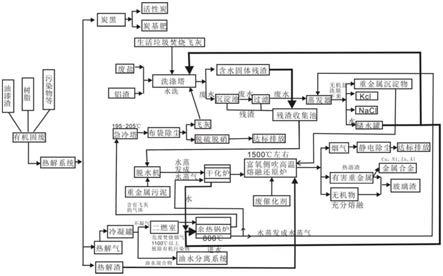
1.本实用新型涉及有机废物综合处理、回收、再利用技术领域,具体提供一种有机废物综合处理、回收、再利用生产线。
背景技术:
2.随着人们对废物无害化处理方法的深入研究,衍生出很多废弃物有效处理方法,对于有机废物,常见的处理方法为热解法,通过热解产生热解气、炭黑等进行二次利用,以达到资源化处理的目的。
3.针对电镀污泥,由于电镀污泥中含有cu、ni、cr、zn、fe等重金属,上海绿澄环保科技有限公司(一种利用高温熔融技术处理特定污染物的方法201510834230.2)研制出了一种利用高温熔融技术处理特定污染物的方法,通过对电镀污泥进行预处理
‑‑
配料、混料和造粒
‑‑
熔融,得到金属合金及玻璃态熔渣。
4.针对垃圾焚烧飞灰,光大环境科技(中国)有限公司研发出了一种垃圾焚烧飞灰等离子熔融处理系统(申请号201610996840.7),包括依次连接的进料装置、等离子熔融炉、二燃室、急冷塔、活性炭喷射装置、布袋除尘器、盐酸发生器、湿法洗涤塔、蒸汽加热器和引风机。根据本发明,可以将列为危险废物的垃圾焚烧飞灰熔融,转化成无毒无害的玻璃体以及盐酸,最大程度地实现垃圾焚烧飞灰的减量化、无害化以及资源化。
5.除了上述方法处理焚烧飞灰外,江苏天楹环保能源成套设备有限公司研发出了一种结合水洗和等离子体熔融处理焚烧飞灰系统,通过将飞灰进行水洗,水洗后废水经过沉淀、过滤和蒸发制得kcl、nacl和重金属沉淀物,飞灰作为经过等离子体技术处理后得到的玻璃体,该方法飞灰处理整条线做到完全的闭合,不需要考虑由二次污染的问题。
6.对于有机固废中的油漆渣、树脂、污染物等,公司之前采用热解方法(一种农、林及高热值有机废弃物热解气化炉202120413917x)进行处理,通过热解回收热解气,以达到资源化处理的目的。
7.但有机废物的类型及种类繁多,对于油漆渣、树脂、污染物、废盐、生活垃圾焚烧飞灰、铝渣、重金属污泥等,目前还没有一套综合处理线能综合处理,分批处理太浪费财力、人力及物力,设备多占地空间大,处理过程中会产生二次垃圾或二次污染,因此急需研制一套有机废物综合处理、回收、再利用生产线以使更多的废物能综合处理并利用,进一步减少更多的设备投入、减少投入成本、减少单独处理时能耗高等问题,达到资源综合回收率高、能耗更少的目的。
技术实现要素:
8.为了解决上述问题,本实用新型提供一种多种废弃物能协同处理,节约投入资金,节省人力、财力,处理过程能达到资源最大化、无害化、资源化处理目的的有机废物综合处理、回收、再利用生产线。
9.本实用新型的技术方案是:
10.一种有机废物综合处理、回收、再利用生产线,包括热解系统、高温熔融系统、废气处理系统及水洗系统;
11.所述热解系统包括依次连接的热解装置、冷凝罐、二燃室、引风机、余热锅炉;
12.所述高温熔融系统包括依次设置的脱水机、干化炉、富氧侧吹高温熔融还原炉;
13.所述废气处理系统包括依次连接的急冷塔、布袋除尘装置、脱硫脱硝装置;
14.所述水洗系统包括依次连接的洗涤塔、沉淀池、过滤池、蒸发器、储水罐;
15.进一步,所述余热锅炉包括相互套设的外壳及内腔室,所述外壳及内腔室之间为余热回收腔,所述二燃室的出气口通过管道、引风机连通余热回收腔的进气端,所述余热回收腔的出气端通过管道连通急冷塔的进气端;
