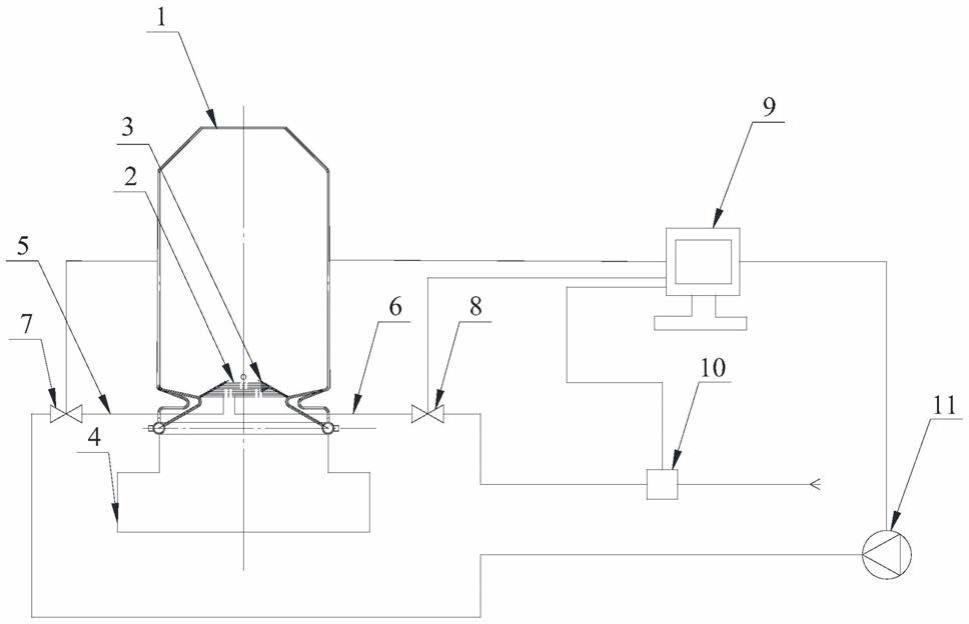
1.本发明属于气化炉排渣领域,具体涉及一种气流床气化炉用防堵渣下渣口结构及其布置方法。
背景技术:
2.我国一次能源储备呈现“富煤、贫油、少气”的特点,这一特点决定了煤炭将在一次性能源生产和消费中占据主导地位,煤炭在一次能源生产和消费构成中始终占比超过50%。煤炭直接燃烧的使用方式会对大气环境造成严重的污染。煤气化技术是高效清洁的洁净煤技术,利用煤气化技术可以生产工业燃料气、民用燃料气、化工合成原料气、合成燃料油原料气、氢燃料电池、合成天然气、火箭燃料等。当前主要的煤气化技术有移动床气化、流化床气化、气流床气化和熔融床气化四类,其中,气流床气化技术因其气化强度高、单炉生产能力大、煤种适应范围广、碳转化率高等优点已成为煤炭气化技术的主要发展方向。
3.气流床气化炉在运行时,反应温度在1350℃~1500℃,煤在其中燃烧后会形成熔渣,形成的熔渣通过下渣口排至渣池。传统形式的气流床气化炉下渣口的形式主要有两种,一种是采用“入口宽,出口窄”的正圆锥台形式,另一种则是采用入口与出口宽窄相同的圆柱形式。在实际运行中,熔渣从下渣口排至渣池依靠的是重力作用,而采用这两种形式下渣口的气化炉因排渣困难经常出现堵渣现象。一旦发生堵渣,只能停炉清除,导致整个生产线全部停运,会给企业造成巨大的经济损失。
技术实现要素:
4.本发明为了解决现有气流床气化炉中下渣口在排渣过程中经常出现堵渣现象,一旦发生堵渣,只能停炉清除,导致整个生产线全部停运,会给企业造成巨大的经济损失的问题,进而提供一种气流床气化炉用防堵渣下渣口结构及其布置方法;
5.一种气流床气化炉用防堵渣下渣口结构,所述下渣口结构包括下渣口、水冷盘管、进水管和出水管,下渣口设置在气化炉的底部,下渣口为圆台状,下渣口的小口端与气化炉的炉体内部连通设置作为入口端,下渣口的大口端设置与气化炉的炉体内部连通设置作为出口端,下渣口主体的内壁上缠绕有水冷盘管,水冷盘管的外侧与下渣口主体焊接固定,缠绕后的水冷盘管形成圆台状通道,且圆台状通道的入口端高于下渣口的入口端,圆台状通道的出口端低于下渣口的出口端,圆台状通道的入口端边缘处沿周向等距加工有n个壶口,进水管设置在圆台状通道的底部,且进水管的一端与水冷盘管的进水端相连,出水管设置在圆台状通道的顶部,且出水管的一端与水冷盘管的出水端相连。;
6.进一步地,所述下渣口的入口端直径为d1,下渣口的出口端直径为d2,且d2=(1.75~2.1)d1;
7.进一步地,所述水冷盘管的入口端直径为d3,水冷盘管的出口端直径为d4,d4=(1.8~2.2)d3;
8.进一步地,所述壶口的个数n的取值范围为1
‑
4个;
9.进一步地,所述下渣口的出口端的正下方设有渣池,渣池与下渣口出口端所在圆周的垂直距离为5~7m;
10.进一步地,所述进水管上设有进水阀,出水管上设有出水阀,进水管上还有设有水泵,出水管上还设有流量计;
11.一种气流床气化炉用防堵渣下渣口结构的布置方法,所述方法是通过以下步骤实现的:
12.步骤一:加工下渣口:下渣口为圆台状,下渣口的小口端作为入口端,端面直径为d1,下渣口的大口端作为出口端,端面直径为d2,且d2=(1.75~2.1)d1;
13.步骤二:安装水冷盘管:将水冷盘管沿步骤一中选取的下渣口主体的内轮廓面缠绕在下渣口上,且将水冷盘管的外侧与下渣口的内轮廓面焊接固定,缠绕后的水冷盘管形成圆台状通道,圆台状通道位于下渣口入口端的端面直径为d3,圆台状通道位于下渣口出口端的端面直径为d4,且d4=(1.80~2.2)d3;
14.步骤三:安装进水管路和出水管路;在进水管上串联进水阀和水泵,并将串联有进水阀和水泵的进水管的输出端与步骤二中水冷盘管的进水口相连,在出水管上串联出水阀和流量计,并将串联有出水阀和流量计的出水管的输人端与步骤二中水冷盘管的出水口相连;
15.步骤四:加工壶口:在步骤四中安装好进水管路和出水管路的圆台状通道的顶端边缘处沿周向等距加工有n个壶口;
16.步骤五:设置渣池:在下渣口的底部设置渣池,并保证下渣口出口端所在圆周与渣池的垂直距离为5~7m;
17.步骤六:布置流量和温度监控装置:在下渣口结构附近设置dcs系统,dcs系统用于接收来自进水管、出水管的温度及流量计的流速信号,dcs系统监控的温度范围区间为160~190℃,dcs系统监控的流速范围区间为6~9m/s。
18.本发明与现有技术相比具有以下有益效果:
19.本发明提供的一种气流床气化炉用防堵渣下渣口结构及其布置方法,可以有效的解决气流床气化炉下渣口在排渣过程中的堵渣现象,相比于传统形式的两种下渣口,本发明主要有以下优势:
20.(1)落渣的起始位置高,在下渣口入口处熔渣温度高;
21.本发明中所涉及的下渣口,其进口所在水平高度要高于传统形式的两种下渣口,如图4所示,喉口虚线a处为传统形式的两种下渣口的入口,b处为本发明下渣口入口,b处比a处高0.5~0.7m。本发明中液态熔渣由于更靠近气化炉内高温区域,在进入下渣口时的温度较高,约为1350℃,传统形式两种下渣口温度为1250℃~1270℃。本发明下渣口比传统形式下渣口在落渣起始处温度高80~100℃。较高的熔渣温度能使灰渣以液态形式排出,而不会形成固态渣,有利于防止下渣口堵渣。
22.(2)废渣的流动形式不同,出渣位置不同,下渣速度快;
23.传统形式的两种下渣口,其下渣过程是这样完成的:液态熔渣在下渣口附近堆积,并流入下渣口,沿下渣口内表面流下排出。而采用本发明形式的下渣口,其下渣过程是这样完成的:随着液态熔渣在下渣口及水冷盘管周围堆积,当其堆积高度达到壶口处后,开始从水冷盘管的上边缘开有的壶口处流进下渣口,随即排至渣池。本发明中熔渣通过壶口流入
下渣口并排出,其流通面积极小,约为0.00025~0.000377m2,传统形式的两种下渣口,其熔渣在流入和排出下渣口的过程中,流经面积大,其中一种为“入口宽,出口窄”的正圆锥台式下渣口熔渣所流经的内表面面积,另一种为“出入口同宽”的圆柱式下渣口熔渣所流经的内表面面积,第一种下渣口的流通面积为0.022765~0.024335m2,第二种下渣口的流通面积为0.02355~0.02512m2。从进入下渣口至排出下渣口的整个排渣过程的速度可用如下公式来计算:
24.v=q/ρa
25.其中,v为排渣速度,q为熔渣质量流量,ρ为熔渣密度,a为熔渣流经的面积。v1是本发明排渣速度,v2是“入口宽,出口窄”的正圆锥台式下渣口排渣速度,v3是“出入口同宽”的圆柱式下渣口排渣速度,经公式v=q/a分析可知,q和ρ不变时,排渣速度v与面积成反比,故v1>>v2、v3,相差接近100倍。传统形式的两种下渣口由于排渣时流经面积大,排渣速度慢,在排渣过程中与接触面进行热交换,放热而温度降低。本发明下渣口由于排渣时流经面积极小(近似一个点),排渣速度极快,远大于另外两种下渣口,整个排渣过程都是以液态熔渣的形式完成,在出口处熔渣温度比另外两种下渣口高120~150℃,有利于防止下渣口堵渣。
附图说明
26.图1是气流床气化炉结构简图
27.图2是气流床下渣口示意图
28.图3是气流床气化炉下渣口a
‑
a向视图
29.图4是传统形式中“入口宽,出口窄”的下渣口结构简图;
30.图5是传统形式中“入口与出口同宽”的下渣口结构简图;
31.图6是本技术中下渣口结构简图;
32.图中:1气化炉、2下渣口主体、3水冷盘管、4渣池、5进水管、6出水管、7水阀、8出水阀、9dcs系统、10流量计、11水泵和12壶口。
具体实施方式
33.具体实施方式一:参照图1至图6说明本实施方式,本实施方式提供一种气流床气化炉用防堵渣下渣口结构,所述下渣口结构包括下渣口2、水冷盘管3、进水管5和出水管6,下渣口2设置在气化炉1的底部,下渣口2为圆台状,下渣口2的小口端与气化炉1的炉体内部连通设置作为入口端,下渣口2的大口端设置与气化炉1的炉体内部连通设置作为出口端,下渣口主体2的内壁上缠绕有水冷盘管3,水冷盘管3的外侧与下渣口主体2焊接固定,缠绕后的水冷盘管3形成圆台状通道,且圆台状通道的入口端高于下渣口2的入口端,圆台状通道的出口端低于下渣口2的出口端,圆台状通道的入口端边缘处沿周向等距加工有n个壶口12,进水管5设置在圆台状通道的底部,且进水管5的一端与水冷盘管3的进水端相连,出水管6设置在圆台状通道的顶部,且出水管6的一端与水冷盘管3的出水端相连。
34.本发明的工作原理是:气化炉1在实际运行中,运行温度为1350℃~1500℃,煤燃烧后所产生的液态熔渣从炉膛内下落至下渣口2和水冷盘管3附近区域。在该区域中,水冷盘管3内通入的冷却水温为155℃~170℃,在冷却水的冷却作用下液态熔渣温度降低至煤灰渣的熔点以下,在水冷盘管3外表面形成固态渣。在形成固态渣之后,气化炉在持续运行
中产生的液态熔渣会与固态渣进行热交换,部分粘附于水冷盘管3表面的固态渣会熔化成为液态熔渣,另一方面液态熔渣会温度降低形成固态渣,最终在水冷盘管3外表面形成一层“保护膜”,避免了水冷盘管3在高温液态熔渣长期作用下被烧损,体现了“以渣抗渣”的原理。另外,随着液态熔渣在下渣口主体2及水冷盘管3周围堆积,当其堆积高度达到壶口12处后,开始从水冷盘管3的上边缘开有的1~4个壶口处流进下渣口2,并排至渣池4。