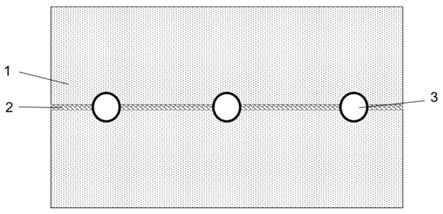
1.本技术涉及隔离剂技术领域,特别是涉及一种非真空叠轧用隔离剂及其制备、使用方法。
背景技术:
2.为了克服宽幅薄板生产难度大、板型难以控制,以及国内外现有能生产薄板的厂家较少等问题,叠轧工艺制薄板已经被国内外广泛熟知,采用叠轧法生产薄板时,其组坯工序决定了最终产品的成功率,而组坯过程都离不开隔离剂。现有叠轧板生产中使用的隔离剂大多需要板坯封焊后抽真空使用,但是抽真空的板坯在轧制时容易出现漏气现象,存在一定的安全隐患;而且现有隔离剂质量参差不齐,隔离效果不好使得钢板粘连无法顺利分板,极大程度上影响了成材率、合格率以及生产效率。
3.现有技术中,专利cn105238216a公开了一种在基板上获得隔离剂层的方法以及含有基板与隔离剂层的复合材料,其选用的粘结成份环氧树脂成本相对较高,且加入了大量的酒精做固化剂,大大增加了生产成本。
4.专利cn108548488a公开了一种复合板用耐高温隔离剂及其制备方法,隔离剂需涂覆厚度1-2mm,该配比隔离效果较差,一定程度上造成了资源的浪费,而且水的比重较大,该隔离剂成份风干所需时间较长,生产效率较低。
5.专利cn112480758a公开了一种真空复合板用隔离剂及其制备、使用方法,该隔离剂涂敷厚度只有0.2-0.3mm,需要复合坯抽真空,存在漏气安全隐患;且该配比的隔离剂中粘结剂聚乙烯醇的比重较低,一定程度上影响了隔离剂的附着能力,隔离剂容易脱落,影响隔离效果。
技术实现要素:
6.本发明的目的在于提供一种非真空叠轧用隔离剂及其制备、使用方法,以克服现有技术中的不足。
7.为实现上述目的之一,本发明提供如下技术方案:一种非真空叠轧用隔离剂,所述隔离剂按照质量百分比计,包括:4%≤隔离粉≤30%,1.0%≤粘结粉≤2.5%,其余为水;所述隔离粉由氧化镁、氧化铝、氧化硅粉中的任意两种或三种组成,所述粘结粉由聚乙烯醇和热固性酚醛树脂组成。
8.在该技术方案中,
9.优选的,所述隔离粉粒径<200μm,所述隔离粉纯度>95%;所述粘结粉粒径<150μm,所述粘结粉纯度>97%;所述水为工业用水。
10.在该技术方案中,选用粒径较大的粉末会增加搅拌时间,且容易存在杂质,影响隔离剂效果;水为工业用水,不可有污物或较多杂。
11.优选的,当所述隔离粉由氧化镁以及氧化铝或氧化硅组成时,按照质量百分比计,所述氧化镁含量为40%-70%;当所述隔离粉由氧化铝以及氧化硅组成时,按照质量百分比
计,所述氧化铝含量为40%-70%;当所述隔离粉有氧化镁、氧化铝和氧化硅组成时,按照质量百分比计,所述氧化镁含量为35%-45%,所述氧化铝含量为35%-45%,所述氧化硅含量为10%-30%。
12.优选的,所述聚乙烯醇占粘结粉质量百分比的60%-80%。
13.为实现上述目的之一,本发明提供如下技术方案:一种非真空叠轧用隔离剂的制备方法,所述制备方法包括:将隔离粉、粘结粉以及水按照配比,搅拌3-10min,随后静置30-60min,直至成粘稠状,且无颗粒感及气泡,得到所述隔离剂。
14.在该技术方案中,所述搅拌时间为3-10min,隔离粉、粘结粉和水三者可以充分混合成粘稠状;所述静置时间为30-60min,隔离剂内的气泡可以充分消除干净。
15.为实现上述目的之一,本发明提供如下技术方案:一种非真空叠轧用隔离剂的使用方法,包括以下步骤:
16.步骤(1):将板坯表面打磨光洁;
