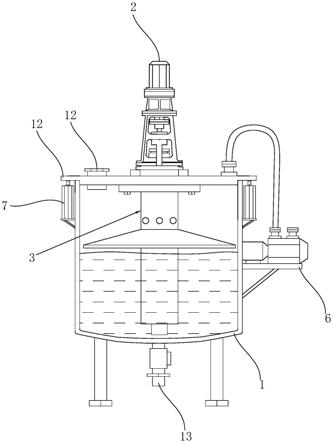
1.本技术涉及环氧树脂灌封胶生产技术领域,尤其是涉及一种环氧树脂灌封胶的制备工艺。
背景技术:
2.环氧灌封胶是指以环氧树脂为主要成分,添加各类功能性助剂和合适的固化剂制作的一类环氧树脂液体封装或灌封材料。相关技术中公开了一种高韧性、耐冲击、高柔性环氧灌封胶,包括a组分和b组分,a组分与b组分的质量比为(10:1)-(20:1),a组分包括以下原料:增韧环氧树脂0-130份,双酚a型环氧树脂5-20份,活性稀释剂1-18份,触变剂1-10份,氧化铝160-320份;b组分包括以下原料:柔性固化剂20-50份,超支化固化剂25-50份,促进剂1-5份。
3.针对上述相关技术中的环氧树脂灌封胶,申请人发现相关技术方案存在以下缺陷:在实际生产过程中发现,填料氧化铝的用量大,而采用常规的分散盘(参考图1)进行分散时,发现有部分填料沉积在分散片下部圆心处,导致物料无法均匀分散脱泡,影响配料的效率和最终产品的质量。
技术实现要素:
4.为了解决相关技术中存在的物料无法均匀分散脱泡,影响配料的效率和最终产品的质量问题,本技术提供了一种环氧树脂灌封胶的制备工艺。
5.本技术提供的一种环氧树脂灌封胶的制备工艺,是通过以下技术方案得以实现的:一种环氧树脂灌封胶的制备工艺,环氧树脂灌封胶包括a组分和b组分,a组分和b组分单独保存且使用时按重量份数比为1:(0.4-0.7)的比例进行混合;所述a组分由包括以下重量份的原料组分:环氧树脂25-40份;填料62-69份;活性稀释剂3-5份;增韧剂5-15份;b组分由包括以下重量份的原料组分:固化剂65-70份;固化促进剂5-7份;所述填料是由65-75份的氧化铝、17-22份的氮化铝、17-22份的氮化硼制备而成;氧化铝的密度4.0g/ml,粒径d50为15-25μm;氮化硼的密度2.3g/ml,粒径d50为8-12μm;氮化铝的密度3.0g/ml,粒径d50为2-5μm,其特征在于:所述环氧树脂灌封胶是由以下方法制备而成,步骤一,制备a组分和b组分:a组分的制备,按配比计量氧化铝、氮化铝、氮化硼,混合均匀后置于110-125℃下烘干1-2h,冷却至室温得填料,按配比计量环氧树脂、填料、活性稀释剂和增韧剂加入到高速分散装置中进行高速分散脱泡,转速控制在350-480rpm,绝对真空度为50-100mbar,脱泡时间为15-30min,得a组分;b组分的制备,将计量准确的固化剂和固化促进剂混合均匀得b组分;步骤二,将b组分加入高速分散装置与a组分进行高速分散脱泡,转速控制在350-480rpm,绝对真空度为50-200mbar,脱泡时间为15-100min,得成品;高速分散装置包括分散釜主体、驱动电机和组合式分散组件,分散釜主体可拆卸连接有封盖;驱动电机固定连接于
封盖;驱动电机通过联轴器与组合式分散组件固定连接;组合式分散组件位于分散釜主体内部,用于对物料进行分散脱泡处理;封盖固定连通有与分散釜主体内部连通的进料管;分散釜主体底部中心固定连通有与分散釜主体内部连通的出料管。
6.通过采用上述技术方案,针对于上述环氧树脂灌封胶配料体系,本技术采用自主研发的高速分散装置对物料进行高效分散脱泡,可将普通分散盘4h的分散时间降低至130min及以下,可有效缩短制备工艺分散脱泡的时间,提升整体生产效率,且可保证配料的精准性,改善最终产品的质量。
7.优选的,所述组合式分散组件包括导流件和组合式搅拌器,导流件可拆卸连接于封盖的下表面;导流件一体成型有贯穿导流件上下表面的流道;组合式搅拌器一端通过联轴器固定连接于驱动电机的输出轴,且组合式搅拌器的另一端靠近分散釜主体的内底面;组合式搅拌器的另一端面与分散釜主体的内底面的垂直距离为1.0-50.0mm;组合式搅拌器位于流道内,且组合式搅拌器与流道留有空隙;组合式搅拌器转动过程中,位于分散釜主体内底部的物料沿流道的轴线在流道内向上运动。
8.通过采用上述技术方案,组合式搅拌器转动可使得物料沿流道的轴线向上运动,物料从导流件的上表面流回至分散釜主体内,可增大气液交换面积,从而改善整体的分散脱泡效率,缩短整体工艺时间,保证所制备产品的质量。
9.优选的,所述导流件包括导流主件、导液分散片和安装法兰,所述导流主件的几何形状为圆环柱;所述导液分散片固定连接于导流主件上部外侧壁;所述安装法兰固定连接于导流主件顶部外侧壁;所述安装法兰可拆卸连接于封盖的下表面;所述导流主件外侧壁贯穿开设有多个与流道连通的导液圆孔;多个所述导液圆孔均匀环绕导流主件的中轴线设置;相邻所述导液圆孔的间距相等;所述导液圆孔位于导液分散片和安装法兰之间;所述导液分散片背向导流主件侧壁的一端与分散釜主体的内壁预留有供物料回流的空隙。
