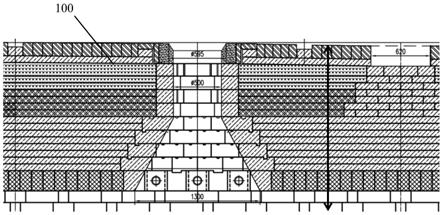
1.本发明属于焦炉节能环保技术领域,具体涉及一种对流散热型焦炉炉顶结构。
背景技术:
2.炼焦生产是炼焦煤在焦炉炭化室内隔绝空气高温干馏的过程,通常炉内温度高达1200-1350℃。由于炼焦生产特点,焦炉炉顶表面温度较高,一般超过70℃,有时高达100℃以上,焦炉炉顶散热约占焦炉总耗热量的8%以上。
3.焦炉有多种型式,包括常规机焦炉、热回收焦炉、半焦(兰炭)炭化炉,其中常规机焦炉占绝大多数,现有焦炉炉顶区的结构,客观造成焦炉炉顶表面温度高,长期生产过程中产生不少负面影响,主要有:一是焦炉炉顶散热量大,炼焦耗热量高,是工业企业节能降耗的重点单元;二是焦炉炉顶区域温度高,岗位人员作业环境差,轮换作业劳动效率低;三是焦炉炉顶区域上升管、护炉铁件等设备长期在高温环境中,纵拉条、横拉条等高温劣化造成焦炉砌体严密性下降,影响焦炉使用寿命;四是焦炉炉顶区域受天气及频繁作业影响砌体损坏,炭化室内荒煤气外逸,造成焦炉无组织排放超标,进一步恶化现场作业环境。
4.国家推动产业结构调整优化,推进产业绿色发展,推进重点行业污染治理升级改造,明确要求重点区域二氧化硫、氮氧化物、颗粒物、挥发性有机物(vocs)全面执行大气污染物特别排放限值,推动实施钢铁等行业超低排放改造,重点区域城市建成区内焦炉实施炉体加罩封闭,并对废气进行收集处理。
5.综上,现有焦炉炉顶区域散热量大,环境温度高,作业环境差、能源浪费大,持续不断的散热,全覆盖式散热面,巨大的散热量,封闭后环境更加恶劣,不仅影响作业人员,甚至绝大多数电气设备都无法承受,当前环境条件下,焦炉炉体加罩封闭基本上没有可能性。
6.焦炉是由耐火砖砌筑而成的用于生产焦炭的热工设备,就顶装焦炉来说,其炉顶区域包括加煤口、看火孔、上升管,与炉内炭化室或燃烧室相连,除此之外的区域(简称隔热耐压层)全部由断热转、漂珠砖等砌筑而成。
7.以当前的主流7米焦炉为例,加煤口底座及加煤口盖、看火孔底座及看火孔盖均为耐热铸件,生产过程中表面温度超过350℃;隔热耐压层100为耐材砌筑实心结构,由上到下共16-18层,分别为1层缸砖+1层粘土砖+3层断热砖+4层漂珠砖+6-8层粘土砖+3层硅砖,参见图1。
8.因炉内温度高达1300℃,虽然耐火材料砌体厚度高达1.485米,也无法避免炉顶区域高温散热问题。炼焦生产过程中,炉顶区域需频繁进行装煤车装煤、上升管系统作业、炉顶维护及加煤口等清扫保养作业。焦炉炉顶温度高,劳动强度大,环境非常恶劣。为改善炉顶作业环境,有些焦炉进行了炉顶翻修,尝试采用一些隔热性能相对较好的耐火材料,实施完成后炉顶面温度明显下降,因炉内持续不断的散热,在较短的时间炉顶区域温度又回升如前,无法根本改变炉顶的作业环境。
9.可以预见的将来,焦炉炉体加罩封闭将成为必然,而实施焦炉炉体加罩封闭,必然要面对封闭空间内焦炉炉体散热、窜漏等带来的巨大风险,这也是焦炉一直以来始终露天
生产,难以安全封闭的根本原因。
技术实现要素:
10.本发明的目的在于提供一种对流散热型焦炉炉顶结构,通过焦炉炉顶区域结构改进,采用绝热复合材料,建立互联互通空气道,有效阻断焦炉炉内热量向炉顶区域的传导,使焦炉炉顶区域散发的热量能快速扩散,实现更低的焦炉炉顶表面温度,更优的炉顶作业环境,更好的护炉铁件及焦炉砌体保护,为焦炉炉体加罩封闭实施奠定基础。
11.为达到上述目的,本发明的技术方案是:
12.一种对流散热型焦炉炉顶结构,焦炉炉顶包括隔热耐压层及其上的上升管、加煤口、看火孔;其包括:所述隔热耐压层自上而下分别设置为缸砖、粘土砖、粘土质空心砖、粘土砖、硅砖;粘土砖与粘土质空心砖通过粘土火泥砌筑,硅砖采用硅火泥砌筑;所述加煤口的底座、看火孔的底座为耐材整体浇筑成型,加煤口盖、看火孔盖为双层结构,上下层间配置可阻断热量传递的隔热毡;绝热型风道,敷设在立火道两侧的横拉条沟下面,与加煤口两侧的空心砖联通,夹层为气凝胶等绝热材料,壳体为轻质绝热板;绝热型风道间连接处为承插结构实现相互间密封,两侧及顶部用浇筑料密封后敷设焦炉炉顶缸砖,底部为断热砖。
