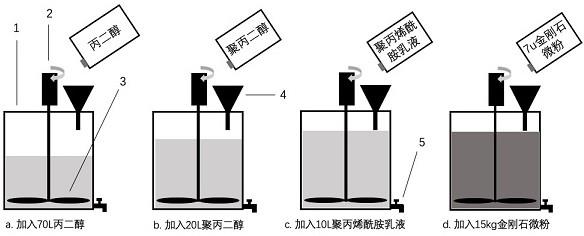
1.本发明涉及一种碳化硅专用钻石切割液的配置方法。
背景技术:
2.碳化硅作为第三代半导体的代表,其具有禁带宽度大、击穿电场高、饱和电子漂移速度高、热导率大等特点,可应用于1200伏特以上的高压环境,因此在严苛环境中有着明显优势;同时,sic晶体因其与外延层材料gan具有高匹配的晶格常数和热膨胀系数及良好的热导率,是gan基器件的理想衬底材料,如led和ld。因此,sic晶体材料已经成为半导体照明技术领域不可缺少的衬底材料。目前,碳化硅和碳化硅基半导体材料已经成为了世界各国研究的热点。
3.将碳化硅晶体应用于器件需加工成一定尺寸的晶圆片,基本工艺包括晶体生长、晶锭检测、晶锭整形、切片、打标、研磨、倒角、抛光、cmp、清洗等步骤。由于碳化硅晶体硬度很高,这为晶体加工带来很大的困难,而将sic晶棒切割成翘曲度小、厚度均匀、低切损的晶片,对于后续的研磨和抛光至关重要。与传统的内圆、外圆切割相比,多线切割具有大切削速度、高加工精度、高效率和较长的寿命等优点,已广泛应用于碳化硅晶片的高效切割。
4.由于碳化硅晶体硬度太高,目前只能用钻石粉砂浆进行多线切割。而且,为保证切割质量,需要砂浆具有良好的悬浮性,以确保整个切割过程中砂浆浓度的稳定性。因此,行业内目前通常采用油性钻石砂浆进行碳化硅晶体的切割。但是,油性砂浆黏度高,黏附性强,不容易清洗,需用煤油进行清洗。而煤油又属于易燃易爆化学品,环评要求高,不宜大量存储,也不能随意排放。
技术实现要素:
5.本发明的目的在于提供一种碳化硅专用钻石切割液的配置方法,以解决上述背景技术中提出的问题。
6.为实现上述目的,本发明提供如下技术方案:一种碳化硅专用钻石切割液的配置方法,制作步骤如下:(1)取所需量的二元醇倒入混料桶中;(2)按比例量取所需量的聚二元醇倒入混料桶中;(3)打开混料桶搅拌功能;(4)称取所需量的分散剂,从混料桶顶部加料口慢慢全部倒入混料桶中;(5)搅拌15min以上,以确保分散剂在混合液中混合均匀;(6)称取所需量的金刚石微粉,从混料桶顶部加料口慢慢全部倒入混料桶中;(7)混合24h,以确保金刚石微粉在切割液中分散均匀,保证后续切割质量;(8)将混合好的砂浆倒入切割机料桶,进行切割。
7.优选的,金刚石微粉粒径采用4~9um,其粒径的正态分布为:4um颗粒占2.4%、5um颗粒占14.1%、6um颗粒占36.2%、7um颗粒占43.5%、9um颗粒占3.8%。
8.优选的,所述金刚石微粉粉浓度为砂浆重量百分比的12%~18%。
9.优选的,所述有机分散剂为聚丙烯酰胺。
10.优选的,所述二元醇的添加比例60~70%,所述聚二元醇的添加比例20~30%,所述聚丙烯酰胺乳液的添加比例8~12%,所述钻粉浓度为砂浆重量百分比的12%~18%。
11.与现有技术相比,本发明的有益效果是:根据本发明的配置方法,砂浆悬浮性好、颗粒分散均匀,可保证碳化硅晶体切割效果,切片ttv好,翘曲较小,同时用清水或低浓度碱液即可清洗晶片表面切割液附着物,有效降低了切割后晶片的清洗难度。本发明操作简单、成本较低、效果良好。
附图说明
12.图1为该发明的金刚石微粉的粒径分布图;图2为该发明的金刚石微粉的粒径分布表;图3为该发明的碳化硅专用钻石切割液的配置方法。
13.图中:1、混料桶;2、变速电机;3、拌桨叶;4、漏斗;5、放液口。
具体实施方式
14.下面将结合本发明实施例中的附图,对本发明实施例中的技术方案进行清楚、完整地描述,显然,所描述的实施例仅仅是本发明一部分实施例,而不是全部的实施例。基于本发明中的实施例,本领域普通技术人员在没有做出创造性劳动前提下所获得的所有其他实施例,都属于本发明保护的范围。
