旋转轴线的距离达到最大值时,蜗杆7 左移距离达到最小值,在这种情况下仍无法满足需要,则需调节第二调节轴13, 改变排油量孔出口的间隙。逆时针旋转,第二调节轴13往外,则间隙变大;顺时针旋转,第二调节轴13往内,间隙变小。当旋紧第二调节轴13时,间隙变为 0,这是油锯大部分情况下的使用状态。当需要机油量较小时,则在第一调节轴 6无法满足条件的情况下将第二调节轴13逆时针拧出;当第二调节轴13逆时针完全拧出时,则机油流量由量具12中心的量孔确定其最小值。由第二调节轴13 调节从出油口18流回的机油流回油路孔道15的进油段,最后被机油阀吸入重新泵出排油口。
50.本实用新型所述的实施例仅仅是对本实用新型的优选实施方式进行的描述,并非对本实用新型构思和范围进行限定,在不脱离本实用新型设计思想的前提下,本领域中工程技术人员对本实用新型的技术方案作出的各种变型和改进,均应落入本实用新型的保护范围,本实用新型请求保护的技术内容,已经全部记载在权利要求书中。