13.优选的,所述粘土质空心砖的下部空腔,内置绝热毡,上层空腔为可空气流通的多孔结构。
14.优选的,在焦炉炉顶面下建立绕行上升管底座、加煤口的s型通风道,实现炉顶面下由机侧到焦侧的风道连通。
15.优选的,所述绝热型风道内径由焦侧到机侧逐步增加。
16.优选的,以加煤口为界,每孔炭化室对应的炉顶顶面下设置s型通风道。
17.优选的,每1-10孔炭化室设一个通风单元,机焦侧所述绝热型风道与外界的连接处配置调节插板或翻板。
18.优选的,机焦侧所述绝热型风道与外界风管连接,配置强制通风系统,实现空气由焦侧到机侧的流通,将焦炉炉顶区域热量带走;每个通风单元均配置气体检测系统,检测通风系统内气体温度,送中控远程监控管理。
19.优选的,还配置焦炉炉顶热成像系统,监控炉顶面温度各点变化,包括炉盖、看火孔盖温度异常升高,及时指令焦炉维护人员实施更换处理。
20.优选的,所述绝热材料为气凝胶。
21.优选的,所述隔热耐压层自上而下分别设置为一层缸砖、两层粘土砖、两层粘土质空心砖、八层粘土砖、三层硅砖。
22.根据炼焦生产特点,焦炉炉顶区域功能一是隔热减少炉体散热,二是耐压承受装煤及炉顶辅助作业,三是密封阻断炭化室正压荒煤气逸散。
23.本发明为改变焦炉炉顶区域结构,增加空气绝热层和对流散热层等高效绝热结构,内置通风道、通风及控制,实现焦炉炉顶表面温度的大幅度下降。具体如下:
24.1、高效绝热结构。高效绝热结构由以下几部分构成。
25.①
隔热耐压层自上而下分别设置为缸砖、粘土砖、粘土质空心砖、粘土砖、硅砖,分别通过粘土火泥、断热浇注料、硅火泥砌筑;
26.②
加煤口、看火孔底座为耐材整体浇筑成型,加煤口盖、看火孔盖为双层结构,上
下层间配置隔热毡阻断热量传递;
27.③
粘土质空心砖下部空腔内置绝热毡,上层空腔为多孔通径可空气流通,具有足够的结构强度;
28.④
绝热型风道敷设在立火道两侧的横拉条沟下面,与加煤口两侧的空心砖联通,夹层为气凝胶等绝热材料,壳体为轻质绝热板。
29.⑤
绝热型风道间连接处为承插结构实现相互间密封,两侧及顶部用浇筑料密封后敷设焦炉炉顶缸砖,底部为断热砖。
30.2、内置s型通风道。焦炉炉顶区域包括上升管底座、加煤口、看火孔,按规律相间排列。
31.在炉顶面下,建立绕行上升管底座、加煤口的s型通风道,实现炉顶面下由机侧到焦侧的风道连通;
32.根据焦炉结构特点及表面温度分布,风道内径由焦侧到机侧逐步增加,便于空气流通;以看火孔为界,每孔炭化室为一个相对独立的炉顶内置s型通风道;
33.为便于施工及运行控制,每1-10孔炭化室为一个配风单元,实现不同组间通风量的调整,机焦侧通风道与外界的连接处配置调节插板(或翻板)。
34.3、通风系统运行监控。机焦侧通风道与外界风管连接,配置强制通风系统,实现空气由焦侧到机侧的流通,将焦炉炉顶区域热量带走。每个配风单元均配置气体检测系统,检测通风系统内气体温度,送中控远程监控管理。
35.如第n个配风单元烟温超平均值20℃以上时,远程或的手动开大该单元的风量调整翻板,反之则关小。如平均烟温升高10℃以上时,调整强制通风风机,增加风量。
36.本发明还配置焦炉炉顶热像系统,监控炉顶面温度各点变化。如某炉盖、看火孔盖温度异常升高,及时指令焦炉维护人员实施更换处理。
37.本发明焦炉炉顶结构以粘土质空心砖、绝热型风道、断热浇筑料的组合,替代原粘土砖、断热砖、漂珠砖组成的实心结构,空心砖下部利用空气绝热原理隔热并配置陶瓷纤维棉,上部有多孔通径,与绝热型风道联通后呈s型绕行加煤口,通过强制通风,以空气对流方式快速带走炉体散热。上下层用断热浇筑料施工,既改善炉顶区域密封性能,又提高断热效果。焦炉炉顶加煤口、看火孔采用双层及整体浇筑结构替代原铸件,大幅度减少该部位散热。通过远程监控系统控制系统可靠运行,指导焦炉炉顶面维修,以及焦炉炉顶大小炉盖的更换。
