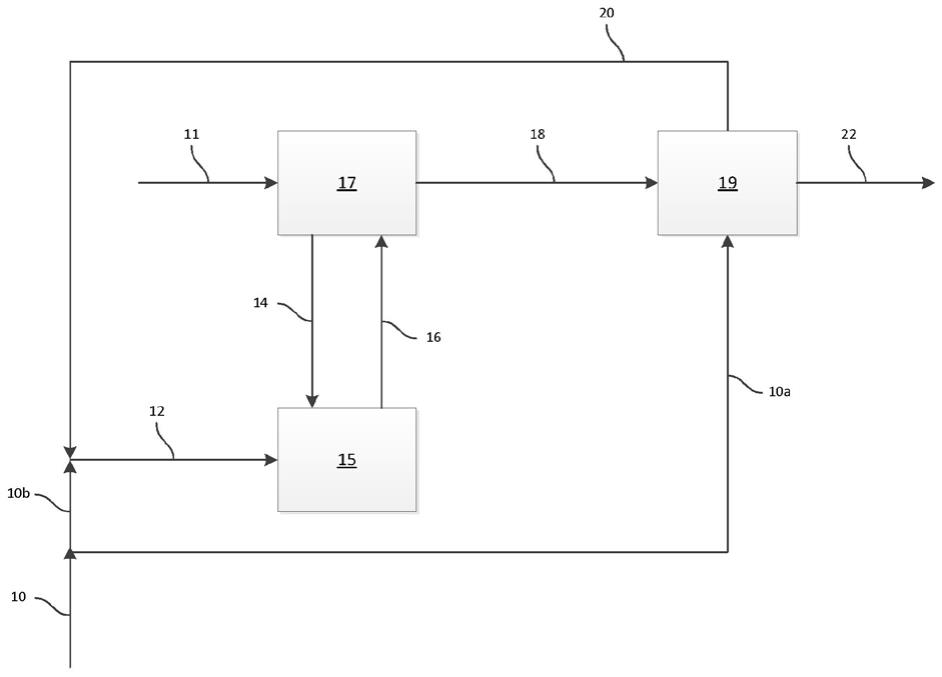
1.本发明涉及用于管理和利用在中间馏分油燃料的制造中加氢处理生物原料的过程中生成的轻馏分,即丙烷的改进的装置和方法。
背景技术:
2.近年来的特点是欧洲共同体对燃料,特别是柴油燃料基料的需求迅速增长,以及与全球变暖和温室气体排放有关的问题的重要性。结果是希望降低对化石基原料的能源依赖性和减少co2排放。
3.在这一背景下,对可容易集成到传统的精炼和燃料生产模式中的由可再生来源制造燃料的新方法的研究是越来越重要的问题。因此,由于化石燃料的成本上升,近年来越来越感兴趣的是将由木质纤维素生物质的转化或由植物油或动物脂肪的生产获得的生物来源的新产品集成到精炼方法中。申请人的发明集中于后者——通常由植物油和动物脂肪副产品生产生物燃料。关于绿色柴油技术和其中使用的催化剂的概述,请参见green diesel: biomass feedstocks, production technologies, catalytic research, fuel properties and performance in compression ignition internal combustion engines”, douvartzides s.、charisiou n.、papageridis k.和goula m. energies 2019, 12, 809,其经此引用并入本文。
4.此外,迄今已知的使用植物油或动物脂肪的方法是资源密集型的并产生co2,co2以其对环境的负面影响著称。在这些生物燃料的生产中更加集成的方法因此肯定有优势。
5.燃料基料的生产因此越来越被认为是对农业世界有吸引力的新出路,尤其是对碾磨含油种子,如油菜籽、大豆或葵花籽的植物油生产商而言。实际上,这些植物油由具有长烷基链的甘油三酯形式的脂肪酸组成,所述长烷基链的结构对应于瓦斯油和煤油馏分的正链烷烃(12至24个碳原子的链长,取决于植物油的性质)。由于在它们的天然状态下与现代柴油发动机不相容,这些植物油必须被预先转化。
6.两种化学途径常用于将这些生物原料转化成中间馏分油燃料:酯交换和加氢处理。
7.酯交换反应利用醇,如甲醇,以产生常被称为生物柴油的植物油甲酯(vome)。这种途径如今在欧洲广泛使用,因为vome的产量在过去十年急剧增加,在2003年达到1.5 mt(在1992年至2003年之间平均年增长率为35%)。促进生物燃料的欧洲指令(2003/30 / ec)特别支持这种生产,其设立了在运输行业中生物燃料消耗量的增长目标。这些消耗量必须在2005年达到用于运输的汽油和柴油燃料的全球消耗量的至少2%,在2010年达到5.75%并在2015年达到8%(以能量衡量的百分比)。但是,这种类型的方法相对昂贵并且需要限制植物油的类型以满足生物柴油规格。此外,必须小心地选择这种类型的方法的进料,以致许多植物油不能以这种方式处理。最后,这些产品的低温流动性质也是限制因素。
8.如上文提到,加氢处理方法在于通过借助加氢精制(hydrotreatment)或加氢转化法将植物油转化成脂肪酸衍生物来直接开发利用植物油,加氢精制或加氢转化法的催化剂
也因其加氢脱氧性质而是本领域技术人员众所周知的(参见例如e. laurent, delmon b., catal.app., 1994,第109卷, 第1期, 第77
ꢀ‑ꢀ
97页和sunflower oil to green diesel over raney-type ni-catalyst”, onyestyak g., harnow s., szegedi a.和kallo d,两者都经此引用并入本文)。
9.由于加氢处理能够生产具有更高稳定性并容易与衍生自矿物油的烃共混的烃产品,加氢处理在商业上更常使用。在这种情况下,将甘油三酯主要转化成链烷烃和饱和的衍生物,由此因其良好的十六烷值而构成柴油燃料池的优异的烃基料。