17.步骤(2):将所述步骤1中的板坯根据变形量在板坯表面涂覆隔离剂,随后进行烘干,烘干温度为100—200℃,烘干时间为30-60min,烘干后所述板坯表面形成隔离层;
18.步骤(3):将至少两块表面覆有隔离层的板坯叠加使得隔离层位于相邻的板坯之间,随后沿板坯四周焊接形成叠轧坯;
19.步骤(4):沿叠轧坯四周焊接形成的焊缝处设置有排气孔;
20.步骤(5):将所述叠轧坯热轧后制得叠轧板,随后将叠轧板分离得到成品钢板。
21.优选的,所述步骤(2)中,所述隔离剂涂覆厚度由板坯总变形量决定,当板坯总变形量>90%时,所述隔离剂涂覆厚度为1.2-1.6mm;当板坯总变形量为80%-90%时,所述隔离剂涂覆厚度为0.8—1.2mm;当板坯总变形量≤80%时,所述隔离剂涂覆厚度为0.4—0.8mm。
22.在该技术方案中,所述隔离剂涂覆厚度与总变形量相关,因为总变形量越大,钢板轧后表面积越大,需要涂覆较多的隔离剂才能很好的达到隔离效果;
23.优选的,当隔离层涂覆厚度>0.8mm时,需分多次涂覆,每次涂覆结束后需在50-80℃下烘烤20-40min,且每次涂覆厚度为0.4-0.5mm。
24.在该技术方案中,由于常温下隔离剂具有流动性,一次性涂覆过多,隔离剂会出现涂覆不均匀现象,影响隔离效果;每次涂覆后需低温烘烤,使隔离剂呈近固态,黏着于板坯表面,烘烤时间低于20min,隔离剂呈半液态,后续涂覆时隔离剂依然会流动,且会影响再次涂覆的效果,烘烤时间大于40min,隔离剂已呈固体,完全黏着于板坯表面,烘烤意义不大;
25.优选的,在板坯表面涂覆隔离剂后进行烘干,烘干温度为100—200℃,烘干时间为30-60min,烘干后所述板坯表面形成隔离层。
26.在该技术方案中,隔离剂烘干温度为100-200℃,烘烤时间为30-60min,对于一次涂覆的隔离剂,温度低于100℃时,需要烘烤的时间过长,增加了时间成本;对于多次涂覆的隔离剂,温度低于100℃,烘烤时间低于30min时,无法确保隔离剂已经完全呈固态黏着于板坯表面,而温度大于200℃,烘烤时间大于60min对隔离剂的黏着作用已无积极作用。
27.优选的,所述步骤(1)中,所述板坯打磨后表面粗糙度ra为0.8-1.6μm。
28.在该技术方案中,所述板坯打磨后表面粗糙度ra为0.8-1.6μm,粗糙度<0.8μm时,板坯过于光滑,不利于隔离剂的粘附,粗糙度>1.6μm时,板坯粗糙,叠轧板分板后隔离粉不
易脱落,影响钢板表面光洁度。
29.优选的,所述步骤(4)中,所述叠轧坯四周每侧焊缝设置有至少一个排气孔,所述排气孔直径为10-30mm,且相邻排气孔间距为1.2-1.5m,所述排气孔内填充有保温棉。
30.在该技术方案中,排气孔直径为10-30mm,相邻排气孔间隔为1.2-1.5m,当排气孔直径<10mm,相邻排气孔间隔>1.5m时,在大变形量下轧制时内部的气体无法及时通过排气孔排出,会有一定的安全隐患;当排气孔孔直径>30mm,相邻排气孔间隔<1.2mm时,排气孔较大且过于密集,不仅影响钢板边部的结合效果,而且对钢板破坏较大,还增加了工作量。
31.与现有技术相比,本技术隔离剂成份选取灵活,成本低廉,操作方便快捷,且无有毒气体挥发,通过该方法制备的隔离剂具有较好的附着能力,不会因为板坯间互相挤压、搬运、碰撞而脱落;使用该隔离剂板坯间留有排气孔,无需抽真空,降低了安全隐患;用该隔离剂轧制的钢板易分离且表面质量良好;隔离粉耐高温,且具有阻燃性,高温下能有效阻碍复合板间粘连,且三种隔离粉1200℃轧制温度下互相不反应,因此成份具有可选择性,一定程度上降低了成本;粘结粉价格低廉,具有优异的环保性能,不影响人体健康,且使用少量便有较高的粘合强度。