16.所述急冷塔的出气端通过管道连通布袋除尘装置,所述布袋除尘装置上设有废气排放口及废物排放口,所述布袋除尘装置的废气排放口通过管道连通脱硫脱硝装置,所述脱硫脱硝装置连通排放烟筒;从所述布袋除尘装置的废物排放口出来的飞灰通过上料机送入到洗涤塔内;
17.所述洗涤塔的顶部设有进水口,所述储水罐通过出水管连接洗涤塔的进水口,出水管上设有泵及阀门;
18.进一步,所述洗涤塔连接废水排放管及废物排放管,所述废水排放管连接沉淀池的进水口,废水排入所述沉淀池内,所述沉淀池的出水口通过管道连通过滤池的进水口;所述蒸发器包括加热室和蒸发室,所述过滤池的出水口通过管道连通蒸发室,所述余热锅炉及干化炉之间的热蒸汽管道上连接分支管道,所述分支管道的另一端连通蒸发器的加热室,所述蒸发室上设有重金属沉淀物出口、盐类排出口,所述加热室底部连接有出水管,出水管的另一端连通储水罐;
19.重金属沉淀物出口连接脱水机的进料口,脱水机的出料口对准干化炉的进料口,干化炉的出料口对准富氧侧吹高温熔融还原炉;
20.进一步,所述干化炉包括相互套设的导热污泥筒和外筒,所述外筒与导热污泥筒之间为高温气体腔,所述干化筒上设有入料口、出料口、进气口和出气口,导热污泥筒内用于放置重金属污泥及后期水洗系统产生的、经脱水机脱水后的含水固体残渣;所述余热锅炉的内腔室通过热蒸汽管道连通高温气体腔,水蒸气通所述过热蒸汽管道及进气口进入到高温气体腔内,水蒸气用于重金属污泥及含水固体残渣的干化处理;
21.所述内腔室的一端设有进水口,所述储水罐通过管道连通内腔室的进水口,所述管道上设有阀门及泵,所述内腔室的顶部连接热蒸汽管道,进入到所述余热回收腔后用于对内腔室内的水进行加热,水经加热蒸发成水蒸气;
22.进一步,所述外筒底部连接出水管,所述出水管另一端连接储水罐或/及余热锅炉的进水口;
23.进一步,所述导热污泥筒内设有与筒体同轴的转轴,所述转轴由外部变频电机控制;
24.进一步,从所述余热锅炉至干化炉方向,所述热蒸汽管道上依次设有除湿器、鼓风机;
25.进一步,所述富氧侧吹高温熔融还原炉上设有进料口、出气口、有害重金属出料口、虹吸口;所述干化炉的出料口对准富氧侧吹高温熔融还原炉的进料口;经脱水机脱水后
的物料通过进料装置送到干化炉的导热污泥筒内,导热污泥筒内的物料通过进料装置输送到富氧侧吹高温熔融还原炉内;
26.上述有机废物的综合处理方法,包括如下步骤:
27.首先,将有机废物送进热解装置内,装满后,关闭炉门,打开燃烧器开始加温,在450度左右状态下,有机废物的组分开始逐渐热解转换成汽相,并在650℃左右稳定,高温状态下有机废物被热解其产物包括炭黑、热解渣、热解气,热解气进入所述冷凝罐得到可凝气(即油水混合物)和不凝气,不凝气为可燃气体,油水混合物进入后续油水分离系统得到热解油和热解水,可燃气体进入二燃室用于燃烧供热,焚烧温度不低于1100度,炉内烟气停留时间大于2s,产生烟气。有机热解燃烧烟气在所述引风机作用下,进入所述余热锅炉回收余热;
28.进一步,从所述余热锅炉回收余热后的烟气进入急冷塔,烟气经急冷后进入所述布袋除尘装置,烟气经布袋除尘装置处理产生飞灰及废气,废气进入脱硫脱硝装置处理后达标排放,飞灰通过上料机送入到洗涤塔内;