10.在典型的可再生柴油厂配置中,将来自氢气站的氢气与经预处理的生物原料一起进料至加氢处理,其包括加氢精制步骤和异构化步骤。
11.生物原料通常需要预处理,因为在动物脂肪和/或植物油中导致痕量元素存在的污染物阻碍在加氢处理过程中将这些原料催化转化成烃的能力。例如,某些元素和含这些元素的化合物(例如磷、含磷化合物、和金属,如钙和镁)毒化加氢处理催化剂或降低其活性,由此缩短它们的有效寿命并因此提高生物燃料生产的总成本。在尽可能最大程度上减少含脂肪酸或含甘油三酯的组分的某些污染物(和因此原料的污染物)的处理方法因此在将生物原料加氢处理成中间馏分油产品中提供重要的商业优势。已经报道了多种多样的不同预处理方案,其各自提供不同优点和缺点。
12.甘油三酯的加氢精制包括几种不同反应。在第一反应中,加入氢以使不饱和植物油甘油三酯的双键饱和。在第二反应中,加入氢以除去丙烷主链,由此将饱和植物油甘油三酯转化成脂肪酸。最后,脂肪酸发生加氢脱氧(通过加入更多的氢,氧作为h2o离开)或脱羧(氧作为co2离开,没有进一步加入氢),或这两者的组合。结果获得直链链烷烃的混合物。下面显示用于加氢精制方法的反应路线。
13.烷烃异构化和裂化步骤随后使得生物燃料的品质等于或优于常规石油燃料的规格。
14.此后处理来自加氢处理段的流出物以将轻质组分(lightened components)与流出物的液体部分分离。这可以许多方式实现,包括送至汽提塔,在此借助汽提蒸气物流,通常过热蒸汽从液体物流中除去一种或多种组分,以形成烃燃料产物。或者,可将流出物送至再沸蒸馏塔以分离轻馏分。
15.无论在分离轻馏分的同一蒸馏塔中还是在单独蒸馏塔中,也常见的是将液体流出物分离成单独的液体产物;这些液体产物通常可包括石脑油产物、煤油产物和/或柴油或瓦斯油产物。
16.本文描述的本发明集中于加氢处理区与氢气站段之间的相互作用。加氢精制段产生若干副产物;一些副产物,如水,源于加氢精制反应,一些轻馏分通过作为副反应发生的轻微裂化产生。加氢精制甘油三酯的主要副产物之一是丙烷。丙烷的管理因此是重要的考
量。当将反应器流出物分离成蒸气和液体时,必须从加氢精制回路中除去丙烷;没有充分除去的丙烷将积聚在再循环气体中,因此稀释送至加氢精制反应器的氢气的纯度。
17.现有技术状况通常以两种方式之一释放丙烷。丙烷的第一种释放(discharge)通常是来自加氢精制回路的高压蒸气排出;这可能可用于将丙烷送至氢气站或用于纯化,但是排出物流具有高浓度的有价值的氢气,其可以使排出物流的目的地变复杂或超尺寸。丙烷的第二种释放通常是来自从液体加氢精制流出物中除去轻馏分的塔的低压排出;这种方法通常使用丙烷作为低价值燃料或需要显著压缩以将丙烷送至另一目的地。通过加氢精制反应生成的丙烷通常太过量以致无法用作用于运行氢气站的燃料并因此可能浪费地燃烧丙烷而没有产生价值。鉴于上述情况,需要更高效和有效管理和利用在中间馏分油的制造中由生物原料的加氢处理生成的丙烷的处理方案。
18.因此本发明的目的是建立与生物原料的加氢处理结合,高效且有效利用轻馏分物流的方法,其包括:a) 将经预处理的生物原料和氢气物流进料至加氢处理区,其利用至少一种固体催化剂催化加氢精制反应并产生加氢处理液体流出物;b) 将所述加氢处理液体流出物和轻质烃汽提介质进料至轻馏分回收区,其中使所述轻质烃汽提介质与所述加氢处理液体流出物接触以产生回收的轻馏分物流和气体汽提的液体流出物物流;和c) 将所述回收的轻馏分物流进料至制氢区,其中所述制氢区利用所述回收的轻馏分物流中的烃作为原料以产生步骤(a)中使用的所述氢气物流的至少一部分。
