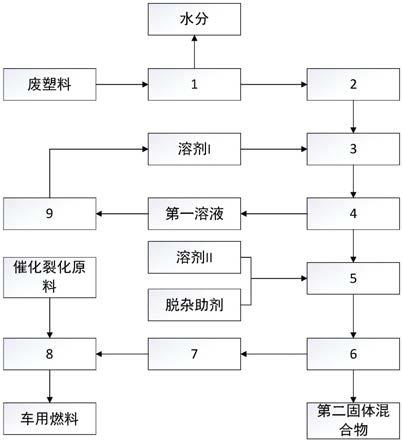
1.本发明涉及固体废塑料处理技术领域,具体涉及一种废塑料制备车用燃料的方法及系统。
背景技术:
2.据统计,我国现有废塑料总量约10亿吨左右并以4000万吨/年的速度逐渐递增。预计到2035年,全球约产生80亿吨左右废塑料。废塑料占城市生活垃圾的15%以上,以北京六里屯垃圾填埋场为例,其占地27公顷,现有填埋量约1200万吨,其中废塑料约200万吨。这不仅造成了严重的环境污染,甚至影响了自然环境中的生态平衡;同时也是对石化资源的严重浪费。现有的废塑料处理技术主要有填埋、焚烧、物理回收和化学回收等几种方式,其中由于废塑料分解速度慢,堆积密度低,导致填埋并不能从本质上解决问题,且易污染地下水资源;而焚烧则易造成严重的大气污染;由于现有废塑料物理回收工艺成本高,经济价值低,企业获利不足导致废塑料物理回收发展较慢。
3.废塑料化学转化是实现废塑料快速回收和转化的有效手段,特别是热塑性废塑料通过热解工艺能得到油品和气体,因此,热解工艺是目前废塑料化学转化的主要工艺路径之一。
4.cn106635115b公开了一种利用混合废塑料垃圾高效清洁制油的方法及水热反应系统,所述方法包括在温度为160~300℃及压力为20~220bar的条件下,使用碱性水溶液对混合废塑料垃圾进行热水解处理;所述混合废塑料垃圾含pe、pp、ps中的一种或几种,及pet,选择性的该混合废塑料垃圾还可包括pvc;将水热处理后的物料中的水相与固相进行分离,将分离得到的固相进行制油。本发明不仅避免了混合废塑料中的pet、pvc对油品质的不利影响,能高效清洁制油,还可产生高附加值的产品,例如ta粉末或颗粒,ps再生塑料。
5.cn108456328a公开了一种废塑料的处理方法,包括:将废塑料、改性催化剂、反应溶剂加入到催化裂解反应器中混合均匀,然后进行催化裂解反应,其特征在于:所述的改性催化剂为改性剂氧化物改性的hzsm-5和hy复合型分子筛催化剂,改性剂选自sn、fe、ti和zn中的一种或多种,所述的反应溶剂为四氢化萘和正十六烷的混合物,所述的催化裂解反应条件如下:反应温度为150-300℃,反应时间为120-240分钟,反应在搅拌下进行,搅拌速率为600-1000转/分钟,反应中通入氢气,氢分压为4-7mpa。
6.cn102786980b公开了一种废塑料炼油生产方法及其生产线,所述方法包括以下步骤:1)废塑料预处理;2)裂解反应;3)催化反应;4)冷凝;5)过滤脱水,通过本方法对废旧塑料进行油化处理,出油率高,出渣率低;所述生产线包括上料装置、高频电加热反应釜、催化塔、冷却过滤罐、冷却液化塔和储油罐,上料装置与高频电加热反应釜连接,高频电加热反应釜与催化塔通过管道连接,催化塔与冷却过滤罐通过管道连接,冷却过滤罐与冷却液化塔通过管道连接,冷却液化塔与储油罐通过管道连接。
7.由于废塑料组成复杂,本身含有大量的杂原子;在塑料生产过程中也会添加大量有机或无机的各类添加剂以提高塑料性能;塑料在丢弃过程中易粘连大量的杂质等原因,
现有技术的热解工艺主要存在的问题是热解油品质不达标,特别是其中cl、si杂质含量高。热解油中的cl主要来自于废塑料中的pvc分解,多为小分子有机氯,在后续的油品加工过程中易分解形成hcl而造成严重的腐蚀。现有技术中针对热解油脱氯主要采用碱性物质中和,但这一方面产生了大量的固废,另一方面使pvc最终转化成nacl、cacl2等无机盐,本质上降低了其价值。热解油中的si主要来自于硅油、硅树脂、硅橡胶粉末等高分子添加剂的分解以及sio2等无机添加剂,主要为烷基环氧硅烷,是后续加工工艺催化剂的毒物,会导致催化剂永久性失活。