本发明中的下渣口主体2采用的是“入口窄,出口宽的”圆台形式,其入口端的直径d1和出口端直径d2之间满足:d2>d1,且d2=(1.75~2.1)d1。相比于传统形式,采用本发明形式的下渣口在排渣时,由于入口宽度小于出口宽度,因此流入排渣口的速度远小于流出排渣口的速度,且该形式的下渣口在排渣时,熔渣不会受到传统形式下渣口斜面支持力的作用,完全在重力的作用下落至排渣口。dcs系统9用于接收来自进水管5、出水管6及流量计10的水温信号和流速信号,当监控的冷却水温度低于160度或高于190度时,会通过调节水泵频率,改变冷却水流量,从而将冷却水温保持在155~190℃的正常范围内。当流速低于6m/s,或高于9m/s时,同样会通过调节水泵频率,改变冷却水流量,而保证流速在正常范围之内。
35.具体实施方式二:参照图1至图6说明本实施方式,本实施方式是对具体实施方式二所述的下渣口2作进一步限定,本实施方式中,所述下渣口2的入口端直径为d1,下渣口2的出口端直径为d2,且d2=(1.75~2.1)d1。其它组成及连接方式与具体实施方式一相同。
36.具体实施方式三:参照图1至图6说明本实施方式,本实施方式是对具体实施方式二所述的水冷盘管3作进一步限定,本实施方式中,所述水冷盘管3的入口端直径为d3,水冷盘管3的出口端直径为d4,d4=(1.8~2.2)d3。其它组成及连接方式与具体实施方式一相同。
37.具体实施方式四:参照图1至图6说明本实施方式,本实施方式是对具体实施方式二所述的壶口12的个数作进一步限定,本实施方式中,所述壶口12的个数n的取值范围为1
‑
4个。其它组成及连接方式与具体实施方式一相同。
38.具体实施方式五:参照图1至图6说明本实施方式,本实施方式是对具体实施方式二所述的下渣口2作进一步限定,本实施方式中,所述下渣口2的出口端的正下方设有渣池4,渣池4与下渣口2出口端所在圆周的垂直距离为5~7m。其它组成及连接方式与具体实施方式一相同。
39.具体实施方式六:参照图1至图6说明本实施方式,本实施方式是对具体实施方式二所述的进水管5和出水管6作进一步限定,本实施方式中,所述进水管5上设有进水阀7,出水管6上设有出水阀8,进水管5上还有设有水泵11,出水管6上还设有流量计10。其它组成及连接方式与具体实施方式一相同。
40.具体实施方式七:参照图1至图6说明本实施方式,本实施方式提供一种气流床气化炉用防堵渣下渣口结构的布置方法,所述方法是通过以下步骤实现的:
41.步骤一:加工下渣口2:下渣口2为圆台状,下渣口2的小口端作为入口端,端面直径为d1,下渣口2的大口端作为出口端,端面直径为d2,且d2=(1.75~2.1)d1;
42.步骤二:安装水冷盘管3:将水冷盘管3沿步骤一中选取的下渣口主体2的内轮廓面缠绕在下渣口2上,且将水冷盘管3的外侧与下渣口2的内轮廓面焊接固定,缠绕后的水冷盘管3形成圆台状通道,圆台状通道位于下渣口2入口端的端面直径为d3,圆台状通道位于下渣口2出口端的端面直径为d4,且d4=(1.80~2.2)d3;
