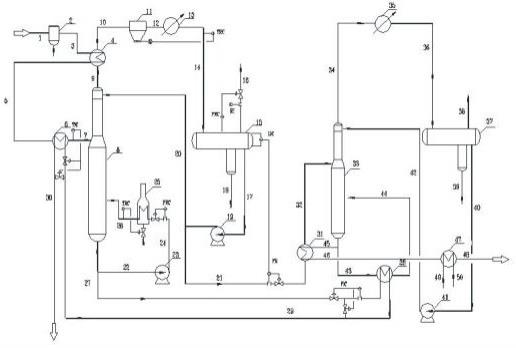
一种连续重整装置预加氢处理后的石脑油分馏工艺
1.技术领域
2.本发明涉及一种连续重整装置预加氢处理后的石脑油分馏工艺,特别是一种降低精制石脑油中的水含量,且提升汽提塔的稳定性;同时优化换热流程,通过回收利用汽提塔顶热量、塔底产物作拔头油分馏塔底热源的方式降低装置能耗,提升装置经济效益的工艺。
背景技术:
3.重整装置的原料馏程和杂质含量一般达不到重整原料油的要求指标,需要通过预处理进行原料的精制和分馏,以脱除其中的硫、氮、砷、铅、铜等有害杂质和轻组分。
4.预处理单元中的分馏部分,经常采用汽提塔和拔头油分馏塔工艺设计,该设计中汽提塔将汽提与分馏轻组分的功能合二为一,汽提塔底产精制石脑油,塔顶含硫轻石脑油进拔头油分馏塔分离出不含硫的轻石脑油。该设计由于汽提塔既要脱水又要分馏,原料的波动对汽提塔的操作稳定性存在较大影响,可能导致精制石脑油的水含量超标,进而降低重整催化剂的活性和寿命。
5.专利cn205528614u公开了一种改善柴油含水量的柴油真空脱水系统,在汽提塔后采用真空脱水系统对汽提塔底产出的柴油进行真空脱水,从而得到符合国家标准的柴油产品,但此法需要增加一套真空脱水系统(含柴油脱水塔、柴油分水罐、冷凝器、水环真空泵、柴油泵、冷凝液泵、聚结器)。本发明通过将聚结器放置在汽提塔进料前,通过降低进料中游离水的含量,再利用汽提塔本身的精馏脱除剩余的游离水和溶解水,可在不增设真空脱水系统(脱水塔、分水罐、冷凝器、水环真空泵、泵、冷凝液泵)的情况下同样使产品水含量达标,从而节省大量设备投资。
技术实现要素:
6.本发明的目的是针对现有技术采用汽提塔和拔头油分馏塔流程分离预加氢产物后,汽提塔底产出的精制石脑油中的水含量超标,汽提塔顶部热量没有回收利用,且汽提塔底部热量没有充分利用等问题,而提供一种优化的连续重整装置预加氢处理后的石脑油分馏工艺,从而降低精制石脑油中的水含量,提升汽提塔的稳定性;同时优化换热流程,降低装置能耗。
7.本发明提供一种连续重整装置预加氢处理后的石脑油分馏工艺,其特征在于包括下述步骤:1)连续重整装置预加氢处理后的石脑油进入聚结器脱除游离水,作为汽提塔进料,依次与汽提塔顶气和汽提塔底液换热,升温后,优选升温到130~180度后,进入汽提塔进行汽提;2)汽提塔汽提后,汽提塔顶气与汽提塔进料换热,再经冷凝冷却,之后进入汽提塔回流罐,汽提塔回流罐中的含硫化氢气体抽出进行脱硫处理,汽提塔回流罐罐底出来的含硫污
水,送至污水处理装置,汽提塔回流罐中液相自罐底抽出,经升压后,大部分物流作为回流返回汽提塔,其它物流与拔头油分馏塔的拔头油分馏塔底物流换热后,送至拔头油分馏塔,汽提塔底液为精制石脑油,大部分升压加热后返回汽提塔作为热源,其余依次与拔头油分馏塔底物流、汽提塔进料换热后抽出装置;3)步骤2)拔头油分馏塔的拔头油分馏塔顶气冷凝冷却后,进入拔头油分馏塔回流罐,拔头油分馏塔回流罐中气相抽出进行脱硫处理,拔头油分馏塔回流罐罐底出来的含硫污水,送至污水处理装置,拔头油分馏塔回流罐中液相从罐底抽出,升压后返回拔头油分馏塔塔顶,拔头油分馏塔塔底物流大部分与汽提塔的汽提塔底液换热,再加热后作为热源,其余与汽提塔回流罐中液相换热冷却后送出装置。