38.本发明与现有技术的区别:
39.本发明为一种高对流散热型焦炉炉顶结构,与当前焦炉炉顶不同的是,本发明所述焦炉炉顶结构上具有空气绝热层和对流散热层,可有效阻断焦炉炉内热量向炉顶区域的传导,可快速扩散焦炉炉顶区域散热,能可靠维持焦炉炉顶区域结构严密,避免焦炉炉顶区域窜漏,指导焦炉炉体维护措施的采取。
40.本发明的有益效果:
41.①
通过粘土质空心砖、绝热型风道及断热浇注料的组合应用,既实现炉内热量的有效隔断,又实现炉内散热的强制通风带走,从而大幅度降低炉顶表面温度;
42.②
通过双层加煤口、看火孔盖及耐材整体浇筑加煤口、看火孔底座,极大的阻断了炉内热量的传递,实现焦炉看火孔、加煤口部位的表面温度大幅度下降;
43.③
通过组合式粘土砖及风道的应用,减少炉顶区耐材缝隙,避免炉内窜漏;
44.④
通过测温、热像等系统的应用,调整系统运行,指导焦炉炉顶面维护及设备更换。
45.⑤
焦炉炉顶面温度降低,可有效改善焦炉炉顶作业环境,减轻高温对横拉条等护炉铁件、装煤车等设备的影响。
附图说明
46.图1为焦炉隔热耐压层的剖面图。
47.图2为本发明实施例的结构示意图。
48.图3为本发明实施例中的结构示意图。
具体实施方式
49.参见图1~图3,本发明所述的对流散热型焦炉炉顶结构,焦炉炉顶200包括隔热耐压层100及其上的上升管、加煤口1、看火孔2;其包括:
50.所述隔热耐压层100自上而下分别设置为缸砖、粘土砖、粘土质空心砖、粘土砖、硅砖;粘土砖与粘土质空心砖通过粘土火泥砌筑,硅砖采用硅火泥砌筑;本实施例中,所述隔热耐压层100自上而下分别设置为一层缸砖、两层粘土砖、两层粘土质空心砖、八层粘土砖、三层硅砖。
51.所述加煤口1的底座、看火孔2的底座为耐材整体浇筑成型,加煤口盖11、看火孔盖21为双层结构,上下层间配置可阻断热量传递的隔热毡;
52.绝热型风道3,敷设在立火道4两侧的横拉条沟5下面,与加煤口1两侧的空心砖联通,夹层为气凝胶等绝热材料,壳体为轻质绝热板;绝热型风道3间连接处为承插结构实现相互间密封,两侧及顶部用浇筑料密封后敷设焦炉炉顶缸砖,底部为断热砖。
53.优选的,所述粘土质空心砖6的下部空腔,内置绝热毡61,上层空腔为可空气流通的多孔结构62。
54.优选的,在焦炉炉顶200顶面下建立绕行上升管底座、加煤口的s型通风道7,实现炉顶面下由机侧到焦侧的绝热型风道3连通。
55.优选的,所述绝热型风道3内径由焦侧到机侧逐步增加。
56.优选的,以加煤口1为界,每孔炭化室对应的炉顶顶面下设置s型通风道7。
57.优选的,每1-10孔炭化室设一个通风单元,机焦侧所述绝热型风道与外界的连接处配置调节插板或翻板8。
58.优选的,机焦侧所述绝热型风道3与外界风管连接,配置强制通风系统9,实现空气由焦侧到机侧的流通,将焦炉炉顶区域热量带走;每个通风单元均配置气体检测系统10,检测通风系统内气体温度,送中控远程监控管理。
59.优选的,还配置焦炉炉顶热成像系统,监控炉顶面温度各点变化,包括炉盖、看火孔盖温度异常升高,及时指令焦炉维护人员实施更换处理。
60.优选的,所述绝热材料为气凝胶。
61.智慧炼焦的是炼焦技术发展的必然趋势,当前炉前、炉顶作业均看到了曙光,但焦炉炉顶面高温及散热,成为焦炉炉顶自动化、无人化的拦路虎,自动化产品普遍无法适应焦
炉炉顶区域的连续、可靠、长周期运行,即将实施的焦炉炉体封闭的前提更是必须降低炉顶面温度,问题突出。应用本发明技术进行焦炉炉顶区域改进,可大幅度降低炉顶面温度,为众多自动化产品的应用带来曙光,推广应用前景十分广阔。