29.将废盐、铝渣、生活垃圾焚烧飞灰以及废气处理系统过程产生飞灰按一定比例投入到洗涤塔中,所述洗涤塔内的物料经过混合、水洗产生废水及含水固体残渣,上述物料依次经过洗涤塔水洗、沉淀池沉淀、过滤池过滤、过滤出一部分含水固体残渣,剩余废水进入到所述蒸发器内经蒸发,生成重金属沉淀物、kcl、nacl、水;
30.进一步,废盐、铝渣、生活垃圾焚烧飞灰以及废气处理系统过程产生飞灰投入比为1:2:4:1;
31.进一步,根据氯化钾和氯化钠的溶解度不同,先在55℃左右获得氯化钾结晶盐,然后继续升温在100℃左右获得氯化钠结晶盐,最终的产物为重金属沉淀物、kcl、nacl、水,重金属沉淀物从重金属沉淀物出口出来后期投放进所述富氧侧吹高温熔融还原炉内,kcl、nacl用于回收外售,水进入到所述储水罐收集。
32.水排入所述储水罐后,所述储水罐内的水一部分加入到余热锅炉的内腔室内,一部分用于所述水洗塔内水洗过程;
33.将水洗系统中沉淀、过滤、蒸发过程产生的含水固体残渣一同收集同重金属污泥一同加入到脱水机内脱水,使水含量降至70%
‑
80%,然后将上述物料通过进料装置送到干化炉的导热污泥筒内,使物料含水率降至20%
‑
30%;
34.干化过程为:向干化炉的高温气体腔内通入热蒸汽,热蒸汽来源于余热锅炉,余热锅炉为双层结构,余热锅炉的内腔室内有水,从二燃室焚烧后的烟气进入到余热锅炉的余热回收腔用于加热水;
35.最后,导热污泥筒内的物料经干化同废催化剂、热解过程中产生的热解渣、水洗系统过程产出的重金属沉淀物按一定比例通过进料装置输送到富氧侧吹高温熔融还原炉内;在高温情况下有机物被降解,所有的有机物完全熔融分解,有害重金属均匀分布在所述富氧侧吹高温熔融还原炉中,熔融玻璃液从所述富氧侧吹高温熔融还原炉下部的玻璃渣出口连续溢流出炉外,经冷却获得玻璃渣。所有被固化在玻璃体当中的重金属无法渗出,从而达到灰渣去毒化的效果;回收的有害重金属通过所述富氧侧吹高温熔融下部的金属渣出口排出炉外,经冷却获得金属合金,烟气通过静电除尘后可以达标排放。
36.进一步,所述富氧侧吹高温熔融还原炉内的温度大于1500摄氏度;
37.进一步,热解过程中产生的高品质炭黑制备活性炭,低品质炭黑做炭基肥材料。热解渣通过后期进入所述富氧侧吹高温熔融还原炉中用于制备玻璃体或生产重金属,无机物通过熔融、冷却后用于制备玻璃体外售;
38.进一步,热解气进入到二燃室后,在高温作用下,热解气中的的co和ch4彻底被氧化,进一步除去二噁英;
39.从所述二燃室出来的热气温度大于800℃;
40.进一步,废催化剂、热解过程中产生的热解渣、干化过程中的产物、水洗系统过程产出的重金属沉淀物的比例为1:1:9:3;
41.进一步,废催化剂为石油炼制废催化剂,废催化剂具体为化工生产和石油炼制过程中加氢脱硫、加氢脱氮、加氢脱重金属、加氢精制、加氢裂化、加氢脱芳烃、选择性加氢裂化、催化重整等工艺过程产生的废催化剂。
42.进一步,有机废物包括油漆渣、树脂、污染物;
43.进一步,有机废物的类型包括:hw08(废矿物油与含矿物油废物)、hw12(染料、涂料废物;油漆渣)、hw13(有机树脂类废物)、hw49(沾染废弃物,抹布、手套、棉纱等);
44.入料前控制以下参数:干基硫(s)含量<1%,干基氯(cl)含量<1%,干基溴(br)含量<1%,干基氮(n)含量<3%;