附图说明
32.为了更清楚地说明本技术实施例或现有技术中的技术方案,下面将对实施例或现有技术描述中所需要使用的附图作简单地介绍,显而易见地,下面描述中的附图仅仅是本技术中记载的一些实施例,对于本领域普通技术人员来讲,在不付出创造性劳动的前提下,还可以根据这些附图获得其他的附图。
33.图1为本发明具体实施例一的双层叠轧坯结构示意图;
34.图2为本发明具体实施例三的三层叠轧坯结构示意图;
35.其中:1为板坯,2为隔离剂,3为排气孔。
具体实施方式
36.下面将结合本发明实施例中的附图,对本发明实施例中的技术方案进行详细的描述,显然,所描述的实施例仅仅是本发明一部分实施例,而不是全部的实施例。基于本发明中的实施例,本领域普通技术人员在没有做出创造性劳动的前提下所获得的所有其他实施例,都属于本发明保护的范围。
37.实施例1
38.结合图1所示,一种非真空叠轧用隔离剂的使用方法,包括:
39.1.称量粒径为180μm的氧化镁粉、氧化铝粉、氧化硅粉15kg倒入容器内,其中氧化镁6kg,氧化铝6kg,氧化硅3kg,再称量粒径为100μm的聚乙烯醇、酚醛树脂共1kg倒入容器内,其中聚乙烯醇0.7kg,酚醛树脂0.3kg,然后倒入68l的工业用水,搅拌10min,静置60min,使粉末充分溶解为粘稠状,且无颗粒感及气泡;
40.2.将220mm厚度的板坯1表面进行打磨,去掉表面的氧化皮及杂物,板坯1表面粗糙度ra为1μm,然后将隔离剂涂覆于光洁的板坯1表面,先在板坯1表面涂覆一层约0.8mm的隔离剂,然后放入在70℃下烘烤30min,使得隔离剂呈近固体状粘附于板坯1表面上,然后继续
涂隔离剂0.5mm,复合板坯的余温会加速隔离剂的凝固,使隔离剂更容易粘着,隔离剂最终涂覆厚度为1.3mm;
41.3.将涂覆有隔离剂的板坯在180℃下烘烤60min后取出,板坯表1面形成一层附着力较强的隔离剂层2;
42.4.将另一块表面打磨干净、表面粗糙度ra为1μm的板坯1与覆有隔离剂的板坯1叠放在一起,采用单丝埋弧焊进行四周焊接得到叠轧坯;
43.5.在叠轧坯焊缝处每隔1.5m开出直径为30mm的排气孔3,为防止隔离剂被污染,气孔内塞入保温棉;
44.6.将总厚度为440mm的叠轧坯进行常规热轧,总变形量为91.36%,得到厚度为38mm的叠轧板,对叠轧板四边进行切割,钢板自动分开,得到两块厚度范围为18.7-19.3mm的钢板,且钢板表面光滑无瑕疵,两块钢板厚度均匀,板型较好,性能合格。
45.实施例2
46.一种非真空叠轧用隔离剂的使用方法,包括:
47.1.称量粒径为180μm的氧化镁粉、氧化铝粉10kg倒入容器内,其中氧化镁5kg,氧化铝5kg,再称量粒径为100μm的聚乙烯醇、酚醛树脂共0.5kg倒入容器内,其中聚乙烯醇0.4kg,酚醛树脂0.1kg,然后倒入35l的工业用水,搅拌8min,静置40min,使粉末充分溶解为粘稠状,且无颗粒感及气泡;
48.2.将100mm厚度的板坯表面进行打磨,去掉表面的氧化皮及杂物,板坯表面粗糙度ra为1μm,然后将隔离剂涂覆于板坯表面,先在板坯表面涂覆一层约0.6mm的隔离剂,然后放入在70℃下烘烤30min,使得隔离剂呈近固体状粘附于板坯表面上,然后继续涂隔离剂0.4mm,复合板坯的余温会加速隔离剂的凝固,使隔离剂更容易粘着,隔离剂最终涂覆厚度为1mm;
49.3.将涂覆有隔离剂的板坯在120℃下烘烤50min后取出,板坯表面形成一层附着力较强的隔离剂层;