技术实现要素:
8.本发明是为了解决现有技术中所得废塑料热解油中有害元素cl、si杂质含量高,导致后续工艺过程管线和设备易腐蚀、催化剂易失活的问题。
9.为实现上述目的,本发明一方面提供了一种废塑料生产车用燃料的方法,包括以下步骤:
10.(1)废塑料和溶剂i进入废塑料第一脱杂单元中,在25~120℃温度下,进行充分混合溶解,溶解后物料经分离单元i,分离为第一溶液和第一固体混合物,所述溶剂i选自四氢呋喃、酮类溶剂、氯化脂肪烃中的一种或几种;
11.(2)第一固体混合物进入废塑料第二脱杂单元,在溶剂ii、脱杂助剂的作用下,在200~450℃温度下进行脱杂反应,反应后物料经分离单元ii,分离为第二溶液和第二固体混合物,所述第二溶液中,氯含量为小于3μg/g,硅含量为小于3μg/g;
12.(3)第二溶液和任选的催化裂化原料进入催化裂化单元,与催化裂化催化剂接触,进行催化裂化反应,经分离至少得到气体、汽油馏分、柴油馏分。
13.在优选的情况下,本发明所述废塑料为新鲜生活垃圾中废塑料、工农业生产中废塑料、陈化垃圾中废塑料中的一种或几种,也可以是上述废塑料初步加工形成的废塑料棒、废塑料粒、废塑料片等中的一种或几种,优选无法物理回收再生的品质较差废塑料,废塑料的种类为pe、pp、ps、pvc中的一种或多种。
14.在优选的情况下,废塑料在进入废塑料第一脱杂单元前进行清洗、干燥和破碎,破碎后的废塑料粒度为1-200mm,进一步优选为1-50mm。
15.在优选的情况下,本发明在废塑料第一脱杂单元中,溶剂i与废塑料的重量比例为1:10~10:1。
16.在优选的情况下,本发明在废塑料第一脱杂单元中,所述溶剂i为四氢呋喃与酮类溶剂以任意重量比例组成的混合溶剂,所述酮类溶剂选自甲乙酮、甲基异丁基酮、环己酮、异佛尔酮中一种或几种。
17.进一步优选,所述酮类溶剂选自甲乙酮、环己酮中一种或几种;更优选为甲乙酮
18.在优选的情况下,所述溶剂i为四氢呋喃与酮类溶剂以1:3~3:1重量比例组成的混合溶剂。进一步优选,所述溶剂i为四氢呋喃与酮类溶剂以1:2~2:1重量比例组成的混合溶剂。
19.在优选的情况下,步骤(1)废塑料第一脱杂单元中,在50~100℃温度下,废塑料在溶剂i中充分混合溶解;优选废塑料的停留时间为30~60min。
20.本发明在步骤(1)中采用溶剂i对混合废塑料进行选择性溶解,将混合废塑料中含
氯塑料溶解到溶液中。当混合废塑料中含有聚苯乙烯,在本发明步骤(1)中,含氯塑料和聚苯乙烯会一起溶解在溶剂i中。本发明优选的溶剂i对含氯塑料的溶解效果好,溶解效率高。
21.在本发明中,所述含氯塑料是指聚氯乙烯、聚偏二氯乙烯及其共聚物中的一种或几种。
22.在本发明中,废塑料经过废塑料第一脱杂单元,脱除了废塑料中大部分含氯废塑料,经过分离单元i,分离所得第一固体混合物中氯含量为小于20μg/g。
23.在本发明其中一种优选的实施方式中,步骤(1)中设置溶剂回收单元,第一溶液进入溶剂回收单元,经选自反萃取、简单蒸馏、闪蒸、精馏中一种或几种方式后,得到回收的溶剂i和含氯塑料颗粒。