45.进一步,本发明中,用于供气的管道上设有动力装置,动力装置包括引风机;
46.进一步,本发明中,用于供水的管道上设有动力装置,动力装置包括阀门及泵;
47.进一步,所述洗涤塔连接的废物排放管底端设有残渣收集池,
48.进一步,所述过滤池上设有排渣口,排渣口通过管道连通残渣收集池;
49.进一步,所述沉淀池上设有排渣口,排渣口通过管道连通残渣收集池;
50.进一步,所述残渣收集池内的残渣通过上料装置被投入到脱水机内;
51.进一步,盐类排出口连通盐类收集罐;
52.进一步,所述干化炉、富氧侧吹高温熔融还原炉之间设有制团机,重金属污泥、飞灰水洗系统的炉渣经干化阶段(含水率20%以下)后,在所述制团机内制团,水分控制在10%以下,制团块度在50mm
‑
200mm之间,制团后的块团采用自然干燥,含h2o≤5%,然后再入所述富氧侧吹高温熔融还原炉。
53.有益效果:
54.本发明不但能实现有机废物的资源化、无害化处理,还能协同其他废物,包括废盐、生活垃圾焚烧飞灰、铝渣、重金属污泥等,一同进行资源化、无害化处理,因此避免了废物单独处理造成的浪费财力、人力及物力,设备多占地空间大,处理过程中会产生二次垃圾或二次污染等问题,本发明能做到废物最大化资源化、无害化处理的目的。
55.本有机废物综合处理方法及处理生产线为一个闭合的流程,该生产线中所产生的热解渣用于生产玻璃体,热解气经余热锅炉回收热量后再进行回收飞灰,热量回收过程节约了能源,实现了资源化利用的目的,经回收热量后通过急冷,避免了二噁英这样的有害气体的再次产生,急冷后通过布袋除尘回收飞灰,而废气通过脱硫脱硝后进行达标排放,进一步,为了避免飞灰中的氯在高温段挥发,在低温出口处冷凝而堵塞下游设备,进一步避免腐蚀问题,我们将飞灰协同废盐、生活垃圾焚烧飞灰、铝渣一同进行水洗处理,不但实现了除氯、废物处理的目的,且废盐有利于更多的kcl、nacl的产出,铝渣有利于后期在富氧侧吹高
温熔融还原炉内生成玻璃体(玻璃体需要硅、钙、铝,铝渣提供更多的铝),飞灰及生活垃圾焚烧飞灰为后续生成玻璃体提供更多的钙、硅、铝,重金属污泥为后期生成玻璃体提供更多的硅,因此玻璃体生成量高,避免了因硅、钙、铝不足造成的玻璃体产量低会有二次污染物生成的问题。在水洗后生成了金属沉淀物、kcl、nacl、水,kcl、nacl被回收外售,水会循环使用,水进入余热锅炉,经二燃室出来的热气加热蒸发生成水蒸气,水蒸气一部分用于干化,一部分用于蒸发器蒸发,因此达到了资源最大化利用的目的,将水洗过程产生的残渣、协同金属污泥一同投入脱水机脱水后进入到干化炉内干化后再放入富氧侧吹高温熔融还原炉内,避免了湿度太大的物料在富氧侧吹高温熔融还原炉损耗更多的燃料且处理过程更长;上述过程回收了热解气的余热,达到了节约资源的目的,将蒸发器产出的重金属沉淀物协同废催化剂、干化后的物料、热解渣一同投入到富氧侧吹高温熔融还原炉内,在高温作用下,有机物被降解,烟气通过静电除尘后可以达标排放,无机物充分熔融冷却后变成玻璃体回收外售,一部分有害重金属被固化在玻璃体当中的重金属无法渗出,从而达到灰渣去毒化的效果;回收的有害重金属通过所述富氧侧吹高温熔融下部的金属渣出口排出炉外,经冷却获得金属合金回收外售。本发明为一个闭环的过程,处理过程不产生二次废物及二次污染。通过本发明,玻璃体产量可增加40%。进一步,上述过程中热解渣中的重金属也能回收利用,其余的不能回收利用的被定在玻璃体内不会造成二次污染且回收利用了。