19.本发明的另一目的是建立与生物原料的加氢处理结合,高效且有效利用轻馏分物流的方法,其包括:a) 将经预处理的生物原料和氢气物流进料至加氢处理区,其利用至少一种固体催化剂催化加氢精制反应并产生加氢处理液体流出物;b) 将所述加氢处理液体流出物和轻质烃汽提介质进料至轻馏分回收区,其中使所述轻质烃汽提介质与所述加氢处理液体流出物接触以产生回收的轻馏分物流和汽提的液体流出物物流;c) 将所述回收的轻馏分物流进料至轻馏分分离区以产生lpg物流和轻质残余气体物流;和d) 将所述轻质残余气体物流进料至制氢区,其中所述制氢区利用所述残余气体物流中的烃作为原料以产生步骤(a)中使用的所述氢气物流的至少一部分。
20.本发明的另一目的是建立与生物原料的加氢处理结合,高效且有效利用轻馏分物流的方法,其包括:a) 将经预处理的生物原料和氢气物流进料至加氢处理区,其利用至少一种固体催化剂催化加氢精制反应并产生加氢处理液体流出物;b) 将所述加氢处理液体流出物和轻质烃汽提介质进料至轻馏分回收区,其中使所述轻质烃汽提介质与所述加氢处理液体流出物接触以产生回收的轻馏分物流和气体汽提的液体流出物物流;c) 将所述气体汽提的液体流出物物流进料至二次加氢处理区,其利用至少一种二次固体催化剂催化附加加氢处理反应以产生二次加氢处理液体流出物;
d) 将所述回收的轻馏分物流进料至制氢区,其中所述制氢区利用所述回收的轻馏分物流中的烃作为原料以产生富氢蒸气流出物物流;e) 将所述富氢蒸气流出物物流进料至所述二次加氢处理区;和其中此后将来自所述二次加氢处理区的过量氢气级联到所述加氢处理区。
技术实现要素:
21.本发明涉及在将生物原料转化成中间馏分油烃燃料的方法的过程中高效且有效利用轻馏分物流的方法。
22.本发明的第一个目的/实施方案是加氢处理生物原料的方法,其包括:a) 将经预处理的生物原料和氢气物流进料至加氢处理区,其利用至少一种固体催化剂催化加氢精制反应并产生加氢处理液体流出物;b) 将所述加氢处理液体流出物和轻质烃汽提介质进料至轻馏分回收区,其中使所述轻质烃汽提介质与所述加氢处理液体流出物接触以产生回收的轻馏分物流和气体汽提的液体流出物物流;和c) 将所述回收的轻馏分物流进料至制氢区,其中所述制氢区利用所述回收的轻馏分物流中的烃作为原料以产生步骤(a)中使用的所述氢气物流的至少一部分。
23.本发明的第二个目的/实施方案是将生物原料加氢处理成中间馏分油烃燃料的方法,其包括:a) 将经预处理的生物原料和氢气物流进料至加氢处理区,其利用固体催化剂催化加氢精制反应并产生加氢处理液体流出物;b) 将所述加氢处理液体流出物和轻质烃汽提介质进料至轻馏分回收区,其中使所述轻质烃汽提介质与所述加氢处理液体流出物接触以产生回收的轻馏分物流和汽提的液体流出物物流;c) 将所述回收的轻馏分物流进料至轻馏分分离区以产生lpg物流和轻质残余气体物流;和d) 将所述轻质残余气体物流进料至制氢区,其中所述制氢区利用所述残余气体物流中的烃作为原料以产生步骤(a)中使用的所述氢气物流的至少一部分。
24.本发明的第三个目的/实施方案是加氢处理生物原料的方法,其包括:a) 将经预处理的生物原料和氢气物流进料至加氢处理区,其利用至少一种固体催化剂催化加氢精制反应并产生加氢处理液体流出物;b) 将所述加氢处理液体流出物和轻质烃汽提介质进料至轻馏分回收区,其中使所述轻质烃汽提介质与所述加氢处理液体流出物接触以产生回收的轻馏分物流和气体汽提的液体流出物物流;c) 将所述气体汽提的液体流出物物流进料至二次加氢处理区,其利用至少一种二次固体催化剂催化附加加氢处理反应以产生二次加氢处理液体流出物;d) 将所述回收的轻馏分物流进料至制氢区,其中所述制氢区利用所述回收的轻馏分物流中的烃作为原料以产生富氢蒸气流出物物流;e) 将所述富氢蒸气流出物物流进料至所述二次加氢处理区;和其中此后将来自所述二次加氢处理区的过量氢气级联到所述加氢处理区。