50.4.将另一块表面打磨干净、表面粗糙度ra为1μm的板坯与覆有隔离剂的板坯叠放在一起,采用单丝埋弧焊进行四周焊接得到叠轧坯;
51.5.在叠轧坯焊缝处每隔1.5m开出直径为20mm的排气孔,为防止隔离剂被污染,气孔内塞入保温棉;
52.6.将总厚度为200mm的叠轧坯进行常规热轧,总变形量为85%,得到厚度为30mm的叠轧板,对叠轧板四边进行切割,钢板自动分开,得到两块厚度范围为14.7-15.3mm的钢板,且钢板表面光滑无瑕疵,两块钢板厚度均匀,板型较好,性能合格。
53.实施例3
54.结合图2所示,一种非真空叠轧用隔离剂的使用方法,包括:
55.1.称量粒径为180μm的氧化硅粉、氧化铝粉5kg倒入容器内,其中氧化硅2kg,氧化铝3kg,再称量粒径为100μm的聚乙烯醇、酚醛树脂共0.2kg倒入容器内,其中聚乙烯醇0.14kg,酚醛树脂0.06kg,然后倒入25l的工业用水,搅拌5min,静置30min,使粉末充分溶解为粘稠状,且无颗粒感及气泡;
56.2.将24mm厚度规格的坯料表面进行打磨,去掉表面的氧化皮及杂物,板坯1表面粗糙度ra为1μm,然后将隔离剂涂覆于该坯料表面,隔离剂涂覆厚度为0.7mm,得到坯料a;
57.3.另取一块24mm厚度规格的坯料,进行上述操作,得到坯料b;
58.4.将涂覆有隔离剂的坯料a、b在100℃下烘烤30min后取出,坯料表面均形成一层附着力较强的隔离层2;
59.5.将另一块24mm厚度规格的坯料c上下表面均打磨干净,表面粗糙度ra为1μm,将坯料c与覆有隔离剂的坯料a、b叠放在一起,坯料c在坯料a、b之间,采用单丝埋弧焊进行四周焊接得到三层叠轧坯;
60.6.在叠轧坯四周焊缝处每隔1.2m开出直径为10mm的排气孔3,为防止隔离剂被污染,气孔内塞入保温棉;
61.7.将总厚度为72mm的叠轧坯进行常规热轧,总变形量为79.2%,得到厚度为15mm的叠轧板,对叠轧板四边进行切割,钢板自动分开,得到三块厚度范围为4.8-5.2mm的钢板,且钢板表面光滑无瑕疵,三块钢板厚度均匀,板型较好,性能合格。
62.综上所述,本技术隔离剂成份选取灵活,成本低廉,操作方便快捷,且无有毒气体挥发,通过该方法制备的隔离剂具有较好的附着能力,不会因为板坯间互相挤压、搬运、碰撞而脱落;使用该隔离剂板坯间留有排气孔,无需抽真空,降低了安全隐患;用该隔离剂轧制的钢板易分离且表面质量良好;隔离粉耐高温,且具有阻燃性,高温下能有效阻碍复合板间粘连,且三种隔离粉1200℃轧制温度下互相不反应,因此成份具有可选择性,一定程度上降低了成本;粘结粉价格低廉,具有优异的环保性能,不影响人体健康,且使用少量便有较高的粘合强度。
63.需要说明的是,在本文中,诸如第一和第二等之类的关系术语仅仅用来将一个实体或者操作与另一个实体或操作区分开来,而不一定要求或者暗示这些实体或操作之间存在任何这种实际的关系或者顺序。而且,术语“包括”、“包含”或者其任何其他变体意在涵盖非排他性的包含,从而使得包括一系列要素的过程、方法、物品或者设备不仅包括那些要素,而且还包括没有明确列出的其他要素,或者是还包括为这种过程、方法、物品或者设备所固有的要素。在没有更多限制的情况下,由语句“包括一个
……”
限定的要素,并不排除在包括要素的过程、方法、物品或者设备中还存在另外的相同要素。
64.以上仅是本技术的具体实施方式,应当指出,对于本技术领域的普通技术人员来说,在不脱离本技术原理的前提下,还可以做出若干改进和润饰,这些改进和润饰也应视为本技术的保护范围。