56.在洗涤塔底端设置了残渣收集池,将洗涤塔、过滤池、沉淀池产生的废渣一同收进残渣收集池内便于后期将所有废渣一起投入到脱水机内;
57.由于在外筒底部设置了出水管,所以经冷却后生成的水能回收到储水罐或余热锅炉内回收利用,节约了资源。
58.由于在导热污泥筒内设有与筒体同轴的转轴,转轴由外部变频电机控制,通过转动导热污泥筒有利于加快干化速度。
59.由于在热蒸汽管道上设置了除湿器及鼓风机,经除湿后的热气更有利于干化过程;
60.由于在干化炉及富氧侧吹高温熔融还原炉之间设置了制团机,更加有利于物料的干燥,更干燥的物料进入富氧侧吹高温熔融还原炉内使得后期反应更快更节约燃料,并且通过制团,便于后期玻璃体成型。
61.本技术中的储水罐内的水为循环利用的过程,因此节约了水资源。
附图说明
62.图1是本实用新型有机废物综合处理、回收、再利用生产线示意图;
63.图2是余热锅炉及干化炉示意图;
64.图中:
65.1、余热锅炉
ꢀꢀꢀꢀꢀꢀꢀꢀꢀꢀꢀꢀ
2、干化炉
ꢀꢀꢀꢀꢀꢀꢀꢀꢀ
3、急冷塔
66.4、蒸发器
ꢀꢀꢀꢀꢀꢀꢀꢀꢀꢀꢀꢀꢀꢀ
5、储水罐
ꢀꢀꢀꢀꢀꢀꢀꢀꢀ
6、二燃室
[0067]1‑
1、外壳
ꢀꢀꢀꢀꢀꢀꢀꢀꢀꢀꢀꢀꢀꢀ1‑
2、余热回收腔
ꢀꢀꢀ1‑
3、内腔室
[0068]2‑
1、外筒
ꢀꢀꢀꢀꢀꢀꢀꢀꢀꢀꢀꢀꢀꢀ2‑
2、高温气体腔
ꢀꢀꢀ2‑
3、导热污泥筒
[0069]
7、热蒸汽管道
ꢀꢀꢀꢀꢀꢀꢀꢀꢀꢀ
8、分支管道
具体实施方式
[0070]
本实施例一种有机废物综合处理、回收、再利用生产线,包括热解系统、高温熔融系统、废气处理系统及水洗系统;
[0071]
所述热解系统包括依次连接的热解装置、冷凝罐、二燃室6、引风机、余热锅炉1;
[0072]
所述高温熔融系统包括依次设置的脱水机、干化炉2、富氧侧吹高温熔融还原炉;
[0073]
所述废气处理系统包括依次连接的急冷塔3、布袋除尘装置、脱硫脱硝装置;
[0074]
所述水洗系统包括依次连接的洗涤塔、沉淀池、过滤池、蒸发器4、储水罐5;
[0075]
本废物综合处理线工作过程如下:
[0076]
有机废物包括油漆渣、树脂、污染物;
[0077]
具体包括:hw08(废矿物油与含矿物油废物)、hw12(染料、涂料废物;油漆渣)、hw13(有机树脂类废物)、hw49(沾染废弃物,抹布、手套、棉纱等);
[0078]
进一步,hw08、hw12、hw13、hw49的投入比为3.5:4:1:1.5;
[0079]
通过上述比例控制干基硫(s)含量<1%,干基氯(cl)含量<1%,干基溴(br)含量<1%,干基氮(n)含量<3%;
[0080]
将上述有机废物按一定比例送进热解装置内,装满后,关闭炉门,打开燃烧器开始加温,在450度左右状态下,有机废物的组分开始逐渐热解转换成汽相,并在650℃左右稳定,高温状态下有机废物被热解其产物包括炭黑、热解渣、热解气,热解气进入冷凝罐得到可凝气(即油水混合物)和不凝气,不凝气为可燃气体,油水混合物进入后续油水分离系统得到热解油和热解水,上述用于回收利用,可燃气体进入二燃室6用于燃烧供热,焚烧温度不低于1100度,炉内烟气停留时间大于2s,产生烟气。有机热解燃烧烟气在引风机作用下,进入余热锅炉1回收余热;