24.在优选的情况下,步骤(1)溶剂回收单元采用反萃取耦合蒸馏的方式,反萃取剂为水,反萃取的温度为70~100℃,蒸馏温度为80~100℃。
25.在本发明其中一种优选的实施方式中,第一溶液进入反萃取装置与反萃取剂水接触后,溶解的含氯塑料以固体颗粒的形式析出,液体部分则是含水的溶剂i。
26.在优选的情况下,反萃取后物料采用过滤的方式进行分离,得到含氯塑料颗粒和含溶剂i的废水。采用的过滤装置为一级或多级串联或并联的压滤机、板框、离心机、螺旋挤压脱溶剂设备中的一种或几种。含溶剂i的废水在溶剂蒸馏装置内经蒸馏处理后,得到水和回收的溶剂i,所得回收的溶剂i可重复使用。
27.在本发明步骤(2)中,第一固体混合物进入废塑料第二脱杂单元,在溶剂ii、脱杂助剂的作用下进行脱杂反应,所述杂质包括有机含硅化合物,金属以及含氯化合物。
28.步骤(2)中,溶剂ii为富含芳烃馏分油,所述富含芳烃馏分油选自石油加工过程、煤热解过程、煤直接液化过程、生物质和/或废塑料热解过程所得液体馏分油的一种或几种。在优选的情况下,溶剂ii的馏程范围为80~540℃;溶剂ii中总芳烃含量高于50质量%,单环芳烃含量高于20质量%;进一步优选溶剂ii中单环芳烃含量高于40质量%。
29.在优选的情况下,步骤(2)中,脱杂助剂选自腐植土、赤泥、炼油装置废催化剂、高岭土、活性炭、半焦、气化灰渣中的一种或几种组成的混配物;脱杂助剂的粒径范围为75~150μm。
30.所述腐殖土为垃圾填埋场挖掘出的废塑料夹带的由植物物质及各类有机垃圾腐烂后形成的混合物。
31.所述半焦为煤、生物质、废塑料等含碳物质在350~600℃条件下热解生成的固体产物。
32.所述气化灰渣为煤、半焦、焦炭、生物质、石油焦、废塑料等含碳物质在高于600℃、常压或加压条件下与气化剂反应后剩余的固体产物。
33.在进一步优选的情况下,步骤(2)中,脱杂助剂选自催化裂化单元废催化裂化催化剂、腐殖土、活性炭中的一种或几种。
34.在优选的情况下,步骤(2)中,溶剂ii与废塑料的重量比例为1:10~10:1。
35.在优选的情况下,以废塑料第二脱杂单元内混合物料总重量为基准,所述的脱杂助剂的重量分数为1%~10%。
36.在优选的情况下,步骤(2)中,脱杂反应的反应条件为:反应温度为280~390℃,压力为0.1~5mpa,第一溶液的停留时间为10~30min。
37.脱杂反应后物料经分离单元ii,分离为第二溶液和第二固体混合物,所述第二溶液为脱杂后废塑料溶液,在所述第二溶液中,氯含量为小于3μg/g,硅含量为小于3μg/g。
38.本发明在所述废塑料第二脱杂单元,将废塑料中的硅杂质进行脱除,并且是以塑料加工过程中添加的有机硅高分子的原始形态脱除,有效避免了硅杂质对后续加工单元催化剂的影响作用。并且进一步降低了废塑料中的氯含量,有效避免了氯杂质对后续加工装置的影响作用。
39.在本发明步骤(3)中,脱除了杂质的废塑料,即第二溶液,与任选的催化裂化原料进入催化裂化单元进行催化裂化反应。在本发明中,所述任选的催化裂化原料是指,在催化裂化单元进料中可以含有任何常规的催化裂化原料,也可以不含有任何其他催化裂化原料,仅有第二溶液。
40.在本发明中,步骤(3)中所述催化裂化单元可以是固定床催化裂化、移动床催化裂化、流化床催化裂化、提升管催化裂化中的一种或几种。或者是tsrfcc、mip、mip-cgp、fdf-cc、mgg、mio、argg催化裂化技术中的一种或几种,具体可根据炼厂现有装置进行灵活选择。
