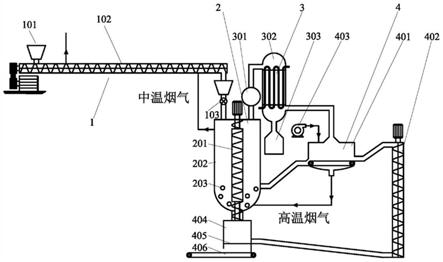
1.本发明属于固体废弃物处置利用领域,更具体地,涉及一种基于热载体双循环供热的废塑料处置系统及方法。
背景技术:
2.塑料因优异的持久性、耐腐蚀、易塑性、稳定性等被广泛应用于社会各行各业,如包装、建筑、汽车、电子电器等。与此同时,由于塑料难以自然降解,随着塑料废弃物产量的急剧增长,诸多环境问题也浮出水面,废塑料回收处理行业面临严峻挑战,因此寻求一种节能、环保、高效的塑料处理工艺方案是必然趋势。
3.现阶段废塑料主要是同生活垃圾一起进入填埋场或焚烧场。然而,传统填埋会污染地下水资源,带来严重的环境问题,且其占用大量土地资源,已逐渐被研究者摒弃。此外,虽然废塑料的热值可高达40mj/kg,几乎与燃油相持平,通过焚烧法可以高效获取其中的能量,然而塑料在燃烧过程中会释放大量氮氧化物、二噁英等污染性气体,造成二次污染,因此加强废塑料的高效回收和合理处置极为重要。
4.相较直接焚烧,由于热解技术可以将废塑料转化为气体、固体、液体等一系列化工燃料和原料,且对不同类型的塑料均具有较好的适应性,热解技术受到国内外研究者的青睐。但在热解的过程中,塑料处于熔融状态,粘度较高,容易粘结在反应器壁面上,引起壁面结焦,这不仅会降低换热效率,导致反应不充分,影响热解装置运行的经济性,同时会引起局部过热,危害热解装置的运行安全。此外,熔融塑料的流动性不佳,且导热性差,这大大增加了输入能耗。同时,针对以聚氯乙烯(pvc)为代表的含氯塑料,在250~300℃的热解过程中会进行脱氯反应,生成诸如hcl等酸性气体,容易对容器产生腐蚀。
技术实现要素:
5.针对现有技术的以上缺陷或改进需求,本发明提供了一种基于热载体双循环供热的废塑料处置系统及方法,其目的在于,解决熔融塑料热解过程中流动性不足、传热差、易结焦沾壁的问题,同时实现系统自维持运行,提高能量利用率。
6.为实现上述目的,按照本发明的一方面,提出了一种基于热载体双循环供热的废塑料处置系统,包括所述核心反应模块用于热解废塑料,包括内循环反应釜以及设置在内循环反应釜内的螺旋杆和热载体,所述螺旋杆用于带动所述热载体从内循环反应釜底部上升到顶部后掉落;
7.所述产物处理模块用于将热解废塑料产生的气相产物分离为液态产物和气态产物;
8.所述热载体循环模块包括球渣分离器、热载体提升装置和燃烧室,其中,所述球渣分离器固定在所述内循环反应釜底部,用于从热解废塑料产生的热解残渣中分离出热载体;所述热载体提升装置用于将球渣分离器分离出的热载体运送至燃烧室;所述燃烧室与所述产物处理模块和内循环反应釜连接,该燃烧室在气态产物的燃烧作用下为热载体供
热,携带热量的热载体回到内循环反应釜中,同时燃烧室中产生的烟气对内循环反应釜外壁腔室进行二次加热。
9.作为进一步优选的,所述热载体为表面具有棱角的近球状体,且热载体表面喷涂有过渡金属元素。
10.作为进一步优选的,所述螺旋杆外设置有套筒,该套筒用于防止热载体上升过程中坠落。
11.作为进一步优选的,所述产物处理模块包括催化提质装置和油气冷凝分离器,所述内循环反应釜、催化提质装置、油气冷凝分离器、燃烧室依次连接;所述催化提质装置用于对气相产物进行原位催化脱氯,所述油气冷凝分离器用于将脱氯后的气相产物分离为液态产物和气态产物,其中液态产物流入油气冷凝分离器下安装的液体收集罐,气态产物进入燃烧室。
12.作为进一步优选的,还包括原料预处理模块,该原料预处理模块包括低温脱氯送料器和控制阀,所述低温脱氯送料器用于将废塑料熔融脱氯,熔融的废塑料通过控制阀进入所述内循环反应釜进行热解;同时,对内循环反应釜外壁腔室进行二次加热后的烟气进入低温脱氯送料器对废塑料进行脱氯。
13.按照本发明的另一方面,提供了一种废塑料处置方法,其采用上述废塑料处置系统实现,包括如下步骤:
14.s1、熔融废塑料在内循环反应釜内热解,生成气相产物和热解残渣;同时热载体不断从内循环反应釜底部通过螺旋杆运至顶部,再落入底部的熔融废塑料中,实现炉内催化热解循环的同时刮除壁面焦炭,避免表面结焦;
15.s2、所述气相产物进入产物处理模块并被分离为液态产物和气态产物,其中气态产物进入燃烧室,燃烧室内的气态产物与外部导入的空气充分混合并燃烧;
16.s3、所述热解残渣进入球渣分离器,球渣分离器将热载体与炉渣分离,分离出的热载体经热载体提升装置进入燃烧室,使热载体吸收气态产物燃烧产生的热量;