[0081]
进一步,上述热解过程中产生的高品质炭黑制备活性炭,低品质炭黑做炭基肥材料。热解渣进入富氧侧吹高温熔融还原炉,还原得到金属,从炉底虹吸口排出外售,无机物通过熔融、冷却后用于制备玻璃体外售。
[0082]
进一步,热解渣投入到所述富氧侧吹高温熔融还原炉中用于制备玻璃体或生产重金属;
[0083]
所述二燃室6内温度不低于1100度,热解气在高温下将烟气中的co、ch4等彻底氧化,因此除去了有害二噁英气体。
[0084]
为避免二噁英的再次生成且达到资源化利用的目的,从二燃室6的顶部排出的烟气,先进入到所述余热锅炉1的余热回收腔1
‑
2内用于加热内腔室1
‑
3内的水,通过高温作用,水经加热蒸发成水蒸气,而利用过的烟气通过管道进入到所述急冷塔3,并在所述急冷塔3内迅速降温至180℃~200℃,因此避免了二噁英的再次生成。
[0085]
随后,经急冷塔3急冷后的烟气进入到布袋除尘器内,所述布袋除尘器吸收烟气中可能再次形成的微量二噁英,与此同时所有的二次飞灰(包括被烟气携带的没有被熔融的飞灰、挥发的盐等)将被所述布袋除尘器中的袋式过滤器捕获,二次飞灰一般可能占投入飞灰的10%,所有的二次飞灰用于投入后续的洗涤塔中,而所述布袋除尘过程产生的气体通过所述脱硫脱硝装置处理后进行达标排放。
[0086]
进一步,飞灰、废盐、铝渣、生活垃圾飞灰中过高的氯含量在高温段挥发,然后在低温出口处冷凝而堵塞下游设备,会引起设备停产。并且,这样的腐蚀问题同样会出现在飞灰
熔融处理过程中,因此对焚烧飞灰进行预处理除氯,我们将飞灰投入到湿式所述洗涤塔进行后续处理。处理过程如下:
[0087]
将废盐、铝渣、生活垃圾焚烧飞灰以及所述废气处理系统过程产生飞灰按一定比例同时投入到洗涤塔内,从所述储水罐5内抽水到洗涤塔内并对其内部的物料进行水洗处理,经水洗处理后,产生上清液及含水固体残渣,上清液废水被排入到所述沉淀池内,并依次经过所述沉淀池、过滤池、蒸发器4,进一步,由所述洗涤塔水洗产生的废水通过沉淀、过滤,过滤出一部分含水固体残渣,剩余废水进入蒸发器4内,蒸发器4的热气由余热锅炉1提供,热气从余热锅炉1至热蒸汽管道7、分支管道8再进入到蒸发器内,蒸发器4根据不同的蒸发溶液进行温度调节,根据氯化钾和氯化钠的溶解度不同,先在55℃左右获得氯化钾结晶盐,然后继续升温在100℃左右获得氯化钠结晶盐,最后产生重金属沉淀物、kcl、nacl、水,重金属沉淀物从重金属沉淀物出口出来投放进所述富氧侧吹高温熔融还原炉内,kcl、nacl用于回收利用外售,水进入到储水罐5收集,储水罐5内的水一部分加入到余热锅炉1的内腔室1
‑
3内,一部分用于水洗塔内水洗过程;
[0088]
进一步,废盐、铝渣、生活垃圾焚烧飞灰以及废气处理系统过程产生飞灰投入比为1:2:4:1;
[0089]
进一步,上述沉淀、过滤过程中也产生了一部分残渣,残渣均通过管道进入到所述残渣收集池,以便后续同蒸发过程产出的含水固体残渣一同送入脱水机中进行脱水处理。
[0090]
将重金属污泥及所述水洗系统产生的含水固体残渣一同放入到所述脱水机内脱水,脱水后,进入到所述干化炉2的导热污泥筒2
‑
3内,所述余热锅炉1包括相互套设的外壳1