10.通过采用上述技术方案,导液分散片可增大气液交换面积,进一步改善整体的分散脱泡效率,缩短整体工艺时间且保证所制备产品的质量优选的,所述导液分散片背向导流主件侧壁的一端的相对地面高度低于所述导液分散片与导流主件侧壁连接处的相对地面高度。
11.通过采用上述技术方案,可增大气液交换面积且便于物料回流至分散釜主体内,提升整体的脱泡效率和分散效率,缩短整体工艺时间,保证所制备产品的质量。
12.优选的,所述导液分散片背向导流主件侧壁的一端点与所述导液分散片和导流主件侧壁连接处的一点连线位于竖直平面内,且与水平面所成的锐角为10-40
°
。
13.通过优化导液分散片的结构,可进一步提升整体的脱泡效率和分散效率,缩短整体工艺时间,保证所制备产品的质量。
14.优选的,所述组合式搅拌器包括螺旋搅拌器,螺旋搅拌器一端通过联轴器固定连接于驱动电机的输出轴;所述螺旋搅拌器另一端的端面与分散釜主体内底面的垂直距离为1.0-50.0mm;所述螺旋搅拌器上的螺旋带长度是所述导液圆孔中轴线到导流主件下表面的垂直距离的0.95.-1.02倍。
15.通过采用上述技术方案,螺旋搅拌器可使得物料沿流道的轴线向上运动,物料从导流件的导液圆孔流向导液分散片,经过导液分散片的物料流回至分散釜主体内,可增大气液交换面积,从而改善整体的分散脱泡效率,缩短整体工艺时间,保证所制备产品的质
量。
16.优选的,所述组合式搅拌器还包括分散盘,所述分散盘固定连接于螺旋搅拌器螺杆周向;所述分散盘与流道之间预留有空隙;所述分散盘反向固定连接于螺旋搅拌器的螺杆周向;所述分散盘转动过程中,流道内的物料在流道内沿流道的轴线方向向上运动;所述分散盘上表面相对地面的垂直高度是所述导液圆孔中轴线与地面垂直距离高度的0.95-1.02倍。
17.通过采用上述技术方案,分散盘转动过程中使得流道中液体沿流道的轴线向上运动,可减缓物料回流至分散釜主体内底部的时间,从而有利于增大气液交换面积,进一步提升整体的分散均匀性和分散效率,缩短整体工艺时间,保证所制备产品的质量。
18.优选的,所述组合式搅拌器还包括设置于减速组件,所述减速组件连接于螺旋搅拌器的螺杆周向;所述分散盘转动连接于减速组件;所述分散盘反向设置于减速组件,分散盘转动过程中,流道内的物料在流道内沿流道的轴线方向向上运动;所述分散盘上表面相对地面的高度是所述导液圆孔中轴线垂直距离地面高度的0.95-1.02倍。
19.通过采用上述技术方案,分散盘转动过程中使得流道中液体沿流道的轴线向上运动,减速组件可进一步减缓物料回流至分散釜主体内底部的时间,从而有利于增大气液交换面积,进一步提升整体的分散均匀性和分散效率,缩短整体工艺时间,保证所制备产品的质量。
20.优选的,所述减速组件包括主动齿轮、传动齿轮、连接杆和连接板,所述主动齿轮固定连接于螺旋搅拌器的螺杆周向;所述传动齿轮与主动齿轮啮合;所述传动齿轮固定连接于连接杆的周向;所述连接板垂直固定连接于导流主件内壁;所述连接杆转动且固定于两块所述连接板之间;所述连接杆的一端穿设连接板的上下表面且连接杆转动连接于连接板;所述分散盘固定连接于连接杆穿设连接板的上下表面的杆端周向,且分散盘位于连接板的上部。
21.通过采用上述技术方案,位于导液圆孔附近的物料在分散盘的作用下,可进行预分散脱泡,有利于增大气液交换面积,进一步提升整体的分散均匀性和分散效率,缩短整体工艺时间,保证所制备产品的质量。
22.综上所述,本技术具有以下优点:1、本技术采用自主研发的高速分散装置进行配料分散脱泡,可缩短整体工艺时间且保证所制备产品的质量。
23.2、本技术通过优化转速、绝对真空度和时间,可有效降低物料的分散脱泡时间,提升了整体工业的生产效率。
附图说明
24.图1是相关技术中分散盘的结构示意图。
25.图2是本技术中实施例1的整体结构示意图。
26.图3是本技术中实施例1中组合式搅拌器的结构示意图。
27.图4是本技术中实施例2中组合式搅拌器的结构示意图。
28.图5是本技术中实施例2中组合式搅拌器与减速组件的连接结构示意图。
29.图中,1、高速分散装置;10、分散釜主体;11、封盖;12、进料管;13、出料管;2、驱动
电机;3、组合式分散组件;4、导流件;40、流道;41、导流主件;411、导液圆孔;42、导液分散片;43、安装法兰;5、组合式搅拌器;51、螺旋搅拌器;52、分散盘;53、减速组件;531、主动齿轮;5311、通孔;532、传动齿轮;533、连接杆;534、连接板;6、气缸;7、真空泵组。
具体实施方式
30.以下结合附图2-5和实施例对本技术作进一步详细说明。