25.可设计本发明的方法,尤其根据本发明的第一和第二个目的/实施方案的本发明的方法,使得此后利用选自溶解气体除去、液体产物分馏、异构化反应步骤和/或加氢裂化反应步骤的一种或多种方法进一步处理所述气体汽提的液体流出物物流以制造中间馏分油烃燃料。
26.可设计本发明的方法,尤其根据本发明的第一和第二个目的/实施方案的本发明的方法,使得此后利用异构化步骤进一步处理所述气体汽提的液体流出物物流以制造中间馏分油烃燃料,所述异构化步骤产生富氢蒸气流出物物流并且此后将所述富氢蒸气流出物级联回所述加氢处理区。
27.可设计本发明的方法,尤其根据本发明的第一和第二个目的/实施方案的本发明的方法,使得此后利用加氢裂化步骤进一步处理所述气体汽提的液体流出物物流以制造中间馏分油烃燃料,所述加氢裂化步骤产生富氢蒸气流出物物流并且此后将所述富氢蒸气流出物级联回所述加氢处理区。
28.在根据本发明的方法中,加氢处理区和/或二次加氢处理区可在145℃至400℃的温度、10巴至150巴的压力和0.1至10 h-1
的lhsv下运行。
29.在根据本发明的方法中,固体催化剂可包含在载体上的加氢脱氧功能物质(function),所述加氢脱氧功能物质包含选自钴和镍的至少一种第viii族金属、选自钼和钨的至少一种第vib族金属、或选自钴和镍的至少一种第viii族金属和选自钼和钨的至少一种第vib族金属的混合物,所述载体包含氧化铝、二氧化硅、二氧化硅-氧化铝、氧化镁、粘土或这些矿物的至少两种的混合物。
30.根据本发明,轻馏分回收区可在大于5巴的压力下运行。
31.在根据本发明的方法中,步骤a)中的所述加氢处理区可产生蒸气流出物,并且所述蒸气流出物可使用例如膜被进一步分离成烃富集物流和氢气富集物流;并且所述烃富集物流可此后与所述回收的轻馏分物流混合,并可将所述氢气富集物流以及所述烃富集物流和所述回收的轻馏分物流的混合物分别送至所述制氢区。
32.在根据本发明的方法中,在步骤c)或d)中产生的所述氢气物流的一部分可用于在所述加氢处理区外的加氢处理。
33.在根据本发明的方法中,尤其根据本发明的第一个目的/实施方案,在将过量氢气级联到加氢处理区之前,可将来自制氢区的所述氢气的至少一部分送至异构化步骤,并且气体汽提的液体流出物可在所述异构化步骤中被进一步处理以制造中间馏分油烃燃料。
34.在根据本发明的方法中,所述轻质烃汽提介质可以是包含甲烷、乙烷、天然气、燃料气体、脱乙烷塔轻质产物、脱甲烷塔轻质产物、获自另一可再生来源的物流,例如来自生物质热解单元或来自气体消化器单元或来自废物和/或塑料热解单元或来自处理可再生原料的任何其它单元的轻质气体或其混合物的物流。
35.在根据本发明的方法中,所述加氢处理区可包括加氢精制步骤和异构化步骤和/或所述二次加氢处理区可包括异构化步骤。
36.在根据本发明的方法中,所述加氢处理区可包括加氢精制步骤和异构化步骤和/或所述二次加氢处理区包括异构化步骤,且所述异构化步骤可使用至少一种不同于所述固体催化剂的固体异构化催化剂。
37.在根据本发明的方法包括上文提到的异构化步骤的情况下,可用的固体异构化催
化剂尤其包含含有选自钯(pd)和铂(pt)的至少一种金属的异构化功能物质,和包含沸石、氧化铝、二氧化硅、二氧化硅-氧化铝、氧化镁、粘土的载体。
38.在根据本发明的方法包括上文提到的异构化步骤的情况下,可用的固体异构化催化剂尤其包含在载体上的异构化功能物质,所述异构化功能物质包含选自钼和钨的至少一种第vib族金属、选自镍和钴的至少一种第viii族金属、或选自钼和钨的至少一种第vib族金属和选自镍和钴的至少一种第viii族金属的组合,所述载体包含沸石、氧化铝、二氧化硅、二氧化硅-氧化铝、氧化镁、粘土和这些矿物的至少两种的混合物。
39.在根据本发明的方法中,加氢处理区和/或二次加氢处理区可包括加氢精制步骤和异构化步骤,且所述异构化步骤优选在0.1至10 h-1