15.一种碳化硅专用钻石切割液的配置方法,制作步骤如下:(1)取所需量的二元醇倒入混料桶中;(2)按比例量取所需量的聚二元醇倒入混料桶中;(3)打开混料桶搅拌功能;(4)称取所需量的分散剂,从混料桶顶部加料口慢慢全部倒入混料桶中;(5)搅拌15min以上,以确保分散剂在混合液中混合均匀;(6)称取所需量的金刚石微粉,从混料桶顶部加料口慢慢全部倒入混料桶中;(7)混合24h,以确保金刚石微粉在切割液中分散均匀,保证后续切割质量;(8)将混合好的砂浆倒入切割机料桶,进行切割。
16.金刚石微粉粒径采用4~9um,其粒径的正态分布为:4um颗粒占2.4%、5um颗粒占14.1%、6um颗粒占36.2%、7um颗粒占43.5%、9um颗粒占3.8%;金刚石微粉粉浓度为砂浆重量百分比的12%~18%,有机分散剂为聚丙烯酰胺;二元醇的添加比例60~70%,所述聚二元醇的添加比例20~30%,所述聚丙烯酰胺乳液的添加比例8~12%,所述钻粉浓度为砂浆重量百分比的12%~18%。
17.本发明实施形态的碳化硅晶体专用钻石切割液可包括金刚石微粉、丙二醇、聚丙二醇和聚丙烯酰胺乳液。本实施形态以配置100升钻石切割液为例;图1示出该实施形态的金刚石微粉的粒径分布图。图2示出该实施形态的金刚石微粉的粒径分布表。应理解,这里所用的金刚石粒径分布并非固定的,即不同的切割工艺可采用不同粒径分布的金刚石微粉;图3示意性示出了该实施形态的碳化硅专用钻石切割液的配置方法,
准备一个120l混料桶1,混料桶1最好采用透明有机玻璃材质。这样可以更好的观测砂浆混合的状态;在混料桶1的顶盖上安装一个变速电机2,可以自由调节搅拌桨叶3的转速,更好地控制砂浆混合的均匀性;将70l丙二醇通过漏斗4慢慢倒入混料桶1中(如图3a),打开搅拌功能,转速调至20rpm;将20l聚丙二醇通过漏斗4慢慢倒入混料桶1中(如图3b),将10l聚丙烯酰胺乳液通过漏斗4慢慢倒入混料桶1中(如图3c),将15kg(如图1)所示粒径分布的金刚石微粉通过漏斗4慢慢倒入混料桶1中(如图3d),混合24h后待用。这样可以保证金刚石微粉能彻底均匀分散、悬浮于切削液中,确保砂浆切割过程中的均匀性和稳定性;通过放液口5,按使用需求将混合好的钻石砂浆倒入切割机砂浆桶,即可开始进行碳化硅晶体的多线切割。
18.需注意:在装入新砂浆前,将切割机砂浆桶内旧液清洗干净。这样可以更好地控制砂浆的切削能力,避免材料的浪费。
19.在一个示例中,待切晶锭为100mm总长的4英寸导电4h晶锭,晶片的切割厚度为510um,采用本发明的碳化硅专用钻石切割液,并设定相应线性渐变切割速率进行切割。
20.上述经过切割的碳化硅晶片几何参数结果优良,且切片直接用清水即可冲洗干净。
21.表1列出了碳化硅晶体常规油性切割砂浆与采用本发明切割砂浆之间的一些效果对比。可知,经本发明方法进行碳化硅晶体切割,使用简便、切割面形好、砂浆粘度低且极易清洗。
22.表1:常规碳化硅油性切割砂浆与本发明的效果对比 ttvwarpbow粘度变化清洗方式常规油性切割砂浆<15<30<20大煤油+热碱液多次漂洗本发明<10<20<15小清水或稀碱液一次清洗本发明的碳化硅专用钻石切割液,可根据不同的切割工艺进行不同比例的自行配置,使用方便。本发明的碳化硅专用钻石切割液粘度变化小,砂浆颗粒分散性好、切割面形好,成本较低,适合广泛用于碳化硅衬底片的批量生产或实验性碳化硅晶片的切割工艺探索,具有很大的产业应用性。另外,本发明的碳化硅专用钻石切割液,易溶于水,切割后的碳化硅晶片用清水或稀碱液就可轻松洗净,清洗过程简单、方便,非常适合碳化硅的批量生产使用。
23.尽管已经示出和描述了本发明的实施例,对于本领域的普通技术人员而言,可以理解在不脱离本发明的原理和精神的情况下可以对这些实施例进行多种变化、修改、替换和变型,本发明的范围由所附权利要求及其等同物限定。