31.设备设备一参考图2,高速分散装置1包括分散釜主体10、封盖11、驱动电机2和组合式分散组件3,封盖11可拆卸连接于分散釜主体10,用于密封分散釜主体10,便于进行抽真空操作。封盖11固定连通有与分散釜主体10内部连通的真空泵组7,真空泵组7用于对分散釜主体10进行抽空处理。驱动电机2固定连接于封盖11的上表面,驱动电机2的输出轴通过联轴器与组合式分散组件3固定连接,组合式分散组件3位于分散釜主体10内部。驱动电机2驱动组合式分散组件3绕自身轴向方向转动,实现对分散釜主体10内物料进行快速分散脱泡处理的目的。
32.参考图2,封盖11上表面固定连通有与分散釜主体10内部连通的进料管12。进料管12一端与分散釜主体10内部连通,进料管12的另一端位于封盖11的上部且位于封盖11上部的进料管12一端周向螺纹且密封连接了密封盖,密封盖的设置可保证分散釜主体10的密封性。分散釜主体10底部中心固定连通有出料管13。出料管13一端与分散釜主体10内部连通,且出料管13的另一端位于分散釜主体10底部下方。为了便于控制物料流出和罐装,出料管13上固定连通了电磁阀。
33.参考图2,为了便于对分散釜主体10内部进行清洗,分散釜主体10外壁固定连接有气缸6。气缸6的数量为两个,两个气缸6关于分散釜主体10的中轴线呈对称设置。气缸6的推杆固定连接于封盖11的下表面。当两个气缸6同时启动时,封盖11在气缸6的推动下被揭开于分散釜主体10,操作人员即可对分散釜主体10内部进行清洗维护。
34.参考图3,组合式分散组件3是由导流件4和组合式搅拌器5组成,组合式搅拌器5的中轴线呈竖直。其中,导流件4可拆卸连接于封盖11的下表面。导流件4贯穿上下表面一体形成有流道40,流道40的中轴线垂直于水平面。流道40的直径是导流件4外径的0.8-0.9倍,本设备中流道40的直径是导流件4外径的0.88倍。
35.参考图3,组合式搅拌器5的一端通过联轴器固定连接于驱动电机2的输出轴,且组合式搅拌器5的另一端靠近分散釜主体10的内底面。组合式搅拌器5的另一端面与分散釜主体10的内底面的垂直距离在5.0-10mm。组合式搅拌器5位于流道40内,且组合式搅拌器5与流道40留有供物料流动的空隙。组合式搅拌器5转动过程中,位于分散釜主体10内底部的物料沿流道40的轴线在流道40内向上运动。
36.参考图3,导流件4包括导流主件41、导液分散片42和安装法兰43,导流主件41的几何形状为圆环柱,主要是导流主件41一体成型了流道40。导液分散片42焊接于导流主件41上部外侧壁,用于导流物料,增大物料的气液接触面积,加快真空脱泡和除去反应生成水,便于填料均匀分散于体系中,提升整体的生产效率,保证最终产品的质量。安装法兰43焊接于导流主件41顶部外侧壁,且安装法兰43的上表面与导流主件41的上表面平齐。安装法兰
43通过螺栓连接于封盖11的下表面,实现了导流件4与封盖11的可拆卸连接的目的。
37.参考图3,导流主件41外侧壁垂直贯穿开设有多个与流道40连通的导液圆孔411。导液圆孔411的中轴线与导流主件41的中轴线相垂直。导液圆孔411位于导液分散片42和安装法兰43之间,且导液圆孔411的中轴线皆位于同一水平面内。导液圆孔411均匀环绕导流主件41的中轴线设置,即相邻导液圆孔411的间距相等。导液分散片42背向导流主件41侧壁的一端与分散釜主体10的内壁之间预留有供物料回流的空隙。
38.参考图3,为了进一步加快真空脱泡效率,导液分散片42背向导流主件41侧壁的一端的相对地面高度低于所述导液分散片42与导流主件41侧壁连接处的相对地面高度。具体地,导液分散片42背向导流主件41侧壁的一端点与导液分散片42和导流主件41侧壁连接处的一点连线位于竖直平面内,且与水平面所成的锐角为10-40
°
,优选为15
°
。
39.参考图3,组合式搅拌器5包括螺旋搅拌器51、分散盘52,螺旋搅拌器51一端通过联轴器与驱动电机2的输出轴固定连接,螺旋搅拌器51的另一端面距离分散釜主体10内底面的垂直距离为5-10mm。螺旋搅拌器51上螺旋带的长度是导液圆孔411的中轴线到导流主件41下表面垂直距离的1.0倍。螺旋搅拌器51的螺距为1.0倍直径或者1.25倍直径,优选为1.0倍直径。螺旋搅拌器51转动过程中,将分散釜主体10底部液料引入流道40内,流道40内的物料沿流道40轴线方向传输至流道40的上部,从导液圆孔411流出导流主件41,流向导液分散片42上表面,经过导液分散片42的分散,物料回流至分散釜主体10底部,从而增大物料的气液接触面积,加快真空脱泡,便于填料均匀分散于体系中,提升整体的生产效率,保证最终产品的质量。
40.参考图3,分散盘52是反向固定连接在螺旋搅拌器51螺杆的周向,目的是分散盘52转动过程中,流道40内的物料在流道40内沿流道40的轴线方向向上运动。分散盘52与流道40之间预留有供物料流道的空隙。分散盘52上表面相对地面的高度是导液圆孔411中轴线与地面垂直距离高度的1.0倍。