43.步骤三:安装进水管路和出水管路;在进水管5上串联进水阀7和水泵10,并将串联
有进水阀7和水泵10的进水管5的输出端与步骤二中水冷盘管3的进水口相连,在出水管6上串联出水阀8和流量计11,并将串联有出水阀8和流量计11的出水管6的输人端与步骤二中水冷盘管3的出水口相连;
44.步骤四:加工壶口:在步骤四中安装好进水管路和出水管路的圆台状通道的顶端边缘处沿周向等距加工有n个壶口12;
45.步骤五:设置渣池4:在下渣口2的底部设置渣池4,并保证下渣口出口端所在圆周与渣池4的垂直距离为5~7m;
46.步骤六:布置流量和温度监控装置:在下渣口结构附近设置dcs系统9,dcs系统9于接收来自进水管5、出水管6的温度及流量计10的流速信号,dcs系统监控的温度范围区间为160~190℃,dcs系统监控的流速范围区间为6~9m/s。
47.本发明已以较佳实施案例揭示如上,然而并非用以限定本发明,任何熟悉本专业的技术人员,在不脱离本发明技术方案范围内,当可以利用上述揭示的结构及技术内容做出些许的更动或修饰为等同变化的等效实施案例,但是凡是未脱离本发明技术方案的内容,依据本发明的技术实质对以上实施案例所做的任何简单修改、等同变化与修饰,均仍属本发明技术方案范围。
48.实施例
49.一台采用传统形式下渣口,造气量80000nm3/h的气化炉,在运行时发生堵渣事故。由于判断迟缓,延误了处理时间,下渣口完全堵住,被迫停炉。由于气化炉是化工企业的生产源头,气化炉停车,导致整个生产线全部停运。一年内气化炉停炉除渣共计8天,综合计算整条煤气化生产线经济损失达6000万元以上。
50.同样以一台造气量80000nm3/h的气化炉为例,其下渣口结构采用本技术所述结构,具体结构参数如下:
51.在造气量80000nm3/h的气化炉的底部加工有圆台状下渣口2,下渣口2的入口端直径为d1,下渣口2的出口端敞直径为d2,d1和d2满足:d2>d1,且d2=1.9d1,在下渣口2的内侧壁上缠绕有水冷盘管3,缠绕后的水冷盘管3形成圆台状通道,圆台状通道的入口端直径为d3,圆台状通道的出口端敞直径为d4,d3和d4满足:d4>d3,且d4=2d3,圆台状通道入口端的边缘开有四个壶口12,且四个壶口12呈圆周分布,相邻两个壶口12的间隔角度为90
°
。下渣口2出口端下方设有渣池4,渣池4与下渣口2出口端所在圆周的垂直距离为6m。进水管5和出水管6上设有分别进水阀7和出水阀8;进水管5上设有水泵11,出水管6上设有流量计10,另外本下渣口结构的周围还设有dcs系统9接收来自进水管5、出水管6及流量计10的温度和流速信号。监控的水温低于155℃或高于190℃时,会通过调节水泵频率,改变冷却水流量,从而将冷却水温保持在155~190℃的正常范围内;监控的流速低于6m/s或高于9m/s时,同样也会通过调节水泵频率,改变冷却水流量,从而将流速稳定在6~9m/s范围之内。
52.采用本发明形式下渣口,灰渣都以液态熔渣的形式排出,排渣顺畅,运行两年没有发生下渣口堵渣现象。堵渣问题得以解决,提高了气化炉运行的安全性和经济性。