的lhsv下运行。
40.在本发明的方法中,所述加氢处理区可包括加氢精制步骤和异构化步骤,并且在所述加氢精制步骤和所述异构化步骤之间可存在级间分离步骤,将轻质气体与所述中间馏分油烃燃料分离。
41.回收的轻馏分物流在进料至所述制氢区之前可与附加进料物流混合。
42.回收的轻馏分物流在进料至所述制氢区之前可与附加进料物流混合,并且所述附加进料物流可由供应所述轻质烃汽提介质的相同来源供应,或所述附加进料物流可由与所述轻质烃汽提介质不同的来源供应。
43.根据本发明,轻馏分回收区可进一步包括胺吸收步骤以除去酸性气体。
44.根据本发明,所述轻馏分回收区可进一步包含吸附剂以除去组分如h2o、h2s、co2、轻硫烃(light sulfur hydrocarbon)或它们的任何组合。
45.根据本发明,生物原料可选自:菜籽油、大豆油、玉米油、椰子油、橄榄油、亚麻籽油、葵花油、棕榈油、麻风树油、芥子油、花生油、大麻油、棉籽油、猪肉脂肪、家禽脂肪、猪油、黄油、牛脂或它们的任何组合。
46.尤其根据本发明的第二个目的/实施方案,所述轻馏分分离区除所述lpg物流和所述轻质残余气体物流外还可产生包含比正丁烷重的石脑油范围烃的液体产物物流。
47.尤其根据本发明的第三个目的/实施方案,此后可利用选自溶解气体除去和/或液体产物分馏的一种或多种方法进一步处理所述二次加氢处理液体流出物物流以制造中间馏分油烃燃料。
48.尤其根据本发明的第三个目的/实施方案,所述轻馏分回收区可包括溶解气体除去步骤,在使加氢处理液体流出物与轻质烃汽提介质接触后,将轻质气体与所述中间馏分油烃燃料分离。
49.根据本发明,所述生物原料可以是与石油烃原料的混合物或与其共同进料,并且石油烃原料可与所述生物原料共同处理。任选地,石油烃原料选自lco轻循环油、柴油、煤油、hcgo、lcgo、vgo或热解油或它们的任何组合。
附图说明
50.图1显示申请人的在将生物原料转化成中间馏分油范围烃的方法的过程中高效和有效利用轻馏分物流的新方法的示意图。
51.发明详述图1显示申请人的在将生物原料转化成中间馏分油范围烃燃料的方法的过程中高
效和有效利用轻馏分物流的新方法的示意图。
52.本文所用的“加氢精制”是指烃原料与氢气之间的化学反应,包括加氢脱氮、加氢脱硫、加氢脱氧、氢解和烯烃饱和;这一术语在本文中也用于包括脱羧和脱羰,因为这些反应在给定反应条件下同时作为氢解的竞争反应发生。
53.本文所用的“加氢处理区”是指其中当与催化剂床接触时在烃原料与氢气之间发生加氢精制和/或加氢处理反应的区域。加氢处理区除一个或多个催化剂床外还可包括以下一种或多种:在一个或多个催化剂床下游分离一个或多个液体物流和一个或多个蒸气物流、再循环气体回路、一个或多个再循环液体回路、用于除去硫化氢和/或二氧化碳的胺分离。此外,加氢处理区还可包括使用不同催化剂的异构化和/或加氢裂化步骤以促进链烷烃的异构化/加氢裂化。
54.本文所用的“中间馏分油”是指通常主要由沸点高于150℃的烃组分构成的烃燃料,包括例如煤油、柴油或瓦斯油。
55.本文所用的“生物原料”是指植物油、动物脂肪、妥尔油和衍生材料,如脂肪酸烷基酯,或其组合。植物油包括,但不限于,菜籽油、大豆油、玉米油、椰子油、橄榄油、亚麻籽油、葵花油、棕榈油、麻风树油、芥子油、花生油、大麻油和棉籽油。动物脂肪包括,但不限于,猪肉脂肪、家禽脂肪、猪油、黄油和牛脂。
56.本文所用的术语轻馏分或轻质烃是指比戊烷轻的化学化合物,包括甲烷、乙烷、丙烷、正丁烷或异丁烷。这样的轻质烃或“轻馏分”通常作为原料和/或作为燃料用于一些烃处理方案。
57.本文所用的lhsv是液时空速,其是每小时的液体体积流量与催化剂体积的比率。具有2 m3/h的流量和1m3催化剂的系统具有2的lhsv。(单位是1/hr)。lhsv与停留时间成反比。