41.分散盘52会随着螺旋搅拌器51转动而发生同步转动,转动的分散盘52带动部分位于流道40内且在导液圆孔411附近的液料沿流道40轴向向上运动,实现了一部分物料从导液圆孔411流出导流主件41,一部分物料被传输至位于导液圆孔411上部的流道40中的目的,对流道40中的物料进行分流处理,避免通过导液圆孔411流出物料的流速过快,进一步增大物料的气液接触面积,加快真空脱泡,便于填料均匀分散于体系中,提升整体的生产效率,保证最终产品的质量。此外,转动的分散盘52可对导液圆孔411附件的液料进行分散处理,可进一步提升真空脱泡的效率,提升整体的生产效率。
42.设备二设备二与设备一的区别在于:参考图4和图5,组合式搅拌器5还包括减速组件53,减速组件53包括主动齿轮531、传动齿轮532、连接杆533和连接板534,主动齿轮531焊接于螺旋搅拌器51的螺杆周向。主动齿轮531贯穿上下表面开设有多个通孔5311。相邻通孔5311中轴线之间的直线距离相等。主动齿轮531的开孔率控制在30-50%,本设备中主动齿轮531的开孔率为40%。传动齿轮532固定连接于连接杆533的轴向,且传动齿轮532与主动齿轮531啮合。导流主件41内壁垂直焊接有两块连接板534。连接杆533转动且固定连接于两块连接板534之间。
43.参考图4和图5,连接杆533相对地面位置较高的一端垂直穿设连接板534的上下表
面,位于连接板534的上表面,且连接杆533是穿设且转动连接于连接板534。分散盘52反向固定连接于连接杆533穿设连接板534的上下表面的杆端的周向。分散盘52反向设置的目的是:一部分物料被传输至位于导液圆孔411上部的流道40中,实现了对物料的分流处理,避免通过导液圆孔411流出的物料流速过快,进一步增大物料的气液接触面积,加快真空脱泡,便于填料均匀分散于体系中,提升整体的生产效率,保证最终产品的质量。
44.参考图4和图5,分散盘52上表面相对地面的高度是导液圆孔411中轴线垂直距离地面高度的1倍。减速组件53中主动齿轮531、传动齿轮532的直径比为3-5:1。本实施例中主动齿轮531与传动齿轮532的直径比控制在4:1因此,螺旋搅拌器51和分散盘52的差速比为3.6:1,即驱动电机2的转速为400rpm,实际分散盘52的转速在1440rpm,可提升整体的生产效率,保证最终产品的质量。实施例
45.实施例1本实施例中的环氧树脂灌封胶包括a组分和b组分,a组分和b组单独保存且使用时按重量份数比为1:0.4的比例进行混合。
46.a组分是由以下重量份的原料组成:25份的环氧树脂、69份的填料、3份的聚乙二醇二缩水甘油醚;15份的端羧基液体丁腈橡胶。
47.填料是由以下重量份数的原料组分:氧化铝65份,氮化硼22份,氮化铝20份。氧化铝的密度4.0g/ml,粒径d50为15μm;氮化硼的密度2.3g/ml,粒径d50为8μm;氮化铝的密度3.0g/ml,粒径d50为3μm。
48.b组分是由以下重量份的原料组成:65份的液体甲基四氢邻苯二甲酸酐和5份的卞基二胺。
49.一种环氧树脂灌封胶的制备工艺,包括以下步骤:步骤一,制备a组分和b组分:a组分的制备,将氧化铝、氮化硼和氮化铝以质量比65:22:20称取,以500rpm混合分散10min,得填料,称取690g的填料置于120℃下烘干2h,冷却至室温,放置在干燥处储存备用,然后将250g的环氧树脂、690g干燥处理的填料、30g的聚乙二醇二缩水甘油醚和150g的端羧基液体丁腈橡胶通过进料管12加入设备一中的分散釜主体10中,进行高速分散、脱泡,绝对真空度为100mbar,转速为350rpm,时间为30min,得a组分;b组分的制备,将650g的液体甲基四氢邻苯二甲酸酐和50g的卞基二胺,以600rpm混合5min,得b组分;步骤二,将步骤一中组成的b组分加入分散釜主体10中与a组分进行高速分散脱泡,转速控制在350rpm,绝对真空度为100mbar,脱泡时间为30min,得成品。
50.实施例2实施例2与实施例1的区别在:一种环氧树脂灌封胶的制备工艺,包括以下步骤:步骤一,制备a组分和b组分:a组分的制备,将氧化铝、氮化硼和氮化铝以质量比65:22:20称取,以500rpm混合分散10min,得填料,称取690g的填料置于120℃下烘干2h,冷却至室温,放置在干燥处储存备用,然后将250g的环氧树脂、690g干燥处理的填料、30g的聚乙二醇二缩水甘油醚和150g