‑
1及内腔室1
‑
3,所述外壳1
‑
1及内腔室1
‑
3之间为余热回收腔1
‑
2,所述干化炉2包括相互套设的导热污泥筒2
‑
3和外筒2
‑
1,所述外筒2
‑
1与导热污泥筒2
‑
3之间为高温气体腔2
‑
2,所述余热锅炉1的内腔室1
‑
3通过热蒸汽管道7连通高温气体腔2
‑
2,水蒸气通所述过热蒸汽管道7及进气口进入到干化炉2的高温气体腔2
‑
2内,水蒸气用于重金属污泥及含水固体残渣的烘干处理;所述导热污泥筒2
‑
3内的重金属污泥及含水固体残渣被水蒸气烘干干化后,通过进料装置输送到富氧侧吹高温熔融还原炉内;
[0091]
进一步,所述富氧侧吹高温熔融还原炉内的温度大于1500摄氏度;将废催化剂、热解过程中产生的热解渣、干化过程中的产物、水洗系统过程产出的重金属沉淀物按一定比例投入到富氧侧吹高温熔融还原炉内;
[0092]
进一步,废催化剂包括加氢脱硫、加氢脱氮、加氢脱重金属、加氢精制、加氢裂化、加氢脱芳烃混合物。
[0093]
进一步,废催化剂、热解过程中产生的热解渣、干化过程中的产物、水洗系统过程产出的重金属沉淀物的加入比例为1:1:9:3;
[0094]
在高温情况下有机物被降解,所有的有机物完全熔融分解,有害重金属均匀分布在所述富氧侧吹高温熔融还原炉中,熔融玻璃液从所述富氧侧吹高温熔融还原炉下部的玻璃渣出口连续溢流出炉外,经冷却获得玻璃渣。所有被固化在玻璃体当中的重金属无法渗出,从而达到灰渣去毒化的效果;回收的有害重金属通过所述富氧侧吹高温熔融下部的金属渣出口排出炉外,经冷却获得金属合金,烟气通过静电除尘后可以达标排放。
[0095]
通过本发明,一年的处理量为hw08(废矿物油与含矿物油废物)7000吨/年,hw12(染料、涂料废物;油漆渣)8000吨/年,hw13(有机树脂类废物)2000吨/年,hw49(沾染废弃
物,抹布、手套、棉纱等)3000吨/年;
[0096]
通过本发明,一年可产玻璃体55000吨,金属合金7000吨,玻璃体产量比传统产量增加了42.5%。
[0097]
进一步,上述过程中所述蒸发器4蒸发出重金属沉淀物、kcl、nacl、水的原理在专利申请号201710305558.4,专利名称一种结合水洗和等离子体熔融处理焚烧飞灰系统中有披露,因此本处就不再赘述。
[0098]
富氧侧吹高温熔融还原炉集合了富氧熔炼炉及富氧侧吹炉两种功能,采用富氧熔炼炉与富氧侧吹炉连接,富氧侧吹炉采用上海和惠生态环境科技有限生产的应用于飞灰熔融的富氧侧吹炉(专利号201911350797.7),富氧熔炼炉采用上海和惠生态环境科技有限生产生产的专利产品。
[0099]
需要说明的是在本实用新型的描述中,需要理解的是,术语“上”、“下”、“前”、“后”、“左”、“右”、“顶”、“底”、“内”、“外”等指示的方位或位置关系为基于附图2所示的方位或位置关系,仅是为了便于描述本实用新型和简化描述,而不是指示或暗示所指的装置或元件必须具有特定的方位、以特定的方位构造和操作,因此不能理解为对本实用新型的限制。
[0100]
以上对本实用新型的一个实施例进行了详细说明,但所述内容仅为本实用新型的较佳实施例,不能被认为用于限定本实用新型的实施范围。凡依本实用新型申请范围所作的均等变化与改进等,均应仍归属于本实用新型的专利涵盖范围之内。