58.将经预处理的生物原料物流11与来自制氢区15的氢气物流16一起进料至加氢处理区17。制氢区15通常是利用烃进料物流化学生产氢气的区段。
59.尽管未显示,但经预处理的生物原料物流可与另一相容的进料,尤其是石油来源的进料,如lco轻循环油、柴油、煤油、hcgo、lcgo、vgo或热解油或它们的任何组合一起处理,只要如本领域技术人员所知对设计做出一些调整。尤其根据共同处理的进料的量,除用于保护制氢单元的普通硫防护装置(sulfur guard)外,本发明还有可能包括脱硫步骤,如在轻馏分回收段中的胺处理或硫捕集吸附剂。实际上,smr或其它技术中所用的催化剂需要低h2s进料量。经预处理的生物原料含量可为总进料的100重量%至50重量%,优选99重量%至60重量%,更优选95重量%至60重量%,更优选为总进料的93重量%至80重量%。这些范围最适于能够使用更具体在生物原料的加氢精制过程中产生的丙烷。
60.但是,在相容进料的加氢处理产生大量轻馏分的本发明的一个实施方案中,可能感兴趣的是共同处理多于50%的共同进料和最多90%。这种实施方案的一个实例是相容进料是vgo沸程烃且加氢处理区包括加氢裂化催化剂。如本领域中已知,烃组分的加氢裂化处理产生显著量的轻馏分烃组分。本发明的这种实施方案随后能够回收这些轻馏分组分以在制氢中补充生物衍生的丙烷。
61.尽管未显示,但其利用“氢气发生步骤”,如蒸汽甲烷重整(smr)、自热重整或部分氧化。此区域通常包括在氢气发生步骤上游的硫防护装置和在氢气发生步骤下游的氢气纯
化步骤。另外,氢气纯化步骤通常使用变压吸附(psa),但也可使用其它手段,如胺吸收、甲烷化等。尽管申请人在本说明书中提到蒸汽重整,但本领域技术人员已知的任何制氢技术都可用于相同的目的。
62.在加氢精制步骤中,加入来自氢气物流16的氢以使来自生物原料11的不饱和植物油甘油三酯的双键饱和和除去丙烷主链,由此将饱和植物油甘油三酯转化成脂肪酸。最后,脂肪酸发生加氢脱氧(通过加入更多的氢,氧作为h2o离开)或脱羧(氧作为co2离开,没有进一步加入氢),或这两者的组合。结果获得包含链烷烃的混合物和轻馏分的液体加氢处理流出物物流18。在加氢处理区17中的这种加氢精制步骤利用固体催化剂催化加氢精制反应。
63.本领域中已知的催化剂通常使用第viii族金属,如镍或钴,其独自或与第vib族金属,如钼或钨组合。本领域众所周知的催化剂类型是在氧化铝载体上的nimo、como和niw的硫化形式,以及还原镍。根据具体的生物原料,该反应通常在通常180℃至400℃的反应温度、10巴至150巴的压力和0.1至10 h-1
的lhsv下运行。
64.加氢处理区17也可包括在已发生加氢精制反应后,能使直链链烷烃发生烷烃异构化和裂化的催化剂。异构化/裂化催化剂可存在于独立于加氢精制反应的阶段中或与加氢精制反应共用同一个阶段。在加氢处理区17包括异构化/加氢裂化步骤的这些情况下,加氢处理流出物物流18包含来自异构化/加氢裂化步骤的液体流出物。
65.加氢处理区17可包括能将一个或多个反应器中的过量氢气和/或液体流出物再循环回一个或多个反应容器的设备。加氢处理区也可使用如胺吸收或膜分离之类的技术从反应器流出物中选择性分离二氧化碳。
66.包含链烷烃的混合物的液体加氢处理流出物物流18此后与轻质烃汽提介质10a一起进料至轻馏分回收区19。轻馏分回收区可利用单级接触器,但通常使用具有多级的单个容器,如蒸馏塔。
67.申请人的发明中的轻馏分回收区19在高压下运行,且如下文详细解释,用于从加氢处理反应器液体流出物中除去丙烷的轻质烃汽提介质10a也适合并用作制氢区的进料。轻质烃汽提介质10a通常是主要由轻质烃,如甲烷或天然气组成的蒸气物流。
68.尽管未显示在图1中,但也可能的是,轻质烃汽提介质获自另一可再生来源,例如来自生物质热解单元或来自气体消化器单元或来自废物和/或塑料热解单元或来自处理可再生原料的任何其它单元的轻质气体。