41.在优选的情况下,步骤(3)中,催化裂化催化剂包括沸石、无机氧化物粘结剂和任选的粘土;
42.以催化剂的总重量计,所述沸石的含量为5-50重量%,无机氧化物的含量为5-90重量%,粘土的含量为0-70重量%;
43.所述沸石为选自含或不含稀土的y型或hy型沸石、含或不含稀土的超稳y型沸石和具有mfi结构的沸石中的至少一种。
44.在优选的情况下,步骤(3)中,催化裂化反应条件为:反应温度460~530℃,剂油比3~10,停留时间2~4s。
45.催化裂化反应产物经分离至少得到气体、汽油馏分、柴油馏分。所得的汽油馏分、柴油馏分均是优质的车用燃料组分,分别经过后续处理后,如汽油馏分经中国石化s-zorb技术、中国石化石科院的rsds技术等,能得到符合国v标准或者国vi标准的清洁汽油。柴油馏分与直馏柴油馏分一起经中国石化石科院的rts技术、柴油加氢超深度脱硫技术等,能得到符合国v标准或者国vi标准的清洁柴油。
46.本发明一方面提供了一种用于上述方法的废塑料生产车用燃料系统,包括:废塑料第一脱杂单元、废塑料第二脱杂单元和催化裂化单元;
47.所述废塑料第一脱杂单元设置废塑料入口、溶剂i入口、物料出口、搅拌装置、加热装置,所述废塑料第一脱杂单元的物料出口与分离单元i连通,所述分离单元i设置第一溶液出口和第一固体混合物出口;
48.所述废塑料第二脱杂单元设置第一固体混合物入口、溶剂ii入口、脱杂助剂入口、物料出口、搅拌装置、加热装置,所述分离单元i的第一固体混合物出口与废塑料第二脱杂单元的第一固体混合物入口连通;所述废塑料第二脱杂单元的物料出口与分离单元ii连通,所述分离单元ii设置第二溶液出口和第二固体混合物出口;
49.所述催化裂化单元设置第二溶液入口、任选的催化裂化原料入口、气体出口、汽油馏分出口、柴油馏分出口,所述分离单元ii设置第二溶液出口与催化裂化单元设置第二溶液入口连通。
50.在本发明其中一种优选的实施方式中,所述废塑料生产车用燃料系统,包括:废塑
料第一脱杂单元、溶剂回收单元、废塑料第二脱杂单元、催化裂化单元;
51.所述废塑料第一脱杂单元设置废塑料入口、溶剂i入口、物料出口、搅拌装置、加热装置,所述废塑料第一脱杂单元的物料出口与分离单元i连通,所述分离单元i设置第一溶液出口和第一固体混合物出口;
52.所述溶剂回收单元设置第一溶液入口、回收溶剂i出口、含氯塑料颗粒出口,分离单元i的第一溶液出口与溶剂回收单元的第一溶液入口连通,溶剂回收单元的回收溶剂i出口与废塑料第一脱杂单元的溶剂i入口连通;
53.所述废塑料第二脱杂单元设置第一固体混合物入口、溶剂ii入口、脱杂助剂入口、物料出口、搅拌装置、加热装置,所述分离单元i的第一固体混合物出口与废塑料第二脱杂单元的第一固体混合物入口连通;所述废塑料第二脱杂单元的物料出口与分离单元ii连通,所述分离单元ii设置第二溶液出口和第二固体混合物出口;
54.所述催化裂化单元设置第二溶液入口、任选的催化裂化原料入口、气体出口、汽油馏分出口、柴油馏分出口,所述分离单元ii设置第二溶液出口与催化裂化单元设置第二溶液入口连通。