8.本发明所述一种连续重整装置预加氢处理后的石脑油分馏工艺,其进一步技术特征在于:所述汽提塔回流罐中液相自罐底抽出,经升压后,大部分物流作为回流返回汽提塔,其它物流进入拔头油分馏塔进料/塔底换热器的壳程与拔头油分馏塔的拔头油分馏塔底物流换热。
9.本发明所述一种连续重整装置预加氢处理后的石脑油分馏工艺,其进一步技术特征在于:所述汽提塔的汽提塔底液为精制石脑油,其中100~300重量%的物流,以汽提塔进料为基准,通过汽提塔重沸炉泵升压,经汽提塔重沸炉加热后返回汽提塔作为热源。优选进入汽提塔重沸炉加热的物流,以加热至30%~70%物流汽化为基准。
10.本发明所述一种连续重整装置预加氢处理后的石脑油分馏工艺,其进一步技术特征在于:所述汽提塔塔顶操作压力为0.9~1.3mpag,塔顶操作温度为90~130℃,回流比为0.1~0.5,以进料重量为基准;所述拔头油分馏塔塔顶操作压力为1.3~1.8 mpag,塔顶操作温度为36~66℃,回流比为0.1~0.5,以进料重量为基准。
11.本发明所述一种连续重整装置预加氢处理后的石脑油分馏工艺,其进一步技术特征在于:所述拔头油分馏塔塔底物流中200~600重量%的物流,以拔头油分馏塔进料为基准,与汽提塔的汽提塔底液换热,再加热后作为热源,优选拔头油分馏塔塔底物流被加热至15~30%物流汽化,之后返回拔头油分馏塔作为热源。
12.本发明所述一种连续重整装置预加氢处理后的石脑油分馏工艺,主要用于连续重整装置,其与现有技术相比的优点是:1)通过对进料的过滤、聚结、沉降、分离,从而降低和稳定汽提塔进料的水含量,同时消除进料中的水含量波动对汽提塔脱水的影响,再通过汽提塔的精馏脱除剩余的游离水和溶解水,降低汽提塔底精制石脑油水含量超标的风险。
13.2)充分利用汽提塔顶物料潜热,减少塔顶空冷器负荷,提升汽提塔进料温度,降低塔底加热炉负荷和燃料气消耗,从而降低装置能耗。
14.3)通过汽提塔产物替代1.0 mpa蒸汽作为拔头油分馏塔底热源,节约1.0 mpa蒸汽,降低装置能耗。
15.4)增加控制方案,使得汽提塔顶压力、进料温度、回流比和塔底重沸炉返回温度均实现稳定控制,汽提塔操作稳定性相应提升。
16.下面用附图和具体实施方式对本发明做进一步的详细说明,但并不限制本发明的范围。
附图说明
17.图1为本发明一种连续重整装置预加氢处理后的石脑油分馏工艺的流程示意图。
18.图中所示附图标记为:1.管线,2.聚结器,3.管线,4.汽提塔进料/塔顶换热器,5.管线, 6.汽提塔进料/塔底换热器,7.管线,8.汽提塔,9.管线,10.管线,11.汽提塔顶空冷器,12.管线,13. 汽提塔顶后冷器,14.管线,15.汽提塔回流罐, 16.管线,17.管线,18.管线,19.汽提塔回流泵, 20.管线,21.管线,22.管线,23.汽提塔重沸炉泵,24.管线,25. 汽提塔重沸炉,26.管线,27.管线,28.拔头油分馏塔重沸器,29.管线,30.管线, 31.拔头油分馏塔进料/塔底换热器,32.管线,33.拔头油分馏塔, 34.管线,35. 拔头油分馏塔空冷器,36 .管线,37.拔头油分馏塔回流罐,38.管线,39.管线,40.管线,41.拔头油分馏塔回流泵,42.管线,43.管线,44.管线,45.管线,46.管线,47.产物冷却器,48.管线,49.管线,50.管线。