的端羧基液体丁腈橡胶通过进料管12加入设备一中的分散釜主体10中,进行高速分散、脱泡,绝对真空度控制在100mbar,转速为400rpm,时间为25min,得a组分;b组分的制备,将650g的液体甲基四氢邻苯二甲酸酐和50g的卞基二胺,以600rpm混合5min,得b组分;步骤二,将步骤一中组成的b组分加入分散釜主体10中与a组分进行高速分散脱泡,转速控制在400rpm,绝对真空度为100mbar,脱泡时间为25min,得成品。
51.实施例3实施例3与实施例1的区别在:一种环氧树脂灌封胶的制备工艺,包括以下步骤:步骤一,制备a组分和b组分:a组分的制备,将氧化铝、氮化硼和氮化铝以质量比65:22:20称取,以500rpm混合分散10min,得填料,称取690g的填料置于120℃下烘干2h,冷却至室温,放置在干燥处储存备用,然后将250g的环氧树脂、690g干燥处理的填料、30g的聚乙二醇二缩水甘油醚和150g的端羧基液体丁腈橡胶通过进料管12加入设备一中的分散釜主体10中,进行高速分散、脱泡,绝对真空度控制在100mbar,转速为440rpm,时间为20min,得a组分;b组分的制备,将650g的液体甲基四氢邻苯二甲酸酐和50g的卞基二胺,以600rpm混合5min,得b组分;步骤二,将步骤一中组成的b组分加入分散釜主体10中与a组分进行高速分散脱泡,转速控制在440rpm,绝对真空度为100mbar,脱泡时间为25min,得成品。
52.实施例4实施例4与实施例1的区别在:一种环氧树脂灌封胶的制备工艺,包括以下步骤:步骤一,制备a组分和b组分:a组分的制备,将氧化铝、氮化硼和氮化铝以质量比65:22:20称取,以500rpm混合分散10min,得填料,称取690g的填料置于120℃下烘干2h,冷却至室温,放置在干燥处储存备用,然后将250g的环氧树脂、690g干燥处理的填料、30g的聚乙二醇二缩水甘油醚和150g的端羧基液体丁腈橡胶通过进料管12加入设备一中的分散釜主体10中,进行高速分散、脱泡,绝对真空度控制在100mbar,转速为480rpm,时间为15min,得a组分;b组分的制备,将650g的液体甲基四氢邻苯二甲酸酐和50g的卞基二胺,以600rpm混合5min,得b组分;步骤二,将步骤一中组成的b组分加入分散釜主体10中与a组分进行高速分散脱泡,转速控制在480rpm,绝对真空度为100mbar,脱泡时间为20min,得成品。
53.实施例5实施例5与实施例1的区别在:一种环氧树脂灌封胶的制备工艺,包括以下步骤:步骤一,制备a组分和b组分:a组分的制备,将氧化铝、氮化硼和氮化铝以质量比65:22:20称取,以500rpm混合分散10min,得填料,称取690g的填料置于120℃下烘干2h,冷却至室温,放置在干燥处储存备用,然后将250g的环氧树脂、690g干燥处理的填料、30g的聚乙二醇二缩水甘油醚和150g
的端羧基液体丁腈橡胶通过进料管12加入设备二中的分散釜主体10中,进行高速分散、脱泡,绝对真空度控制在100mbar,转速为350rpm,时间为30min,得a组分;b组分的制备,将650g的液体甲基四氢邻苯二甲酸酐和50g的卞基二胺,以600rpm混合5min,得b组分;步骤二,将步骤一中组成的b组分加入分散釜主体10中与a组分进行高速分散脱泡,转速控制在350rpm,绝对真空度为100mbar,脱泡时间为30min,得成品。
54.实施例6实施例6与实施例1的区别在:一种环氧树脂灌封胶的制备工艺,包括以下步骤:步骤一,制备a组分和b组分:a组分的制备,将氧化铝、氮化硼和氮化铝以质量比65:22:20称取,以500rpm混合分散10min,得填料,称取690g的填料置于120℃下烘干2h,冷却至室温,放置在干燥处储存备用,然后将250g的环氧树脂、690g干燥处理的填料、30g的聚乙二醇二缩水甘油醚和150g的端羧基液体丁腈橡胶通过进料管12加入设备二中的分散釜主体10中,进行高速分散、脱泡,绝对真空度控制在100mbar,转速为480rpm,时间为15min,得a组分;b组分的制备,将650g的液体甲基四氢邻苯二甲酸酐和50g的卞基二胺,以600rpm混合5min,得b组分;步骤二,将步骤一中组成的b组分加入分散釜主体10中与a组分进行高速分散脱泡,转速控制在480rpm,绝对真空度为100mbar,脱泡时间为15min,得成品。
55.实施例7实施例7与实施例1的区别在:一种环氧树脂灌封胶的制备工艺,包括以下步骤:步骤一,制备a组分和b组分:a组分的制备,将氧化铝、氮化硼和氮化铝以质量比65:22:20称取,以500rpm混合分散10min,得填料,称取690g的填料置于120℃下烘干2h,冷却至室温,放置在干燥处储存备用,然后将250g的环氧树脂、690g干燥处理的填料、30g的聚乙二醇二缩水甘油醚和150g的端羧基液体丁腈橡胶通过进料管12加入设备二中的分散釜主体10中,进行高速分散、脱泡,绝对真空度控制在100mbar,转速为400rpm,时间为20min,得a组分;b组分的制备,将650g的液体甲基四氢邻苯二甲酸酐和50g的卞基二胺,以600rpm混合5min,得b组分;步骤二,将步骤一中组成的b组分加入分散釜主体10中与a组分进行高速分散脱泡,转速控制在480rpm,绝对真空度为100mbar,脱泡时间为60min,脱泡60min后,停止搅拌,继续抽真空40min,得成品。