55.在优选的情况下,所述废塑料第一脱杂单元为一级或多级串联或并联的釜式溶解装置,或者是具有溶解作用的异形溶解装置,或者是具有相同功能的设备如连续螺旋浸取器。所述废塑料第一脱杂单元内设置搅拌装置及加热装置,所述的搅拌装置是电力驱动,或者是磁力驱动,并且是桨式、锚式、框式、螺条式中的一种或几种,所述搅拌装置的搅拌速率为1~300r/min,优选为60~100r/min;所述的加热装置是内加热式和/或外加热式中的一种或几种。外热式可以是夹套式或半圆盘管中的一种或几种,内热式为各类内置盘管;热源可以是电、导热油、蒸汽、明火加热中的一种或几种。
56.在优选的情况下,所述废塑料第二脱杂单元为一级或多级串联或并联的釜式溶解装置,或者是具有溶解作用的异形溶解装置,或者是具有相同功能的设备如连续螺旋浸取器。所述废塑料第二脱杂单元内设置搅拌装置及加热装置,所述的搅拌装置是电力驱动,或者是磁力驱动,并且是桨式、锚式、框式、螺条式中的一种或几种,所述搅拌装置的搅拌速率为1~300r/min,优选为60~100r/min;所述的加热装置是内加热式和/或外加热式中的一种或几种。外热式可以是夹套式或半圆盘管中的一种或几种,内热式为各类内置盘管;热源可以是电、导热油、蒸汽、明火加热中的一种或几种。
57.在优选的情况下,所述分离单元i和分离单元ii是一级或多级串联的各种形式的带保温功能的耐油、耐有机溶剂的连续式自动固液分离设备,或者是各种型号的可自动更换滤网的过滤器、带刮板的压滤机、错流过滤器、卧螺离心机、螺旋挤压脱溶剂设备中的一种或多种。
58.所述分离单元i和分离单元ii设置加热及保温装置,加热装置可以是外热式或内热式的一种或几种;外热式可以是夹套式或半圆盘管中的一种或几种,内热式为各类内置盘管;热源可以是电、导热油、蒸汽、明火加热中的一种或几种。优选所述分离单元i的过滤器所用滤网孔径为0.1~10mm,进一步优选为0.1~1mm。优选所述分离单元ii的过滤器所用滤网孔径为0.001~1mm,优选为1~10μm。
59.本发明的特点:
60.本发明在废塑料第一脱杂单元,采用溶剂i将废塑料中的含氯废塑料溶解,在溶剂
回收单元,在溶剂回收的同时物理回收含氯废塑料,不仅脱氯效果高,溶剂回收利用率高,而且脱氯的同时避免产生大量的固废,还得到了价值相对高的含氯废塑料颗粒。
61.本发明在废塑料第二脱杂单元,将废塑料中的硅杂质进行脱除,并且是以塑料加工过程中添加的有机硅高分子的原始形态脱除,有效避免了后续加工单元催化剂的失活问题。所得杂质含量低的第二溶液送至催化裂化单元进行催化裂化反应制备车用燃料。本发明有助于解决“白色污染”,制备车用燃料,具有良好的环境效益、社会效益和经济效益。
附图说明
62.图1是本发明提供的废塑料制备清洁燃料方法的示意图。
63.图中:1、干燥单元;2、破碎单元;3、废塑料第一脱杂单元;4、分离单元i;5、废塑料第二脱杂单元;6、分离单元ii;7、流体输送单元;8、催化裂化单元;9、溶剂回收单元。
具体实施方式
64.下面结合附图对本发明进行进一步说明,但并不因此而限制本发明。
65.图1是本发明提供的废塑料生产车用燃料的方法示意图中的一种,说明书中所述的其它技术方案的示意图不再单独列出。
66.如图1所示,废塑料依次进入干燥单元1和破碎单元2进行处理,干燥和破碎后的废塑料颗粒和溶剂i进入废塑料第一脱杂单元3中,进行充分混合溶解,溶解后物料经分离单元i 4,分离为第一溶液和第一固体混合物。所得第一溶液进入溶剂回收单元9经处理后,得到回收溶剂i和含氯塑料颗粒。所得第一固体混合物进入废塑料第二脱杂单元5,在溶剂ii、脱杂助剂的作用下进行脱杂反应,反应后物料经分离单元ii 6,分离为第二溶液和第二固体混合物。所得第二溶液和经流体输送单元7进入催化裂化单元8,与任选的催化裂化原料与催化裂化催化剂接触,进行催化裂化反应,经分离得到气体、汽油馏分、柴油馏分、重循环油馏分和油浆,所得汽油馏分和柴油馏分为车用燃料。