具体实施方式
19.如图1所示,连续重整装置预加氢处理后的石脑油通过管线1进入聚结器2,脱除游离水后,经过管线3进入汽提塔进料/塔顶换热器4与汽提塔8的汽提塔顶气换热,之后经管线5进入汽提塔进料/塔底换热器6与汽提塔8的汽提塔底液换热,升温到130~180度后进入汽提塔8。
20.所述汽提塔8的汽提塔顶气中含有轻组分、硫化氢和微量水,依次经管线9进入汽提塔进料/塔顶换热器4换热,经管线10进入汽提塔顶空冷器11冷却,再经管线12进入汽提塔顶后冷器13冷凝冷却,之后经管线14进入汽提塔回流罐15,含硫化氢的气体在压力控制下经管线16可送至脱硫装置;罐底出来的含硫污水经管线18抽出,可送至酸性水汽提装置,液相自罐底经管线17抽出,经汽提塔回流泵19升压后,大部分物流在流量控制下作为回流经管线20返回汽提塔8,其它物流在回流罐液位和流量串级控制下经过管线21进入拔头油分馏塔进料/塔底换热器31的壳程与拔头油分馏塔33的拔头油分馏塔底物流换热,之后经管线32送至拔头油分馏塔33。汽提塔8的塔底物为精制石脑油,大部分(通常是100~300重量%的物流,以汽提塔进料为基准)经管线22通过汽提塔重沸炉泵23升压,在流量控制下经管线24通过汽提塔重沸炉25加热至30%~70%汽化后返回汽提塔8作为热源,其余经管线27通过拔头油分馏塔重沸器28、汽提塔进料/塔底换热器6管程分别与拔头油分馏塔底产物、汽提塔进料换热后经管线30可送往重整及再接触部分作为进料。
21.所述汽提塔塔顶操作压力为0.9~1.3mpag,塔顶操作温度为90~130℃,回流比(以进料重量为基准)为0.1~0.5。
22.所述拔头油分馏塔塔顶操作压力为1.3~1.8 mpag,塔顶操作温度为36~66℃,回流比(以进料重量为基准)为0.1~0.5。
23.拔头油分馏塔33的拔头油分馏塔顶气经管线34通过拔头油分馏塔空冷器35冷凝冷却后,经管线36进入拔头油分馏塔回流罐37,拔头油分馏塔回流罐37中气相在压力控制下经管线38可送至脱硫装置;拔头油分馏塔回流罐37罐底出来的含硫污水经管线39抽出,含硫污水可送至酸性水汽提装置,拔头油分馏塔回流罐37中液相从罐底抽出,经管线40通过拔头油分馏塔回流泵41升压,之后作为回流经管线42返回拔头油分馏塔33塔顶,拔头油分馏塔33塔底物流大部分(通常是200~600重量%的物流,以拔头油分馏塔进料为基准)经
管线43通过拔头油分馏塔重沸器28与汽提塔8的塔底物换热,被加热至15~30%汽化后经管线44返回拔头油分馏塔33作为热源,其余在拔头油分馏塔釜液位和流量串级控制下,经管线45通过拔头油分馏塔进料/塔底换热器31管程换热,之后经管线46再进入产物冷却器47冷却后经管线48送出装置。
24.本发明通过对进料的过滤、聚结、沉降、分离,从而降低和稳定汽提塔进料的水含量,同时消除进料中的水含量波动对汽提塔脱水的影响,再通过汽提塔的精馏脱除剩余的游离水和溶解水,降低汽提塔底精制石脑油水含量超标的风险;同时本发明可以充分利用汽提塔顶物料潜热,减少塔顶空冷器负荷,提升汽提塔进料温度,降低塔底加热炉负荷和燃料气消耗,使用汽提塔产物替代1.0 mpa蒸汽作为拔头油分馏塔底热源,从而降低装置能耗。