56.实施例8实施例8与实施例1的区别在于:一种环氧树脂灌封胶的制备工艺,包括以下步骤:步骤一,制备a组分和b组分:a组分的制备,将氧化铝、氮化硼和氮化铝以质量比65:22:20称取,以500rpm混合分散10min,得填料,称取690g的填料置于120℃下烘干2h,冷却至室温,放置在干燥处储存备用,然后将250g的环氧树脂、690g干燥处理的填料、30g的聚乙二醇二缩水甘油醚和150g
的端羧基液体丁腈橡胶通过进料管12加入设备一中的分散釜主体10中,进行高速分散、脱泡,绝对真空度为50mbar,转速为350rpm,时间为30min,得a组分;b组分的制备,将650g的液体甲基四氢邻苯二甲酸酐和50g的卞基二胺,以600rpm混合5min,得b组分;步骤二,将步骤一中组成的b组分加入分散釜主体10中与a组分进行高速分散脱泡,转速控制在350rpm,绝对真空度为50mbar,脱泡时间为30min,得成品。
57.实施例9实施例9与实施例1的区别在于:一种环氧树脂灌封胶的制备工艺,包括以下步骤:步骤一,制备a组分和b组分:a组分的制备,将氧化铝、氮化硼和氮化铝以质量比65:22:20称取,以500rpm混合分散10min,得填料,称取690g的填料置于120℃下烘干2h,冷却至室温,放置在干燥处储存备用,然后将250g的环氧树脂、690g干燥处理的填料、30g的聚乙二醇二缩水甘油醚和150g的端羧基液体丁腈橡胶通过进料管12加入设备一中的分散釜主体10中,进行高速分散、脱泡,绝对真空度为50mbar,转速为350rpm,时间为30min,得a组分;b组分的制备,将650g的液体甲基四氢邻苯二甲酸酐和50g的卞基二胺,以600rpm混合5min,得b组分;步骤二,将步骤一中组成的b组分加入分散釜主体10中与a组分进行高速分散脱泡,转速控制在350rpm,绝对真空度为200mbar,脱泡时间为30min,得成品。
58.实施例10实施例10与实施例1的区别在于:一种环氧树脂灌封胶的制备工艺,包括以下步骤:步骤一,制备a组分和b组分:a组分的制备,将氧化铝、氮化硼和氮化铝以质量比65:22:20称取,以500rpm混合分散10min,得填料,称取690g的填料置于120℃下烘干2h,冷却至室温,放置在干燥处储存备用,然后将250g的环氧树脂、690g干燥处理的填料、30g的聚乙二醇二缩水甘油醚和150g的端羧基液体丁腈橡胶通过进料管12加入设备一中的分散釜主体10中,进行高速分散、脱泡,绝对真空度为50mbar,转速为420rpm,时间为30min,得a组分;b组分的制备,将650g的液体甲基四氢邻苯二甲酸酐和50g的卞基二胺,以600rpm混合5min,得b组分;步骤二,将步骤一中组成的b组分加入分散釜主体10中与a组分进行高速分散脱泡,转速控制在420rpm,绝对真空度为50mbar,脱泡时间为40min,脱泡40min后,停止搅拌,继续抽真空40min,得成品。
59.对比例对比例1一种环氧树脂灌封胶的制备工艺,包括以下步骤:步骤一,制备a组分和b组分:a组分的制备,将氧化铝、氮化硼和氮化铝以质量比65:22:20称取,以500rpm混合分散10min,得填料,称取690g的填料置于120℃下烘干2h,冷却至室温,放置在干燥处储存备用,然后将250g的环氧树脂、690g干燥处理的填料、30g的聚乙二醇二缩水甘油醚和150g
的端羧基液体丁腈橡胶加入常规高速分散釜中,采用常规的分散盘(参见图1)中进行高速分散、脱泡,绝对真空度控制在100mbar,转速为2800rpm,时间为3h,得a组分;b组分的制备,将650g的液体甲基四氢邻苯二甲酸酐和50g的卞基二胺,以600rpm混合5min,得b组分;步骤二,将步骤一中组成的b组分加入常规高速分散釜中与a组分进行高速分散脱泡,绝对真空度控制200mbar,转速为2800rpm,时间为1h,得成品。