17.s4、燃烧室中产生的烟气对内循环反应釜外壁腔室进行二次加热;同时吸收了热量的热载体重新进入内循环反应釜,对熔融废塑料进行催化热解,形成自维持供热系统。
18.作为进一步优选的,所述内循环反应釜内的温度为450℃~500℃。
19.作为进一步优选的,所述燃烧室内温度为600℃~700℃,且燃烧室内过剩空气系数为1.05~1.15。
20.作为进一步优选的,先将干燥粉碎的混合废塑料在低温脱氯送料器中加热到250℃~320℃,得到脱氯后的熔融废塑料,然后对该熔融废塑料进行热解;同时低温脱氯送料器中的热量由对内循环反应釜外壁腔室进行二次加热后产生的烟气提供。
21.作为进一步优选的,所述混合废塑料的粒度为2mm~5mm。
22.总体而言,通过本发明所构思的以上技术方案与现有技术相比,主要具备以下的技术优点:
23.1.本发明针对熔融塑料导热性差、难以流动扩散的问题,设计了热载体内外双循环系统,实现传热强化的能量高效利用;同时利用热解产生的可燃气燃烧后的热量为核心反应模块供热,实现系统自维持运行,有效提高能量利用率,降低成本。
24.2.对于容器壁面易结焦和能耗高这两个问题,均为熔融塑料流动性差的表现之
一,本发明在热解过程中增加传热金属小球作为热载体,通过热载体运动强化熔融塑料流动,增强传热;同时热载体在运动过程中会与容器壁面发生碰撞,可刮除壁面附着物,避免壁面结焦和受热不均,强化换热效果。
25.3.本发明将热载体设计为具有棱角的近球状体,更有利于在热载体内循环过程中将壁面附着焦炭刮落;并进一步在热载体表面喷涂了过渡金属元素,使其具备一定的催化裂解能力,在加强换热的同时可实现热解过程中的原位提质,节省能耗。
26.4.针对热解生成的酸性气体,由于聚氯乙烯(pvc)热解分为200~300℃的脱氯过程和440~580℃的分子链断裂过程,因此本发明增设了低温脱氯送料器对废塑料进行预加热,可提前脱除酸性气体,避免对反应釜壁面造成腐蚀。
附图说明
27.图1为本发明实施例基于热载体双循环供热的废塑料处置系统结构示意图;
28.图2为本发明实施例内循环反应釜内热载体循环示意图。
29.在所有附图中,相同的附图标记用来表示相同的元件或结构,其中:1
‑
原料预处理模块,2
‑
核心反应模块,3
‑
产物处理模块,4
‑
热载体循环模块,101
‑
加料斗,102
‑
低温脱氯送料器,103
‑
控制阀,201
‑
螺旋杆,202
‑
内循环反应釜,203
‑
热载体,204
‑
内循环反应釜盖,205
‑
套筒,301
‑
催化提质装置,302
‑
油气冷凝分离器,303
‑
液体收集罐,401
‑
燃烧室,402
‑
热载体提升装置,403
‑
鼓风机,404
‑
球渣分离器,405
‑
炉渣滤网,406
‑
炉渣传送带。
具体实施方式
30.为了使本发明的目的、技术方案及优点更加清楚明白,以下结合附图及实施例,对本发明进行进一步详细说明。应当理解,此处所描述的具体实施例仅仅用以解释本发明,并不用于限定本发明。此外,下面所描述的本发明各个实施方式中所涉及到的技术特征只要彼此之间未构成冲突就可以相互组合。
31.本发明实施例提供的一种基于热载体双循环供热的废塑料处置系统,如图1所示,包括原料预处理模块1、核心反应模块2、产物处理模块3和热载体循环模块4,其中:
32.原料预处理模块1包括依次连接的加料斗101、低温脱氯送料器102和控制阀103,低温脱氯送料器102用于将废塑料熔融脱氯,熔融的废塑料通过控制阀103进入内循环反应釜202内。
33.核心反应模块2包括内循环反应釜202以及设置在该内循环反应釜202内的螺旋杆201和热载体203,其中,内循环反应釜202上设置有内循环反应釜盖204,螺旋杆201叶片经过粗糙处理,且螺旋杆201外设置有套筒205,当热载体203沉入反应釜的底部后,在螺旋杆201和套筒205的共同作用下提升至反应釜顶部,热载体203重新坠落,实现强化换热作用,如图2所示。优选的,热载体203为表面具有不规则棱角的近球状体,其直径为5mm~10mm,且热载体203表面喷涂有过渡金属元素,优选为ni。