67.下面结合实施例对本发明作进一步的说明,但并不因此而使本发明受到任何限制。
68.在实施例中,固体混合物中氯含量采用库仑法进行测定,具体方法为《石油化工分析方法》(ripp试验方法)中的《电量法测定原油中总氯含量》(ripp 64-90)的方法进行测定。所用仪器为微库仑分析仪。试样为粉碎后的废塑料粉末样品。
69.在实施例中,液体混合物中氯含量同样采用《电量法测定原油中总氯含量》(ripp 64-90)的方法进行测定。所不同的是试样为液体混合物。
70.在实施例中,液体混合物中硅含量采用《使用过的润滑油中添加剂元素、磨损金属和污染物以及基础油中某些元素测定法(电感耦合等离子体发射光谱法)》(gb17476-1998)方法进行测定。
71.实施例1~5
72.废塑料a为按pe:pp:ps:pvc=10:5:1:1.5比例混配的市售混合物,其中pe、pp、pvc为薄膜状,ps为泡沫状。破碎为<50mm,废塑料a破碎颗粒和预热至65℃的溶剂i进入废塑料第一脱杂单元中,在65℃下,进行充分混合溶解,溶解后物料经高温过滤器,并在65℃下分离为第一溶液和第一固体混合物。
73.实施例1所用溶剂i为四氢呋喃,溶剂i与废塑料a的重量比例为10:1;所得第一固体混合物中氯含量为23μg/g。
74.实施例2所用溶剂i为甲乙酮,溶剂i与废塑料a的重量比例为10:1;所得第一固体混合物中氯含量为25μg/g。
75.实施例3所用溶剂i为四氢呋喃和环己酮重量比为1:1的混合物,溶剂i与废塑料a的重量比例为5:1;所得第一固体混合物中氯含量为22μg/g。
76.实施例4所用溶剂i为四氢呋喃与甲乙酮重量比为1:1的混合物,溶剂i与废塑料a的重量比例为10:1;所得第一固体混合物中氯含量为13μg/g。
77.实施例5所用有机溶剂为四氢呋喃与甲乙酮重量比为1:2的混合物,溶剂i与废塑料a的重量比例为10:1;所得第一固体混合物中氯含量为19μg/g。
78.实施例6
79.将实施例5所得第一固体混合物送至废塑料第二脱杂单元,在溶剂ii、脱杂助剂的作用下,在350℃温度下进行脱杂反应,反应后物料经高温过滤器,分离为第二溶液和第二固体混合物,所得第二溶液中,氯含量为2.7μg/g,硅含量为3.0μg/g。
80.采用的溶剂ii为富含芳烃的馏分油,是石油加工过程中所得蜡油馏分的混合油,其馏程范围为220~540℃,总芳烃含量为59.6质量%,单环芳烃含量为21质量%;溶剂ii与第一固体混合物的重量比例为5:1。
81.采用的脱杂助剂为半焦,粒径为75~100μm。以废塑料第二脱杂单元内混合物料总重量为基准,所述的脱杂助剂的重量分数为2.5%。
82.实施例7
83.将实施例5所得第一固体混合物送至废塑料第二脱杂单元,在溶剂ii、脱杂助剂的作用下,在350℃温度下进行脱杂反应,反应后物料经高温过滤器,分离为第二溶液和第二固体混合物,所得第二溶液中,氯含量为2.5μg/g,硅含量为2.2μg/g。
84.采用的溶剂ii为催化裂化馏分油,其馏程范围为150~338℃,总芳烃含量为76.8质量%,单环芳烃含量为63.8质量%;溶剂ii与第一固体混合物的重量比例为5:1。