60.对比例2一种环氧树脂灌封胶的制备工艺,包括以下步骤:步骤一,制备a组分和b组分:a组分的制备,将氧化铝、氮化硼和氮化铝以质量比65:22:20称取,以500rpm混合分散10min,得填料,称取690g的填料置于120℃下烘干2h,冷却至室温,放置在干燥处储存备用,然后将250g的环氧树脂、690g干燥处理的填料、30g的聚乙二醇二缩水甘油醚和150g的端羧基液体丁腈橡胶加入常规高速分散釜中,采用常规的分散盘(参见图1)中进行高速分散、脱泡,绝对真空度控制在100mbar,转速为2800rpm,时间为2.0h,得a组分;b组分的制备,将650g的液体甲基四氢邻苯二甲酸酐和50g的卞基二胺,以600rpm混合5min,得b组分;步骤二,将步骤一中组成的b组分加入常规高速分散釜中与a组分进行高速分散脱泡,绝对真空度控制200mbar,转速为2800rpm,时间为1.0h,得成品。
61.对比例3一种环氧树脂灌封胶的制备工艺,包括以下步骤:步骤一,制备a组分和b组分:a组分的制备,将氧化铝、氮化硼和氮化铝以质量比65:22:20称取,以500rpm混合分散10min,得填料,称取690g的填料置于120℃下烘干2h,冷却至室温,放置在干燥处储存备用,然后将250g的环氧树脂、690g干燥处理的填料、30g的聚乙二醇二缩水甘油醚和150g的端羧基液体丁腈橡胶通过进料管12加入设备一中的分散釜主体10中,进行高速分散、脱泡,绝对真空度控制在100mbar,转速为250rpm,时间为30min,得a组分;b组分的制备,将650g的液体甲基四氢邻苯二甲酸酐和50g的卞基二胺,以600rpm混合5min,得b组分;步骤二,将步骤一中组成的b组分加入分散釜主体10中与a组分进行高速分散脱泡,转速控制在250rpm,绝对真空度为100mbar,脱泡时间为30min,得成品。
62.对比例4一种环氧树脂灌封胶的制备工艺,包括以下步骤:步骤一,制备a组分和b组分:a组分的制备,将氧化铝、氮化硼和氮化铝以质量比65:22:20称取,以500rpm混合分散10min,得填料,称取690g的填料置于120℃下烘干2h,冷却至室温,放置在干燥处储存备用,然后将250g的环氧树脂、690g干燥处理的填料、30g的聚乙二醇二缩水甘油醚和150g的端羧基液体丁腈橡胶通过进料管12加入设备一中的分散釜主体10中,进行高速分散、脱泡,绝对真空度控制在100mbar,转速为520rpm,时间为15min,得a组分;b组分的制备,将650g的液体甲基四氢邻苯二甲酸酐和50g的卞基二胺,以600rpm
混合5min,得b组分;步骤二,将步骤一中组成的b组分加入分散釜主体10中与a组分进行高速分散脱泡,转速控制在520rpm,绝对真空度为100mbar,脱泡时间为15min,得成品。注:以520rpm进行配料过程中发现,物料发生飞溅的情况,因此,转速控制在500rpm以下,避免出现物料发生飞溅的情况的转速上限在480rpm。
63.对比例5对比例5与实施例1的区别在于:一种环氧树脂灌封胶的制备工艺,包括以下步骤:步骤一,制备a组分和b组分:a组分的制备,将氧化铝、氮化硼和氮化铝以质量比65:22:20称取,以500rpm混合分散10min,得填料,称取690g的填料置于120℃下烘干2h,冷却至室温,放置在干燥处储存备用,然后将250g的环氧树脂、690g干燥处理的填料、30g的聚乙二醇二缩水甘油醚和150g的端羧基液体丁腈橡胶通过进料管12加入设备一中的分散釜主体10中,进行高速分散、脱泡,绝对真空度为30mbar,转速为350rpm,时间为30min,得a组分;b组分的制备,将650g的液体甲基四氢邻苯二甲酸酐和50g的卞基二胺,以600rpm混合5min,得b组分;步骤二,将步骤一中组成的b组分加入分散釜主体10中与a组分进行高速分散脱泡,转速控制在350rpm,绝对真空度为30mbar,脱泡时间为30min,得成品。
64.对比例6对比例6与实施例1的区别在于:一种环氧树脂灌封胶的制备工艺,包括以下步骤:步骤一,制备a组分和b组分:a组分的制备,将氧化铝、氮化硼和氮化铝以质量比65:22:20称取,以500rpm混合分散10min,得填料,称取690g的填料置于120℃下烘干2h,冷却至室温,放置在干燥处储存备用,然后将250g的环氧树脂、690g干燥处理的填料、30g的聚乙二醇二缩水甘油醚和150g的端羧基液体丁腈橡胶通过进料管12加入设备一中的分散釜主体10中,进行高速分散、脱泡,绝对真空度为300mbar,转速为350rpm,时间为30min,得a组分;b组分的制备,将650g的液体甲基四氢邻苯二甲酸酐和50g的卞基二胺,以600rpm混合5min,得b组分;步骤二,将步骤一中组成的b组分加入分散釜主体10中与a组分进行高速分散脱泡,转速控制在350rpm,绝对真空度为300mbar,脱泡时间为30min,得成品。
65.性能检测试验检测方法/试验方法1、物料分散性能的测试:通过100目的筛网进行分筛,观察筛网上是否存在颗粒物残留,从而判断配料的分散情况。