69.使用相同的轻质烃汽提介质作为制氢区15的进料物流是有利的,因为其必须以适中的压力存在以进入制氢系统,如蒸汽重整器。
70.因此使用其作为轻馏分回收区19中的汽提介质能使其在高压下运行。
71.丙烷——加氢精制反应的主要副产物,是多种制氢方法的合适原料。通过利用轻馏分回收区,在加氢处理区中产生的轻馏分,即丙烷能够用于制氢;这允许至少部分由可再生原料制氢,并减少必须从其它来源输入的原料量。
72.加氢处理液体流出物物流18在轻馏分回收区19中被分离成回收的轻馏分蒸气物流20和气体汽提的液体流出物物流22。回收的轻馏分物流20通常包含丙烷、在加氢处理区17中产生的其它轻馏分和轻质烃汽提介质10a中的组分。
73.气体汽提的液体流出物物流22通常包含链烷烃并且此后适合通过本领域技术人员已知的许多方法进一步处理成可出售产品,包括柴油燃料、煤油、喷气燃料、瓦斯油和/或
石脑油。气体汽提的液体流出物物流22也可含有来自轻质烃回收区的溶解的轻馏分;当分离时,这些轻馏分在进一步处理后可用作燃料气体。
74.制氢区15通常包括硫防护装置、蒸汽重整器和变压吸附(psa)段(都未显示)。包含氢气和其它轻馏分的加氢处理区排出物流14任选在硫防护装置、蒸汽重整器或psa的上游被送至制氢区15。如果被送至蒸汽重整器上游,可将加氢处理区排出物流14中的烃转化成氢气。或者,如果不需要转化该物流中的轻馏分,可将加氢处理区排出物流14送至psa;这在一些情况下可能更合意,因为该物流通常富含氢气。
75.如上文提到,使用相同的轻质烃汽提介质10a作为制氢区15的进料物流带来处理效率。图1显示这种实施方案,其中轻质烃进料物流10用作轻质烃汽提介质10a和制氢区进料物流10b。制氢进料物流10b此后与回收的轻馏分物流20合并,并且合并的物流12用作燃料并被送至制氢区15。
76.通常,制氢区15的进料(天然气或其它)需要压缩以进入该装置。在这种情况下,经压缩的进料可用作如上所述的汽提介质,但通过用低压轻馏分进料物流10a气体在低压下运行轻馏分回收区19、然后将回收的轻馏分物流20级联到压缩步骤,也有可能实现类似的效果;这允许回收的轻馏分物流20和制氢区进料物流10b共用压缩设备。
77.尽管未显示在图1中,但也可能的是,气体汽提的液体流出物物流22可首先与氢气物流16一起被送至异构化或加氢裂化步骤以产生中间馏分油燃料并且其中在异构化或加氢裂化方法中未利用的过量氢气此后被级联到加氢处理区17。
78.尽管未显示并且取决于特定装置的规格,但制氢进料物流10b和轻质烃汽提介质10a可来自分开的来源。此外并且尽管也未显示,但制氢进料物流10b和回收的轻馏分物流20可在分开的物流中被送至制氢区15。
79.在一些应用中,可能有价值的是作为可出售液体产品回收所述回收的轻馏分物流20的丙烷组分。在这种情况下并且尽管未显示在图1中,回收的轻馏分物流20可被送至液化石油气(lpg)回收段。
[0080]“液化石油气或lpg”通常由丙烷、丁烷或其混合物组成。lpg回收段可利用膜、分馏或它们的一些组合回收丙烷。在这一步骤中,从回收的轻馏分物流20中除去液体可出售丙烷或lpg。包含轻质气体,如甲烷和/或乙烷的剩余回收的轻馏分物流20此后可用作蒸汽重整器的进料或用作燃料。
[0081]
已经就具体实施方案和应用公开了本文所述的发明。但是,这些细节无意作为限制,并且根据这一教导,其它实施方案是本领域技术人员显而易见的。因此要理解的是,附图和说明书例示本发明的原理,并且不应被解释为限制其范围。
[0082]
具体实施方式:通过以下实施例进一步描述本发明,其不应被解释为限制本发明的范围。
[0083]
在根据图1的单元中处理由大豆油组成的经预处理的生物原料物流11以及来自制氢区15的氢气物流16。制氢区15是蒸汽甲烷重整(smr)单元。