85.采用的脱杂助剂为腐殖土,粒径为75~100μm。以废塑料第二脱杂单元内混合物料总重量为基准,所述的脱杂助剂的重量分数为2.5%。
86.实施例8
87.将实施例5所得第一固体混合物送至废塑料第二脱杂单元,在溶剂ii、脱杂助剂的作用下,在350℃温度下进行脱杂反应,反应后物料经高温过滤器,分离为第二溶液和第二固体混合物,所得第二溶液中,氯含量为2.5μg/g,硅含量为2.5μg/g。
88.采用的溶剂ii为富含芳烃馏分油,其馏程范围为138~362℃,总芳烃含量为90.9质量%,单环芳烃含量为26.8质量%;溶剂ii与第一固体混合物的重量比例为5:1。
89.采用的脱杂助剂为气化灰渣与催化裂化单元平衡剂以重量比为1:1混合的混合物,粒径为75~100μm。以废塑料第二脱杂单元内混合物料总重量为基准,所述的脱杂助剂的重量分数为2.5%。
90.实施例9
91.将实施例5所得第一固体混合物送至废塑料第二脱杂单元,在溶剂ii、脱杂助剂的作用下,在350℃温度下进行脱杂反应,反应后物料经高温过滤器,分离为第二溶液和第二
固体混合物,所述第二溶液中,氯含量为2.5μg/g,硅含量为2.8μg/g。
92.采用的溶剂ii为富含芳烃馏分油,其馏程范围为138~362℃,总芳烃含量为90.9质量%,单环芳烃含量为26.8质量%;溶剂ii与第一固体混合物的重量比例为5:1。
93.采用的脱杂助剂为催化裂化单元平衡剂,粒径为75~100μm。以废塑料第二脱杂单元内混合物料总重量为基准,所述的脱杂助剂的重量分数为2.5%。
94.实施例10
95.将实施例6所得第二溶液送至催化裂化单元,与催化裂化催化剂接触,进行催化裂化反应,经分离得到气体、汽油馏分、柴油馏分、重循环油、油浆,所得重循环油在催化裂化单元内进行循环。
96.催化裂化催化剂牌号为gor-a,是中国石化催化剂分公司生产。
97.催化裂化反应温度为500℃,剂油比为4,反应时间为2.02s。
98.所得产品产率如表1所示。由于有机硅分解产物主要为八甲基环四硅氧烷(d4)和十甲基环五硅氧烷(d5),主要集中在汽油馏分中,因此重点分析汽油馏分中的杂质含量。
99.实施例11
100.将实施例7所得第二溶液和催化裂化原料vgo一起送至催化裂化单元,第二溶液与vgo的重量比为1:1,与催化裂化催化剂接触,进行催化裂化反应,经分离得到气体、汽油馏分、柴油馏分、重循环油和油浆,所得重循环油在催化裂化单元内进行循环。
101.催化裂化催化剂牌号为gor-a,是中国石化催化剂分公司生产。
102.催化裂化反应条件为温度为500℃,剂油比为4,反应时间为2.02s。
103.所得产品产率如表1所示。
104.表1
105.106.实施例12
107.所用废塑料b为广东省某垃圾填埋场挖出陈化垃圾中分选出的废塑料,分选后的废塑料基本无水分存在,灰分含量约为9.9重量%。分选回收的废塑料通过传送带送入间歇换热式干燥器中,所用热源为低阶蒸汽,干燥器温度为105℃,废塑料在干燥器中的停留时间为30min;干燥后的废塑料通过传送带送往剪切式破碎机,将废塑料破碎成小于10mm碎片;通过螺旋进料器将破碎的废塑料送至第一脱杂单元的外热式釜式溶解釜,通过计量泵将甲乙酮:四氢呋喃=2:1的混合溶剂以塑溶重量比1:5的比例,一并送往外热式釜式溶解釜,溶解釜溶解温度为65℃,操作压力为常压,搅拌桨转速为60r/min,废塑料b在溶解釜内溶解30min后更换新鲜溶剂洗涤一次,溶解釜采用两釜并联的方式;混合物通过溶解釜底部的卸料口送往高温过滤器,在65℃下将混合物分离为第一固体混合物及第一溶液。第一溶液通过闪蒸回收溶剂i和含氯废塑料。