34.产物处理模块3包括催化提质装置301和油气冷凝分离器302,内循环反应釜202、催化提质装置301、油气冷凝分离器302、燃烧室401依次连接,油气冷凝分离器302下接有液体收集罐303,用于收集冷凝的液态产物,气态产物则进入燃烧室401。
35.热载体循环模块4包括鼓风机403、燃烧室401、热载体提升装置402和球渣分离器
404,其中,球渣分离器404与热载体提升装置402相连,热载体提升装置402将球渣分离器404分离出的热载体203运输至燃烧室401;鼓风机403将外界空气导入燃烧室401,促进气态产物的燃烧,为热载体203供热;进而热载体203携带热量进入内循环反应釜202,实现热载体的炉外循环;同时燃烧室401产生的高温烟气引入反应釜外壁腔室进行二次加热,二次加热后的低温烟气进入低温脱氯送料器102对废塑料进行脱氯,从而实现烟气能量梯度利用。
36.采用上述基于热载体双循环供热的废塑料处置系统进行废塑料高效提质一体化处置,包括以下步骤:
37.1)经干燥粉碎后的混合废塑料,在低温脱氯送料器102中加热到250℃~320℃熔融,以去除其中大多数的卤素;
38.2)步骤1)中产生的熔融状态的废塑料通过控制阀103送入内循环反应釜202内,同时表面载有催化剂的热载体203从热解炉顶部落入粘稠熔融塑料中,实现直接接触式传热和原位催化反应,将塑料高效催化热解,生成热解高温气相产物和热解残渣;
39.3)步骤2)中所涉及的热载体203沉入热解炉的底部后,再由螺旋杆201运至反应釜顶部,对热载体进行二次加热,提升后的小球重新坠落,实现炉内催化热解循环的同时刮除壁面焦炭,避免表面结焦;
40.4)步骤2)中所涉及的热解高温气相产物进入催化提质装置301进行原位催化脱氯;
41.5)步骤4)产生的气相产物进入油气冷凝分离器302,分离成液态产物和气态产物,其中液态产物流入液体收集罐303;
42.6)步骤5)分离的气态产物进入燃烧室401,与鼓风机403导入的空气进行充分混合并燃烧;
43.7)步骤2)产生的热解残渣进入球渣分离器404,将热载体203与炉渣分离;
44.8)步骤7)分离的热载体进入热载体提升装置402,将热载体送入燃烧室401,充分吸收热量;
45.9)步骤8)的热载体重新进入内循环反应釜202,对熔融塑料进行高效催化热解,形成自维持供热系统,并刮除壁面焦炭,避免壁面结焦;
46.10)步骤8)产生的高温烟气进入内循环反应釜202外腔进行二次加热;二次加热后的烟气进入低温脱氯送料器102。
47.进一步的,步骤1)中的混合废塑料粒度为2mm~5mm。
48.进一步的,低温脱氯送料器102的温度为250℃~320℃,送料速度为10g/s~12g/s。
49.进一步的,内循环反应釜202内的温度为450℃~500℃。
50.进一步的,燃烧室401内壁面温度为600℃~700℃,通过调整鼓风机403风量维持燃烧室401内过剩空气系数在1.05~1.15,保证完全燃烧。
51.以下为具体实施例:
52.粒度为2mm~5mm的废塑料进入温度为300℃低温脱氯送料器,脱除主要成分为hcl的酸性气体;剩余原料进入内循环反应釜内进行热解反应,内循环反应釜内的温度为480℃;表面载有ni催化剂的热载体(al2o3)从热解炉顶部落入粘稠熔融塑料中,实现直接接触式传热和原位催化反应,将塑料高效催化热解;当热载体沉入热解炉的底部后,再由螺旋杆
运至反应釜顶部,提升后的小球重新坠落,实现强化换热,装置的连续运行可重复实现以上过程;由于热载体的不规则形式,在坠落过程中可将壁面焦炭刮除;在反应结束后炉渣及热载体由内循环反应釜底部出料口引出并分离,反应过程中产生的气相产物进入油气冷凝分离器;气相产物经冷凝后分离出热解油和热解气,热解油用于生产化工产品或提质为燃料油,热解气则进入燃烧室为预处理和热载体供热,燃烧室内温度为600℃;调整鼓风机风量维持燃烧室内过剩空气系数为1.05,保证热解气能够完全燃烧。热载体从固相混合物中分离,经由热载体提升装置提升后送入燃烧室内加热;当热载体温度达到550℃后,送入至内循环反应釜内进行传热。相比传统的热解工艺,采用该热载体能量利用率可提高20%,产生经济效益约60万元,直接减少碳排放共约250吨。
53.本领域的技术人员容易理解,以上所述仅为本发明的较佳实施例而已,并不用以限制本发明,凡在本发明的精神和原则之内所作的任何修改、等同替换和改进等,均应包含在本发明的保护范围之内。