[0084]
这种进料的相关性质列在下表1中:表1
来源单位标准经预处理的大豆油比重d15/4 d4052/d12980.923
脂肪酸组成 nfeniso12966.2+nfeniso5508 c14:0重量% 0.5c14:1重量% 0.0c15:0重量% 0.0c16:0重量% 10.0c16:1重量% 0.0c17:0重量% 0.0c17:1重量% 0.0c18:0重量% 4.0c18:1重量% 23.0c18:2重量% 53.0c18:3重量% 8.0c20:0重量% 0.5c20:1重量% 0.5c22:0重量% 0.0c22:1重量% 0.5甘油酯组成 nfeniso12966.2+nfeniso5508 游离脂肪酸重量% 0.5甘油单酯重量% 0.0甘油二酯重量% 0.0甘油三酯重量% 99.5脂肪酸甲酯重量% 0.0总计重量% 100.0硫fx或uv重量ppmd2622/d545310总氮重量ppmd4629/d576220磷重量ppmd51853金属重量ppmd51855
[0085]
在加氢精制步骤中,加入氢以使来自生物原料11的不饱和植物油甘油三酯的双键饱和和除去丙烷主链,由此将饱和植物油甘油三酯转化成脂肪酸。最后,脂肪酸发生加氢脱氧(通过加入更多的氢,氧作为h2o离开)或脱羧(氧作为co2离开,没有进一步加入氢),或这两者的组合。结果获得包含链烷烃的混合物和轻馏分的液体加氢处理流出物物流18。
[0086]
在加氢处理区17中的这种加氢精制步骤利用在氧化铝载体上的硫化nimo催化剂。该催化剂包含4重量%镍和14重量%钼。
[0087]
下表2显示加氢精制单元的操作条件:表2
操作条件根据本发明使用丙烷高压排出的现有技术使用丙烷低压排出的现有技术反应器压力
ꢀꢀꢀꢀꢀꢀꢀꢀꢀꢀꢀꢀꢀꢀꢀꢀꢀꢀꢀꢀꢀꢀꢀꢀꢀꢀꢀꢀ
mpa10.610.610.6wabt(hdo/hdt)
ꢀꢀꢀꢀꢀꢀꢀꢀꢀꢀꢀꢀꢀꢀꢀꢀ
℃340343343hdo/hdt催化剂lhsv
ꢀꢀꢀꢀꢀꢀꢀ
h-1
0.250.250.25
[0088]
加氢处理区17不包括从反应器流出物中任何选择性分离二氧化碳。
[0089]
将包含链烷烃的混合物的液体加氢处理流出物物流18此后与轻质烃汽提介质10a
一起进料至轻馏分回收区19。轻馏分回收区利用在高压(3 mpa)下运行的蒸馏塔,并且用于从加氢处理反应器液体流出物中除去丙烷的轻质烃汽提介质10a用作制氢区的进料。轻质烃汽提介质10a是由具有下表3中所示的组成的轻质烃组成的蒸气物流。
[0090]
表3。
[0091]
加氢处理液体流出物物流18在轻馏分回收区19中被分离成回收的轻馏分蒸气物流20和气体汽提的液体流出物物流22。回收的轻馏分物流20包含丙烷、在加氢处理区17中产生的其它轻馏分和轻质烃汽提介质10a的组分。
[0092]
下表4显示根据本发明和根据现有技术的产物收率:表4。
[0093]
丙烷随轻馏分从回收区被送至smr单元。这允许至少部分由可再生原料制氢,并相应地减少smr单元的输入原料。在现有技术方案中排出到smr的来自加氢处理段的氢气需要smr的额外燃料消耗和水力容量(hydraulic capacity)而没有有利地有助于制氢;大量氢气排出到smr因此代表该方法的显著低效性。确实,根据表4,从加氢处理段排出到smr的h2减少50重量%,并且能够回收丙烷并将其输送到smr而没有额外压缩。以这种方式,提出的本发明能够提供高压和低压丙烷除去的优点,而没有招致任一选项的严重低效性。这可粗略地通过“等效h2节省”量化,其代表送至smr的丙烷的化学计量制氢能力与排出到smr和损失到燃料中的h2总和之间的差值。
[0094]
鉴于上述情况,根据本发明的处理方案更高效并利用在中间馏分油的制造中由生物原料的加氢处理生成的丙烷。