66.2、测试甲乙组的含水量:按照gb/t 6283-2008《化工产品中水分含量的测定卡尔.费休法(通用方法)》中的规定进行。
67.3、测试固化物的绝缘性能:按照gb/t 15022.2-2007《电气绝缘用树脂基活性复合物第2部分:试验方法》中的规定进行。
68.4、比重的测试:按照gb/t 12007.5-1989《环氧树脂密度测定法比重瓶法》中的规定进行。
69.5、导热系数的测试:按照gb/t 11205-2009《橡胶热导率的测定热线法》中的规定进行。
70.数据分析表1是实施例1-10和对比例1-6的分散性测试参数测试项情况实施例1均匀分散,100目筛分无颗粒物残留实施例2均匀分散,100目筛分无颗粒物残留实施例3均匀分散,100目筛分无颗粒物残留实施例4均匀分散,100目筛分无颗粒物残留实施例5均匀分散,100目筛分无颗粒物残留实施例6均匀分散,100目筛分无颗粒物残留实施例7均匀分散,100目筛分无颗粒物残留实施例8均匀分散,100目筛分无颗粒物残留实施例9均匀分散,100目筛分无颗粒物残留实施例10均匀分散,100目筛分无颗粒物残留对比例1分散不均,100目筛网有颗粒物残留对比例2分散不均,100目筛网有较多颗粒物残留对比例3分散不均,100目筛网有颗粒物残留对比例4均匀分散,100目筛分无颗粒物残留对比例5均匀分散,100目筛分无颗粒物残留对比例6分散不均,100目筛网有颗粒物残留表2是实施例1-10和对比例1-6的测试参数 比重(g/ml)导热系数w/(m*k)含水量ppm绝缘性能ω*mm实施例11.851.1144681.02*10
16
实施例21.861.1163901.08*10
16
实施例31.841.1164321.05*10
16
实施例41.871.1134641.02*10
16
实施例51.861.1143461.12*10
16
实施例61.851.1163671.10*10
16
实施例71.861.117961.23*10
16
实施例81.851.1164031.06*10
16
实施例91.841.1134968.7*10
15
实施例101.861.1161061.21*10
16
对比例11.781.05810387.21*10
14
对比例21.791.06415203.1*10
14
对比例31.811.1125127.9*10
15
对比例41.851.1154011.02*10
16
对比例51.861.1153821.09*10
16
对比例61.841.1126822.1*10
15
结合实施例1-10和对比例1-6并结合表1-2可以看出,采用设备一中的高速分散装置进行真空脱泡处理,步骤一中绝对真空度控制在50-100mbar,转速为350-480rpm,时间为15-30min且步骤二,绝对真空度控制在50-200mbar,转速为350-480rpm,时间为15-100min,可制备得到含水量较低且绝缘性能更好的成品,且可有效缩短整体工艺的时间,提升整体的生产效率。
71.结合实施例1-10和对比例1-6并结合表1-2可以看出,实施例5与实施例1对比可知,采用设备二中的高速分散装置进行真空脱泡处理的效率优于采用设备一中的高速分散装置进行真空脱泡处理的效率。
72.结合实施例1-10和对比例1-6并结合表1-2可以看出,实施例1中物料的分散效果比对比例3中物料的分散效果好,且与对比例4中物料的分散效果相近,因此,采用自行研发的高速分散装置进行真空脱泡处理,步骤一中绝对真空度控制在100mbar,转速为350-480rpm,时间为15-30min且步骤二,绝对真空度控制在100mbar,转速为350-480rpm,时间为15-30min,可制备得到含水量低且绝缘性能更好的成品,且可有效缩短整体工艺的时间,提升整体的生产效率。
73.结合实施例1-10和对比例1-6并结合表1-2可以看出,实施例7中制备产品性能含水量最低且绝缘性最佳,因此,实施例7步骤二,转速控制在480rpm,绝对真空度为100mbar,脱泡时间为60min,脱泡60min后,停止搅拌,继续抽真空40min,可得到含水量低且绝缘性优良的环氧树脂灌封胶。实施例7相对于实施例1-6虽然整体工艺时间有所延长,但是最终制备的产品含水量低,绝缘性优良,且与比对比例1相比,整体工艺时间缩短,不仅可保证配料的精准性,改善产品的质量,同时可有效缩短整体工艺的时间,提升整体的生产效率。
74.本具体实施例仅仅是对本技术的解释,其并不是对本技术的限制,本领域技术人员在阅读完本说明书后可以根据需要对本实施例做出没有创造性贡献的修改,但只要在本技术的权利要求范围内都受到专利法的保护。