108.第一固体混合物在80℃下干燥进一步回收溶剂i后通过螺旋进料器输送至第二脱杂单元的外热式釜式溶解釜,通过计量泵将溶剂ii以塑溶重量比1:10的比例送往外热式釜式溶解釜,通过计量泵将fcc催化剂平衡剂按剂塑重量比1:10的比例送往外热式釜式溶解釜,脱杂反应温度为390℃,操作压力为0.5mpa,搅拌桨转速为60r/min,第一固体混合物在溶解釜内停留时间为30min,溶解釜采用两釜并联的方式;溶解一定时间后混合物通过溶解釜底部的卸料口将送往高温过滤器,在350℃下将反应后物料进行过滤脱除其中不溶杂质得到第二溶液;利用单螺杆泵将第二溶液送往催化裂化单元。与催化裂化催化剂接触,进行催化裂化反应,经分离得到气体、汽油馏分、柴油馏分、油浆和半焦。
109.溶剂ii为催化裂化馏分油,其馏程范围为150~338℃,总芳烃含量为76.8质量%,单环芳烃含量为63.8质量%。
110.催化裂化催化剂牌号为gor-a,是中国石化催化剂分公司生产。
111.催化裂化反应条件为温度为500℃,剂油比为4,反应时间为2.02s。
112.所得产品产率及部分杂质含量如表2所示。
113.实施例13
114.废塑料b原料,第一脱杂单元的溶剂i和反应条件,第二脱杂单元的溶剂ii、脱硅助剂和反应条件,催化裂化单元的催化剂与反应条件均与实施例12相同。所不同的是,进入催化裂化单元的进料是第二溶液与催化裂化原料胜利vgo重量比为1:1的混合原料。
115.原料中杂质、反应过程的积碳沉积于催化剂上会导致催化剂失活,为提高催化剂使用寿命,实施例所用催化裂化单元装置为循环流化床装置,即失活的催化剂在另一装置中再生处理,但金属杂质导致的永久性失活无法再生,因此为维持催化裂化装置稳定运转,需要置换其中的部分催化剂,以使催化剂活性处于较平衡、稳定的状态。通常以维持原有装置稳定运转时处理1t原料油所需的催化剂置换量为指标,本实施例中催化裂化催化剂置换量为1.2kg/t。
116.所得产品产率及部分杂质含量如表2所示。
117.对比例1
118.采用胜利vgo在催化裂化单元进行反应,催化裂化单元的催化剂与反应条件均与实施例12相同。所得产品产率及部分杂质含量如表2所示。
119.对比例2
120.废塑料b原料,第一脱杂单元的溶剂i和反应条件,第二脱杂单元的溶剂ii和反应条件,催化裂化单元的进料、催化剂与反应条件均与实施例13相同。所不同的是,第二脱杂单元没有脱硅助剂。
121.本对比例中催化裂化催化剂置换量为1.22kg/t。
122.所得产品产率及部分杂质含量如表2所示。
123.表2
[0124][0125]
通过对比例与实施例结果的比较可以发现,本发明所述实施例可以大幅降低油品中有害元素的相对含量,获得合格的成品油。需说明的是,由于vgo中添加了部分塑料,导致fcc单元的干气、液化气和焦炭产率略有增加,而汽、柴油收率略有降低。
[0126]
以上所述仅为本发明的任意实施例,并不用于限制本发明,对于本领域的技术人员来讲,本发明可以有各种更改和变化。凡在本发明的精神和原则之内,所做的任何修改、等同替换、改进等,均应包含在本发明的保护范围之内。